1. |
Bochenek K., Dlouhy I.♦, Węglewski W., Chmielewski M.♦, Stepanek R.♦, Cupera J.♦, Pietrzak K., Chmielewski T.♦, Morek R.♦, Basista M., Fracture and wear behavior of high-chromium cast iron obtained from industrial waste and reinforced with alumina particles,
Journal of Materials Research and Technology, ISSN: 2238-7854, DOI: 10.1016/j.jmrt.2025.06.109, Vol.37, pp.1579-1595, 2025 Streszczenie: In response to the specific requirements of the grinding mill industry, a new composite material for mill crushing parts has been developed. This innovative material, which is both cost-effective and environmentally sustainable, is manufactured from industrial waste of high-chromium cast iron (HCCI) reinforced with aluminum oxide (electrocorundum) particles. The HCCI shavings were crushed, sieved, and milled with the addition of 20 wt% of electrocorundum. The HCCI+20%Al2O3 powder mixture was consolidated through the process of hot pressing. By optimizing the process conditions, a composite material was obtained with a remarkably high relative density of 99.84%. Fracture toughness under quasistatic and dynamic loading conditions as well as wear resistance of the HCCI/Al2O3 composite samples were the main material properties investigated in accordance with the intended application. The wear test program included the ball-on-disc test, the linear abrasive test, and the abrasive blasting test. The base HCCI alloy and the HCCI reinforced with uncoated zirconia toughened alumina were used as reference materials. The results from the Taber linear abrasive test and the abrasive blasting test demonstrated the superior wear resistance of the HCCI/Al2O3 composite over the reference materials. However, in the ball-on-disc test, the HCCI/Al₂O₃ composite exhibited a higher degree of wear compared to the reference materials. This effect was found to be attributable to a specific microstructure of the reinforcing phase. The HCCI/Al₂O₃ composite shows promise for industrial applications. However, the hot pressing step requires scaling up to industrial pressing facilities to obtain reasonably sized samples for use in grinding mills. Słowa kluczowe: high-chromium cast iron, iron-alumina composites, powder metallurgy, fracture, wear behavior Afiliacje autorów:
Bochenek K. | - | IPPT PAN | Dlouhy I. | - | inna afiliacja | Węglewski W. | - | IPPT PAN | Chmielewski M. | - | Institute of Electronic Materials Technology (PL) | Stepanek R. | - | inna afiliacja | Cupera J. | - | inna afiliacja | Pietrzak K. | - | IPPT PAN | Chmielewski T. | - | inna afiliacja | Morek R. | - | inna afiliacja | Basista M. | - | IPPT PAN |
| 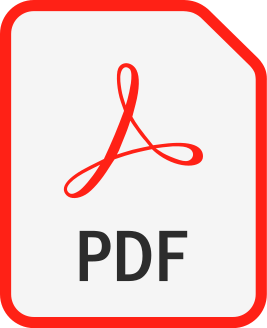 | 100p. |
2. |
Sitek R.♦, Bochenek K., Maj P.♦, Marczak M.♦, Żaba K.♦, Kopeć M., Kaczmarczyk G.♦, Kamiński J.♦, Hot-Pressing of Ti-Al-N Multiphase Composite: Microstructure and Properties,
Applied Sciences, ISSN: 2076-3417, DOI: 10.3390/app15031341, Vol.15, No.1341, pp.1-15, 2025 Streszczenie: This study focuses on the development and characterization of a bulk Ti-Al-N
multiphase composite enriched with BN addition and sintered through hot pressing. The
research aimed to create a material with optimized mechanical and corrosion-resistant
properties suitable for demanding industrial applications. The composite was synthesized using a powder metallurgy approach with a mixture of AlN, TiN, and BN powders, processed under a high temperature and pressure. Comprehensive analyses, including microstructural evaluation, hardness testing, X-ray tomography, and electrochemical corrosion assessments, were conducted. The results confirmed the formation of a multiphase microstructure consisting of TiN, Ti₂AlN and Ti₃AlN phases. The microstructure was uniform with minimal porosity, achieving a hardness within the range of 500–540 HV2. Electrochemical tests revealed the formation of a passive oxide layer that provided moderate corrosion resistance in chloride-rich environment. However, localized pitting corrosion was observed under extreme conditions. The study highlights the potential of a BN admixture to enhance mechanical and corrosion-resistant properties and suggests directions for further optimization in sintering processes and material formulations. Słowa kluczowe: AlN-TiN(BN) composite,hot-pressing,μCT,corrosion resistance Afiliacje autorów:
