1. |
Haponova O., Tarelnyk V.♦, Tarelnyk N.♦, Kurp P.♦, The Formation of C-S Coatings by Electrospark Alloying with the Use Special Process Media,
Solid State Phenomena, ISSN: 1662-9779, DOI: 10.4028/p-5KfyZQ, Vol.355, pp.85-93, 2024 Streszczenie: The paper presents an analysis of technologies for improving the quality parameters of the surface layers of parts, which were carried out by the method of electrospark alloying (ESA) and by additional saturation of surfaces with alloying elements from special process media (STM). The technology of sulfocementation was considered. Metallographic and hardness tests after sulfocementation by ESA showed that the treated surface consists of layers: "soft", hardened and base metal. As the discharge energy increases, the thickness, microhardness and integrity of the coating increase. The presence of sulfur in STM promotes the sulfidation process. It is shown that sulfur accumulates on the surface of the metal at a depth of up to 30 μm. This zone is characterized by reduced microhardness. A strengthened layer is formed under this layer, it has an increased carbon content and high microhardness. Słowa kluczowe: electro-spark alloying, special technological environment, coating, sulfocementation, microstructure, microhardness Afiliacje autorów:
Haponova O. | - | IPPT PAN | Tarelnyk V. | - | Sumy National Agrarian University (UA) | Tarelnyk N. | - | Sumy National Agrarian University (UA) | Kurp P. | - | Kielce University of Technology (PL) |
| 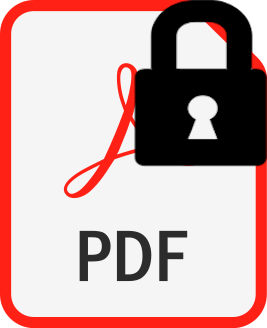 |
2. |
Kurp P.♦, Danielewski H.♦, Szwed B.♦, Borkowski K.♦, Zrak A.♦, Haponova O.♦, Discussion about Metal Expansion Joints Manufacturing Technology of Preventing Thermal Deformation Pipelines Intended for the Fluids Transport,
Communications - Scientific Letters of the University of Žilina, ISSN: 1335-4205, DOI: 10.26552/com.C.2023.030, Vol.25, No.2, pp.111-117, 2023 Streszczenie: In this paper, the authors discuss the method of deformations compensation (resulting from the impact of variable temperatures and pressure) in pipelines intended for fluids transport (liquids and gases). Classical methods of compensation through the so-called "natural compensation" and using special devices called expansion joints. In this paper authors present research work on a new type of the metal expansion joints, called bellow-lens expansion joints. The mechanically assisted laser forming method, which was used to manufacture the bellow-lens expansion joints, was presented. The method uses CO2 laser radiation to heat the element from which the expansion joint will be made and the proprietary system consists of an actuator and swivel handle. Słowa kluczowe: metal expansion joints, laser forming, pipelines compensating, pipelines thermal deformation Afiliacje autorów:
Kurp P. | - | Kielce University of Technology (PL) | Danielewski H. | - | inna afiliacja | Szwed B. | - | inna afiliacja | Borkowski K. | - | inna afiliacja | Zrak A. | - | inna afiliacja | Haponova O. | - | inna afiliacja |
| 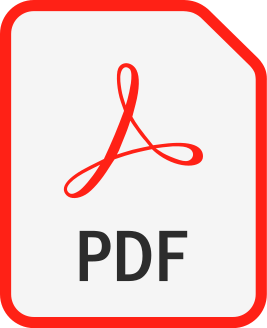 | 70p. |
3. |
Haponova O.♦, Tarelnyk Viacheslav B.♦, Antoszewski B.♦, Radek N.♦, Tarelnyk Nataliia V.♦, Kurp P.♦, Myslyvchenko Oleksandr M.♦, Hoffman J., Technological Features for Controlling Steel Part Quality Parameters by the Method of Electrospark Alloying Using Carburezer Containing Nitrogen—Carbon Components,
