1. |
Bochenek K., Dlouhy I.♦, Węglewski W., Chmielewski M.♦, Stepanek R.♦, Cupera J.♦, Pietrzak K., Chmielewski T.♦, Morek R.♦, Basista M., Fracture and wear behavior of high-chromium cast iron obtained from industrial waste and reinforced with alumina particles,
Journal of Materials Research and Technology, ISSN: 2238-7854, DOI: 10.1016/j.jmrt.2025.06.109, Vol.37, pp.1579-1595, 2025 Streszczenie: In response to the specific requirements of the grinding mill industry, a new composite material for mill crushing parts has been developed. This innovative material, which is both cost-effective and environmentally sustainable, is manufactured from industrial waste of high-chromium cast iron (HCCI) reinforced with aluminum oxide (electrocorundum) particles. The HCCI shavings were crushed, sieved, and milled with the addition of 20 wt% of electrocorundum. The HCCI+20%Al2O3 powder mixture was consolidated through the process of hot pressing. By optimizing the process conditions, a composite material was obtained with a remarkably high relative density of 99.84%. Fracture toughness under quasistatic and dynamic loading conditions as well as wear resistance of the HCCI/Al2O3 composite samples were the main material properties investigated in accordance with the intended application. The wear test program included the ball-on-disc test, the linear abrasive test, and the abrasive blasting test. The base HCCI alloy and the HCCI reinforced with uncoated zirconia toughened alumina were used as reference materials. The results from the Taber linear abrasive test and the abrasive blasting test demonstrated the superior wear resistance of the HCCI/Al2O3 composite over the reference materials. However, in the ball-on-disc test, the HCCI/Al₂O₃ composite exhibited a higher degree of wear compared to the reference materials. This effect was found to be attributable to a specific microstructure of the reinforcing phase. The HCCI/Al₂O₃ composite shows promise for industrial applications. However, the hot pressing step requires scaling up to industrial pressing facilities to obtain reasonably sized samples for use in grinding mills. Słowa kluczowe: high-chromium cast iron, iron-alumina composites, powder metallurgy, fracture, wear behavior Afiliacje autorów:
Bochenek K. | - | IPPT PAN | Dlouhy I. | - | inna afiliacja | Węglewski W. | - | IPPT PAN | Chmielewski M. | - | Institute of Electronic Materials Technology (PL) | Stepanek R. | - | inna afiliacja | Cupera J. | - | inna afiliacja | Pietrzak K. | - | IPPT PAN | Chmielewski T. | - | inna afiliacja | Morek R. | - | inna afiliacja | Basista M. | - | IPPT PAN |
| 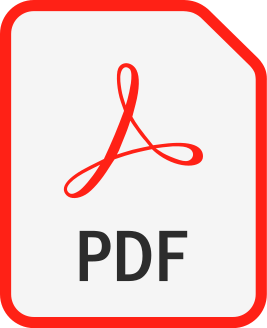 | 100p. |
2. |
Sequeira A., Węglewski W., Bochenek K., Hutsch T.♦, Jain A., Weissgaerber T.♦, Basista M.A., Thermal Conductivity of AlSi12/Al2O3-Graded Composites Consolidated by Hot Pressing and Spark Plasma Sintering: Experimental Evaluation and Numerical Modeling,
METALLURGICAL AND MATERIALS TRANSACTIONS A-PHYSICAL METALLURGY AND MATERIALS SCIENCE, ISSN: 1073-5623, DOI: 10.1007/s11661-024-07506-5, pp.1-18, 2024 Streszczenie: Functionally graded metal matrix composites have attracted the attention of various industries as materials with tailorable properties due to spatially varying composition of constituents. This research work was inspired by an application, such as automotive brake disks, which requires advanced materials with improved wear resistance on the outer surface as combined with effective heat flux dissipation of the graded system. To this end, graded AlSi12/Al2O3 composites (FGMs) with a stepwise gradient in the volume fraction of alumina reinforcement were produced by hot pressing and spark plasma sintering techniques. The thermal conductivities of the individual composite layers and the FGMs were evaluated experimentally and simulated numerically using 3D finite element (FE) models based on micro-computed X-ray tomography (micro-XCT) images of actual AlSi12/Al2O3 microstructures. The numerical models incorporated the effects of porosity of the fabricated AlSi12/Al2O3 composites, thermal resistance, and imperfect interfaces between the AlSi12 matrix and the alumina particles. The obtained experimental data and the results of the numerical models are in good agreement, the relative error being in the range of 4 to 6 pct for different compositions and FGMstructure. The predictive capability of the proposed micro-XCT-based FE model suggests that this model can be applied to similar types of composites and different composition gradients. Afiliacje autorów:
Sequeira A. | - | IPPT PAN | Węglewski W. | - | IPPT PAN | Bochenek K. | - | IPPT PAN | Hutsch T. | - | inna afiliacja | Jain A. | - | IPPT PAN | Weissgaerber T. | - | inna afiliacja | Basista M.A. | - | IPPT PAN |
| 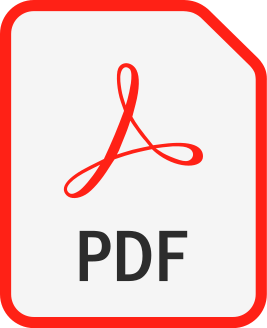 | 200p. |
3. |
Węglewski W., Sequeira A., Bochenek K., Rosc J.♦, Brunner R.♦, Basista M.A., Finite element modeling of thermal residual stresses in functionally graded aluminum-matrix composites using X-ray micro-computed tomography,
FINITE ELEMENTS IN ANALYSIS AND DESIGN, ISSN: 0168-874X, DOI: 10.1016/j.finel.2024.104239, Vol.241, No.104239, pp.1-16, 2024 Streszczenie: Metal-ceramic composites by their nature have thermal residual stresses at the micro-level, which can compromise the integrity of structural elements made from these materials. The evaluation of thermal residual stresses is therefore of continuing research interest both experimentally and by modeling. In this study, two functionally graded aluminum alloy matrix composites, AlSi12/Al2O3 and AlSi12/SiC, each consisting of three composite layers with a stepwise gradient of ceramic content (10, 20, 30 vol%), were produced by powder metallurgy. Thermal residual stresses in the AlSi12 matrix and the ceramic reinforcement of the ungraded and graded composites were measured by neutron diffraction. Based on the X-ray micro-computed tomography (micro-XCT) images of the actual microstructure, a series of finite element models were developed to simulate the thermal residual stresses in the AlSi12 matrix and the reinforcing ceramics Al2O3 and SiC. The accuracy of the numerical predictions is high for all cases considered, with a difference of less than 5 % from the neutron diffraction measurements. It is shown numerically and validated by neutron diffraction data that the average residual stresses in the graded AlSi12/Al2O3 and AlSi12/SiC composites are lower than in the corresponding ungraded composites, which may be advantageous for engineering applications. Słowa kluczowe: Finite element modeling,Micro-XCT,Thermal residual stress,Hot pressing,Aluminum matrix composites Afiliacje autorów:
