1. |
Haponova O., Tarelnyk V.♦, Zhylenko T.♦, Tarelnyk N.♦, Vasilenko O.♦, Pavlovskyi S.♦, Improvement of the Quality Parameters of the Surface Layers of Steel Parts after Aluminizing by Electrospark Alloying. Pt. 2. Results of the Influence of the Productivity of Aluminizing by Electrospark Alloying on the Structural State of Steel Surfaces,
Metallofizika i Noveishie Tekhnologii, ISSN: 1024-1809, DOI: 10.15407/mfint.46.04.0313, Vol.46, No.4, pp.313-324, 2024 Streszczenie: In the article, investigation is carried out at the second stage of aluminizing, when a consistent substance containing aluminium powder (the first option) or graphite powder and aluminium powder (the second option) is applied to the surface that has undergone aluminizing at the first stage, before further electrospark alloying with an aluminium electrode, and, regardless of the drying of the consistent substance, the aluminizing process is carried out at a discharge energy of 0.52–2.6 J and a productivity of 1.0–2.0 cm2/min, while the discharge energy and productivity are chosen such that the surface roughness decreases by ≅ 3–4 times. At the second stage aluminizing for both options, when using a consistent substance that contains aluminium powder or aluminium powder and graphite powder, the microhardness of the ‘white layer’ and the diffusion zone are increased (to a greater degree when graphite is present in the consistent substance), the surface roughness is decreased, and the integrity of the coating is of 100%. Before practical implementation, it is recommended to carry out the aluminizing process according to the first option at the discharge energy Wp = 4.6–6.8 J, using a consistent substance containing aluminium powder and graphite powder at the second stage. Słowa kluczowe: electrospark alloying, aluminizing, productivity, surface layer, quality, structure, roughness, microhardness, thickness of the white layer, coating continuity Afiliacje autorów:
Haponova O. | - | IPPT PAN | Tarelnyk V. | - | inna afiliacja | Zhylenko T. | - | inna afiliacja | Tarelnyk N. | - | inna afiliacja | Vasilenko O. | - | inna afiliacja | Pavlovskyi S. | - | inna afiliacja |
| 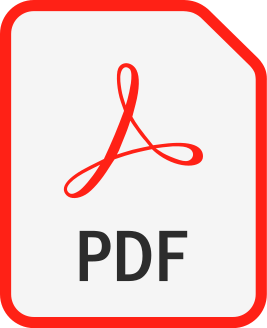 | 40p. |
2. |
Haponova O.♦, Tarelnyk V.♦, Zhylenko T.♦, Tarelnyk N.♦, Sarzhanov O.♦, Melnyk V.♦, Vlasovets V.♦, Pavlovskyy S.♦, Okhrimenko V.♦, Tkachenko A.♦, Improvement of Quality Parameters of Surface Layers of Steel Parts after Aluminizing by Electrospark Alloying. Pt. 1. Features of the Structural State of Steel Surfaces after Aluminizing,
Metallofizika i Noveishie Tekhnologii, ISSN: 1024-1809, DOI: 10.15407/mfint.45.12.1449, Vol.45, No.12, pp.1449-1472, 2023 Streszczenie: The structure formation and properties of the surface layers of steel parts after alloying by traditional technologies and the method of electrospark alloying (ESA) is analysed in the article. As a result of the study of the productivity of the ESA process by aluminium electrode-tool, which is one of the important parameters of the ESA technology, reserves are revealed for improving the quality of the surface layers of steel parts during aluminizing. Two options for reducing productivity in relation to the traditional are studied: the first one, when productivity is reduced by ≅ 2 times; the second one, when performance is reduced by ≅ 4 times. As established, in the first variant, when the discharge energy increases from 0.52 to 6.8 J, at the first stage of aluminizing of steel 20 and steel 40, the thickness of the ‘white’ layer from 20 to 75 and from 25 to 110 μm, respectively; the thickness of the diffusion zone increases from 35 to 120 and from 40 to 140 μm, respectively; the microhardness of the ‘white layer’ increases from 2200 to 7400 and from 2400 to 7450 MPa, respectively; the surface roughness Ra increases