1. |
Sadowski T.♦, Postek E., Pietras D.♦, Guhathakurta J.♦, Kruszka L.♦, Grążka M.♦, Data-based micromechanical modelling of the dynamic response of interpenetrated composites,
ICCS27 - 27th International Conference on Composite Structures, 2024-09-03/09-06, Ravenna (IT), No.1014, pp.130-130, 2024 | 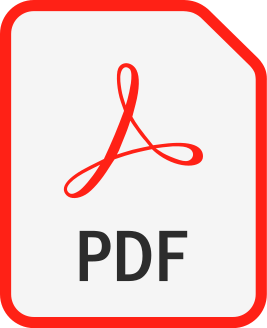 |
2. |
Postek E., Pietras D.♦, Guhathakurta J.♦, Kruszka L.♦, Grążka M.♦, Sadowski T.♦, Experimental testing and numerical modelling of impacts in interpenetrated composite,
ICCSE3, 3rd International Conference on Computations for Science and Engineering, 2023-08-20/08-23, Neapol (IT), pp.19-20, 2023 Streszczenie:
The interpenetrating composites consist of a scaffold and metallic matrix, which fills it being introduced under pressure. The scaffold is usually crushable. In our case, the SiC material stands for the skeleton, while the AlSi12 alloy is the matrix. Both materials are crushable. The SiC phase is brittle throughout the loading process, but the AlSi12 alloy is brittle during the elastic phase; then, its behaviour becomes viscous-plastic. The presentation concerns the experimental testing and simulations of the impact and fragmentation of metal matrix composite - AlSi12/SiC. The numerical model of the internal structure is created based on CT scanning. The microstructure of the composite is complex and consists of a metallic phase (85%), ceramic SiC skeleton, porosity, and a system of not perfect interfaces. The impacts are realized in the following few scenarios. The exemplary scenario is realized by imposing the initial conditions on the sample that hits a hard elastic barrier. The second one corresponds to SHPB experiments. The last one is the hitting of an elastic impactor against the sample. The influence of the impact velocities and material parameters of the phases on the failure modes is observed. Previously, analyses of the modes of loading application on the micromechanical failure of metal matrix composite were analysed in [1, 2]. An analysis of the empty SiC scaffolds is presented in [3]. The proposed finite element model of the AlSi12/SiC composite behaviour describing gradual degradation under impact loading was tested for different scenarios of hitting. In all cases, the growth of damage in the composite is very realistic. These results lead to the conclusion the proposed finite element model is very effective.
Acknowledgement: The results presented in this paper were obtained within the framework of research grant No. 2019/33/B/ST8/01263 financed by the National Science Centre, Poland. The numerical analyses were done in the ICM UW in Warsaw and in CI TASK in Gdańsk, Poland.
References:
[1] Postek, E. and Sadowski, T. Distributed microcracking process of WC/Co cermet under dynamic impulse compressive loading. Compos. Struct. (2018) 194: 494-508.
[2] Postek, E. and Sadowski, T. Qualitative comparison of dynamic compressive pressure load and impact of WC/Co composite. Int. J. Refract. Hard. Met. (2018) 77: 68-81.
[3] Postek, E., Sadowski, T. and Bieniaś, J. Simulation of impact and fragmentation of SiC skeleton, Phys. Letters (2021) 24:578-587.