Materials, ISSN: 1996-1944, DOI: 10.3390/ma15176085, Vol.15, No.6085, pp.1-14, 2022 Streszczenie: A new method of surface modification based on the method of electrospark alloying (ESA) using carburizer containing nitrogen—carbon components for producing coatings is considered. New processes have been proposed that include the step of applying saturating media in the form of paste-like nitrogenous and nitrogenous-carbon components, respectively, onto the surface without waiting for those media to dry, conducting the ESA process with the use of a steel electrode-tool, as well as with a graphite electrode-tool. Before applying the saturating media, an aluminium layer is applied onto the surface with the use of the ESA method at a discharge energy of Wp = 0.13–6.80 J. A saturating medium in the form of a paste was applied to the surfaces of specimens of steel C22 and steel C40. During nitriding, nitrocarburizing and carburization by ESA (CESA) processes, with an increase in the discharge energy (Wp), the thickness, micro hardness and continuity of the “white layer” coatings, as well as the magnitude of the surface roughness, increase due to saturation of the steel surface with nitrogen and/or carbon, high cooling rates, formation of non-equilibrium structures, formation of special phases, etc. In the course of nitriding, nitrocarburizing and CESA processing of steels C22 and C40, preliminary processing with the use of the ESA method by aluminum increases the thickness, microhardness and continuity of the “white layer”, while the roughness changes insignificantly. Analysis of the phase composition indicates that the presence of the aluminum sublayer leads to the formation of the aluminum-containing phases, resulting in a significant increase in the hardness and, in addition, in an increase in the thickness and quality of the surface layers. The proposed methods can be used to strengthen the surface layers of the critical parts and their elements for compressor and pumping equipment Słowa kluczowe: electrospark alloying,coatings,roughness,structure,microhardness,continuity,X-ray diffraction analysis,nitriding,nitrocarburizing,carburization Afiliacje autorów:
Haponova O. | - | inna afiliacja | Tarelnyk Viacheslav B. | - | Sumy National Agrarian University (UA) | Antoszewski B. | - | Kielce University of Technology (PL) | Radek N. | - | inna afiliacja | Tarelnyk Nataliia V. | - | Sumy National Agrarian University (UA) | Kurp P. | - | Kielce University of Technology (PL) | Myslyvchenko Oleksandr M. | - | I. M. Frantsevich Institute for Problems in Materials (UA) | Hoffman J. | - | IPPT PAN |
| 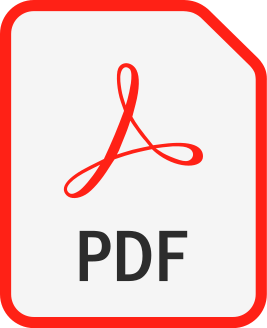 | 140p. |
4. |
Widłaszewski J., Nowak Z., Kurp P.♦, Effect of pre-stress on laser-induced thermoplastic deformation of Inconel 718 beams,
Materials, ISSN: 1996-1944, DOI: 10.3390/ma14081847, Vol.14, No.8, pp.1847-1-18, 2021 Streszczenie: Laser thermal forming is an application of laser heating without any intentional use of external forces. Force-assisted laser bending and laser-assisted bending are hybrid techniques, which combine the use of external forces and local heating to increase the effectiveness of forming. A quantitative description of bending deformation induced by concurrent laser heating and mechanical loading is proposed in this study. Mechanical loading is expressed by the bending moment while the curvature is used to describe the resulting deformation. The contribution of a relatively less known mechanism of laser thermal bending in the hybrid process is identified. The mechanism is able to produce the so-called convex deformation, i.e., bending away from the incident laser beam. Experimental and numerical analysis is performed with thin-walled beams made of Inconel 718 nickel-based superalloy in the factory-annealed state. The Johnson–Cook constitutive material model is used in numerical simulations validated by experimental results. Słowa kluczowe: laser bending, laser-assisted bending, Inconel 718, Johnson–Cook model, curvature Afiliacje autorów:
Widłaszewski J. | - | IPPT PAN | Nowak Z. | - | IPPT PAN | Kurp P. | - | Kielce University of Technology (PL) |
| 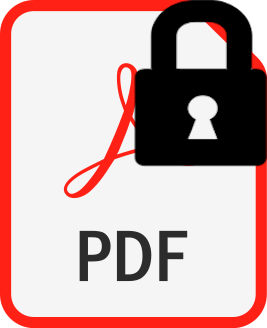 | 140p. |
5. |
Nowak Z., Nowak M., Pęcherski R.B., Wiśniewski K., Widłaszewski J., Kurp P.♦, Computational modeling of thermoplastic behavior of inconel 718 in application to laser-assisted bending of thin-walled tubes,
INTERNATIONAL JOURNAL FOR MULTISCALE COMPUTATIONAL ENGINEERING, ISSN: 1543-1649, DOI: 10.1615/IntJMultCompEng.2019029858, Vol.17, No.3, pp.317-338, 2019 Streszczenie: Laser-assisted tube bending is a promising manufacturing process which enables production of forms and shapes that cannot be obtained by purely mechanical bending. It is particularly suitable for high hardness and brittle materials, such as nickel alloys, ceramics and cast iron. In the current paper, mechanical loading and simultaneous heating by a moving laser beam are used in a controlled manner to obtain the required deformation. Experimental investigation of the Inconel 718 (IN718) alloy provides the basis for identification of parameters of two constitutive models, which encompass softening phenomena and the coupling of temperature and strains. Numerical simulations are conducted to provide more insight into the laser-assisted bending process of the IN718 thin-walled tubes. Temperature, stress and deformation fields are determined in sequentially coupled thermomechanical analyses using the FE code ABAQUS. Laser beam is modeled as a surface heat flux using the dedicated DFLUX procedure. The temperature field is used as a thermal load in the static general step, together with an external mechanical load. The process of tube bending is controlled by the displacement of the piston rod of the actuator, while the thrust force is the resulting value. Słowa kluczowe: laser-assisted bending of tubes, identification of material parameters, numerical simulations Afiliacje autorów:
Nowak Z. | - | IPPT PAN | Nowak M. | - | IPPT PAN | Pęcherski R.B. | - | IPPT PAN | Wiśniewski K. | - | IPPT PAN | Widłaszewski J. | - | IPPT PAN | Kurp P. | - | Kielce University of Technology (PL) |
| 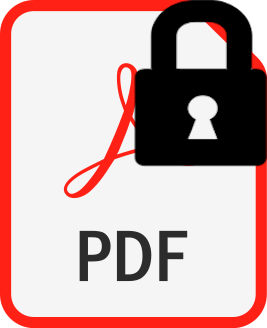 | 40p. |
6. |
Widłaszewski J., Nowak M., Nowak Z., Kurp P.♦, Laser-assisted thermomechanical bending of tube profiles,
ARCHIVES OF METALLURGY AND MATERIALS, ISSN: 1733-3490, DOI: 10.24425/amm.2019.126268, Vol.64, No.1, pp.421-430, 2019 Streszczenie: The subject of the work is the analysis of thermomechanical bending process of a thin-walled tube made of X5CrNi18-10 stainless steel. The deformation is produced at elevated temperature generated with a laser beam in a specially designed experimental setup. The tube bending process consists of local heating of the tube by a moving laser beam and simultaneous kinematic enforcement of deformation with an actuator and a rotating bending arm. During experimental investigations, the resultant force of the actuator and temperature at the laser spot are recorded. In addition to experimental tests, the bending process of the tube was modelled using the finite element method in the ABAQUS program. For this purpose, the tube deformation process was divided into two sequentially coupled numerical simulations. The first one was the heat transfer analysis for a laser beam moving longitudinally over the tube surface. The second simulation described the process of mechanical bending with the time-varying temperature field obtained in the first simulation. The force and temperature recorded during experiments were used to verify the proposed numerical model. The final stress state and the deformation of the tube after the bending process were analyzed using the numerical solution. The results indicate that the proposed bending method can be successfully used in forming of the thin-walled profiles, in particular, when large bending angles and a small spring-back effect are of interest. Słowa kluczowe: laser forming, laser-assisted bending, numerical modelling Afiliacje autorów:
Widłaszewski J. | - | IPPT PAN | Nowak M. | - | IPPT PAN | Nowak Z. | - | IPPT PAN | Kurp P. | - | Kielce University of Technology (PL) |
| 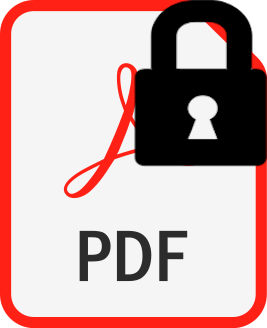 | 40p. |
7. |
Kurp P.♦, Widłaszewski J., Mucha Z.♦, Laserowo-mechaniczne formowanie elementów cienkościennych,
MECHANIK, ISSN: 0025-6552, DOI: 10.17814/mechanik.2018.2.30, Vol.91, No.2, pp.148-151, 2018 Streszczenie: W niniejszym artykule autorzy przedstawiają założenia oraz wstępne wyniki badań doświadczalnych i symulacji numerycznych procesu formowania elementów cienkościennych z wykorzystaniem wiązki laserowej i obciążenia mechanicznego. Na podstawie założeń zaprojektowano i wykonano stanowisko do gięcia cienkościennych rur i dyfuzorów stożkowych stosowanych w budowie silników lotniczych. Metoda i stanowisko kształtowania, przetestowane w warunkach laboratoryjnych, a także wyniki analizy numerycznej procesu pokazują nowe możliwości formowania elementów cienkościennych Słowa kluczowe: kształtowanie laserowe, obróbka laserowa, elementy cienkościenne, stopy niklu, metoda elementów skończonych Afiliacje autorów:
Kurp P. | - | Kielce University of Technology (PL) | Widłaszewski J. | - | IPPT PAN | Mucha Z. | - | inna afiliacja |
| 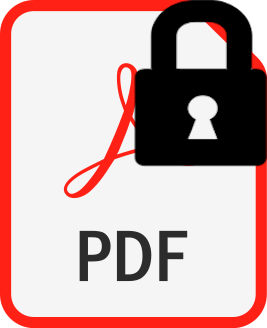 | 11p. |
8. |
Widłaszewski J., Nowak M., Nowak Z., Kurp P.♦, Laser-assisted forming of thin-walled profiles,
Metal Forming, ISSN: 0867-2628, Vol.XXVIII, No.3, pp.183-198, 2017 Streszczenie: Forming processes assisted by localised laser heating are studied in recent years. Heating is used to make it possible or facilitate forming of materials, which exhibit such adverse properties as: brittleness, effects of high work-hardening or a high elastic springback. The hereby presented investigations concern the hybrid thermo-mechanical forming of thin-walled parts using local heating of the material by the laser beam. The research is aimed at forming of parts from materials used in the aviation industry, such as the nickel-base super-alloys Inconel 625, Inconel 718, and also martensitic superalloys AISI 410 and AISI 325. Preliminary investigations are conducted using X5CrNil8-10 (1.4301) stainless steel. Experimental study and numerical simulations cover the behaviour of thin beams 1 mm thick, subjected to mechanical load in the cantilever arrangement and heated by the CO2 laser beam moving from the free end of the sample towards its fixture. The possibility of obtaining large bending deformations relatively easily due to the application of laser beam is demonstrated experimentally. Experimentally verified finite element numerical simulations show the intense plastic flow of the material layer heated by the laser beam. It is accompanied by a shift of the cross-section neutral axis of the beam. Bending of thin-walled tubes in a specially designed device is studied in the next step. It allows introducing mechanical loading in a controlled manner, heating the material by a moving laser beam and forcing the required deformation according to the kinematic scheme of the device. Słowa kluczowe: laser-assisted forming, finite element method, thin-walled structure Afiliacje autorów:
Widłaszewski J. | - | IPPT PAN | Nowak M. | - | IPPT PAN | Nowak Z. | - | IPPT PAN | Kurp P. | - | Kielce University of Technology (PL) |
| 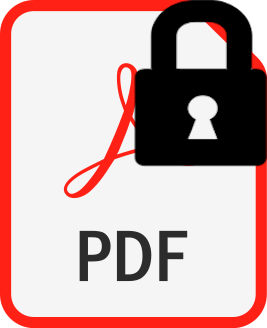 | 10p. |