1. |
Strojny-Nędza A.♦, Pietrzak K. Z., Jóźwik I.♦, Bucholc B., Wyszkowska E.♦, Kurpaska Ł.♦, Grabias A.♦, Malinowska A.♦, Chmielewski M.♦, Effect of Nitrogen Atmosphere Annealing of Alloyed Powders on the Microstructure and Properties of ODS Ferritic Steels,
Materials, ISSN: 1996-1944, DOI: 10.3390/ma17081743, Vol.17, No.8, pp.1-19, 2024 Streszczenie: Oxide Dispersion Strengthened (ODS) ferritic steels are promising materials for the nuclear power sector. This paper presents the results of a study on the sintering process using the Spark Plasma Sintering (SPS) technique, focusing on ODS ferritic steel powders with different contents (0.3 and 0.6 vol.%) of Y2O3. The novelty lies in the analysis of the effect of pre-annealing treatment on powders previously prepared by mechanical alloying on the microstructure, mechanical, and thermal properties of the sinters. Using the SPS method, it was possible to obtain well-densified sinters with a relative density above 98%. Pre-annealing the powders resulted in an increase in the relative density of the sinters and a slight increase in their thermal conductivity. The use of low electron energies during SEM analysis allowed for a fairly good visualization of the reinforcing oxides uniformly dispersed in the matrix. Analysis of the Mössbauer spectroscopy results revealed that pre-annealing induces local atomic rearrangements within the solid solution. In addition, there was an additional spectral component, indicating the formation of a Cr-based paramagnetic phase. The ODS material with a higher Y2O3 content showed increased Vickers hardness values, as well as increased Young’s modulus and nanohardness, as determined by nanoindentation tests. Słowa kluczowe: spark plasma sintering, ODS ferritic steel, mechanical alloying, Mössbauer spectroscopy, nanoindentation Afiliacje autorów:
Strojny-Nędza A. | - | Institute of Electronic Materials Technology (PL) | Pietrzak K. Z. | - | IPPT PAN | Jóźwik I. | - | Institute of Electronic Materials Technology (PL) | Bucholc B. | - | IPPT PAN | Wyszkowska E. | - | National Centre for Nuclear Research (PL) | Kurpaska Ł. | - | National Centre for Nuclear Research (PL) | Grabias A. | - | Lukasiewicz Institute of Microelectronics and Photonics (PL) | Malinowska A. | - | inna afiliacja | Chmielewski M. | - | Institute of Electronic Materials Technology (PL) |
| 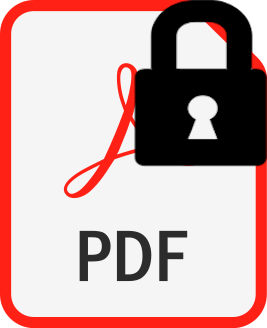 | 140p. |
2. |
Chmielewski M.♦, Zybała R.♦, Strojny-Nędza A.♦, Piątkowska A.♦, Dobrowolski A.P.♦, Jagiełło J.♦, Diduszko R.♦, Bazarnik P.♦, Nosewicz S., Microstructural Evolution of Ni-SiC Composites Manufactured by Spark Plasma Sintering,
METALLURGICAL AND MATERIALS TRANSACTIONS A-PHYSICAL METALLURGY AND MATERIALS SCIENCE, ISSN: 1073-5623, DOI: 10.1007/s11661-023-06999-w, Vol.54, No.-, pp.2191-2207, 2023 Streszczenie: The presented paper concerns the technological aspects of the interface evolution in the nickel-silicon carbide composite during the sintering process. The goal of our investigation was to analyse the material changes occurring due to the violent reaction between nickel and silicon carbide at elevated temperatures. The nickel matrix composite with 20 vol pct SiC particles as the reinforcing phase was fabricated by the spark plasma sintering technique. The sintering tests were conducted with variable process conditions (temperature, time, and pressure). It was revealed that the strong interaction between the individual components and the scale of the observed changes depends on the sintering parameters. To identify the microstructural evolution, scanning electron microscopy, energy dispersive spectroscopy, transmission electron microscopy, X-ray diffraction, and Raman spectroscopy were used. The silicon carbide decomposition process progresses with the extension of the sintering time. As the final product of the observed reaction, new phases from the Ni-Si system and free carbon were detected. The step-by-step materials evolution allowed us to reveal the course of the reaction and the creation of the new structure, especially in the reaction zone. The detailed analysis of the SiC decomposition and formation of new components was the main achievement of the presented paper. Afiliacje autorów:
Chmielewski M. | - | Institute of Electronic Materials Technology (PL) | Zybała R. | - | Politechnika Warszawska (PL) | Strojny-Nędza A. | - | Institute of Electronic Materials Technology (PL) | Piątkowska A. | - | Institute of Electronic Materials Technology (PL) | Dobrowolski A.P. | - | Military University of Technology (PL) | Jagiełło J. | - | inna afiliacja | Diduszko R. | - | Tele and Radio Research Institute (PL) | Bazarnik P. | - | Politechnika Warszawska (PL) | Nosewicz S. | - | IPPT PAN |
| 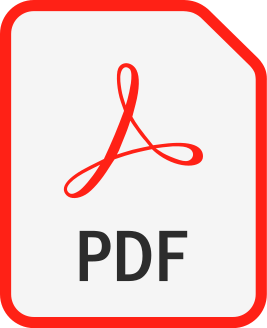 | 200p. |
3. |
Kowiorski K.♦, Heljak M.♦, Strojny-Nędza A.♦, Bucholc B., Chmielewski M.♦, Djas M.♦, Kaszyca K.♦, Zybała R.♦, Małek M.♦, Swieszkowski W.♦, Chlanda A.♦, Compositing graphene oxide with carbon fibers enables improved dynamical thermomechanical behavior of papers produced at a large scale,
, DOI: 10.1016/j.carbon.2023.02.009, Vol.206, pp.26-36, 2023 Streszczenie: This article discusses the morphology and thermomechanical properties of graphene oxide (GO) paper sheets and GO paper composites reinforced with carbon fibers. GO paper was fabricated using GO paste obtained by the condensation of GO aqueous solution synthesized using the Hummers' method. Carbon fibers were implemented to improve the mechanical properties of the pristine GO paper. All the investigated papers were subjected to thermal treatment to check thermo-related morphological and mechanical properties. The results presented in this study allowed for the deeper insight into morphological, structural, and mechanical volume and surface-related properties of pristine GO and GO-based composite materials reinforced with carbon fibers. We showed that there are two important factors that should be taken into consideration for the design and fabrication of GO-based papers. These factors were the concentration of the reinforcing agent and the thermal reduction of the papers. Both factors have influenced the final properties of the resulting GO-based papers. For the first time, it was revealed how the addition of the reinforcing material affects the GO paper thermal expansion coefficient. Słowa kluczowe: Flake graphene, Graphene oxide, Graphene oxide paper, Carbon fibers, Mechanical properties Afiliacje autorów:
Kowiorski K. | - | inna afiliacja | Heljak M. | - | Politechnika Warszawska (PL) | Strojny-Nędza A. | - | Institute of Electronic Materials Technology (PL) | Bucholc B. | - | IPPT PAN | Chmielewski M. | - | Institute of Electronic Materials Technology (PL) | Djas M. | - | inna afiliacja | Kaszyca K. | - | Lukasiewicz Institute of Microelectronics and Photonics (PL) | Zybała R. | - | Politechnika Warszawska (PL) | Małek M. | - | inna afiliacja | Swieszkowski W. | - | inna afiliacja | Chlanda A. | - | Politechnika Warszawska (PL) |