Sitek R. | - | Politechnika Warszawska (PL) | Bochenek K. | - | IPPT PAN | Maj P. | - | Politechnika Warszawska (PL) | Marczak M. | - | inna afiliacja | Żaba K. | - | inna afiliacja | Kopeć M. | - | IPPT PAN | Kaczmarczyk G. | - | inna afiliacja | Kamiński J. | - | inna afiliacja |
| 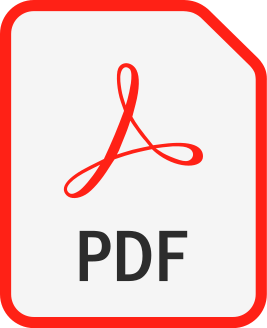 | 100p. |
3. |
Lisowski P., Jóźwiak-Niedźwiedzka D., Osial M., Bochenek K., Denis P., Glinicki M.A., Power ultrasound-assisted enhancement of granulated blast furnace slag reactivity in cement paste,
CEMENT AND CONCRETE COMPOSITES, ISSN: 0958-9465, DOI: 10.1016/j.cemconcomp.2024.105781, Vol.154, No.105781, pp.1-19, 2024 Streszczenie: This paper introduces a first-time investigation into the impact of power ultrasound (PUS)-assisted preparation on the physicochemical and mechanical properties of cement-granulated blast furnace slag (GBFS) composite pastes. Pastes containing deposited GFBS with varying particle size fractions, partially replacing Portland cement, were prepared using PUS (ultrasonic horn tip, 20 kHz, 700 W) in pulse mode in a vertical jacketed glass sonoreactor with closed-circuit cooling. Cement paste incorporating 20 wt.% GBFS as mass substitution with varying particle size fractions was characterized by several physicochemical techniques at different curing ages. Exploring the cement and GBFS interaction induced by PUS, the compressive and flexural strength, the elastic modulus and indentation hardness, the heat of hardening, the mineral composition of hydration products, and the specific surface area BET were evaluated for a curing time of up to 28 days. The grain size distribution of GFBS and the reaction mixture's pH were measured. Both mechanical properties, heat of hydration and nanoporosity exhibited strong sensitivity to PUS treatment. Sonofragmentation of GBFS particles (especially the 125–250 μm fraction) increased with increasing sonication time, resulting in a relative increase of fraction <63 μm and a decrease of fraction >125 μm by 275 % and 60 %, respectively. Using the obtained SEM-EDS data, a simplified mechanism is proposed to explain the effects induced by PUS treatment. Słowa kluczowe: Power ultrasound treatment, Portland cement, Granulated blast furnace slag, Early strength development, C-S-H/C-A-S-H, Seeding effect Afiliacje autorów:
Lisowski P. | - | IPPT PAN | Jóźwiak-Niedźwiedzka D. | - | IPPT PAN | Osial M. | - | IPPT PAN | Bochenek K. | - | IPPT PAN | Denis P. | - | IPPT PAN | Glinicki M.A. | - | IPPT PAN |
| 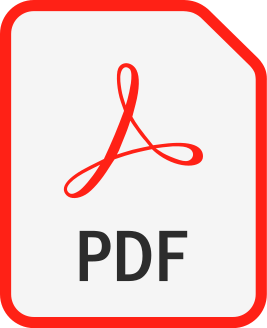 | 200p. |
4. |
Sequeira A., Węglewski W., Bochenek K., Hutsch T.♦, Jain A., Weissgaerber T.♦, Basista M.A., Thermal Conductivity of AlSi12/Al2O3-Graded Composites Consolidated by Hot Pressing and Spark Plasma Sintering: Experimental Evaluation and Numerical Modeling,
METALLURGICAL AND MATERIALS TRANSACTIONS A-PHYSICAL METALLURGY AND MATERIALS SCIENCE, ISSN: 1073-5623, DOI: 10.1007/s11661-024-07506-5, pp.1-18, 2024 Streszczenie: Functionally graded metal matrix composites have attracted the attention of various industries as materials with tailorable properties due to spatially varying composition of constituents. This research work was inspired by an application, such as automotive brake disks, which requires advanced materials with improved wear resistance on the outer surface as combined with effective heat flux dissipation of the graded system. To this end, graded AlSi12/Al2O3 composites (FGMs) with a stepwise gradient in the volume fraction of alumina reinforcement were produced by hot pressing and spark plasma sintering techniques. The thermal conductivities of the individual composite layers and the FGMs were evaluated experimentally and simulated numerically using 3D finite element (FE) models based on micro-computed X-ray tomography (micro-XCT) images of actual AlSi12/Al2O3 microstructures. The numerical models incorporated the effects of porosity of the fabricated AlSi12/Al2O3 composites, thermal resistance, and imperfect interfaces between the AlSi12 matrix and the alumina particles. The obtained experimental data and the results of the numerical models are in good agreement, the relative error being in the range of 4 to 6 pct for different compositions and FGMstructure. The predictive capability of the proposed micro-XCT-based FE model suggests that this model can be applied to similar types of composites and different composition gradients. Afiliacje autorów:
Sequeira A. | - | IPPT PAN | Węglewski W. | - | IPPT PAN | Bochenek K. | - | IPPT PAN | Hutsch T. | - | inna afiliacja | Jain A. | - | IPPT PAN | Weissgaerber T. | - | inna afiliacja | Basista M.A. | - | IPPT PAN |
| 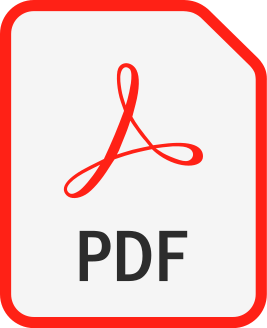 | 200p. |
5. |
Kalita D.♦, Mulewska K.♦, Jóźwik I.♦, Zaborowska A.♦, Gawęda M.♦, Chromiński W.♦, Bochenek K., Rogal Ł.♦, Metastable β-Phase Ti–Nb Alloys Fabricated by Powder Metallurgy: Effect of Nb on Superelasticity and Deformation Behavior,
METALLURGICAL AND MATERIALS TRANSACTIONS A-PHYSICAL METALLURGY AND MATERIALS SCIENCE, ISSN: 1073-5623, DOI: 10.1007/s11661-023-07285-5, pp.1-17, 2024 Streszczenie: This study investigates the effect of Nb concentration on the mechanical properties, superelasticity, as well as deformation behavior of metastable β-phase Ti–Nb alloys produced via powder metallurgy. The alloys were fabricated through mechanical alloying, followed by consolidation using hot pressing. The resulting microstructure comprises fine β-phase grains with TiC carbide precipitates at the grain boundaries. The study reveals non-linear variations in the values of yield strength for the manufactured materials, which were attributed to the occurrence of various deformation mechanisms activated during the loading. It was found that the mechanisms change with the increasing concentration of Nb in the manner: stress-induced martensitic transformation, twinning, slip. However, all these mechanisms were activated at a reduced concentration of Nb compared to the materials obtained by casting technology previously reported in the literature. This is most probably associated with the elevated oxygen content, which affects the stability of the parent β-phase. The study revealed that superelasticity in Ti–Nb-based alloys prepared using powder metallurgy may be achieved by reducing the content of β-stabilizing elements compared to alloys obtained by conventional technologies. In this study, the Ti–14Nb (at. pct) alloy exhibited the best superelasticity, whereas conventionally fabricated Ti–Nb alloys displayed superelasticity at an Nb concentration of approximately 26 at. pct. The developed material exhibited a non-conventional, one-stage yielding behavior, resulting in a superelastic response at significantly higher stresses compared to conventionally fabricated Ti–Nb alloys. Afiliacje autorów:
Kalita D. | - | inna afiliacja | Mulewska K. | - | National Centre for Nuclear Research (PL) | Jóźwik I. | - | Institute of Electronic Materials Technology (PL) | Zaborowska A. | - | inna afiliacja | Gawęda M. | - | inna afiliacja | Chromiński W. | - | inna afiliacja | Bochenek K. | - | IPPT PAN | Rogal Ł. | - | Institute of Metallurgy and Materials Science, Polish Academy of Sciences (PL) |
| 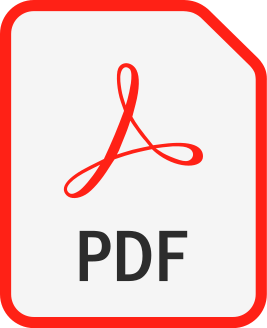 | 200p. |
6. |
Pietrzyk-Thel P., Jain A., Bochenek K., Michalska M.♦, Basista M. A., Szabo T.♦, Nagy P.♦, Wolska A.♦, Klepka M.♦, Flexible, tough and high-performing ionogels for supercapacitor application,
Journal of Materiomics, ISSN: 2352-8478, DOI: 10.1016/j.jmat.2024.01.008, pp.1-41, 2024 Streszczenie: Ionogels are an attractive class of materials for smart and flexible electronics and are prepared from the combination of a polymer and ionic liquid which is entrapped in this matrix. Ionogels provide a continuous conductive phase with high thermal, mechanical, and chemical stability. However, because of the higher percentage of ionic liquids it is difficult to obtain an ionogel with high ionic conductivity and mechanical stability, which are very important from an application point of view. In this work, ionogel films with high flexibility, excellent ionic conductivity, and exceptional stability were prepared using polyvinyl alcohol as the host polymer matrix and 1-ethyl-3-methylimidazolium hydrogen sulfate as the ionic liquid using water as the solvent for energy storage application. The prepared ionogel films exhibited good mechanical stability along with sustaining strain of more than 100% at room temperature and low temperature, the ability to withstand twisting up to 360° and different bending conditions, and excellent ionic conductivity of 5.12 × 10−3 S/cm. The supercapacitor cell fabricated using the optimized ionogel film showed a capacitance of 39.9 F/g with an energy and power densities of 5.5 Wh/kg and 0.3 kW/kg, respectively confirming the suitability of ionogels for supercapacitor application. Słowa kluczowe: Ionic liquid, Gel polymer electrolyte, Ionic conductivity, 1-Ethyl-3-methylimidazolium hydrogen sulfate, Supercapacitors Afiliacje autorów:
Pietrzyk-Thel P. | - | IPPT PAN | Jain A. | - | IPPT PAN | Bochenek K. | - | IPPT PAN | Michalska M. | - | Łukasiewicz Research Network‒Institute of Electronic Materials Technology (PL) | Basista M. A. | - | IPPT PAN | Szabo T. | - | inna afiliacja | Nagy P. | - | inna afiliacja | Wolska A. | - | inna afiliacja | Klepka M. | - | inna afiliacja |
| 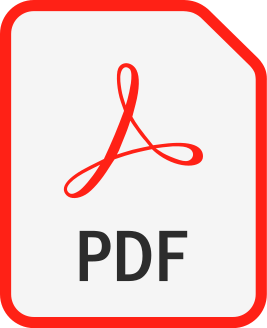 | 140p. |
7. |
Węglewski W., Sequeira A., Bochenek K., Rosc J.♦, Brunner R.♦, Basista M.A., Finite element modeling of thermal residual stresses in functionally graded aluminum-matrix composites using X-ray micro-computed tomography,
FINITE ELEMENTS IN ANALYSIS AND DESIGN, ISSN: 0168-874X, DOI: 10.1016/j.finel.2024.104239, Vol.241, No.104239, pp.1-16, 2024 Streszczenie: Metal-ceramic composites by their nature have thermal residual stresses at the micro-level, which can compromise the integrity of structural elements made from these materials. The evaluation of thermal residual stresses is therefore of continuing research interest both experimentally and by modeling. In this study, two functionally graded aluminum alloy matrix composites, AlSi12/Al2O3 and AlSi12/SiC, each consisting of three composite layers with a stepwise gradient of ceramic content (10, 20, 30 vol%), were produced by powder metallurgy. Thermal residual stresses in the AlSi12 matrix and the ceramic reinforcement of the ungraded and graded composites were measured by neutron diffraction. Based on the X-ray micro-computed tomography (micro-XCT) images of the actual microstructure, a series of finite element models were developed to simulate the thermal residual stresses in the AlSi12 matrix and the reinforcing ceramics Al2O3 and SiC. The accuracy of the numerical predictions is high for all cases considered, with a difference of less than 5 % from the neutron diffraction measurements. It is shown numerically and validated by neutron diffraction data that the average residual stresses in the graded AlSi12/Al2O3 and AlSi12/SiC composites are lower than in the corresponding ungraded composites, which may be advantageous for engineering applications. Słowa kluczowe: Finite element modeling,Micro-XCT,Thermal residual stress,Hot pressing,Aluminum matrix composites Afiliacje autorów:
Węglewski W. | - | IPPT PAN | Sequeira A. | - | IPPT PAN | Bochenek K. | - | IPPT PAN | Rosc J. | - | inna afiliacja | Brunner R. | - | inna afiliacja | Basista M.A. | - | IPPT PAN |
| 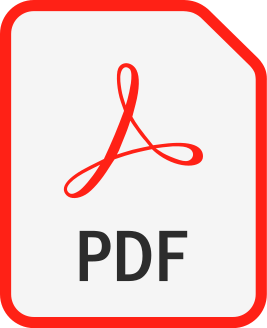 | 100p. |
8. |
Zargarian S., Kupikowska-Stobba B., Kosik-Kozioł A., Bartolewska M., Zakrzewska A., Rybak D., Bochenek K., Osial M., Pierini F., Light-responsive biowaste-derived and bio-inspired textiles: Dancing between bio-friendliness and antibacterial functionality,
Materials Today Chemistry, ISSN: 2468-5194, DOI: 10.1016/j.mtchem.2024.102281, Vol.41, pp.102281-1-15, 2024 Streszczenie: Functional antibacterial textiles fabricated from a hybrid of organic waste-derived and bio-inspired materials offer sustainable solutions for preventing microbial infections. In this work, we developed a novel antibacterial textile created through the valorization of spent coffee grounds (SCG). Electrospinning and electrospraying techniques were employed to integrate the biowaste within a polymeric nanofiber matrix, ensuring uniform particle distribution and providing structural support for enhanced applicability. Modification with polydopamine (PDA) significantly enhanced the textile's photothermal performance. Specific attention was paid to understanding the relation between temperature change and key variables, including the surrounding liquid volume, textile layer stacking, and applied laser power. Developed platforms demonstrated excellent photothermal stability. While the SCG-based textile demonstrated exceptional biocompatibility, the PDA-modified textile effectively eradicated Staphylococcus aureus (S. aureus) under near-infrared (NIR) irradiation. The developed textiles in our work demonstrate a dynamic balance between biocompatibility and on-demand antibacterial functionality, offering adaptable solutions in accordance with the desired application. Słowa kluczowe: Organic waste valorization, Spent coffee grounds, Micro-nanostructured textiles, Bio-inspired photothermal agents, Polydopamine, Antibacterial textiles Afiliacje autorów:
Zargarian S. | - | IPPT PAN | Kupikowska-Stobba B. | - | IPPT PAN | Kosik-Kozioł A. | - | IPPT PAN | Bartolewska M. | - | IPPT PAN | Zakrzewska A. | - | IPPT PAN | Rybak D. | - | IPPT PAN | Bochenek K. | - | IPPT PAN | Osial M. | - | IPPT PAN | Pierini F. | - | IPPT PAN |
| 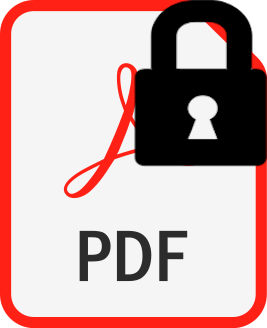 | 70p. |
9. |
Bochenek K., Arneitz S.♦, Sommitsch C.♦, Basista M.A., Comparison of Mechanical Properties of Bulk NiAl-Re-Al2O3 Intermetallic Material Manufactured by Laser Powder Bed Fusion and Hot Pressing,
Journal of Materials Engineering and Performance, ISSN: 1059-9495, DOI: 10.1007/s11665-024-09657-3, pp.1-10, 2024 Streszczenie: The low fracture toughness of NiAl at room temperature is one of the critical issues limiting its application in aircraft engines. It has been previously shown that a small addition of rhenium and alumina significantly improves the fracture toughness of hot-pressed NiAl. In this work, NiAl with an admixture of rhenium and alumina was produced by laser powder bed fusion additive technology (LPBF). The purpose was to compare the fracture toughness, bending strength, and microhardness of the NiAl-Re-Al2O3 material produced by LPBF and hot pressing (HP). Our results show that the LPBF material has lower fracture toughness and bending strength compared to its hot-pressed equivalent. Microcracks generated by thermal stresses during the LPBF process were the primary cause of this behavior. To improve the LPBF material, a post-processing by HP was applied. However, the fracture toughness of the (LPBF + HP) material remained at 50% of the KIC of the HP material. This study supports hot pressing as a suitable processing method for NiAl with rhenium and alumina additions. However, a hybrid approach combining LPBF and HP proved to be highly effective on the raw NiAl powder, resulting in superior fracture toughness of the final material compared to that consolidated by singular HP. Słowa kluczowe: NiAl intermetallic,additive manufacturing ,hot pressing ,mechanical properties Afiliacje autorów:
Bochenek K. | - | IPPT PAN | Arneitz S. | - | inna afiliacja | Sommitsch C. | - | inna afiliacja | Basista M.A. | - | IPPT PAN |
| 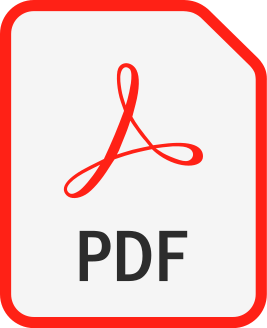 | 70p. |
10. |
Michalska M.♦, Pavlovsky J.♦, Scholtzova E.♦, Peter S.♦, Vlastimil M.♦, Bochenek K., Jain A., Koki C.♦, Takeharu Y.♦, Hirotomo N.♦, A facile approach for fabricating g-C3N4-based materials as metal-free photocatalysts,
Results in Engineering, ISSN: 2590-1230, DOI: 10.1016/j.rineng.2024.103109, Vol.24, No.103109, pp.1-14, 2024 Streszczenie: This study presents a novel, straightforward approach for synthesizing graphitic carbon nitrides (g-C3N4, g-CN) from melamine, requiring merely 30 min of thermal holding at temperatures ranging from 400 to 550 °C in an atmosphere comprising either nitrogen or air. Elemental analysis, X-ray powder diffraction (XRD), Fourier-transform infrared spectroscopy (FTIR), diffuse reflectance (UV–Vis DRS), photoluminescence (PL) spectroscopy and scanning electron microscopy (SEM) were employed to assess the quality of the as-prepared powders. Furthermore, theoretical calculations utilizing the Density Functional Theory (DFT) method were conducted to reinforce the experimental findings of the research. A further investigation of the thermal stability of the selected sample was conducted using a unique combination of thermogravimetry–coupled with differential scanning calorimetry, quadrupole mass spectrometry (TG-DSC-MS) and advanced temperature-programmed desorption (TPD) analyzes. The current study focuses on the effect of synthesis conditions (temperature and nitrogen/air environment) on the structure, morphology, and photocatalytic performance of g-C3N4 compounds synthesized using this approach. The g-C3N4-based materials were examined as potential photocatalysts using the acid orange 7 (AO7) photodegradation methodology. To enable comparison of the photodegradation experiments, two separate lamps with wavelengths of 360 nm (UV light) and 420 nm (VIS light) were utilized. The primary objective was to present a novel method for the synthesis of g-C3N4-based materials. This was achieved by demonstrating that organic composites generated at lower temperatures have the best photocatalytic capabilities. Furthermore, the approach to achieving high-quality photocatalysts was shown to be cost-effective, environmentally friendly, and scalable. Afiliacje autorów:
Michalska M. | - | Łukasiewicz Research Network‒Institute of Electronic Materials Technology (PL) | Pavlovsky J. | - | inna afiliacja | Scholtzova E. | - | inna afiliacja | Peter S. | - | inna afiliacja | Vlastimil M. | - | inna afiliacja | Bochenek K. | - | IPPT PAN | Jain A. | - | IPPT PAN | Koki C. | - | inna afiliacja | Takeharu Y. | - | inna afiliacja | Hirotomo N. | - | inna afiliacja |
| 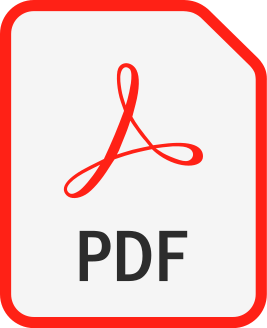 | 20p. |
11. |
Milczarek M., Jarząbek D., Jenczyk P., Bochenek K., Filipiak M.♦, Novel paradigm in AFM probe fabrication: Broadened range of stiffness, materials, and tip shapes,
TRIBOLOGY INTERNATIONAL, ISSN: 0301-679X, DOI: 10.1016/j.triboint.2023.108308, Vol.180, No.108308, pp.1-12, 2023 Streszczenie: Atomic force microscopes could be used in wide range of nanotribology experiments but probes available on the market are only made of silicon or silicon nitride with a stiffness in the range of 0.01–100 N/m, which significantly limits the possible research. We strive to solve this problem by designing all-metal probes. The proposed fabrication method is characterised by the use of a copper substrate and electrodeposition in a mould prepared by indentation and photolithography. Prototype probes fabricated with this method were made of nickel with a stiffness of 20 N/m and 2800 N/m and were used for topography and friction measurements. Both the method and all-metal probes showed flexibility and great potential, especially in the field of nano/microtribology. Słowa kluczowe: Atomic force microscopy, Microfabrication, Cantilever, Metal probe, Friction, Nanotribology Afiliacje autorów:
Milczarek M. | - | IPPT PAN | Jarząbek D. | - | IPPT PAN | Jenczyk P. | - | IPPT PAN | Bochenek K. | - | IPPT PAN | Filipiak M. | - | inna afiliacja |
| 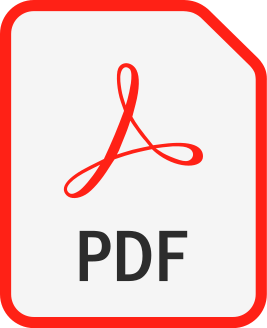 | 200p. |
12. |
Maj P.♦, Bochenek K., Sitek R.♦, Koralnik M.♦, Jonak K.♦, Wieczorek M.♦, Pakieła Z.♦, Mizera J.♦, Comparison of mechanical properties and structure of Haynes 282 consolidated via two different powder metallurgy methods: laser powder bed fusion and hot pressing,
ARCHIVES OF CIVIL AND MECHANICAL ENGINEERING, ISSN: 1644-9665, DOI: 10.1007/s43452-023-00674-y, Vol.23, No.130, pp.1-11, 2023 Streszczenie: The development of powder metallurgy methods in recent years has caused traditional casting methods to be replaced in many industrial applications. Using such methods, it is possible to obtain parts having the required geometry after a process that saves both manufacturing costs and time. However, there are many material issues that decrease the functionality of these methods, including mechanical properties anisotropy and greater susceptibility to cracking due to chemical segregation. The main aim of the current article is to analyze these issues in depth for two powder metallurgy manufacturing processes: laser powder bed fusion (LPBF) and hot-pressing (HP) methods—selected for the experiment because they are in widespread use. Microstructure and mechanical tests were performed in the main manufacturing directions, X and Z. The results show that in both powder metallurgy methods, anisotropy was an issue, although it seems that the problem was more significant for the samples produced via LPBF SLM technique, which displayed only half the elongation in the building direction (18%) compared with the perpendicular direction (almost 38%). However, it should be noted that the fracture toughness of LPBF shows high values in the main directions, higher even than those of the HP and wrought samples. Additionally, the highest level of homogeneity even in comparison with wrought sample, was observed for the HP sintered samples with equiaxed grains with visible twin boundaries. The tensile properties, mainly strength and elongation, were the highest for HP material. Overall, from a practical standpoint, the results showed that HP sintering is the best method in terms of homogeneity based on microstructural and mechanical properties. Słowa kluczowe: Haynes 282 nickel alloy, LPBF, HP, SEM , Static tensile test Afiliacje autorów:
Maj P. | - | Politechnika Warszawska (PL) | Bochenek K. | - | IPPT PAN | Sitek R. | - | Politechnika Warszawska (PL) | Koralnik M. | - | inna afiliacja | Jonak K. | - | inna afiliacja | Wieczorek M. | - | inna afiliacja | Pakieła Z. | - | Politechnika Warszawska (PL) | Mizera J. | - | Politechnika Warszawska (PL) |
| 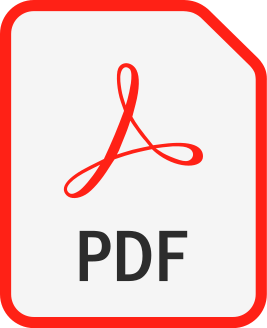 | 140p. |
13. |
Manippady S., Michalska M.♦, Krajewski M., Bochenek K., Basista M.A., Zaszczyńska A., Czeppe T.♦, Rogal ♦, Jain A., One-step synthesis of a sustainable carbon material for high performance supercapacitor and dye adsorption applications,
Materials Science and Engineering: B, ISSN: 0921-5107, DOI: 10.1016/j.mseb.2023.116766, Vol.297, No.116766, pp.1-14, 2023 Streszczenie: The sustainable transformation of bio-waste into usable, material has gained great scientific interest. In this paper, we have presented preparation of an activated carbon material from a natural mushroom (Suillus boletus) and explor its properties for supercapacitor and dye adsorption applications. The produced cell exhibited a single electrode capacitance of ∼247 F g−1 with the energy and power density of ∼35 Wh kg−1 and 1.3 kW kg−1, respectively. The cell worked well for ∼20,000 cycles with ∼30% initial declination in capacitance. Three cells connected in series glowed a 2.0 V LED for ∼1.5 min. Moreover, ultrafast adsorption of methylene blue dye onto the prepared carbon as an adsorbent was recorded with ∼100% removal efficiency in an equilibrium time of three minutes. The performed tests indicate that the mushroom-derived activated carbon has the potential to become a high-performance electrode material for supercapacitors and an adsorbent for real-time wastewater treatment applications. Słowa kluczowe: Activated carbon, Amorphous material, Biomass, Polymer gel electrolyte, Supercapacitor, Dye adsorption Afiliacje autorów:
Manippady S. | - | IPPT PAN | Michalska M. | - | Łukasiewicz Research Network‒Institute of Electronic Materials Technology (PL) | Krajewski M. | - | IPPT PAN | Bochenek K. | - | IPPT PAN | Basista M.A. | - | IPPT PAN | Zaszczyńska A. | - | IPPT PAN | Czeppe T. | - | Institute of Metallurgy and Materials Science, Polish Academy of Sciences (PL) | Rogal | - | Institute of Metallurgy and Materials Science, Polish Academy of Sciences (PL) | Jain A. | - | IPPT PAN |
| 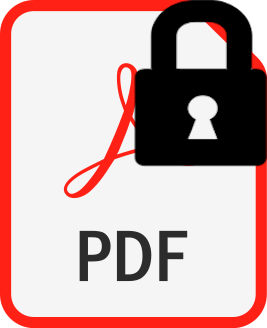 | 100p. |
14. |
Jain A., Ziai Y., Bochenek K., Manippady Sai R., Pierini F., Michalska M.♦, Utilization of compressible hydrogels as electrolyte materials for supercapacitor applications,
RSC Advances, ISSN: 2046-2069, DOI: 10.1039/d3ra00893b, Vol.13, pp.11503-11512, 2023 Streszczenie: Utilization of CoO@Co3O4-x-Ag (x denotes 1, 3, and 5 wt% of Ag) nanocomposites as supercapacitor electrodes is the main aim of this study. A new low-temperature wet chemical approach is proposed to modify the commercial cobalt oxide material with silver nanoparticle (NP) balls of size 1–5 nm. The structure and morphology of the as-prepared nanocomposites were investigated by X-ray diffraction (XRD), scanning electron microscopy (SEM), transmission electron microscopy (TEM), and N2 adsorption–desorption measurements. Hydrogels known to be soft but stable structures were used here as perfect carriers for conductive nanoparticles such as carbons. Furthermore, hydrogels with a large amount of water in their network can give more flexibility to the system. Fabrication of an electrochemical cell can be achieved by combining these materials with a layer-by-layer structure. The performance characteristics of the cells were examined by electrochemical impedance spectroscopy (EIS), cyclic voltammetry (CV), and galvanostatic charge discharge (GCD). Cobalt oxide modified with 5 wt% Ag gave the best supercapacitor results, and the cell offers a specific capacitance of ∼38 mF cm−2 in two-electrode configurations. Afiliacje autorów:
Jain A. | - | IPPT PAN | Ziai Y. | - | IPPT PAN | Bochenek K. | - | IPPT PAN | Manippady Sai R. | - | IPPT PAN | Pierini F. | - | IPPT PAN | Michalska M. | - | Łukasiewicz Research Network‒Institute of Electronic Materials Technology (PL) |