Węglewski W. | - | IPPT PAN | Sequeira A. | - | IPPT PAN | Bochenek K. | - | IPPT PAN | Rosc J. | - | inna afiliacja | Brunner R. | - | inna afiliacja | Basista M.A. | - | IPPT PAN |
| 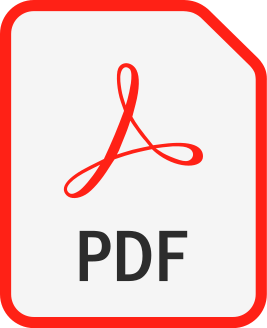 | 100p. |
4. |
Nosewicz S., Jurczak G., Wejrzanowski T.♦, Ibrahim S.H.♦, Grabias A.♦, Węglewski W., Kaszyca K.♦, Rojek J., Chmielewski M.♦, Thermal conductivity analysis of porous NiAl materials manufactured by spark plasma sintering: Experimental studies and modelling,
INTERNATIONAL JOURNAL OF HEAT AND MASS TRANSFER, ISSN: 0017-9310, DOI: 10.1016/j.ijheatmasstransfer.2022.123070, Vol.194, pp.123070-1-19, 2022 Streszczenie: This work presents a comprehensive analysis of heat transfer and thermal conductivity of porous materials manufactured by spark plasma sintering. Intermetallic nickel aluminide (NiAl) has been selected as the representative material. Due to the complexity of the studied material, the following investigation consists of experimental, theoretical and numerical sections. The samples were manufactured in different combinations of process parameters, namely sintering temperature, time and external pressure, and next tested using the laser flash method to determine the effective thermal conductivity. Microstructural characterisation was extensively examined by use of scanning electron microscopy and micro-computed tomography (micro-CT) with a special focus on the structure of cohesive bonds (necks) formed during the sintering process. The experimental results of thermal conductivity were compared with theoretical and numerical ones. Here, a finite element framework based on micro-CT imaging was employed to analyse the macroscopic (effective thermal conductivity, geometrical and thermal tortuosity) and microscopic parameters (magnitude and deviation angle of heat fluxes, local tortuosity). The comparison of different approaches toward effective thermal conductivity evaluation revealed the necessity of consideration of additional thermal resistance related to sintered necks. As micro-CT analysis cannot determine the particle contact boundaries, a special algorithm was implemented to identify the corresponding spots in the volume of finite element samples; these are treated as the resistance phase, marked by lower thermal conductivity. Multiple simulations with varying content of the resistance phase and different values of thermal conductivity of the resistance phase have been performed, to achieve consistency with experimental data. Finally, the Landauer relation has been modified to take into account the thermal resistance of necks and their thermal conductivity, depending on sample densification. Modified theoretical and finite element models have provided updated results covering a wide range of effective thermal conductivities; thus, it was possible to reconstruct experimental results with satisfactory accuracy. Słowa kluczowe: thermal conductivity, porous materials, spark plasma sintering, micro-computed tomography, nickel aluminide, finite element modelling, tortuosity Afiliacje autorów:
Nosewicz S. | - | IPPT PAN | Jurczak G. | - | IPPT PAN | Wejrzanowski T. | - | Politechnika Warszawska (PL) | Ibrahim S.H. | - | Politechnika Warszawska (PL) | Grabias A. | - | Lukasiewicz Institute of Microelectronics and Photonics (PL) | Węglewski W. | - | IPPT PAN | Kaszyca K. | - | Lukasiewicz Institute of Microelectronics and Photonics (PL) | Rojek J. | - | IPPT PAN | Chmielewski M. | - | Institute of Electronic Materials Technology (PL) |
| 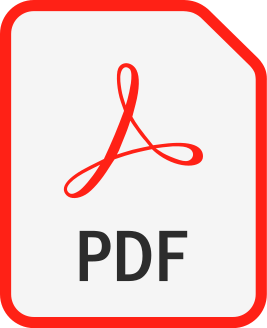 | 200p. |
5. |
Darban H., Bochenek K., Węglewski W., Basista M., Experimental Determination of the Length-Scale Parameter for the Phase-Field Modeling of Macroscale Fracture in Cr–Al2O3 Composites Fabricated by Powder Metallurgy,
METALLURGICAL AND MATERIALS TRANSACTIONS A-PHYSICAL METALLURGY AND MATERIALS SCIENCE, ISSN: 1073-5623, DOI: 10.1007/s11661-022-06677-3, pp.1-23, 2022 Streszczenie: A novel approach is proposed to determine a physically meaningful length-scale parameter for the phase-field modeling of macroscale fracture in metal–ceramic composites on an example of chromium–alumina composite fabricated by powder metallurgy. The approach is based on the fractography analysis by the scanning electron microscopy (SEM) with the aim to measure the process zone size and use that value as the length-scale parameter in the phase-field modeling. Mode I and mixed-mode I/II fracture tests are conducted on Cr–Al2O3 composites at different reinforcement volume fractions and particle sizes using single-edge notched beams under four-point bending. The fracture surfaces are analyzed in detail by SEM to determine the size of the process zone where the microscale nonlinear fracture events occur. The model adequately approximates the experimentally measured fracture toughness and the fracture loads. It is shown that the model prediction of the crack initiation direction under the mixed-mode loading is in agreement with the experiments and the generalized maximum tangential stress criterion. These outcomes justify using the process zone size as the scale parameter in the phase-field modeling of macroscale fracture in chromium–alumina and similar metal–ceramic composites. Afiliacje autorów:
Darban H. | - | IPPT PAN | Bochenek K. | - | IPPT PAN | Węglewski W. | - | IPPT PAN | Basista M. | - | IPPT PAN |
| 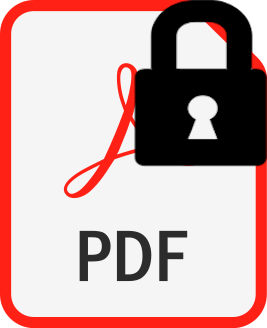 | 200p. |
6. |
Węglewski W., Pitchai P.♦, Chmielewski M.♦, Guruprasad P.J.♦, Basista M., Thermal conductivity of Cu-matrix composites reinforced with coated SiC particles: Numerical modeling and experimental verification,