| 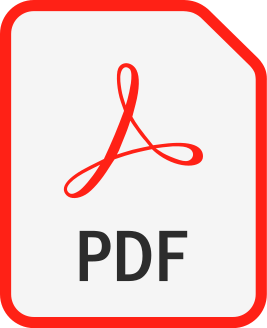 |
4. |
Bochenek K., Węglewski W., Strojny-Nędza A.♦, Pietrzak K., Chmielewski T.♦, Chmielewski M.♦, Basista M., Microstructure, Mechanical, and Wear Properties of NiCr-Re-Al2O3 Coatings Deposited by HVOF, Atmospheric Plasma Spraying, and Laser Cladding,
Journal of Thermal Spray Technology, ISSN: 1059-9630, DOI: 10.1007/s11666-022-01400-5, pp.1-25, 2022 Streszczenie: Metallic coatings are often applied on steel tubes in power generation boilers to improve their performance and extend the lifetime. Besides the high-temperature corrosion and erosion protection, the coatings should manifest good adhesion and cohesion strength, and relatively low residual stresses. In this study, three processing techniques: high velocity oxygen fuel spraying (HVOF), atmospheric plasma spraying (APS), and direct laser cladding were employed to obtain novel NiCr-Re and NiCr-Re-Al2O3 coatings intended for application in combustion boilers. The main objective was to assess the suitability of these three techniques to deposit NiCr-Re and NiCr-Re-Al2O3 composite coatings on a 16Mo3 steel substrate. For this purpose, a comparative analysis of the coatings behavior in selected tests was conducted. Of the three processing techniques, thermal spraying by HVOF turned out to be the optimum choice for the studied coatings. From among several variants of the HVOF-sprayed coatings, namely NiCr+1%Re, NiCr+2%Re, NiCr+1%Re+5%Al2O3, and NiCr+1%Re+10%Al2O3 (all vol.%), the NiCr+1%Re material exhibited the lowest extent of cracking in the disk bend test, the highest tensile strength (405 MPa) in the in-plane tension test, the highest Vickers hardness (379 HV2), the lowest specific wear rate (2.23·10-4 mm3/N m), and the lowest level of average residual tensile stress (120 MPa). Słowa kluczowe: alumina, HVOF, mechanical behavior, nickel-chromium coatings, rhenium, residual stress, wear resistance Afiliacje autorów:
Bochenek K. | - | IPPT PAN | Węglewski W. | - | IPPT PAN | Strojny-Nędza A. | - | Institute of Electronic Materials Technology (PL) | Pietrzak K. | - | IPPT PAN | Chmielewski T. | - | Politechnika Warszawska (PL) | Chmielewski M. | - | Institute of Electronic Materials Technology (PL) | Basista M. | - | IPPT PAN |
| 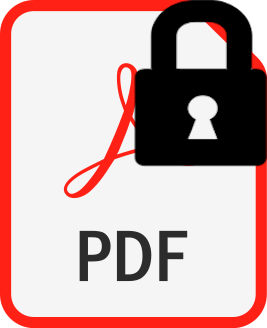 | 140p. |
5. |
Pietrzak K., Gładki A.♦, Strojny-Nędza A.♦, Wejrzanowski T.♦, Kaszyca K.♦, Analysis of uniformity of the distribution of reinforcing phase in Cu/SiC composite materials using mu CT methods,
Image Analysis & Stereology, ISSN: 1580-3139, DOI: 10.5566/ias.1911, Vol.40, No.1, pp.39-47, 2021 Streszczenie: Tomography allows embedding of one space in another, especially ℛ2→ℛ3, and observation of the nature of the volumetric internal composite structure. Now, not only a simple interpretation is expected of geometry defined via single thresholds of structures. The binary segmentation used for numerical struc-ture analysis requires more detailed presentation. This paper shows an example of image analysis tech-niques applied to study the homogeneity of two-phase material. Using tomography analysis, the results of the homogeneity of the SiC particles with 10vol.%, 20vol.%, 30vol.%, 40vol.% volumetric bulk density of Cu/SiC composites are presented. Finally, for two independent coordinate systems, the distribution of SiC particle masses and their total moments of inertia were determined. The results confirmed that for well-mixed composite powders the homogeneity of the reinforcing phase is expected in samples with a SiC volume near 30vol.%. In this case, segregation by translation and rotation of SiC particles in the matrix, during the sintering process is restricted. Słowa kluczowe: Cu/SiC composite materials, image analysis, isotropy, uniformity Afiliacje autorów:
Pietrzak K. | - | IPPT PAN | Gładki A. | - | Institute of Electronic Materials Technology (PL) | Strojny-Nędza A. | - | Institute of Electronic Materials Technology (PL) | Wejrzanowski T. | - | Politechnika Warszawska (PL) | Kaszyca K. | - | Lukasiewicz Institute of Microelectronics and Photonics (PL) |
| 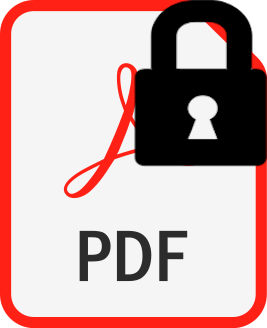 | 70p. |
6. |
Strojny-Nędza A.♦, Pietrzak K., Gili F.♦, Chmielewski M.♦, FGM based on copper–alumina composites for brake disc applications,
ARCHIVES OF CIVIL AND MECHANICAL ENGINEERING, ISSN: 1644-9665, DOI: 10.1007/s43452-020-00079-1, Vol.20, No.3, pp.83-1-13, 2020 Streszczenie: Copper-alumina composites of the interpenetrating networks type are interesting materials for many applications because of their properties. On the base of preliminary investigations and practical works, in order to obtain a material with high resistance to friction wear as well as good dissipation of heat generated during work, it was decided that a developed material would be prepared on the base of the Cu-Al2O3 composite, with a graded composition. In this paper, we present the developed method of manufacturing dense copper–alumina FGMs, using ceramic preform with a graded porosity infiltrated with molten copper. The article also presents the full characterization of the obtained materials and mainly the impact of microstructure on the useful properties. The produced gradient material of a Cu-Al2O3 brake disk underwent tribological tests under conditions resembling real conditions. These disks also went through a series of abrasive wear trials at different operation stages. In comparison with the reference material (i.e., grey cast iron), the obtained gradient materials are characterized by a lower degree of wear when retaining a similar coefficient of friction value due to the ceramic phase addition. Additionally, it was found that using the copper-based gradient material guarantees faster heat dissipation from the contact area. Słowa kluczowe: composites, interpenetrating network materials, functionally gradient materials, brake disc Afiliacje autorów:
Strojny-Nędza A. | - | Institute of Electronic Materials Technology (PL) | Pietrzak K. | - | IPPT PAN | Gili F. | - | inna afiliacja | Chmielewski M. | - | Institute of Electronic Materials Technology (PL) |
| 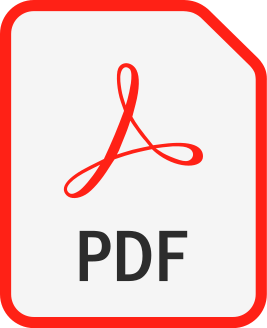 | 140p. |
7. |
Strojny-Nędza A.♦, Egizabal P.♦, Pietrzak K.♦, Zieliński R.♦, Kaszyca K.♦, Piątkowska A.♦, Chmielewski M.♦, Corrosion and thermal shock resistance of metal (Cu, Al) matrix composites reinforced by SiC particles,