Słowa kluczowe: Cermets, Interpenetration, Impact, Viscoplasticity, Peridynamics Afiliacje autorów:
Postek E. | - | IPPT PAN | Pietras D. | - | Lublin University of Technology (PL) | Guhathakurta J. | - | CT-LAB Stuttgart (DE) | Kruszka L. | - | Military University of Technology (PL) | Grążka M. | - | Military University of Technology (PL) | Sadowski T. | - | Lublin University of Technology (PL) |
| 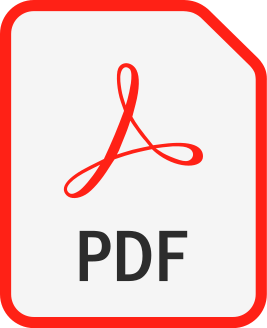 |
3. |
Postek E., Pietras D.♦, Guhathakurta J.♦, Sadowski T.♦, Numerical model of impact and fragmentation of interpenetrated composite,
ICCSE, 2nd International Conference on Computations for Science and Engineering, 2022-08-30/09-02, Rimini (IT), pp.24-24, 2022 Streszczenie: The interpenetrating composites consist of a scaffold and metallic matrix, which fills it being introduced under pressure. The scaffold is usually crushable. In our case, the SiC material stands for the skeleton, while the AlSi12 alloy is the matrix. Both materials are crushable. The SiC phase is brittle throughout the loading process, but the AlSi12 alloy is brittle during the elastic phase; then, its behaviour becomes viscous-plastic. The presentation concerns the simulations of impact and fragmentation of metal matrix composite - AlSi12/SiC. The numerical model of the internal structure is created based on CT scanning. The microstructure of the composite is complex and consists of metallic phase (85%), ceramic SiC skeleton, porosity, and system of not perfect interfaces. The impacts are realized in the following few scenarios. The exemplary scenario is realized by imposing the initial conditions on the sample that hits a hard elastic barrier. The second one corresponds to SHPB experiments. The last one is the hitting of an elastic impactor against the sample. The influence of the impact velocities and material parameters of the phases on the failure modes is observed. Previously, analyses of the modes of loading application on the micromechanical failure of metal matrix composite were analysed in [1, 2]. An analysis of the empty SiC scaffolds is presented in [3]. The proposed finite element model of the AlSi12/SiC composite behavior describing gradual degradation under impact loading was tested for different scenarios of hitting. In all cases, the growth of damage in the composite is very realistic. These results lead to the conclusion the proposed finite element model is very effective. Acknowledgment: The results presented in this paper were obtained within the framework of research grant No. 2019/33/B/ST8/01263 financed by the National Science Centre, Poland. The numerical analyses were done in the ICM UW in Warsaw, CYFRONET AGH in Krakow and in CI TASK in Gdańsk, Poland. Słowa kluczowe: Impact, Interpenetrated Ceramic Composites, Fragmentation, Peridynamics Afiliacje autorów:
Postek E. | - | IPPT PAN | Pietras D. | - | Lublin University of Technology (PL) | Guhathakurta J. | - | CT-LAB Stuttgart (DE) | Sadowski T. | - | Lublin University of Technology (PL) |
| 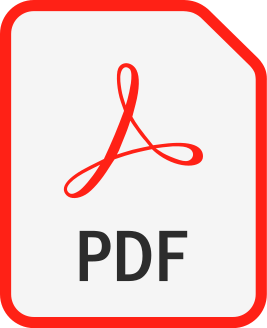 |
4. |
Pietras D.♦, Sadowski T.♦, Postek E., Boniecki M.♦, Tarasiuk J.♦, Badania eksperymentalne kompozytów AlSi/SiC w stanach jednoosiowego rozciągania i ściskania,
PLASTMET 2021, XII Konferencja Naukowa, Zintegrowane Studia Podstaw Deformacji Plastycznej Metali, 2021-11-23/11-26, Łańcut (PL), pp.54-55, 2021 Streszczenie: W pracy przedstawiono badania eksperymentalne kompozytów ceramicznych infiltrowanych poddanych działaniu obciążeń mechanicznych. Rozpatrywany typ kompozytów wytwarzany jest z pianki ceramicznej typu SiC, która wypełniona jest stopem AlSi. Ten typ zaawansowanego kompozytu jest stosowany w przemyśłe kosmicznym, lotniczym i samochodowym.
Przeprowadzono obserwacje mikroskopowe struktury badanych kompozytów oraz pianki ceramicznej, wykonano skany micro-CT.
Odpowiedź na obciążenia dynamiczne zbadano prętem Hopkinsona używając próbek krępych.
Uzyskane wyniki pokazują postacie zniszczenia próbek cylindrycznych i beleczek. Wskazują one na istotny wpływ szkieletu ceramicznego na zachowanie kompozytu.
The experimental testing of interpenetrating composite was presented for uniaxial compression or tension. The analysed composite was manufactured using SiC ceramic foaminfiltrated by an alloy of AlSi. This type of composites is used in cosmic, aerospace, or automotive idustries.
The response of the rested material waas investigated using stocky samples in the Hopkinson bar device.
The obtained results exhibit different modes of fracture of cylindrical and beam samples. They indicate the substantial influence of the ceramic skeleton on the behaviour of the composite under the dynamic loading.