INTERNATIONAL JOURNAL OF HEAT AND MASS TRANSFER, ISSN: 0017-9310, DOI: 10.1016/j.ijheatmasstransfer.2022.122633, Vol.188, pp.122633-1-18, 2022 Streszczenie: Copper-matrix composites reinforced with silicon carbide (SiC) particles are heat sink materials with potential application in the electronic industry. A major challenge in the manufacturing of these materials, involving sintering process, is to prevent the decomposition of SiC and the subsequent dissolution of silicon in the copper matrix. This is overcome by coating SiC particles with metallic layers. In this study, a combined experimental and computational micromechanics approach was used to investigate thermal conductivity of Cu-matrix composites reinforced with silicon carbide particles coated with chromium, titanium, or tungsten layers. Plasma Vapor Deposition (PVD) was used to produce the metallic layers on SiC particles, while Spark Plasma Sintering (SPS) to consolidate the powder mixtures of copper and coated silicon carbide. Thermal conductivities of the fabricated three-phase composites Cu/SiC/Cr, Cu/SiC/Ti and Cu/SiC/W were evaluated using the Laser Flash technique. Finite Element Method (FEM) and Variational Asymptotic Method (VAM) based homogenization techniques were used for computational modeling of thermal conductivity. In the numerical models complex material microstructures were accounted for using micro-CT images of the sintered compacts. Comparison of the experimental results with simulations highlighted the importance of including the effect of imperfect interfaces to accurately model thermal conductivity of the investigated composites. Słowa kluczowe: metal-matrix composites, powder metallurgy, plasma vapor deposition, imperfect interface, thermal conductivity, numerical modeling Afiliacje autorów:
Węglewski W. | - | IPPT PAN | Pitchai P. | - | Indian Institute of Science (IN) | Chmielewski M. | - | Institute of Electronic Materials Technology (PL) | Guruprasad P.J. | - | Indian Institute of Technology (IN) | Basista M. | - | IPPT PAN |
| 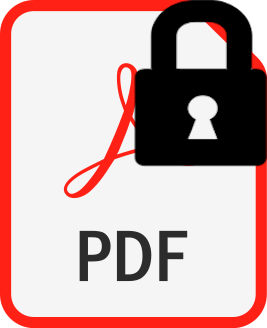 | 200p. |
7. |
Bochenek K., Węglewski W., Strojny-Nędza A.♦, Pietrzak K., Chmielewski T.♦, Chmielewski M.♦, Basista M., Microstructure, Mechanical, and Wear Properties of NiCr-Re-Al2O3 Coatings Deposited by HVOF, Atmospheric Plasma Spraying, and Laser Cladding,
Journal of Thermal Spray Technology, ISSN: 1059-9630, DOI: 10.1007/s11666-022-01400-5, pp.1-25, 2022 Streszczenie: Metallic coatings are often applied on steel tubes in power generation boilers to improve their performance and extend the lifetime. Besides the high-temperature corrosion and erosion protection, the coatings should manifest good adhesion and cohesion strength, and relatively low residual stresses. In this study, three processing techniques: high velocity oxygen fuel spraying (HVOF), atmospheric plasma spraying (APS), and direct laser cladding were employed to obtain novel NiCr-Re and NiCr-Re-Al2O3 coatings intended for application in combustion boilers. The main objective was to assess the suitability of these three techniques to deposit NiCr-Re and NiCr-Re-Al2O3 composite coatings on a 16Mo3 steel substrate. For this purpose, a comparative analysis of the coatings behavior in selected tests was conducted. Of the three processing techniques, thermal spraying by HVOF turned out to be the optimum choice for the studied coatings. From among several variants of the HVOF-sprayed coatings, namely NiCr+1%Re, NiCr+2%Re, NiCr+1%Re+5%Al2O3, and NiCr+1%Re+10%Al2O3 (all vol.%), the NiCr+1%Re material exhibited the lowest extent of cracking in the disk bend test, the highest tensile strength (405 MPa) in the in-plane tension test, the highest Vickers hardness (379 HV2), the lowest specific wear rate (2.23·10-4 mm3/N m), and the lowest level of average residual tensile stress (120 MPa). Słowa kluczowe: alumina, HVOF, mechanical behavior, nickel-chromium coatings, rhenium, residual stress, wear resistance Afiliacje autorów:
Bochenek K. | - | IPPT PAN | Węglewski W. | - | IPPT PAN | Strojny-Nędza A. | - | Institute of Electronic Materials Technology (PL) | Pietrzak K. | - | IPPT PAN | Chmielewski T. | - | Politechnika Warszawska (PL) | Chmielewski M. | - | Institute of Electronic Materials Technology (PL) | Basista M. | - | IPPT PAN |
| 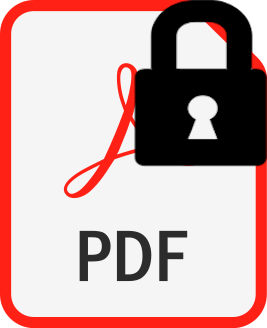 | 140p. |
8. |
Maj J., Węglewski W., Bochenek K., Rogal Ł.♦, Woźniacka S., Basista M., A comparative study of mechanical properties, thermal conductivity, residual stresses, and wear resistance of aluminum-alumina composites obtained by squeeze casting and powder metallurgy,
METALLURGICAL AND MATERIALS TRANSACTIONS A-PHYSICAL METALLURGY AND MATERIALS SCIENCE, ISSN: 1073-5623, DOI: 10.1007/s11661-021-06401-7, pp.1-10, 2021 Streszczenie: Squeeze casting and powder metallurgy techniques were employed to fabricate AlSi12/Al2O3 composites, which are lightweight structural materials with potential applications in the automotive industry. The impact of the processing route on the material properties was studied. Comparative analyses were conducted for the Vickers hardness, flexural strength, fracture toughness, thermal conductivity, thermal residual stresses, and frictional wear. Our results show that the squeeze cast composite exhibits superior properties to those obtained using powder metallurgy. Afiliacje autorów:
Maj J. | - | IPPT PAN | Węglewski W. | - | IPPT PAN | Bochenek K. | - | IPPT PAN | Rogal Ł. | - | Institute of Metallurgy and Materials Science, Polish Academy of Sciences (PL) | Woźniacka S. | - | IPPT PAN | Basista M. | - | IPPT PAN |
| 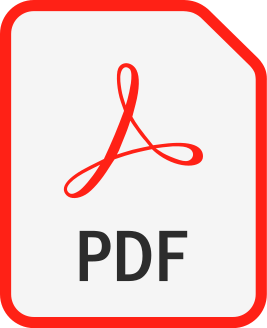 | 200p. |
9. |
Węglewski W., Pitchai P.♦, Bochenek K., Bolzon G.♦, Konetschnik R.♦, Sartory B.♦, Ebner R.♦, Kiener D.♦, Basista M., Experimental and numerical investigation of the deformation and fracture mode of microcantilever beams made of Cr(Re)/Al2O3 metal–matrix composite,
METALLURGICAL AND MATERIALS TRANSACTIONS A-PHYSICAL METALLURGY AND MATERIALS SCIENCE, ISSN: 1073-5623, DOI: 10.1007/s11661-020-05687-3, Vol.51, No.5, pp.2377-2390, 2020 Streszczenie: This work presents a combined experimental and computational study of the deformation and fracture of microcantilever specimens made of chromium(rhenium)-alumina metal–matrix composite (MMC), with a particular focus on the failure properties of the metal–ceramic interfaces. The obtained experimental results show that the bending strength of microcantilevers containing alumina particles in critical cross-sections near specimen's fixed end is considerably higher than that of unreinforced chromium(rhenium) samples. Brittle cracking along chromium–alumina interfaces is the dominant fracture mode of the composite microcantilevers. The interface characteristics are determined in an indirect way by numerical simulations of the experiment with account of the actual specimen microstructure from the scanning electron microscope (SEM) images. A parametric study demonstrates that the overall material response may be reproduced by different sets of model parameters, whereas the actual failure mode permits to discriminate among the possible alternatives. Using this approach, the in situ values of the chromium–alumina interface cohesive strength and the fracture energy are estimated. Afiliacje autorów:
Węglewski W. | - | IPPT PAN | Pitchai P. | - | Indian Institute of Science (IN) | Bochenek K. | - | IPPT PAN | Bolzon G. | - | inna afiliacja | Konetschnik R. | - | inna afiliacja | Sartory B. | - | inna afiliacja | Ebner R. | - | inna afiliacja | Kiener D. | - | inna afiliacja | Basista M. | - | IPPT PAN |
| 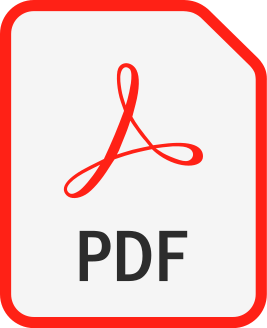 | 200p. |
10. |
Bochenek K., Węglewski W., Morgiel J.♦, Maj M., Basista M., Enhancement of fracture toughness of hot-pressed NiAl-Re material by aluminum oxide addition,
MATERIALS SCIENCE AND ENGINEERING A-STRUCTURAL MATERIALS PROPERTIES MICROSTRUCTURE AND PROCESSING, ISSN: 0921-5093, DOI: 10.1016/j.msea.2020.139670, Vol.790, pp.139670-1-6, 2020 Streszczenie: In the search for a remedy to increase the fracture toughness of NiAl, the effect of rhenium and aluminum oxide addition is explored. Using a powder metallurgy processing route an optimum composition of NiAl-Re-Al2O3 material is found which manifests KIC over two times higher than as-received NiAl sintered under the same conditions. Słowa kluczowe: fracture behavior, stress/strain measurements, intermetallics, composites, powder metallurgy, grains and interfaces Afiliacje autorów:
Bochenek K. | - | IPPT PAN | Węglewski W. | - | IPPT PAN | Morgiel J. | - | Institute of Metallurgy and Materials Science, Polish Academy of Sciences (PL) | Maj M. | - | IPPT PAN | Basista M. | - | IPPT PAN |
| 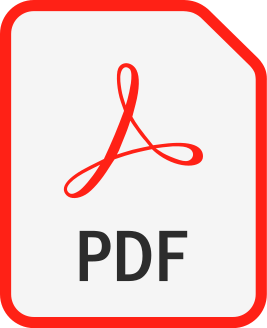 | 140p. |
11. |
Węglewski W., Krajewski M., Bochenek K., Denis P., Wysmołek A.♦, Basista M., Anomalous size effect in thermal residual stresses in pressure sintered alumina-chromium composites,
MATERIALS SCIENCE AND ENGINEERING A-STRUCTURAL MATERIALS PROPERTIES MICROSTRUCTURE AND PROCESSING, ISSN: 0921-5093, DOI: 10.1016/j.msea.2019.138111, Vol.762, pp.138111-1-10, 2019 Streszczenie: This paper explores an anomalous size effect in thermal residual stresses occurring in the alumina matrix of Al2O3/Cr sintered composite upon varying the particle size of the chromium reinforcement. When a coarse chromium powder (45 µm mean particle size) is used the average residual stress in the alumina phase after cooling is compressive in accordance with the classical Eshelby solution. However, in the case of a fine chromium (5 µm mean particle size) it switches to tension. This effect, detected by photoluminescence piezospectroscopy, is also confirmed by X-ray and neutron diffraction experiments. As the classical micromechanics models are incapable to capture it, a finite element model is developed with the actual composite microstructure being reconstructed from the microtomography images. It is shown by numerical simulations that the anomalous size effect is associated with the complex microstructure of the composite fabricated with the fine chromium powder. It is also pointed out that the temperature dependence of the coefficients of thermal expansion of the matrix and the reinforcement affects the residual stress levels. Słowa kluczowe: thermal residual stress, metal-ceramic composites, size effect, microcomputed tomography, finite element analysis Afiliacje autorów:
Węglewski W. | - | IPPT PAN | Krajewski M. | - | IPPT PAN | Bochenek K. | - | IPPT PAN | Denis P. | - | IPPT PAN | Wysmołek A. | - | Uniwersytet Warszawski (PL) | Basista M. | - | IPPT PAN |
| 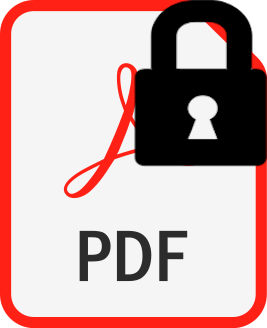 | 140p. |
12. |
Krajewski M., Węglewski W., Bochenek K., Wysmołek A.♦, Basista M., Optical measurements of thermal residual stresses in alumina reinforced with chromium,
JOURNAL OF APPLIED PHYSICS, ISSN: 0021-8979, DOI: 10.1063/1.5083115, Vol.125, No.13, pp.135104-1-10, 2019 Streszczenie: This work describes optical measurements of processing-induced thermal residual stresses in an alumina matrix reinforced with chromium particles. This ceramic-metal composite is manufactured by the powder metallurgy method comprising powder mixing in a planetary ball mill and consolidation by hot pressing. Two different chromium powders (5 μm and 45 μm mean particle size) are used, while the average alumina particle size is kept constant (1 μm). The residual stresses in aluminum oxide are determined by applying two optical methods: photoluminescence piezo-spectroscopy (PLPS) and Raman spectroscopy (RS). Both experimental techniques reveal a chromium size effect in the residual stress measurements. When the fine chromium powder (5 μm) is used, the average residual stress in the ceramic phase is tensile (unusual effect), whereas for the coarser chromium powder (45 μm) it becomes compressive. The PLPS measurements of the hydrostatic residual stress component in the ceramic phase yield the values of 0.290 and −0.130 GPa for samples with 5 μm and 45 μm chromium powders, respectively. In the RS experiments, the corresponding stress component in the alumina equals 0.351 GPa for the composite with 5 μm chromium and −0.158 GPa for that with 45 μm chromium powder. These values indicate that the residual stress in the alumina reinforced with 5 μm chromium is approximately twice higher than that in the alumina reinforced with 45 μm chromium. Finally, the validity of the results obtained with the optical techniques is confirmed by the neutron diffraction measurements. Afiliacje autorów:
Krajewski M. | - | IPPT PAN | Węglewski W. | - | IPPT PAN | Bochenek K. | - | IPPT PAN | Wysmołek A. | - | Uniwersytet Warszawski (PL) | Basista M. | - | IPPT PAN |
| 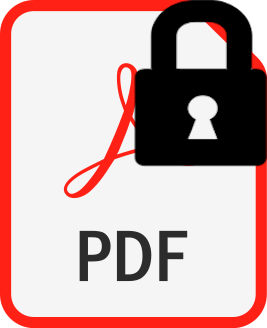 | 70p. |
13. |
Bochenek K., Węglewski W., Morgiel J.♦, Basista M., Influence of rhenium addition on microstructure, mechanical properties and oxidation resistance of NiAl obtained by powder metallurgy,