BULLETIN OF THE POLISH ACADEMY OF SCIENCES: TECHNICAL SCIENCES, ISSN: 0239-7528, DOI: 10.24425/bpasts.2020.134644, Vol.68, No.5, pp.1227-1236, 2020 Streszczenie: This paper presents the results of studies concerning the production and characterization of Al-SiC/W and Cu-SiC/W composite materials with a 30% volume fraction of reinforcing phase particles as well as the influence of corrosion and thermal shocks on the properties of selected metal matrix composites. Spark plasma sintering method (SPS) was applied for the purpose of producing these materials. In order to avoid the decomposition of SiC surface, SiC powder was coated with a thin tungsten layer using plasma vapour deposition (PVD) method. The obtained results were analysed by the effect of the corrosion and thermal shocks on materials density, hardness, bending strength, tribological and thermal properties. Qualitative X-ray analysis and observation of microstructure of sample surfaces after corrosion tests and thermal shocks were also conducted. The use of PVD technique allows us to obtain an evenly distributed layer of titanium with a constant thickness of 1.5 μm. It was found that adverse environmental conditions and increased temperature result in a change in the material behaviour in wear tests. Słowa kluczowe: metal-matrix composites, silicon carbide, wear resistance, corrosion, thermal shocks Afiliacje autorów:
Strojny-Nędza A. | - | Institute of Electronic Materials Technology (PL) | Egizabal P. | - | Fundacion Tecnalia Research and Innovation (ES) | Pietrzak K. | - | inna afiliacja | Zieliński R. | - | Łukasiewicz Research Network‒Institute of Electronic Materials Technology (PL) | Kaszyca K. | - | Lukasiewicz Institute of Microelectronics and Photonics (PL) | Piątkowska A. | - | Institute of Electronic Materials Technology (PL) | Chmielewski M. | - | Institute of Electronic Materials Technology (PL) |
| 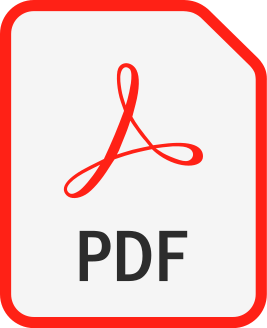 | 100p. |
8. |
Pietrzak K., Strojny-Nędza A.♦, Kaszyca K.♦, Shepa I.♦, Mudra E.♦, Vojtko M.♦, Dusza J.♦, Antal V.♦, Hovancova J.♦, Chmielewski M.♦, Oxidation and corrosion resistance of NiCr-Re and NiCr-Re-Al2O3 materials fabricated by spark plasma sintering,
Metals, ISSN: 2075-4701, DOI: 10.3390/met10081009, Vol.10, No.8, pp.1009-1-12, 2020 Streszczenie: The thermal and oxidation resistance of elements found in the combustion boilers of power generation plants are some of the most important factors deciding their effectiveness. This paper shows the experimental results of the influence of NiCr-based material composition on the microstructure and phase changes occurring during the oxidation and corrosion process. NiCr alloy was modified by the addition of rhenium and aluminum oxide. Materials were densified using the spark plasma sintering method at a sintering temperature of 1050 °C. Oxidation tests conducted up to 1100 °C under synthetic airflow revealed the formation of a thin Cr2O3 layer protecting the material against in-depth oxidation. Results of electrochemical corrosion in a 0.5 M NaCl solution indicated a positive role of Re and Al2O3 addition, confirmed by low corrosion current density values in comparison to the other reference materials. According to the provided positive preliminary test results, we can conclude that a NiCr-Re-Al2O3 system in coating form was successfully obtained by the plasma spraying method. Słowa kluczowe: NiCr, rhenium, aluminium oxide, metal matrix composites, oxidation, corrosion Afiliacje autorów:
Pietrzak K. | - | IPPT PAN | Strojny-Nędza A. | - | Institute of Electronic Materials Technology (PL) | Kaszyca K. | - | Lukasiewicz Institute of Microelectronics and Photonics (PL) | Shepa I. | - | inna afiliacja | Mudra E. | - | inna afiliacja | Vojtko M. | - | inna afiliacja | Dusza J. | - | Institute of Materials Research, Slovak Academy of Sciences (SK) | Antal V. | - | inna afiliacja | Hovancova J. | - | inna afiliacja | Chmielewski M. | - | Institute of Electronic Materials Technology (PL) |
| 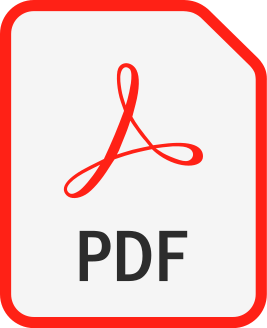 | 70p. |
9. |
Bazarnik P.♦, Nosewicz S., Romelczyk-Baishya B.♦, Chmielewski M.♦, Strojny-Nędza A.♦, Maj J., Huang Y.♦, Lewandowska M.♦, Langdon T.G.♦, Effect of spark plasma sintering and high-pressure torsion on the microstructural and mechanical properties of a Cu–SiC composite,
MATERIALS SCIENCE AND ENGINEERING A-STRUCTURAL MATERIALS PROPERTIES MICROSTRUCTURE AND PROCESSING, ISSN: 0921-5093, DOI: 10.1016/j.msea.2019.138350, Vol.766, pp.138350-1-11, 2019 Streszczenie: This investigation examines the problem of homogenization in metal matrix composites (MMCs) and the methods of increasing their strength using severe plastic deformation (SPD). In this research MMCs of pure copper and silicon carbide were synthesized by spark plasma sintering (SPS) and then further processed via high-pressure torsion (HPT). The microstructures in the sintered and in the deformed materials were investigated using Scanning Electron Microscopy (SEM) and Scanning Transmission Electron Microscopy (STEM). The mechanical properties were evaluated in microhardness tests and in tensile testing. The thermal conductivity of the composites was measured with the use of a laser pulse technique. Microstructural analysis revealed that HPT processing leads to an improved densification of the SPS-produced composites with significant grain refinement in the copper matrix and with fragmentation of the SiC particles and their homogeneous distribution in the copper matrix. The HPT processing of Cu and the Cu–SiC samples enhanced their mechanical properties at the expense of limiting their plasticity. Processing by HPT also had a major influence on the thermal conductivity of materials. It is demonstrated that the deformed samples exhibit higher thermal conductivity than the initial coarse-grained samples. Słowa kluczowe: copper, silicon carbide, high-pressure torsion, spark plasma sintering, thermal conductivity Afiliacje autorów:
Bazarnik P. | - | Politechnika Warszawska (PL) | Nosewicz S. | - | IPPT PAN | Romelczyk-Baishya B. | - | Politechnika Warszawska (PL) | Chmielewski M. | - | Institute of Electronic Materials Technology (PL) | Strojny-Nędza A. | - | Institute of Electronic Materials Technology (PL) | Maj J. | - | IPPT PAN | Huang Y. | - | Bournemouth University (GB) | Lewandowska M. | - | inna afiliacja | Langdon T.G. | - | University of Southampton (GB) |
| 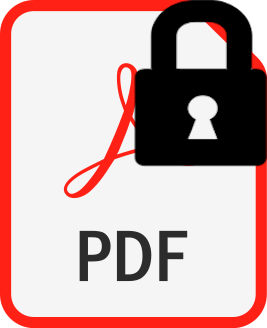 | 140p. |
10. |
Chmielewski M.♦, Nosewicz S., Wyszkowska E.♦, Kurpaska Ł.♦, Strojny-Nędza A.♦, Piątkowska A.♦, Bazarnik P.♦, Pietrzak K., Analysis of the micromechanical properties of copper-silicon carbide composites using nanoindentation measurements,
CERAMICS INTERNATIONAL, ISSN: 0272-8842, DOI: 10.1016/j.ceramint.2019.01.257, Vol.45, No.7A, pp.9164-9173, 2019 Streszczenie: The study presents a detailed analysis of the impact of the coating type of silicon carbide particles and its share by volume on the microstructure and micromechanical properties of Cu-SiC composites. In order to protect the carbide from decomposition during the manufacturing of the composites, the surface of SiC was modified via a plasma vapour deposition technique with a layer of metals (W, Cr, Ti and Ni). Composites with a variable share of the ceramic phase (10–50 %vol.) were obtained at a temperature of 950 °C using spark plasma sintering. An analysis of the structures of the composites, especially in the metal-ceramic boundary region, was conducted with the use of scanning and transmission electron microscopy. The mechanical properties of the composites in the Cu-interface-SiC system were studied via a nanoindentation technique. The comparison of the results of hardness and Young's modulus studies were completed in relation to the actual structures of the materials, which in turn made it possible to determine the impact of the interfacial structure on the global properties of the composite materials. Słowa kluczowe: copper-silicon carbide composites, nanoindentation, SPS, interface study Afiliacje autorów:
Chmielewski M. | - | Institute of Electronic Materials Technology (PL) | Nosewicz S. | - | IPPT PAN | Wyszkowska E. | - | National Centre for Nuclear Research (PL) | Kurpaska Ł. | - | National Centre for Nuclear Research (PL) | Strojny-Nędza A. | - | Institute of Electronic Materials Technology (PL) | Piątkowska A. | - | Institute of Electronic Materials Technology (PL) | Bazarnik P. | - | Politechnika Warszawska (PL) | Pietrzak K. | - | IPPT PAN |
| 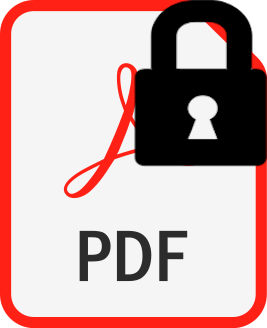 | 100p. |
11. |
Maj J., Basista M., Węglewski W., Bochenek K., Strojny-Nędza A.♦, Naplocha K.♦, Panzner T.♦, Tatarkova M.♦, Fiori F.♦, Effect of microstructure on mechanical properties and residual stresses in interpenetrating aluminum-alumina composites fabricated by squeeze casting,
MATERIALS SCIENCE AND ENGINEERING A-STRUCTURAL MATERIALS PROPERTIES MICROSTRUCTURE AND PROCESSING, ISSN: 0921-5093, DOI: 10.1016/j.msea.2017.12.091, Vol.715, pp.154-162, 2018 Streszczenie: Aluminum-alumina composites with interpenetrating network structure are interesting structural materials due to their high resistance to elevated temperature and frictional wear, good heat conductivity, enhanced mechanical strength and fracture toughness. In this paper aluminum-alumina bulk composites and FGMs are manufactured by pressure infiltration of porous alumina preforms with molten aluminium alloy (EN AC-44200). Influence of the interpenetrating microstructure on the macroscopic bending strength, fracture toughness, hardness and heat conduction is examined. Special focus is on processing-induced thermal residual stresses in aluminium-alumina composites due to their potentially detrimental effects on material performance in structural elements under in-service conditions. The residual stresses are measured experimentally in the ceramic phase by neutron diffraction and simulated numerically using a micro-CT based Finite Element model, which takes into account the actual interpenetrating microstructure of the composite. The model predictions for two different volume fractions of alumina agree fairly well with the neutron diffraction measurements Słowa kluczowe: A. stress measurements, X-ray analysis, finite element analysis, B. composites, C. casting methods Afiliacje autorów:
Maj J. | - | IPPT PAN | Basista M. | - | IPPT PAN | Węglewski W. | - | IPPT PAN | Bochenek K. | - | IPPT PAN | Strojny-Nędza A. | - | Institute of Electronic Materials Technology (PL) | Naplocha K. | - | Wroclaw University of Science and Technology (PL) | Panzner T. | - | Paul Scherrer Institut (CH) | Tatarkova M. | - | Institute of Materials Research, Slovak Academy of Sciences (SK) | Fiori F. | - | Universita Politecnica delle Marche (IT) |
| 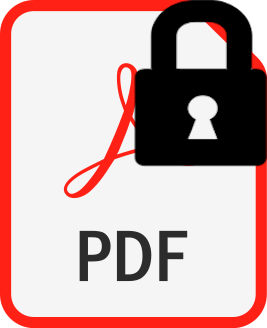 | 35p. |
12. |
Strojny-Nędza A.♦, Pietrzak K.♦, Gładki A.♦, Nosewicz S., Jarząbek D.M., Chmielewski M.♦, The effect of ceramic type reinforcement on structure and properties of Cu-Al2O3 composites,
BULLETIN OF THE POLISH ACADEMY OF SCIENCES: TECHNICAL SCIENCES, ISSN: 0239-7528, DOI: 10.24425/124271, Vol.66, No.4, pp.553-560, 2018 Streszczenie: The purpose of this paper is to elaborate on mechanical alloying conditions for a composite powder consisting of copper and brittle aluminium oxides. Detailed analysis of the Cu-Al2O3 powder mixture structure obtained in the mechanical alloying process allows for the study of the homogenization phenomena and for obtaining grains (in composite form) with a high degree of uniformity. The Cu-5 vol.%Al2O3 composites were obtained by means of the spark plasma sintering technique. The results presented herein were studied and discussed interms of the impact of using a different form of aluminium oxide powder and a different shape of copper powder on composite properties. Research methodology included microstructure analysis as well as its relation to the strength of Cu-Al2O3 interfaces. It transpires from the results presented below that the application of electrocor undum as a reinforcement phase in composites decreases poro sity in the ceramic phase, thus improving thermal properties and interfacial strength. Słowa kluczowe: metal matrix composites, spark plasma sintering, thermal conductivity, interfacial strength Afiliacje autorów:
Strojny-Nędza A. | - | Institute of Electronic Materials Technology (PL) | Pietrzak K. | - | inna afiliacja | Gładki A. | - | Institute of Electronic Materials Technology (PL) | Nosewicz S. | - | IPPT PAN | Jarząbek D.M. | - | IPPT PAN | Chmielewski M. | - | Institute of Electronic Materials Technology (PL) |
| 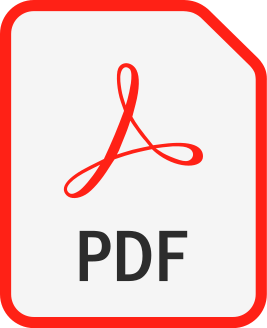 | 25p. |
13. |
Jóźwik I.♦, Strojny-Nędza A.♦, Chmielewski M.♦, Pietrzak K.♦, Kurpaska Ł.♦, Nosewicz S., High resolution SEM characterization of nano-precipitates in ODS steels,
MICROSCOPY RESEARCH AND TECHNIQUE, ISSN: 1059-910X, DOI: 10.1002/jemt.23004, Vol.81, No.5, pp.502-508, 2018 Streszczenie: The performance of the present-day scanning electron microscopy (SEM) extends far beyond delivering electronic images of the surface topography. Oxide dispersion strengthened (ODS) steel is on of the most promising materials for the future nuclear fusion reactor because of its good radiation resistance, and higher operation temperature up to 750°C. The microstructure of ODS should not exceed tens of nm, therefore there is a strong need in a fast and reliable technique for their characterization. In this work, the results of low-kV SEM characterization of nanoprecipitates formed in the ODS matrix are presented. Application of highly sensitive photo-diode BSE detector in SEM imaging allowed for the registration of single nm-sized precipitates in the vicinity of the ODS alloys. The composition of the precipitates has been confirmed by TEM-EDS. Słowa kluczowe: ODS steels, scanning electron microscopy, spark plasma sintering Afiliacje autorów:
Jóźwik I. | - | Institute of Electronic Materials Technology (PL) | Strojny-Nędza A. | - | Institute of Electronic Materials Technology (PL) | Chmielewski M. | - | Institute of Electronic Materials Technology (PL) | Pietrzak K. | - | inna afiliacja | Kurpaska Ł. | - | National Centre for Nuclear Research (PL) | Nosewicz S. | - | IPPT PAN |
| 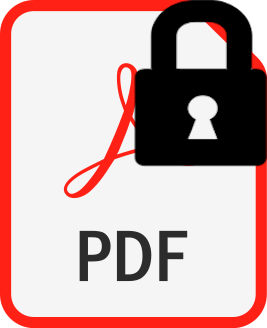 | 25p. |
14. |
Pietrzak K.♦, Strojny-Nędza A.♦, Olesińska W.♦, Bańkowska A.♦, Gładki A.♦, Cu-rGO subsurface layer creation on copper substrate and its resistance to oxidation,