from 1.1 to 9.0 and from 1.0 to 8.1 μm, respectively, and the continuity increases from 80 to 100% starting with Wp = 4.6 J and from 60 to 100% at Wp = 6.8 J. In the second variant, when the discharge energy increases from 0.52 to 6.8 J, at the first stage of processing steel 20 and steel 40, the thickness of the ‘white’ layer increases for steel 20 from 25 to 60 μm at Wp = 4.6 J, and then it doesn’t change for steel 40 from 30 to 100 μm; the thickness of the diffusion zone increases from 45 to 130, respectively; the microhardness of the ‘white layer’ increases from 2250 to 7300 and from 2450 to 7300 MPa, respectively; the surface roughness Ra increases from 1.3 to 9.0 and from 1.6 to 8.1 μm, respectively, and the continuity for both steel 20 and steel 40 at Wp = 0.52 J is of 95% and further increases to 100%. Słowa kluczowe: electrospark alloying, aluminizing, productivity, surface layer, structure, roughness, microhardness, thickness of the white layer, coating continuity Afiliacje autorów:
Haponova O. | - | inna afiliacja | Tarelnyk V. | - | inna afiliacja | Zhylenko T. | - | inna afiliacja | Tarelnyk N. | - | inna afiliacja | Sarzhanov O. | - | inna afiliacja | Melnyk V. | - | inna afiliacja | Vlasovets V. | - | inna afiliacja | Pavlovskyy S. | - | inna afiliacja | Okhrimenko V. | - | inna afiliacja | Tkachenko A. | - | inna afiliacja |
| 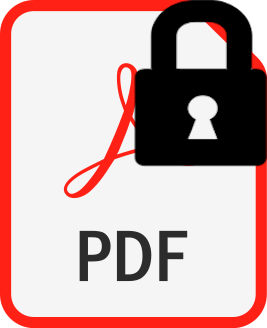 | 40p. |
3. |
Tarelnyk V.♦, Haponova O.♦, Tarelnyk N.♦, Konoplianchenko Y.♦, Bondarev S.♦, Radionov O.♦, Mayfat M.♦, Okhrimenko A.♦, Dumanchuk M.♦, Sirovitskiy K.♦, The Surfaces Properties of Steel Parts with Wear-Resistant Coatings of the 1М and 90% ВК6 + 10% 1M Composition Applied by the Method of Electrospark Alloying with the Use of Special Technological Environments. Pt. 2. Wear Resistance, Topographic and Mechanical Properties,
Metallofizika i Noveishie Tekhnologii, ISSN: 1024-1809, DOI: 10.15407/mfint.45.06.0773, Vol.45, No.6, pp.773-794, 2023 Streszczenie: In the article, as a result of comparative tests, it is established that steel samples with a coating applying the electrospark alloying method (ESA) with a BK6 hard-alloy electrode with the use of a special technological environment (STE) with a composition of 0.5%Si + 0.5%B + 2%Cr + 7%Ni + 90% vaseline, the wear of which after 24 hours of testing is of 221 mg that is 122% less than that for samples without coating and 15% and 31% for samples with coatings applying the nichrome-electrodes’ wire X20H80 using STE composition of 0.5%Si + 0.5%B + 59%BK6 + 40% vaseline and STE composition of 5%Si + 5%B + 90% vaseline, respectively, and by 22% and 47% less than with coatings applying the electrodes made by the method of powder metallurgy (PM), the composition of which is of 90%BK6 + 10%1M and 1M, respectively. For P6M5 steel, better resistance against hydroabrasive wear is possessed by samples with a coating applying the ESA method with an electrode made of hard alloy BK6 using STE composition of 0.5%Si + 0.5%B + 2%Cr + 7%Ni + 90% vaseline, the wear of which after 24 hours of testing is of 188 mg that is 43% less than in samples without coating and by 6% and 15% in samples with a coating applying the ESA method with an electrode made of nichrome wire of the composition X20H80 using STE composition of 0.5%Si + 0.5%B + 59%BK6 + 40% vaseline and STE composition of 5%Si + 5%B + 90% vaseline, and by 24% and 27% less than with coatings applying the electrodes produced by the PM method with a composition of 90%BK6 + 10%1M and 1M, respectively. In ESA with electrodes-tools made both by the PM method and by the new technology of wire X20H80 and hard alloy BK6 and STE, parts made of steel 45 and steel P6M5 have a decrease in the strength limit and yield limit, respectively, and both the relative elongation and the relative