MATERIALS SCIENCE AND ENGINEERING A-STRUCTURAL MATERIALS PROPERTIES MICROSTRUCTURE AND PROCESSING, ISSN: 0921-5093, DOI: 10.1016/j.msea.2018.08.032, Vol.735, pp.121-130, 2018 Streszczenie: The search for new materials capable of replacing nickel-based superalloys in aerospace applications has increased rapidly in the recent years. One of the candidates for this purpose is nickel aluminide NiAl provided that its main drawback, namely the inferior fracture toughness at room temperature is overcome. We propose rhenium as an addition to NiAl to improve its mechanical properties without compromising on the oxidation resistance. Two powder metallurgy techniques (HP and SPS) were used to obtain NiAl/Re sinters. Small amounts of rhenium (0.6 at.%; 1.25at.%; 1.5 at.%) almost doubled the flexural strength of NiAl and improved its fracture toughness by 60%. Microscopic investigations revealed rhenium particles at the boundaries of NiAl grains resulting in an enhanced fracture toughness. Mass changes during oxidation at 900 oC, 1100 oC and 1300 oC were relatively low. Plausible mechanisms of the fracture toughness enhancement and the oxidation behavior are discussed. Słowa kluczowe: nickel aluminide, rhenium, fracture toughness, oxidation resistance, powder metallurgy, grain boundary strengthening Afiliacje autorów:
Bochenek K. | - | IPPT PAN | Węglewski W. | - | IPPT PAN | Morgiel J. | - | Institute of Metallurgy and Materials Science, Polish Academy of Sciences (PL) | Basista M. | - | IPPT PAN |
| 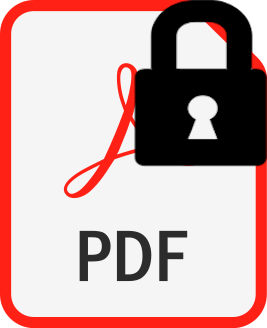 | 35p. |
14. |
Maj J., Basista M., Węglewski W., Bochenek K., Strojny-Nędza A.♦, Naplocha K.♦, Panzner T.♦, Tatarkova M.♦, Fiori F.♦, Effect of microstructure on mechanical properties and residual stresses in interpenetrating aluminum-alumina composites fabricated by squeeze casting,
MATERIALS SCIENCE AND ENGINEERING A-STRUCTURAL MATERIALS PROPERTIES MICROSTRUCTURE AND PROCESSING, ISSN: 0921-5093, DOI: 10.1016/j.msea.2017.12.091, Vol.715, pp.154-162, 2018 Streszczenie: Aluminum-alumina composites with interpenetrating network structure are interesting structural materials due to their high resistance to elevated temperature and frictional wear, good heat conductivity, enhanced mechanical strength and fracture toughness. In this paper aluminum-alumina bulk composites and FGMs are manufactured by pressure infiltration of porous alumina preforms with molten aluminium alloy (EN AC-44200). Influence of the interpenetrating microstructure on the macroscopic bending strength, fracture toughness, hardness and heat conduction is examined. Special focus is on processing-induced thermal residual stresses in aluminium-alumina composites due to their potentially detrimental effects on material performance in structural elements under in-service conditions. The residual stresses are measured experimentally in the ceramic phase by neutron diffraction and simulated numerically using a micro-CT based Finite Element model, which takes into account the actual interpenetrating microstructure of the composite. The model predictions for two different volume fractions of alumina agree fairly well with the neutron diffraction measurements Słowa kluczowe: A. stress measurements, X-ray analysis, finite element analysis, B. composites, C. casting methods Afiliacje autorów:
Maj J. | - | IPPT PAN | Basista M. | - | IPPT PAN | Węglewski W. | - | IPPT PAN | Bochenek K. | - | IPPT PAN | Strojny-Nędza A. | - | Institute of Electronic Materials Technology (PL) | Naplocha K. | - | Wroclaw University of Science and Technology (PL) | Panzner T. | - | Paul Scherrer Institut (CH) | Tatarkova M. | - | Institute of Materials Research, Slovak Academy of Sciences (SK) | Fiori F. | - | Universita Politecnica delle Marche (IT) |
| 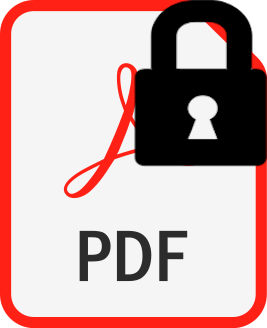 | 35p. |
15. |
Basista M., Jakubowska J., Węglewski W., Processing Induced Flaws in Aluminum–Alumina Interpenetrating Phase Composites,
Advanced Engineering Materials, ISSN: 1438-1656, DOI: 10.1002/adem.201700484, Vol.19, No.12, pp.1700484-1-14, 2017 Streszczenie: This review paper deals with flaws in aluminum–alumina composites and FGMs induced by their manufacturing processes. Aluminum–alumina composites have been studied for many years as potentially interesting materials for applications, for example, in the automotive sector due to their enhanced mechanical strength, wear resistance, good heat conductivity and low specific weight. The focus here is on the interpenetrating phase composites (IPCs) manufactured by infiltration of porous alumina preforms with molten aluminum alloys. The primary objective is to provide an updated overview of research findings on a variety of flaws occurring at different stages of the manufacturing processes. Some precautions on how to avoid processing induced flaws in aluminum–alumina bulk composites and FGMs are mentioned. Afiliacje autorów:
Basista M. | - | IPPT PAN | Jakubowska J. | - | IPPT PAN | Węglewski W. | - | IPPT PAN |
| 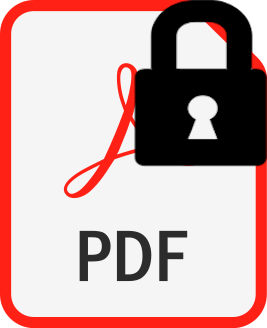 | 30p. |
16. |
Strojny-Nędza A.♦, Pietrzak K.♦, Teodorczyk M.♦, Basista M., Węglewski W., Chmielewski M.♦, Influence of Material Ccating on the heat Transfer in a layered Cu-SiC-Cu Systems,
ARCHIVES OF METALLURGY AND MATERIALS, ISSN: 1733-3490, DOI: 10.1515/amm-2017-0199, Vol.62, No.2B, pp.1311-1314, 2017 Streszczenie: This paper describes the process of obtaining Cu-SiC-Cu systems by way of spark plasma sintering. A monocrystalline form of silicon carbide (6H-SiC type) was applied in the experiment. Additionally, silicon carbide samples were covered with a layer of tungsten and molybdenum using chemical vapour deposition (CVD) technique. Microstructural examinations and thermal properties measurements were performed. A special attention was put to the metal-ceramic interface. During annealing at a high temperature, copper reacts with silicon carbide. To prevent the decomposition of silicon carbide two types of coating (tungsten and molybdenum) were applied. The effect of covering SiC with the aforementioned elements on the composite's thermal conductivity was analyzed. Results were compared with the numerical modelling of heat transfer in Cu-SiC-Cu systems. Certain possible reasons behind differences in measurements and modelling results were discussed. Słowa kluczowe: copper matrix composites, silicon carbide, interface, thermal conductivity, modelling Afiliacje autorów:
Strojny-Nędza A. | - | Institute of Electronic Materials Technology (PL) | Pietrzak K. | - | inna afiliacja | Teodorczyk M. | - | Institute of Electronic Materials Technology (PL) | Basista M. | - | IPPT PAN | Węglewski W. | - | IPPT PAN | Chmielewski M. | - | Institute of Electronic Materials Technology (PL) |
| 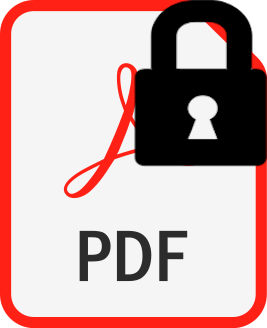 | 30p. |
17. |