APPLIED SURFACE SCIENCE, ISSN: 0169-4332, DOI: 10.1016/j.apsusc.2016.11.155, Vol.421, pp.228-233, 2017 Streszczenie: On the basis of a specially designed experiment, this paper presents a model, which is an attempt to explain the mechanism of formatting and creating oxidation resistance of Cu-rGO subsurface layers. Practically zero chemical affinity of copper to carbon is a fundamental difficulty in creating composite structures of Cu-C, properties which are theoretically possible to estimate. In order to bind the thermally reduced graphene oxide with copper surface, the effect of structural rebuilding of the copper oxide, in the process of annealing in a nitrogen atmosphere, have been used. On intentionally oxidized and anoxic copper substrates the dispersed graphene oxide (GO) and thermally reduced graphene oxide (rGO) were loaded. Annealing processes after the binding effects of both graphene oxide forms to Cu substrates were tested. The methods for high-resolution electron microscopy were found subsurface rGO-Cu layer having a substantially greater resistance to oxidation than pure copper. The mechanism for the effective resistance to oxidation of the Cu-rGO has been presented in a hypothetical form Słowa kluczowe: Metal matrix composite, Copper, Graphene, Oxidation Afiliacje autorów:
Pietrzak K. | - | inna afiliacja | Strojny-Nędza A. | - | Institute of Electronic Materials Technology (PL) | Olesińska W. | - | Institute of Electronic Materials Technology (PL) | Bańkowska A. | - | Institute of Electronic Materials Technology (PL) | Gładki A. | - | Institute of Electronic Materials Technology (PL) |
| 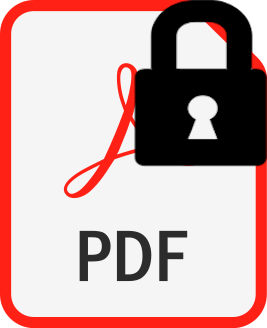 | 35p. |
15. |
Chmielewski M.♦, Pietrzak K.♦, Teodorczyk M.♦, Nosewicz S., Jarząbek D.M., Zybała R.♦, Bazarnik P.♦, Lewandowska M.♦, Strojny-Nędza A.♦, Effect of metallic coating on the properties of copper-silicon carbide composites,
APPLIED SURFACE SCIENCE, ISSN: 0169-4332, DOI: 10.1016/j.apsusc.2016.12.130, Vol.421, pp.159-169, 2017 Streszczenie: In the presented paper a coating of SiC particles with a metallic layer were used to prepare copper matrix composite materials. The role of the layer was to protect the silicon carbide from decomposition and dissolution of silicon in the copper matrix during the sintering process. The SiC particles were covered by chromium, tungsten and titanium using Plasma Vapour Deposition method. After powder mixing of components, the final densification process via Spark Plasma Sintering (SPS) method at temperature 950C was provided. The almost fully dense materials were obtained (> 97.5%). The microstructure of obtained composites was studied using scanning electron microscopy as well as transmission electron microscopy. The microstructural analysis of composites confirmed that regardless of the type of deposited material, there is no evidence for decomposition process of silicon carbide in copper. In order to measure the strength of the interface between ceramic particles and the metal matrix, the micro tensile tests have been performed. Furthermore, thermal diffusivity was measured with the use of the laser pulse technique. In the context of performed studies, the tungsten coating seems to be the most promising solution for heat sink application. Compared to pure composites without metallic layer, Cu-SiC with W coating indicate the higher tensile strength and thermal diffusitivy, irrespective of an amount of SiC reinforcement. The improvement of the composite properties is related to advantageous condition of Cu-SiC interface characterized by well homogenity and low porosity, as well as individual properties of the tungsten coating material. Słowa kluczowe: metal matrix composites, silicon carbide, metallic layers deposition, thermal conductovity, interface strength Afiliacje autorów:
Chmielewski M. | - | Institute of Electronic Materials Technology (PL) | Pietrzak K. | - | inna afiliacja | Teodorczyk M. | - | Institute of Electronic Materials Technology (PL) | Nosewicz S. | - | IPPT PAN | Jarząbek D.M. | - | IPPT PAN | Zybała R. | - | Politechnika Warszawska (PL) | Bazarnik P. | - | Politechnika Warszawska (PL) | Lewandowska M. | - | inna afiliacja | Strojny-Nędza A. | - | Institute of Electronic Materials Technology (PL) |
| 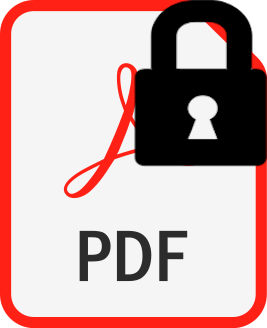 | 35p. |
16. |
Pietrzak K.♦, Gładki A.♦, Frydman K.♦, Wójcik-Grzybek D.♦, Strojny-Nędza A.♦, Wejrzanowski T.♦, Copper-carbon nanoforms composites – processing, microstructure and thermal properties,
ARCHIVES OF METALLURGY AND MATERIALS, ISSN: 1733-3490, DOI: 10.1515/amm-2017-0198, Vol.62, No.2B, pp.1307-1310, 2017 Streszczenie: The main current of publication is focused around the issues and problems associated with the formation of composite materials with Cu matrix and reinforcing phases in the various carbon nanoforms. The core of the research has been focused on thermal conductivity of these composites types. This parameter globally reflects the state of the structure, quality of raw materials and the technology used during the formation of composite materials. Vanishingly low affinity of copper for carbon, multilayered forms of graphene, the existence of critical values of graphene volume in the composite are not conducive to the classic procedures of composites designing. As a result, the expected, significant increase in thermal conductivity of composites is not greater than for pure copper matrix. Present paper especially includes: (i) data of obtaining procedure of copper/graphene mixtures, (ii) data of sintering process, (iii) the results of structure investigations and of thermal properties. Structural analysis revealed the homogenous distribution of graphene in copper matrix, the thermal analysis indicate the existence of carbon phase critical concentration, where improvement of thermal diffusivity to pure copper can occur Słowa kluczowe: metal matrix composite, sintering, copper, graphene, thermal diffusivity Afiliacje autorów:
Pietrzak K. | - | inna afiliacja | Gładki A. | - | Institute of Electronic Materials Technology (PL) | Frydman K. | - | Institute of Electronic Materials Technology (PL) | Wójcik-Grzybek D. | - | Institute of Electronic Materials Technology (PL) | Strojny-Nędza A. | - | Institute of Electronic Materials Technology (PL) | Wejrzanowski T. | - | Politechnika Warszawska (PL) |
| 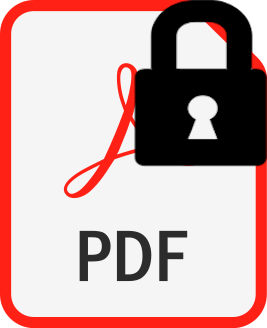 | 30p. |
17. |
Strojny-Nędza A.♦, Pietrzak K.♦, Teodorczyk M.♦, Basista M., Węglewski W., Chmielewski M.♦, Influence of Material Ccating on the heat Transfer in a layered Cu-SiC-Cu Systems,
ARCHIVES OF METALLURGY AND MATERIALS, ISSN: 1733-3490, DOI: 10.1515/amm-2017-0199, Vol.62, No.2B, pp.1311-1314, 2017 Streszczenie: This paper describes the process of obtaining Cu-SiC-Cu systems by way of spark plasma sintering. A monocrystalline form of silicon carbide (6H-SiC type) was applied in the experiment. Additionally, silicon carbide samples were covered with a layer of tungsten and molybdenum using chemical vapour deposition (CVD) technique. Microstructural examinations and thermal properties measurements were performed. A special attention was put to the metal-ceramic interface. During annealing at a high temperature, copper reacts with silicon carbide. To prevent the decomposition of silicon carbide two types of coating (tungsten and molybdenum) were applied. The effect of covering SiC with the aforementioned elements on the composite's thermal conductivity was analyzed. Results were compared with the numerical modelling of heat transfer in Cu-SiC-Cu systems. Certain possible reasons behind differences in measurements and modelling results were discussed. Słowa kluczowe: copper matrix composites, silicon carbide, interface, thermal conductivity, modelling Afiliacje autorów:
Strojny-Nędza A. | - | Institute of Electronic Materials Technology (PL) | Pietrzak K. | - | inna afiliacja | Teodorczyk M. | - | Institute of Electronic Materials Technology (PL) | Basista M. | - | IPPT PAN | Węglewski W. | - | IPPT PAN | Chmielewski M. | - | Institute of Electronic Materials Technology (PL) |
| 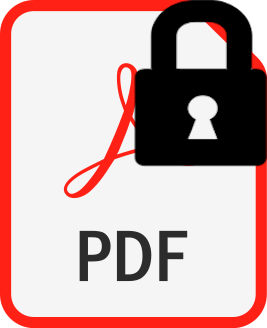 | 30p. |
18. |
Chmielewski M.♦, Pietrzak K.♦, Strojny-Nędza A.♦, Jarząbek D.M., Nosewicz S., Investigations of interface properties in copper-silicon carbide composites,
ARCHIVES OF METALLURGY AND MATERIALS, ISSN: 1733-3490, DOI: 10.1515/amm-2017-0200, Vol.62, No.2B, pp.1315-1318, 2017 Streszczenie: This paper analyses the technological aspects of the interface formation in the copper-silicon carbide composite and its effect on the material's microstructure and properties. Cu-SiC composites with two different volume content of ceramic reinforcement were fabricated by hot pressing (HP) and spark plasma sintering (SPS) technique. In order to protect SiC surface from its decomposition, the powder was coated with a thin tungsten layer using plasma vapour deposition (PVD) method. Microstructural analyses provided by scanning electron microscopy revealed the significant differences at metal-ceramic interface. Adhesion force and fracture strength of the interface between SiC particles and copper matrix were measured. Thermal conductivity of composites was determined using laser flash method. The obtained results are discussed with reference to changes in the area of metal-ceramic boundary. Słowa kluczowe: copper matrix composites, silicon carbide, interface, thermal conductivity, adhesion Afiliacje autorów:
Chmielewski M. | - | Institute of Electronic Materials Technology (PL) | Pietrzak K. | - | inna afiliacja | Strojny-Nędza A. | - | Institute of Electronic Materials Technology (PL) | Jarząbek D.M. | - | IPPT PAN | Nosewicz S. | - | IPPT PAN |
| 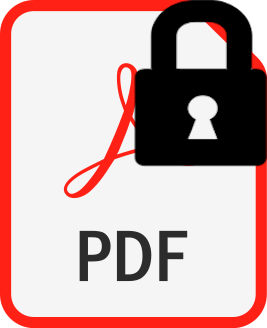 | 30p. |
19. |
Chmielewski M.♦, Pietrzak K.♦, Strojny-Nędza A.♦, Kaszyca K.♦, Zybala R.♦, Bazarnik P.♦, Lewandowska M.♦, Nosewicz S., Microstructure and thermal properties of Cu-SiC composite materials depending on the sintering technique,
SCIENCE OF SINTERING, ISSN: 0350-820X, DOI: 10.2298/SOS1701011C, Vol.49, No.1, pp.11-22, 2017 Streszczenie: The presented paper investigates the relationship between the microstructure and thermal properties of copper–silicon carbide composites obtained through hot pressing (HP) and spark plasma sintering (SPS) techniques. The microstructural analysis showed a better densification in the case of composites sintered in the SPS process. TEM investigations revealed the presence of silicon in the area of metallic matrix in the region close to metal ceramic boundary. It is the product of silicon dissolving process in copper occurring at an elevated temperature. The Cu-SiC interface is significantly defected in composites obtained through the hot pressing method, which has a major influence on the thermal conductivity of materials. Słowa kluczowe: metal matrix composites, silicon carbide, interface, spark plasma sintering, thermal conductivity Afiliacje autorów:
Chmielewski M. | - | Institute of Electronic Materials Technology (PL) | Pietrzak K. | - | inna afiliacja | Strojny-Nędza A. | - | Institute of Electronic Materials Technology (PL) | Kaszyca K. | - | Lukasiewicz Institute of Microelectronics and Photonics (PL) | Zybala R. | - | Politechnika Warszawska (PL) | Bazarnik P. | - | Politechnika Warszawska (PL) | Lewandowska M. | - | inna afiliacja | Nosewicz S. | - | IPPT PAN |
| 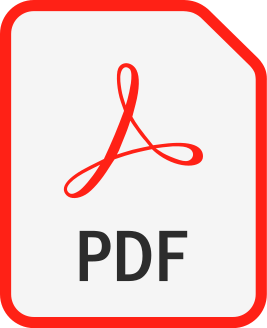 | 30p. |
20. |
Wejrzanowski T.♦, Grybczuk M.♦, Chmielewski M.♦, Pietrzak K.♦, Kurzydłowski K.J.♦, Strojny-Nędza A.♦, Thermal conductivity of metal-graphene composites,
MATERIALS AND DESIGN, ISSN: 0264-1275, DOI: 10.1016/j.matdes.2016.03.069, Vol.99, pp.163-173, 2016 Streszczenie: In this paper the results of numerical simulations and experimental studies are presented which describe potential and limitation of applications of single-layer (SLG) and multi-layer (MLG) graphene for thermal conductivity enhancement (TCE) of copper. A series of composite structures were studied which are representative of most widely used systems. The influence of structural parameters on the macroscopic thermal conductivity was analyzed, both experimentally and by numerical simulations. Analytical and Finite Element Method modeling were carried out to investigate a wide range of phenomena, including the effect of copper-MLG interface, copper grain size, volume fraction, thickness and orientation of MLG platelets as well as spatial distribution of MLG defined by percolation factor. Both modeling and the experimental results show that the volume fraction of MLG regions, their size, orientation and spatial distribution may significantly affect the thermal conductivity of metal matrix composites. TCE can be obtained for the laminate-like structure or particulate composites with highly aligned MLG regions. The thermal conductivity of such composites is strongly anisotropic and enhanced in the direction perpendicular to the layers. The results obtained in this study predict that SLG will have a negative effect on the thermal conductivity of copper matrix composites. Słowa kluczowe: Thermal conductivity, Composites, Graphene, Finite element method Afiliacje autorów:
Wejrzanowski T. | - | Politechnika Warszawska (PL) | Grybczuk M. | - | inna afiliacja | Chmielewski M. | - | Institute of Electronic Materials Technology (PL) | Pietrzak K. | - | inna afiliacja | Kurzydłowski K.J. | - | Politechnika Warszawska (PL) | Strojny-Nędza A. | - | Institute of Electronic Materials Technology (PL) |
| 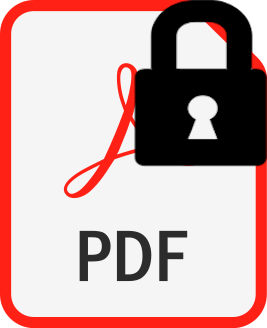 | 35p. |
21. |
Pietrzak K.♦, Sobczak N.♦, Chmielewski M.♦, Homa M.♦, Gazda A.♦, Zybała R.♦, Strojny-Nędza A.♦, Effects of Carbon Allotropic Forms on Microstructure and Thermal Properties of Cu-C Composites Produced by SPS,
