1. |
Yddal T.♦, Gilja O.H.♦, Cochran S.♦, Postema M.♦, Kotopoulis S.♦, Glass-windowed ultrasound transducers,
Ultrasonics, ISSN: 0041-624X, DOI: 10.1016/j.ultras.2016.02.005, Vol.68, pp.108-119, 2016 Streszczenie: In research and industrial processes, it is increasingly common practice to combine multiple measurement modalities. Nevertheless, experimental tools that allow the co-linear combination of optical and ultrasonic transmission have rarely been reported. The aim of this study was to develop and characterise a water-matched ultrasound transducer architecture using standard components, with a central optical window larger than 10 mm in diameter allowing for optical transmission. The window can be used to place illumination or imaging apparatus such as light guides, miniature cameras, or microscope objectives, simplifying experimental setups.
Four design variations of a basic architecture were fabricated and characterised with the objective to assess whether the variations influence the acoustic output. The basic architecture consisted of a piezoelectric ring and a glass disc, with an aluminium casing. The designs differed in piezoelectric element dimensions: inner diameter, ID = 10 mm, outer diameter, OD = 25 mm, thickness, TH = 4 mm or ID = 20 mm, OD = 40 mm, TH = 5 mm; glass disc dimensions OD = 20–50 mm, TH = 2–4 mm; and details of assembly.
The transducers’ frequency responses were characterised using electrical impedance spectroscopy and pulse-echo measurements, the acoustic propagation pattern using acoustic pressure field scans, the acoustic power output using radiation force balance measurements, and the acoustic pressure using a needle hydrophone. Depending on the design and piezoelectric element dimensions, the resonance frequency was in the range 350–630 kHz, the −6 dB bandwidth was in the range 87–97%, acoustic output power exceeded 1 W, and acoustic pressure exceeded 1 MPa peak-to-peak.
3D stress simulations were performed to predict the isostatic pressure required to induce material failure and 4D acoustic simulations. The pressure simulations indicated that specific design variations could sustain isostatic pressures up to 4.8 MPa.The acoustic simulations were able to predict the behaviour of the fabricated devices. A total of 480 simulations, varying material dimensions (piezoelectric ring ID, glass disc diameter, glass thickness) and drive frequency indicated that the emitted acoustic profile varies nonlinearly with these parameters. Słowa kluczowe: Ultrasound transducer, De-fouling, Optical window, Acoustic field simulation Afiliacje autorów:
Yddal T. | - | Haukeland University Hospital (NO) | Gilja O.H. | - | Haukeland University Hospital (NO) | Cochran S. | - | University of Dundee (GB) | Postema M. | - | inna afiliacja | Kotopoulis S. | - | Haukeland University Hospital (NO) |
| 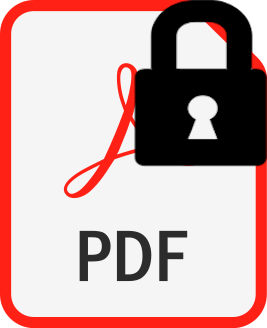 | 30p. |
2. |
Yddal T.♦, Cochran S.♦, Gilja O.H.♦, Postema M.♦, Kotopoulis S.♦, Open-source, high-throughput ultrasound treatment chamber,
Biomedical Engineering-Biomedizinische Technik, ISSN: 1862-278X, DOI: 10.1515/bmt-2014-0046, Vol.60, No.1, pp.77-87, 2015 Streszczenie: Studying the effects of ultrasound on biological cells requires extensive knowledge of both the physical ultrasound and cellular biology. Translating knowledge between these fields can be complicated and time consuming. With the vast range of ultrasonic equipment available, nearly every research group uses different or unique devices. Hence, recreating the experimental conditions and results may be expensive or difficult. For this reason, we have developed devices to combat the common problems seen in state-of-the-art biomedical ultrasound research. In this paper, we present the design, fabrication, and characterisation of an open-source device that is easy to manufacture, allows for parallel sample sonication, and is highly reproducible, with complete acoustic calibration. This device is designed to act as a template for sample sonication experiments. We demonstrate the fabrication technique for devices designed to sonicate 24-well plates and OptiCell™ using three-dimensional (3D) printing and low-cost consumables. We increased the pressure output by electrical impedance matching of the transducers using transmission line transformers, resulting in an increase by a factor of 3.15. The devices cost approximately €220 in consumables, with a major portion attributed to the 3D printing, and can be fabricated in approximately 8 working hours. Our results show that, if our protocol is followed, the mean acoustic output between devices has a variance of <1%. We openly provide the 3D files and operation software allowing any laboratory to fabricate and use these devices at minimal cost and without substantial prior know-how. Słowa kluczowe: Sonoporation, experimentation devices, rapid prototyping, ultrasound transducers Afiliacje autorów:
Yddal T. | - | Haukeland University Hospital (NO) | Cochran S. | - | University of Dundee (GB) | Gilja O.H. | - | Haukeland University Hospital (NO) | Postema M. | - | inna afiliacja | Kotopoulis S. | - | Haukeland University Hospital (NO) |
| 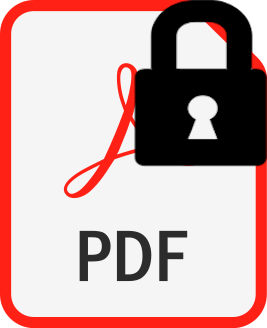 | 15p. |