Basista M., Węglewski W., Bochenek K., Poniżnik Z., Nowak Z., Micro-CT Finite Element Analysis of Thermal Residual Stresses and Fracture in Metal-Ceramic Composites,
Advanced Engineering Materials, ISSN: 1438-1656, DOI: 10.1002/adem.201600725, Vol.19, No.8, pp.1600725-1-9, 2017 Streszczenie: This paper presents a simple way of using X-ray micro-computed tomography (micro-CT) in numerical modeling of material properties of metal-ceramic composites. It shows step by step the proposed methodology with details of the finite element mesh creation, so that it can easily be reproduced by interested researchers. Two case studies are considered to show the proposed approach at work: i) determination of processing-induced residual stresses in hot pressed Cr/Al2O3 and NiAl/Al2O3 particulate composites and ii) determination of J-integral for an interpenetrating phase composite made of porous alumina preform infiltrated with molten copper. The method is straightforward and effective but has its limitations that are pointed out. Afiliacje autorów:
Basista M. | - | IPPT PAN | Węglewski W. | - | IPPT PAN | Bochenek K. | - | IPPT PAN | Poniżnik Z. | - | IPPT PAN | Nowak Z. | - | IPPT PAN |
| 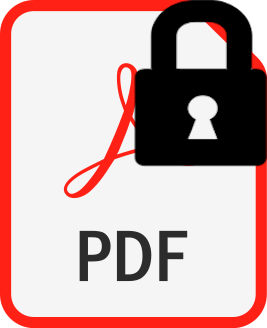 | 30p. |
18. |
Chmielewski M.♦, Pietrzak K.♦, Basista M., Węglewski W., Rhenium doped chromium–alumina composites for high-temperature applications,
International Journal of Refractory Metals and Hard Materials, ISSN: 0263-4368, DOI: 10.1016/j.ijrmhm.2015.07.012, Vol.54, pp.196-202, 2016 Streszczenie: Dense chromium–alumina composites doped with rhenium have been developed by the hot pressing method (bulk composite) and plasma spraying (composite coating). The obtained materials show superior mechanical properties, insensitivity to chemically aggressive environment, good resistance to frictional wear and oxidation at elevated temperature. These enhanced properties make the Cr/Re/Al2O3 composites interesting structural materials for energy and transport applications operating in demanding service conditions, e.g. fluidal boilers in power plants or valve seats in combustion engines. Słowa kluczowe: Metal–ceramic composites, Powder technology, Mechanical properties, Coatings Afiliacje autorów:
Chmielewski M. | - | Institute of Electronic Materials Technology (PL) | Pietrzak K. | - | inna afiliacja | Basista M. | - | IPPT PAN | Węglewski W. | - | IPPT PAN |
| 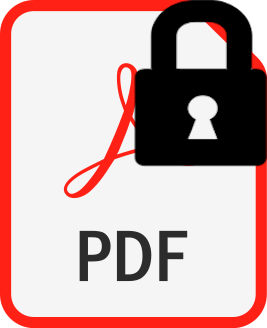 | 35p. |
19. |
Strojny-Nędza A.♦, Pietrzak K.♦, Węglewski W., The Influence of Al2O3 Powder Morphology on the Properties of Cu-Al2O3 Composites Designed for Functionally Graded Materials (FGM),
Journal of Materials Engineering and Performance, ISSN: 1059-9495, DOI: 10.1007/s11665-016-2204-3, Vol.25, No.8, pp.3173-3184, 2016 Streszczenie: In order to meet the requirements of an increased efficiency applying to modern devices and in more general terms science and technology, it is necessary to develop new materials. Combining various types of materials (such as metals and ceramics) and developing composite materials seem to be suitable solutions. One of the most interesting materials includes Cu-Al2O3 composite and gradient materials (FGMs). Due to their potential properties, copper-alumina composites could be used in aerospace industry as rocket thrusters and components in aircraft engines. The main challenge posed by copper matrix composites reinforced by aluminum oxide particles is obtaining the uniform structure with no residual porosity (existing within the area of the ceramic phase). In the present paper, Cu-Al2O3 composites (also in a gradient form) with 1, 3, and 5 vol.% of aluminum oxide were fabricated by the hot pressing and spark plasma sintering methods. Two forms of aluminum oxide (αAl2O3 powder and electrocorundum) were used as a reinforcement. Microstructural investigations revealed that near fully dense materials with low porosity and a clear interface between the metal matrix and ceramics were obtained in the case of the SPS method. In this paper, the properties (mechanical, thermal, and tribological) of composite materials were also collected and compared. Technological tests were preceded by finite element method analyses of thermal stresses generated in the gradient structure, and additionally, the role of porosity in the formation process of composite properties was modeled. Based on the said modeling, technological conditions for obtaining FGMs were proposed. Słowa kluczowe: functionally gradient material, shot pressing, metal matrix composites, microstructure, spark plasma sintering, thermal conductivity Afiliacje autorów:
Strojny-Nędza A. | - | Institute of Electronic Materials Technology (PL) | Pietrzak K. | - | inna afiliacja | Węglewski W. | - | IPPT PAN |
| 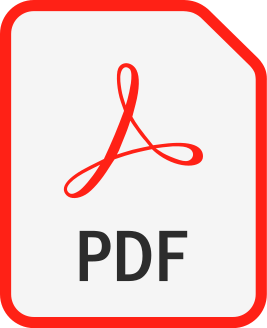 | 20p. |
20. |
Strojny-Nędza A.♦, Pietrzak K.♦, Węglewski W., The Influence of Electrocorundum Granulation on the Properties of Sintered Cu/Electrocorundum Composites,
SCIENCE OF SINTERING, ISSN: 0350-820X, DOI: 10.2298/SOS1503249S, Vol.47, pp.249-258, 2015 Streszczenie: Copper/alumina composites are extensively used in automotive and aerospace industry for products that are subjected to severe thermal and mechanical loadings, such as rocket thrusters and components of aircraft engines. These materials are well-known for their good frictional wear resistance, good resistance to thermal fatigue, high thermal conductivity and high specific heat. In this paper, the sintering process of copper/electrocorundum composites reinforced by electrocorundum particles with diameters of 3 or 180 μm and 1, 3, 5 vol.% content is presented. The effects of different particle sizes of the ceramic reinforcement on the microstructure, physical, mechanical, tribological and thermal properties of the fabricated composites are discussed. Słowa kluczowe: copper/alumina composites, sintering, modeling of thermal properties, microstructure, mechanical properties Afiliacje autorów:
Strojny-Nędza A. | - | Institute of Electronic Materials Technology (PL) | Pietrzak K. | - | inna afiliacja | Węglewski W. | - | IPPT PAN |
| 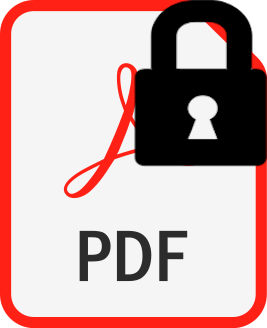 | 30p. |
21. |
Węglewski W., Basista M., Manescu A.♦, Chmielewski M.♦, Pietrzak K.♦, Schubert Th.♦, Effect of grain size on thermal residual stresses and damage in sintered chromium–alumina composites: Measurement and modeling,