Journal of Materials Engineering and Performance, ISSN: 1059-9495, DOI: 10.1007/s11665-015-1851-0, Vol.25, No.8, pp.3077-3083, 2016 Streszczenie: Combination of extreme service conditions and complex thermomechanical loadings, e.g., in electronics or power industry, requires using advanced materials with unique properties. Dissipation of heat generated during the operation of high-power electronic elements is crucial from the point of view of their efficiency. Good cooling conditions can be guaranteed, for instance, with materials of very high thermal conductivity and low thermal expansion coefficient, and by designing the heat dissipation system in an accurate manner. Conventional materials such as silver, copper, or their alloys, often fail to meet such severe requirements. This paper discusses the results of investigations connected with Cu-C (multiwall carbon nanotubes (MWNTs), graphene nanopowder (GNP), or thermally reduced graphene oxide (RGO)) composites, produced using the spark plasma sintering technique. The obtained composites are characterized by uniform distribution of a carbon phase and high relative density. Compared with pure copper, developed materials are characterized by similar thermal conductivity and much lower values of thermal expansion coefficient. The most promising materials to use as heat dissipation elements seems to be copper-based composites reinforced by carbon nanotubes (CNTs) and GNP. Słowa kluczowe: copper matrix composites, graphene, spark plasma sintering, thermal properties Afiliacje autorów:
Pietrzak K. | - | inna afiliacja | Sobczak N. | - | Foundry Research Institute (PL) | Chmielewski M. | - | Institute of Electronic Materials Technology (PL) | Homa M. | - | Foundry Research Institute (PL) | Gazda A. | - | Foundry Research Institute (PL) | Zybała R. | - | Politechnika Warszawska (PL) | Strojny-Nędza A. | - | Institute of Electronic Materials Technology (PL) |
| 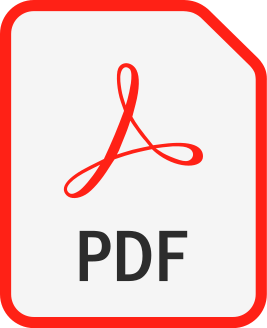 | 20p. |
22. |
Strojny-Nędza A.♦, Pietrzak K.♦, Węglewski W., The Influence of Al2O3 Powder Morphology on the Properties of Cu-Al2O3 Composites Designed for Functionally Graded Materials (FGM),
Journal of Materials Engineering and Performance, ISSN: 1059-9495, DOI: 10.1007/s11665-016-2204-3, Vol.25, No.8, pp.3173-3184, 2016 Streszczenie: In order to meet the requirements of an increased efficiency applying to modern devices and in more general terms science and technology, it is necessary to develop new materials. Combining various types of materials (such as metals and ceramics) and developing composite materials seem to be suitable solutions. One of the most interesting materials includes Cu-Al2O3 composite and gradient materials (FGMs). Due to their potential properties, copper-alumina composites could be used in aerospace industry as rocket thrusters and components in aircraft engines. The main challenge posed by copper matrix composites reinforced by aluminum oxide particles is obtaining the uniform structure with no residual porosity (existing within the area of the ceramic phase). In the present paper, Cu-Al2O3 composites (also in a gradient form) with 1, 3, and 5 vol.% of aluminum oxide were fabricated by the hot pressing and spark plasma sintering methods. Two forms of aluminum oxide (αAl2O3 powder and electrocorundum) were used as a reinforcement. Microstructural investigations revealed that near fully dense materials with low porosity and a clear interface between the metal matrix and ceramics were obtained in the case of the SPS method. In this paper, the properties (mechanical, thermal, and tribological) of composite materials were also collected and compared. Technological tests were preceded by finite element method analyses of thermal stresses generated in the gradient structure, and additionally, the role of porosity in the formation process of composite properties was modeled. Based on the said modeling, technological conditions for obtaining FGMs were proposed. Słowa kluczowe: functionally gradient material, shot pressing, metal matrix composites, microstructure, spark plasma sintering, thermal conductivity Afiliacje autorów:
Strojny-Nędza A. | - | Institute of Electronic Materials Technology (PL) | Pietrzak K. | - | inna afiliacja | Węglewski W. | - | IPPT PAN |
| 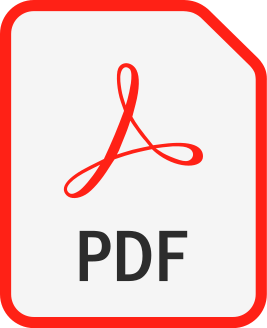 | 20p. |
23. |
Jarząbek D.M., Chmielewski M.♦, Dulnik J., Strojny-Nędza A.♦, The Influence of the Particle Size on the Adhesion Between Ceramic Particles and Metal Matrix in MMC Composites,
Journal of Materials Engineering and Performance, ISSN: 1059-9495, DOI: 10.1007/s11665-016-2107-3, Vol.25, No.8, pp.3139-3145, 2016 Streszczenie: This study investigated the influence of the particle size on the adhesion force between ceramic particles and metal matrix in ceramic-reinforced metal matrix composites. The Cu-Al2O3 composites with 5 vol.% of ceramic phase were prepared by a powder metallurgy process. Alumina oxide powder as an electrocorundum (Al2O3) powder with different particle sizes, i.e., fine powder <3 µm and coarse powder of 180 µm was used as a reinforcement. Microstructural investigations included analyses using scanning electron microscopy with an integrated EDS microanalysis system and transmission microscopy. In order to measure the adhesion force (interface strength), we prepared the microwires made of the investigated materials and carried out the experiments with the use of the self-made tensile tester. We have observed that the interface strength is higher for the sample with coarse particles and is equal to 74 ± 4 MPa and it is equal to 68 ± 3 MPa for the sample with fine ceramic particles. Słowa kluczowe: adhesion, interface strength, metal matrix composites, nanocomposites, tensile test Afiliacje autorów:
Jarząbek D.M. | - | IPPT PAN | Chmielewski M. | - | Institute of Electronic Materials Technology (PL) | Dulnik J. | - | IPPT PAN | Strojny-Nędza A. | - | Institute of Electronic Materials Technology (PL) |
| 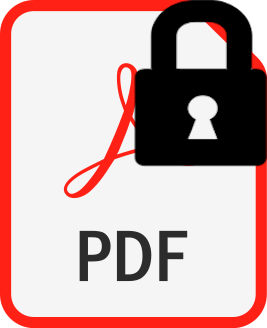 | 20p. |
24. |
Strojny-Nędza A.♦, Pietrzak K.♦, Węglewski W., The Influence of Electrocorundum Granulation on the Properties of Sintered Cu/Electrocorundum Composites,
SCIENCE OF SINTERING, ISSN: 0350-820X, DOI: 10.2298/SOS1503249S, Vol.47, pp.249-258, 2015 Streszczenie: Copper/alumina composites are extensively used in automotive and aerospace industry for products that are subjected to severe thermal and mechanical loadings, such as rocket thrusters and components of aircraft engines. These materials are well-known for their good frictional wear resistance, good resistance to thermal fatigue, high thermal conductivity and high specific heat. In this paper, the sintering process of copper/electrocorundum composites reinforced by electrocorundum particles with diameters of 3 or 180 μm and 1, 3, 5 vol.% content is presented. The effects of different particle sizes of the ceramic reinforcement on the microstructure, physical, mechanical, tribological and thermal properties of the fabricated composites are discussed. Słowa kluczowe: copper/alumina composites, sintering, modeling of thermal properties, microstructure, mechanical properties Afiliacje autorów:
Strojny-Nędza A. | - | Institute of Electronic Materials Technology (PL) | Pietrzak K. | - | inna afiliacja | Węglewski W. | - | IPPT PAN |
| 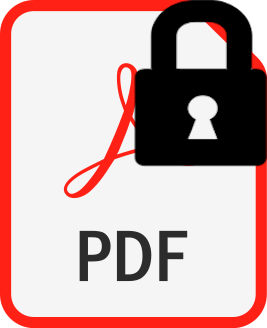 | 30p. |
25. |
Chmielewski M.♦, Pietrzak K.♦, Strojny-Nędza A.♦, Dubiel B.♦, Czyrska-Filemonowicz A.♦, Effect of rhenium addition on the strengthening of chromium-alumina composite materials,