narrowing increase. With further abrasive-free ultrasonic finishing (AFUF), both the strength limit and the yield strength increase, and both the relative elongation and the relative narrowing decrease. For practical implementation, wear-resistant coatings formed according to the new technology, using tool electrodes made of X20H80 wire and hard alloy BK6 and STE in two stages with the following AFUF are proposed, the growth of the strength limit and the yield limit of which increase for steel 45 and steel P6M5 by 4.9% and 4.6% and 3.5% and 2.7%, respectively, and relative elongation and relative contraction decrease by 1.7% and 1.3% and 2.0% and 1.7%, respectively. At the same time, the surface roughness is Ra = 1.1 μm, and the integrity is of 100% Słowa kluczowe: electrospark alloying, electrode tool, coating, white layer, microhardness, roughness, integrity Afiliacje autorów:
Tarelnyk V. | - | inna afiliacja | Haponova O. | - | inna afiliacja | Tarelnyk N. | - | inna afiliacja | Konoplianchenko Y. | - | inna afiliacja | Bondarev S. | - | inna afiliacja | Radionov O. | - | inna afiliacja | Mayfat M. | - | inna afiliacja | Okhrimenko A. | - | inna afiliacja | Dumanchuk M. | - | inna afiliacja | Sirovitskiy K. | - | inna afiliacja |
| 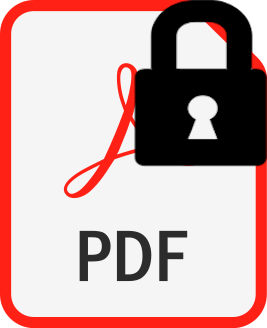 | 40p. |
4. |
Tarelnyk V.♦, Haponova O.♦, Melnyk V.♦, Tarelnyk N.♦, Zubko V.♦, Vlasovets V.♦, Konopliachenko V.♦, Bondarev S.♦, Radionov O.♦, Mayfat M.♦, Okhrimenko V.♦, Tkachenko A.♦, The Surfaces Properties of Steel Parts with Wear-Resistant Coatings of the 1M and 90% BK6 + 10% 1M Composition Applied by the Method of Electrospark Alloying with the Use of Special Technological Environments. Pt. 1. The Strengthened-Surfaces’ Structural State Features,
Metallofizika i Noveishie Tekhnologii, ISSN: 1024-1809, DOI: 10.15407/mfint.45.05.0663, Vol.45, No.5, pp.663-686, 2023 Streszczenie: The article describes a new method of forming the protective coatings of steel parts operating under conditions of abrasive wear both in general mechanical engineering, the composition of which is of 90% ВК6 + 10% 1М, and in industries, where there may be radiation exposure and the composition of 1М (70% Ni, 20% Cr, 5% Si, 5% B), by applying them by the method of electrospark alloying (ESA) with compact electrodes-tools made of nichrome wire X20Н80 and ВК6 hard alloy and using special technological media (STM), which include the necessary alloying elements. As a result of these research, it is established that the surface layers of the 45 and Р6M5 steels after applying wear-resistant coatings have a structure that consists of three areas: the ‘white layer’, the transition zone below, and the base metal. When the discharge energy (Wp) increases from 0.52 to 2.6 J, the thicknesses of the ‘white layer’ and the transition zone, their microhardness and surface roughness increase, but the integrity of the applied coating decreases. The highest microhardness of 9750-12800 and 14250-14600 MPa corresponds to the coating formed on steel 45 and Р6M5, respectively, during ESA by means of both the compact electrodes-tools made of hard alloy ВК6 and the STM with the composition of 0.5% Si + 0.5% B + 2% Cr + 7% Ni + 90% Vaseline. Słowa kluczowe: electrospark alloying, electrode tool, coating, white layer, microhardness, roughness, continuity Afiliacje autorów:
Tarelnyk V. | - | inna afiliacja | Haponova O. | - | inna afiliacja | Melnyk V. | - | inna afiliacja | Tarelnyk N. | - | inna afiliacja | Zubko V. | - | inna afiliacja | Vlasovets V. | - | inna afiliacja | Konopliachenko V. | - | inna afiliacja | Bondarev S. | - | inna afiliacja | Radionov O. | - | inna afiliacja | Mayfat M. | - | inna afiliacja | Okhrimenko V. | - | inna afiliacja | Tkachenko A. | - | inna afiliacja |
| 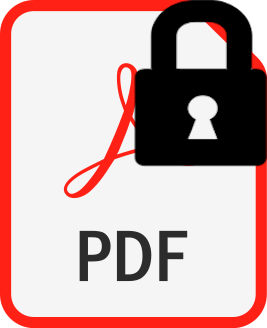 | 40p. |