COMPOSITES PART B-ENGINEERING, ISSN: 1359-8368, DOI: 10.1016/j.compositesb.2014.06.027, Vol.67, pp.119-124, 2014 Streszczenie: In this paper we present the results of experimental measurements and numerical modeling of the effect of particle size on the residual thermal stresses arising in sintered metal–matrix composites after cooling down from the fabrication temperature. On example of novel Cr(Re)/Al2O3 composites processed by (i) spark plasma sintering and (ii) hot pressing the residual thermal stresses are measured by neutron diffraction technique and determined by a FEM model based on micro-CT scans of the material microstructure. Then numerical model of microcracking induced by residual stresses is applied to predict the effective Young modulus of the damaged composite. Comparison of the numerical results with the measured data of the residual stresses and Young’s modulus is presented and fairly good agreement is noted. Słowa kluczowe: Metal–matrix composites (MMC), Residual/internal stress, Finite element analysis (FEA), Sintering Afiliacje autorów:
Węglewski W. | - | IPPT PAN | Basista M. | - | IPPT PAN | Manescu A. | - | Universita degli Studi di Ancona (IT) | Chmielewski M. | - | Institute of Electronic Materials Technology (PL) | Pietrzak K. | - | inna afiliacja | Schubert Th. | - | Fraunhofer Institut für Fertigungstechnik und Angewandte Materialforschung (DE) |
| 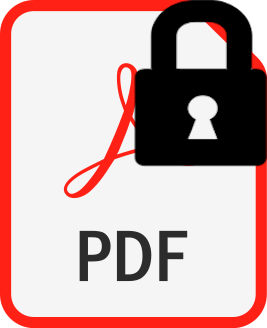 | 40p. |
22. |
Węglewski W., Bochenek K., Basista M., Schubert Th.♦, Jehring U.♦, Litniewski J., Mackiewicz S., Comparative assessment of Young’s modulus measurements of metal-ceramic composites using mechanical and non-destructive tests and micro-CT based computational modeling,
COMPUTATIONAL MATERIALS SCIENCE, ISSN: 0927-0256, DOI: 10.1016/j.commatsci.2013.04.007, Vol.77, pp.19-30, 2013 Streszczenie: It is commonly known that the available non-destructive and mechanical methods of the Young modulus measurement yield different results. This paper presents comparison of the results of experimental determination and numerical modeling of the Young modulus of Cr–Al2O3–Re composites (MMC) processed by a powder metallurgical method (SPS). In the computational model a finite element analysis is combined with images of the real material microstructure obtained from micro-computed tomography (micro-CT). Experimental measurements were carried out by four testing methods: three-point bending, resonance frequency damping analysis (RFDA), ultrasonic pulse-echo technique, and scanning acoustic microscopy. The paper also addresses the issue which of the four experimental methods at hand gives results closest to the theoretical predictions of the micro-CT based FEM model. Słowa kluczowe: Finite element analysis (FEA), Micro-CT based FE model, Metal matrix composites, Elastic modulus, Mechanical and nondestructive techniques Afiliacje autorów:
Węglewski W. | - | IPPT PAN | Bochenek K. | - | IPPT PAN | Basista M. | - | IPPT PAN | Schubert Th. | - | Fraunhofer Institut für Fertigungstechnik und Angewandte Materialforschung (DE) | Jehring U. | - | Fraunhofer Institut für Fertigungstechnik und Angewandte Materialforschung (DE) | Litniewski J. | - | IPPT PAN | Mackiewicz S. | - | IPPT PAN |
| 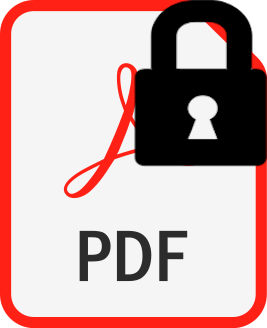 | 30p. |
23. |
Chmielewski M.♦, Węglewski W., Comparison of experimental and modelling results of thermal properties in Cu-AlN composite materials,
BULLETIN OF THE POLISH ACADEMY OF SCIENCES: TECHNICAL SCIENCES, ISSN: 0239-7528, DOI: 10.2478/bpasts-2013-0050, Vol.61, No.2, pp.507-514, 2013 Streszczenie: Copper-based composites could be widely used in automotive, electronic or electrical industry due to their very promising thermal properties. In the present paper, Cu-AlN metal matrix composites with ceramic volume fractions between 0.1 and 0.4 were fabricated by hot pressing method in vacuum. Dependence of the coefficient of thermal expansion (CTE) and the thermal conductivity (TC) on the chemical composition of composites has been investigated. The measured values of the thermal expansion coefficient have been compared with the analytical models’ predictions. A numerical model based on FEAP 7.5 in 3D space has been used to evaluate the influence of the porosity on the thermal properties (thermal conductivity) of the composite. A fairly good correlation between the FEM results and the experimental measurements has been obtained. Słowa kluczowe: thermal properties, porosity, copper-based composites Afiliacje autorów:
Chmielewski M. | - | Institute of Electronic Materials Technology (PL) | Węglewski W. | - | IPPT PAN |
| 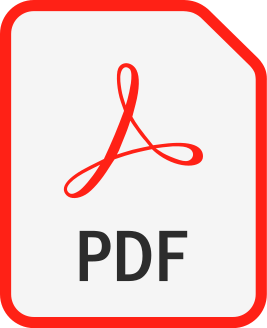 | 25p. |
24. |
Basista M., Pietrzak K.♦, Węglewski W., Chmielewski M.♦, Kompozyty spiekane Cr-Al2O3 z dodatkiem renu. Wytwarzanie, właściwości, modelowanie, zastosowania,
RUDY I METALE NIEŻELAZNE, ISSN: 0035-9696, Vol.R58, No.10, pp.556-563, 2013 Streszczenie: Celem pracy było zbadanie wpływu dodatku renu na właściwości termomechaniczne i użytkowe kompozytów Cr-Al2O3 wytwarzanych metodą spiekania pod ciśnieniem w prasie HP oraz metodą Spark Plasma Sintering (SPS). Uzyskano kompozyty o gęstości przekraczającej 98% gęstości teoretycznej. Właściwości mechaniczne (m.in. moduł Younga, wytrzymałość na zginanie, twardość, odporność na pękanie, granica plastycznośći) oraz odporność na utlenianie wytworzonych materiałów są obiecujące. Zbudowano model numeryczny do obliczeń wielkości naprężeń resztkowych obecnych w materiałach faz kompozytu po procesie spiekania oraz modułów sprężystości. Wykorzystano w tym celu obrazy rzeczywistej mikrostruktury kompozytu otrzymane z tomografii komputerowej. Uzyskano dobrą zgodność wyników modelu z wynikami pomiarów naprężeń metodą XRD. Przedstawiono ponadto porównanie wyników obliczeń numerycznych i pomiarów modułu Younga przy zastosowaniu różnych metod Słowa kluczowe: kompozyty MMC, metalurgia proszków, modelowanie MES, mikrotomografia komputerowa, naprężenia resztkowe Afiliacje autorów:
Basista M. | - | IPPT PAN | Pietrzak K. | - | inna afiliacja | Węglewski W. | - | IPPT PAN | Chmielewski M. | - | Institute of Electronic Materials Technology (PL) |
| 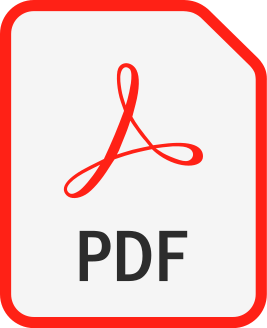 | 7p. |
25. |
Węglewski W., Basista M., Chmielewski M.♦, Pietrzak K., Modeling of thermally induced damage in the processing of Cr–Al2O3 composites,