Słowa kluczowe: Kompozyty metalowo ceramiczne, kompozyty infiltrowane, skany CT, pręt Hopkinsona, dynamika, pękanie zniszczenie / Metal matrix composites, infiltrated composites, CT scanning, Hopkinson bar, dynamics, fracture, failure Afiliacje autorów:
Pietras D. | - | Lublin University of Technology (PL) | Sadowski T. | - | Lublin University of Technology (PL) | Postek E. | - | IPPT PAN | Boniecki M. | - | Institute of Electronic Materials Technology (PL) | Tarasiuk J. | - | inna afiliacja |
| 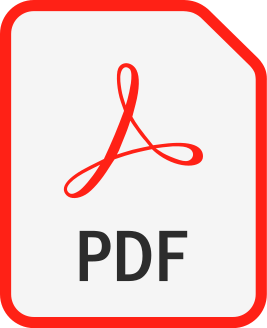 |
5. |
Postek E., Sadowski T.♦, Pietras D.♦, Uderzenie interpenetrowanego kompozytu Al/SiC,
PLASTMET 2021, XII Konferencja Naukowa, Zintegrowane Studia Podstaw Deformacji Plastycznej Metali, 2021-11-23/11-26, Łańcut (PL), pp.57-58, 2021 Streszczenie: Kompozyty ceramiczne infiltrowane (IPC) znajdują zastosowanie w kilku strategicznie ważnych gałęziach przemysłu. Przykładami są przemysł motoryzacyjny, energetyka jądrowa lub przemysł kosmiczny. Badany kompozyt składa się ze szkieletu SiC i wypełnienia stopem aluminium. Próbki poddawane są mechanicznemu obciążeniu udarowemu. Dla materiału kruchego zastosowany został konstytutywny model uszkodzeń zaś materiał wypełnienia jest modelowany jako sprężysto-plastyczny. Do obliczeń zastosowana została perydynamika. Ważnym parametrem jest uwzględniana w obliczeniach odporność na pękanie materiału szkieletu. Zbadane zostało zachowanie próbki dla małych i dużych prędkości uderzenia. Ostatnia uwaga dotycząca metody peridynamiki dotyczy jej praktycznego wykorzystania, a mianowicie wyniki badań numerycznych potwierdzają stosowalność metody do oceny materiałów IPC, mimo że metoda ta powinna być używana przy zastosowaniu masowo zrównoleglonego oprogramowania i nowoczesnych klastrów komputerowych by uzyskiwać wyniki w rozsądnym czasie.
Infiltrated ceramic composites (IPCs) are used in several strategically important
industries. Examples are the automotive industry, nuclear Energy, or the space industry. The
tested composite consists of a SiC skeleton and an aluminum alloy filling. The samples are
subjected to impact loading. For the brittle material, a constitutive model of damage has been
used, and the filling material is modeled as elastic-plastic. Peridynamics was used for the
calculations. A final remark considering the peridynamics method concerns the practical use of
peridynarnics, namely, the results of the numerical studies confirm the feasibility of the method
for evaluation of the IPCs materials even though it should be used massively parallelized
software and up-to-date computer clusters to obtain results within a reasonable time.
Słowa kluczowe: kompozyty metalowo-ceramiczne, kompozyty interpenetrowane, uderzenie, perydynamika / metal matrix composites, interpenetrated composites, impact, peridynamics Afiliacje autorów:
Postek E. | - | IPPT PAN | Sadowski T. | - | Lublin University of Technology (PL) | Pietras D. | - | Lublin University of Technology (PL) |
| 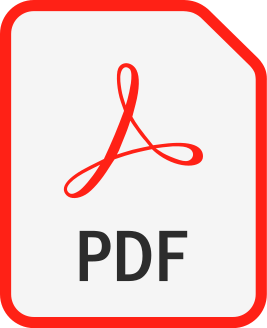 |
6. |
Sadowski T.♦, Postek E., Pietras D.♦, Gieleta R.♦, Kruszka L.♦, Non-linear dynamic and quasi-static responses of two-phase ceramic matrix and metal matrix composites subjected to compression and degradation,
ICTAM2021, 25th International Congress of Theoretical and Applied Mechanics, 2021-08-22/08-27, Mediolan (virtual) (IT), pp.257-258, 2021 Streszczenie: The paper presents modelling and experimental testing of non-linear degradation processes developing in the two-phase ceramic matrix (CMCs) and metal matrix composites (MMCs) subjected to quasi-static and dynamic compressive loading. Modelling was performed by a multiscale approach using both: (1) analytical and (2) numerical methods and selected Representative Volume Elements (RVE) based on SEM observations of composites. Both quasi-static and dynamic experimental tests were done applying standard MTS (100 kN) servo-hydraulic machine and Split Hopkinson Pressure Bar (SHPB) stand for impact tests with loading velocities 20 – 30 m/s. As a result, we observed for CMCs in quasi-static loading failure mode by splitting of cylindrical samples, whereas for impact loading dynamic crushing process took place. Słowa kluczowe: metal-matrix composites, dynamic testing, Split Hopkinson Pressure Bar, peridynamics Afiliacje autorów:
Sadowski T. | - | Lublin University of Technology (PL) | Postek E. | - | IPPT PAN | Pietras D. | - | Lublin University of Technology (PL) | Gieleta R. | - | inna afiliacja | Kruszka L. | - | Military University of Technology (PL) |
| 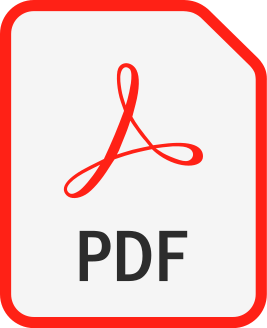 |
7. |
Sadowski T.♦, Postek E., Pietras D.♦, Boniecki M.♦, Szutkowska M.♦, Description of quasi-static and dynamic damage processes in 2-phase ceramic matrix and metal matrix composites reinforced by ceramic grains,
ACE-X 2021, 14th INTERNATIONAL CONFERENCE ON ADVANCED COMPUTATIONAL ENGINEERING AND EXPERIMENTING - ACE-X 2021, 2021-07-04/07-08, St. Julian's (MT), pp.9-10, 2021 Streszczenie: Quasi-static degradation of brittle composites exhibits different mechanical responses under uniaxial tension and uniaxial compression. In this paper, we analysed cracking processes and failure under quasi-static loading of 2 phase ceramic material made of alumina and zirconia mixture, subjected to tension and compression. Constitutive modelling of two-phase ceramic composites obeys description of (1) elastic deformations of initially porous material, (2) limited plasticity and (3) cracks initiation and propagation. Modelling of polycrystalline ceramics at the mesoscopic level under mechanical loading is related to the analysis of a set of grains, which create a so-called Representative Volume Element (RVE). The basic elements of the defect structure inside polycrystal are: micro- and meso-cracks, kinked and wing cracks. To get the macroscopic response of the material one can calculate averaged values of stress and strain over the RSE with the application of an analytical approach. The dynamic degradation process was illustrated for 2 phase ceramic matrix composite and cermet, which was subjected to short compressive impulse. The pulse duration was 10-7s and the applied pressure level - 480 MPa. In the proposed, more advanced finite element formulation of the cermet behaviour is was necessary to take into account the following data and phenomena revealing inside of the RVE: (1) spatial distribution of the cermet constituents, (2) system of grain boundaries/binder interfaces modelled by interface elements, (3) rotation of brittle grains. The cermet response due to pulse loading is significantly different in comparison to the quasi-static behaviour, i.e. the stress distributions and microcracking processes are quite different. Słowa kluczowe: cermets, dynamic behaviour, brittle cracking Afiliacje autorów:
Sadowski T. | - | Lublin University of Technology (PL) | Postek E. | - | IPPT PAN | Pietras D. | - | Lublin University of Technology (PL) | Boniecki M. | - | Institute of Electronic Materials Technology (PL) | Szutkowska M. | - | Institute of Advanced Manufacturing Technology (PL) |
| 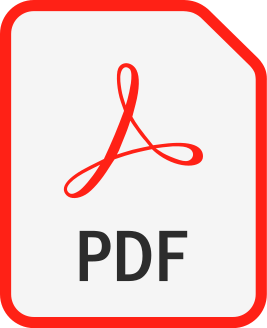 |
8. |
Sadowski T.♦, Pietras D.♦, Postek E., Experimental testing and of modelling of gradual degradation of Al2O3/ZrO2 ceramic composite under slow and high strain rates,
ICCS23, ICCS23 - 23rd International Conference on Composite Structures & MECHCOMP6 - 6th International Conference on Mechanics of Composites, 2020-09-01/09-04, Porto (PT), pp.143-143, 2020 Streszczenie: Gradual degradation of brittle composites exhibits different mechanical response under uniaxial tension and uniaxial compression. In this paper, we analysed cracking processes and failure under quasi-static loading of 2 phase ceramic material made of Al2O3 and ZrO2 mixture, subjected to tension and compression. Constitutive modelling of two-phase ceramic composites obeys description of (1) elastic deformations