INTERNATIONAL JOURNAL OF MATERIALS RESEARCH, ISSN: 1862-5282, DOI: 10.3139/146.111002, Vol.105, No.2, pp.200-207, 2014 Streszczenie: Chromium–alumina composites are well known for their good mechanical properties in comparison to pure ceramics or metals. These composites are characterized by high hardness and high mechanical strength. The aim of the present work was to improve the properties of chromium–alumina composites even more and expand the range of their possible applications by addition of rhenium. To achieve this goal, chromium–alumina composites containing 2 and 5 vol.% of rhenium were produced via powder metallurgy. The microstructural characterization of the processed material was performed using light microscopy, scanning and transmission electron microscopy as well as X-ray diffraction analysis. Measurement of selected properties such as Young's modulus, bend strength and hardness revealed an advantageous influence of rhenium additions. The results are discussed in terms of the influence of rhenium volume content on the microstructure and on the physical and mechanical properties of the chromium–alumina composites. The solid solution is only partially formed. The properties strongly depend on the amount and distribution of both aluminium oxide and rhenium content. Afiliacje autorów:
Chmielewski M. | - | Institute of Electronic Materials Technology (PL) | Pietrzak K. | - | inna afiliacja | Strojny-Nędza A. | - | Institute of Electronic Materials Technology (PL) | Dubiel B. | - | AGH University of Science and Technology (PL) | Czyrska-Filemonowicz A. | - | AGH University of Science and Technology (PL) |
| 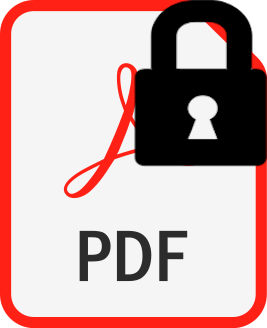 | 25p. |
26. |
Chmielewski M.♦, Nosewicz S., Pietrzak K.♦, Rojek J., Strojny-Nędza A.♦, Mackiewicz S., Dutkiewicz J.♦, Sintering Behavior and Mechanical Properties of NiAl, Al2O3, and NiAl-Al2O3 Composites,
Journal of Materials Engineering and Performance, ISSN: 1059-9495, DOI: 10.1007/s11665-014-1189-z, Vol.23, No.11, pp.3875-3886, 2014 Streszczenie: It is commonly known that the properties of sintered materials are strongly related to technological conditions of the densification process. This paper shows the sintering behavior of a NiAl-Al2O3 composite, and its individual components sintered separately. Each kind of material was processed via the powder metallurgy route (hot pressing). The progress of sintering at different stages of the process was tested. Changes in the microstructure were examined using scanning and transmission electron microscopy. Metal-ceramics interface was clean and no additional phases were detected. Correlation between the microstructure, density, and mechanical properties of the sintered materials was analyzed. The values of elastic constants of NiAl/Al2O3 were close to intermetallic ones due to the volume content of the NiAl phase particularly at low densities, where small alumina particles had no impact on the composite’s stiffness. The influence of the external pressure of 30 MPa seemed crucial for obtaining satisfactory stiffness for three kinds of the studied materials which were characterized by a high dense microstructure with a low number of isolated spherical pores. Słowa kluczowe: ceramics, composites, electron, intermetallic, metallic matrix, microscopy, powder metallurgy, sintering, structural Afiliacje autorów:
Chmielewski M. | - | Institute of Electronic Materials Technology (PL) | Nosewicz S. | - | IPPT PAN | Pietrzak K. | - | inna afiliacja | Rojek J. | - | IPPT PAN | Strojny-Nędza A. | - | Institute of Electronic Materials Technology (PL) | Mackiewicz S. | - | IPPT PAN | Dutkiewicz J. | - | Institute of Metallurgy and Materials Science, Polish Academy of Sciences (PL) |
| 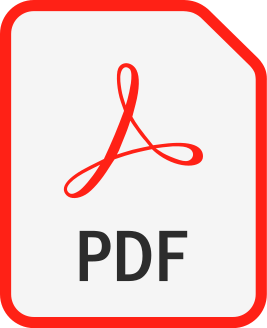 | 20p. |
27. |
Jach K.♦, Pietrzak K.♦, Wajler A.♦, Strojny-Nędza A.♦, Fabrication of an alumina-copper composite using a ceramic preform,
Powder Metallurgy and Metal Ceramics, ISSN: 1068-1302, DOI: 10.1007/s11106-014-9577-3, Vol.52, No.11-12, pp.680-685, 2014 Streszczenie: In this work alumina preforms with an open porosity of 85 and 90% were produced by the replication method. The obtained preforms were used for the fabrication of Cu–Al2O3 composites. We analyzed the effect of applying pressure during a hot-pressing process on the microstructure and mechanical and thermal properties of the obtained materials. It was found that application of higher pressure (10 MPa) during sintering led to the destruction of the ceramic preforms. It facilitated filling of the remaining pores with copper, which resulted in a more homogeneous material with better mechanical and thermal properties. Słowa kluczowe: Cu–Al2O3 composites, hot-pressing process, ceramic reforms, microstructure, mechanical properties Afiliacje autorów:
Jach K. | - | Institute of Electronic Materials Technology (PL) | Pietrzak K. | - | inna afiliacja | Wajler A. | - | Institute of Electronic Materials Technology (PL) | Strojny-Nędza A. | - | Institute of Electronic Materials Technology (PL) |
| 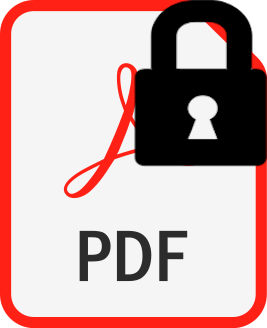 | 15p. |
28. |
Chmielewski M.♦, Pietrzak K., Kaliński D.♦, Strojny A.♦, Processing and thermal properties of Cu-AlN composites,
Advances in Science and Technology, ISSN: 1662-0356, DOI: 10.4028/www.scientific.net/AST.65.100, Vol.65, pp.100-105, 2010 Streszczenie: Heat transfer by conduction is involved in the use of heat sinks dissipitating heat from electronic devices. Effective transfer of heat requires using materials of high thermal conductivity. In addition, it requires appropriate values of thermal expansion, matched to the semiconductor materials, high purity of materials used and good contact between bonded elements across which heat transfer occurs. The conventional materials are not able to fulfil still raising and complex requirements. The solutions of this problem could be using the composites materials, where the combinations of different properties is possible to use. This study presents the technological tests and the analysis of correlation between processing parameters and the properties of copperaluminium nitride composites. Composite materials were obtained by mixing in planetary ball mill and then densified using the sintering under pressure or hot pressing method. The microstructure of obtained composite materials using optical microscopy and scanning electron microscopy were analyzed. Coefficient of thermal expansion (CTE) and thermal conductivity (TC) were investigated depending on the process conditions Słowa kluczowe: Composite Material, Hot-Pressing, Sintering, Thermal Conductivity (TC), Thermal Diffusivity, Thermal Expansion Coefficient Afiliacje autorów:
Chmielewski M. | - | Institute of Electronic Materials Technology (PL) | Pietrzak K. | - | IPPT PAN | Kaliński D. | - | Institute of Electronic Materials Technology (PL) | Strojny A. | - | Institute of Electronic Materials Technology (PL) |
| 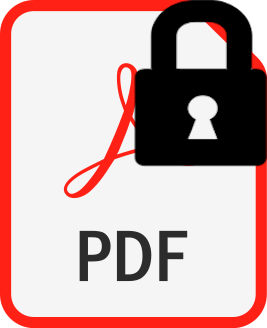 |