COMPOSITES PART B-ENGINEERING, ISSN: 1359-8368, DOI: 10.1016/j.compositesb.2011.07.016, Vol.43B, No.2, pp.255-264, 2012 Streszczenie: Thermal stresses induced during the cooling of Cr–Al2O3 (MMC) processed by sintering are modeled numerically using the FEA. The composite microstructure is modeled as (i) random distribution of ceramic particles (voxels) in the metal matrix, and (ii) using micro-CT scans of the real microstructure transformed into a FE mesh. Numerical simulations of the thermal residual stresses are compared with the test data measured by X-ray diffraction. A simple numerical model is then proposed to predict the overall elastic properties of the composite with account of the porosity and damage induced by the thermal stresses. Comparison of the model predictions with the measured data for Young’s modulus is presented. Słowa kluczowe: Metal-matrix composites (MMCs), Residual/internal stress, Finite element analysis (FEA), Sintering Afiliacje autorów:
Węglewski W. | - | IPPT PAN | Basista M. | - | IPPT PAN | Chmielewski M. | - | Institute of Electronic Materials Technology (PL) | Pietrzak K. | - | IPPT PAN |
| 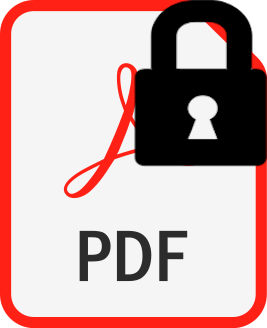 | 45p. |
26. |
Węglewski W., Chmielewski M.♦, Kaliński D.♦, Pietrzak K., Basista M., Thermal residual stresses generated during processing of Cr/Al2O3 composites and their influence on macroscopic elastic properties,
Advances in Science and Technology, ISSN: 1662-0356, DOI: 10.4028/www.scientific.net/AST.65.27, Vol.65, pp.27-32, 2010 Streszczenie: This work is focused on the modeling of thermal stresses induced during the fabrication of the metal/ceramic composites. On example of Cr-Al2O3 composite processed by powder metallurgy, thermal stresses after fabrication are determined by FEM model for different contents of metal and ceramic phases. Numerical model of microcracking induced by thermal stresses is then proposed and applied to compute the overall elastic properties of the damaged composite. Comparison of the model predictions with the measur ed data for Young's modulus is presented. Słowa kluczowe: Cr-Al2O3 composite, mechanical properties, thermal stress modeling, microcracking, Young’s modulus modeling Afiliacje autorów:
Węglewski W. | - | IPPT PAN | Chmielewski M. | - | Institute of Electronic Materials Technology (PL) | Kaliński D. | - | Institute of Electronic Materials Technology (PL) | Pietrzak K. | - | IPPT PAN | Basista M. | - | IPPT PAN |
| 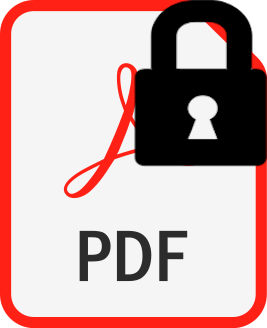 |
27. |
Basista M., Węglewski W., Chemically assisted damage of concrete: a model of expansion under external sulfate attack,
INTERNATIONAL JOURNAL OF DAMAGE MECHANICS, ISSN: 1056-7895, Vol.18, pp.155-175, 2009 Streszczenie: A micromechanical model is proposed to simulate the deformation of cementitious composites exposed to external sulfate attack. The model involves coupled physico-chemical processes of nonsteady diffusion with reaction, topo-chemical reaction of ettringite formation, expansion of ettringite inclusions, microcracking of hardened cement paste and percolation of sulfates through heavily deteriorated mortar. The Fick’s second law with reaction term is assumed to govern the transport of the sulfate ions. The Eshelby solution and the equivalent inclusion method are used to determine the eigenstrain of expanding ettringite crystals in microcracked hardened cement paste. The degradation of transport properties is studied in the effective medium and the percolation regime. An initial boundary value problem (2D) of expansion of a mortar specimen immersed in a sodium sulfate solution is solved and compared with available test data. Słowa kluczowe: chemo-damage, micromechanics, concrete, microcracking, sulfate attack Afiliacje autorów:
Basista M. | - | IPPT PAN | Węglewski W. | - | IPPT PAN |
| 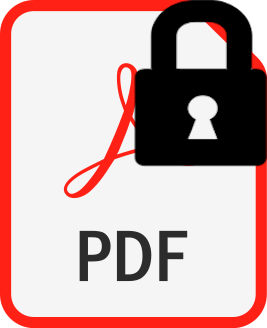 | 32p. |
28. |
Basista M., Węglewski W., Micromechanical modelling of sulphate corrosion in concrete: Influence of ettringite forming reaction,
Theoretical and Applied Mechanics, ISSN: 1450-5584, DOI: 10.2298/TAM0803029B, Vol.35, No.1-3, pp.29-52, 2008 Streszczenie: Two micromechanical models are developed to simulate the expansion of cementitious composites exposed to external sulphate attack. The di®erence between the two models lies in the form of chemical reaction of the ettringite formation (through-solution vs. topochemical). In both models the Fick's second law with reaction term is assumed to govern the transport of the sulphate ions. The Eshelby solution and the equivalent inclusion method are used to determine the eigenstrain of the expanding ettringite crystals in microcracked hardened cement paste. The degradation of transport properties is studied in the efective medium and the percolation regime. An initial-boundary value problem (2D) of expansion of a mortar specimen immersed in a sodium sulphate solution is solved and compared with available test data. The obtained results indicate that the topochemical mechanism is the one capable of producing the experimentally observed amount of expansion. Słowa kluczowe: chemo-damage, sulphate attack, topochemical reaction, through-solution reaction, ettringite, micromechanics, microcracking, percolation Afiliacje autorów:
Basista M. | - | IPPT PAN | Węglewski W. | - | IPPT PAN |
| 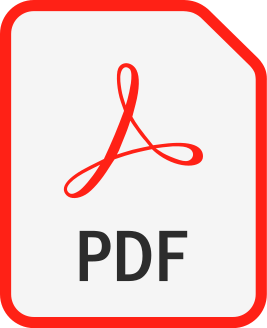 |
29. |
Basista M., Węglewski W., Modelling of damage and fracture in ceramic-matrix composites,
JOURNAL OF THEORETICAL AND APPLIED MECHANICS, ISSN: 1429-2955, Vol.44, No.3, pp.455-484, 2006 Streszczenie: This is a review paper on the existing approaches to modelling of discrete cracks (fracture) and diffuse microcracking (damage) in ceramic matrix composites under mechanical or thermal loading. The focus is on Ceramic Matrix Composites (CMC) with metal particle inclusions and on interpenetrating metal ceramic networks. The second phase in form of ceramic inclusions is not considered. The models of toughening mechanisms are discussed in considerable detail. Sections 2-5 deal with discrete cracks while Sections 6-9 with diffuse microcracking. The paper is concluded with identification of unresolved problems and topics for future research in the area of fracture and damage of CMC. Słowa kluczowe: ceramic matrix composites, particles, interpenetrating networks, fracture, damage, toughening mechanisms, bridging, cracks, microcracks, cavitation, debonding Afiliacje autorów:
Basista M. | - | IPPT PAN | Węglewski W. | - | IPPT PAN |
| 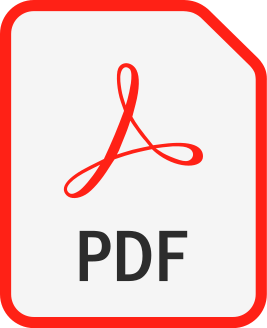 |