1. |
Pietrzak K., Jach K.♦, Kaliński D.♦, Chmielewski M.♦, Morgiel J.♦, Processing and Microstructure of Al2O3-Cu Composite Material Interpenetrating Network Type,
Euro PM2011 Congress and Exhibition, 2011-10-09/10-12, Barcelona (ES), Vol.2, pp.1-6, 2011 Streszczenie: Alumina/copper composites have been used where high thermal conductivity, high absorption and dissipation of heat, high resistance to thermal fatigue and good frictional wear resistance are required. This kind of composites may be applied in medicine, electronic and automotive industry. Both the physical and mechanical properties of this type of composites are strongly influenced by the properties of its individual constituents and, also, by the properties of interface layer between ceramic and metal. One of the solution, from the point of view of the best properties’ achievements (especially thermal, structural and shape stability), is the production of ceramic-metal composites with interpenetrating networks structure. They can be produced using porous alumina performs, which are infiltrated (pressure or pressureless) by molten metal or sintered with metallic powders. The subject of the presented paper is the development of the interpenetrating network Al2O3-Cu composites, processed by sintering porous ceramic perform (85 and 90% porosity) with copper powder. The paper presents the new developed technology, results of microstructure investigations, measurements of the selected physical and mechanical properties and the analysis of the influence of the processing conditions on the properties and interface morphology between ceramic and copper Afiliacje autorów:
Pietrzak K. | - | IPPT PAN | Jach K. | - | Institute of Electronic Materials Technology (PL) | Kaliński D. | - | Institute of Electronic Materials Technology (PL) | Chmielewski M. | - | Institute of Electronic Materials Technology (PL) | Morgiel J. | - | Institute of Metallurgy and Materials Science, Polish Academy of Sciences (PL) |
| 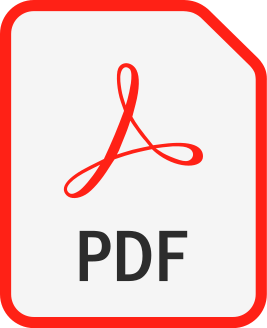 |
2. |
Pietrzak K., Jach K.♦, Kaliński D.♦, Chmielewski M.♦, Improving alumina wettabillity by modification of copper alloys chemical composition,
PM2010, Powder Metallurgy World Congress and Exhibition, 2010-10-10/10-14, Florence (IT), Vol.2, pp.361-367, 2010 | |