of initially porous material, (2) limited plasticity and (3) cracks initiation and propagation. Modelling of polycrystalline ceramics at the mesoscopic level under mechanical loading is related to the analysis of a set of grains, i.e. Representative Volume Element (RVE). The basic elements of the defect structure inside polycrystal are micro-cracks and meso-cracks, kinked and wing cracks. To get a macroscopic response of the material one can calculate averaged values of stress and strain over the RSE with an application of the analytical approach. High strain rate degradation process was illustrated for Al2O3/ZrO2 composite, which was subjected to short compressive impulse. The pulse duration was 10-7s. In the proposed more advanced finite elements formulation it was necessary to take into account the following data and phenomena appearing inside of the RVE: (1) spatial distribution of the composite constituents, (2) system of grain boundaries/binder interfaces modelled by interface elements, (3) rotation of brittle grains. The numerical model of gradual degradation of the Al2O3//ZrO2 composite response due to pulse compressive loading presents correctness and capability of the proposed FEM approach. Słowa kluczowe: brittle composites, representative volume element, degradation, damage, peridynamics Afiliacje autorów:
Sadowski T. | - | Lublin University of Technology (PL) | Pietras D. | - | Lublin University of Technology (PL) | Postek E. | - | IPPT PAN |
| 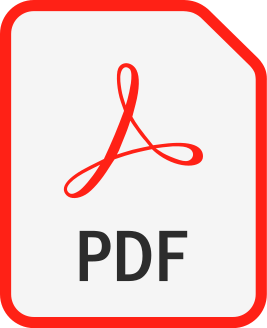 |
9. |
Sadowski T.♦, Postek E., Pietras D.♦, Boniecki M.♦, Szutkowska M.♦, Modelling of Quasi-static and Dynamic Damage Process in Ceramic Matrix Composites,
MECHCOMP 2019, 5th International Conference on Mechanics of Composites, 2019-07-01/07-04, Lizbona (PT), pp.80-81, 2019 Streszczenie: Quasi-static degradation of brittle composites exhibits different mechanical response under uniaxial tension and uniaxial compression. In this paper we analysed cracking processes and failure under quasi-static loading of 2 phase ceramic material made of alumina and zirconia mixture, subjected to tension and compression. Constitutive modelling of two phase ceramic composites obeys description of: (1) elastic deformations of initially porous material, (2) limited plasticity and (3) cracks initiation and propagation. Modelling of polycrystalline ceramics at mesoscopic level under mechanical loading is related to analysis of a set of grains, which create so called Representative Volume Element (RVE). The basic elements of the defect structure inside polycrystal are: micro- and meso-cracks, kinked and wing cracks. To get macroscopic response of the material one can calculate averaged values of stress and strain over the RSE with application of analytical approach. Dynamic degradation process was illustrated for 2 phase ceramic matix composite and cermet, which was subjected to short compressive impulse.
The pulse duration was 10-7s and the applied pressure level - 480 MPa. In the proposed more advanced nite elements formulation of the cermet behaviour is was necessary to take into account the following data and phenomena revealing inside of the RVE: (1) spatial distribution of the cermet constituents, (2) system of grain boundaries/binder interfaces modelled by interface elemnets, (3) rotation of brittle grains. The cermet response due to pulse loading is signifcantly different in comparison to the quasistatic behaviour, i.e. the stress distributions and microcracking processes are quite different. Słowa kluczowe: brittle composites, damage, quasi-static behaviour, dynamics, RVE Afiliacje autorów:
Sadowski T. | - | Lublin University of Technology (PL) | Postek E. | - | IPPT PAN | Pietras D. | - | Lublin University of Technology (PL) | Boniecki M. | - | Institute of Electronic Materials Technology (PL) | Szutkowska M. | - | Institute of Advanced Manufacturing Technology (PL) |
| 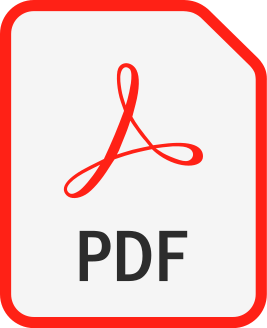 |