| 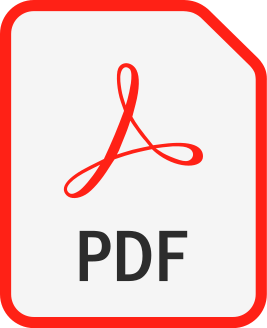 | 100p. |
15. |
Krajewski M., Kaczmarek A., Tokarczyk M.♦, Lewińska S.♦, Włoczewski M.♦, Bochenek K., Jarząbek D., Mościcki T., Hoffman J., Ślawska-Waniewska A.♦, Laser-Assisted Growth of Fe3O4 Nanoparticle Films on Silicon Substrate in Open Air,
physica status solidi (a), ISSN: 1862-6319, DOI: 10.1002/pssa.202200786, No.2200786, pp.1-5, 2023 Streszczenie: This work presents a growth of Fe3O4 nanoparticle films on silicon substrate. The iron oxide is deposited applying a pulsed laser deposition technique. The process is performed in open air in the absence and presence of external magnetic field. In fact, the morphologies of the obtained Fe3O4–Si samples are similar. The Fe3O4 nanoparticles are spherical with average diameters of 30 nm and are densely agglomerated on the Si substrate. The Fe3O4–Si material prepared in the absence of magnetic field has revealed more intense signals during X-ray diffraction and Raman measurements. The magnetic investigations indicate that the Fe3O4 nanoparticles are significantly coupled with the Si substrate and do not exhibit superparamagnetic behavior. Moreover, the Verwey transition is 98 K for both investigated Fe3O4–Si samples. Słowa kluczowe: Fe3O4 nanoparticles,magnetic materials,pulsed laser deposition Afiliacje autorów:
Krajewski M. | - | IPPT PAN | Kaczmarek A. | - | IPPT PAN | Tokarczyk M. | - | Uniwersytet Warszawski (PL) | Lewińska S. | - | Institute of Physics, Polish Academy of Sciences (PL) | Włoczewski M. | - | inna afiliacja | Bochenek K. | - | IPPT PAN | Jarząbek D. | - | IPPT PAN | Mościcki T. | - | IPPT PAN | Hoffman J. | - | IPPT PAN | Ślawska-Waniewska A. | - | inna afiliacja |
| 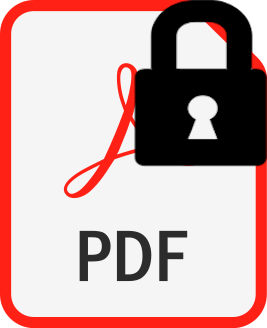 | 70p. |
16. |
Darban H., Bochenek K., Węglewski W., Basista M., Experimental Determination of the Length-Scale Parameter for the Phase-Field Modeling of Macroscale Fracture in Cr–Al2O3 Composites Fabricated by Powder Metallurgy,
METALLURGICAL AND MATERIALS TRANSACTIONS A-PHYSICAL METALLURGY AND MATERIALS SCIENCE, ISSN: 1073-5623, DOI: 10.1007/s11661-022-06677-3, pp.1-23, 2022 Streszczenie: A novel approach is proposed to determine a physically meaningful length-scale parameter for the phase-field modeling of macroscale fracture in metal–ceramic composites on an example of chromium–alumina composite fabricated by powder metallurgy. The approach is based on the fractography analysis by the scanning electron microscopy (SEM) with the aim to measure the process zone size and use that value as the length-scale parameter in the phase-field modeling. Mode I and mixed-mode I/II fracture tests are conducted on Cr–Al2O3 composites at different reinforcement volume fractions and particle sizes using single-edge notched beams under four-point bending. The fracture surfaces are analyzed in detail by SEM to determine the size of the process zone where the microscale nonlinear fracture events occur. The model adequately approximates the experimentally measured fracture toughness and the fracture loads. It is shown that the model prediction of the crack initiation direction under the mixed-mode loading is in agreement with the experiments and the generalized maximum tangential stress criterion. These outcomes justify using the process zone size as the scale parameter in the phase-field modeling of macroscale fracture in chromium–alumina and similar metal–ceramic composites. Afiliacje autorów:
Darban H. | - | IPPT PAN | Bochenek K. | - | IPPT PAN | Węglewski W. | - | IPPT PAN | Basista M. | - | IPPT PAN |
| 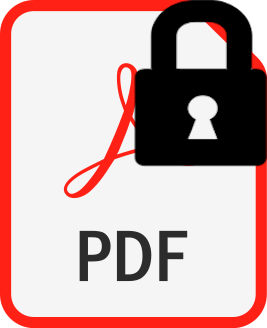 | 200p. |
17. |
Bochenek K., Węglewski W., Strojny-Nędza A.♦, Pietrzak K., Chmielewski T.♦, Chmielewski M.♦, Basista M., Microstructure, Mechanical, and Wear Properties of NiCr-Re-Al2O3 Coatings Deposited by HVOF, Atmospheric Plasma Spraying, and Laser Cladding,
Journal of Thermal Spray Technology, ISSN: 1059-9630, DOI: 10.1007/s11666-022-01400-5, pp.1-25, 2022 Streszczenie: Metallic coatings are often applied on steel tubes in power generation boilers to improve their performance and extend the lifetime. Besides the high-temperature corrosion and erosion protection, the coatings should manifest good adhesion and cohesion strength, and relatively low residual stresses. In this study, three processing techniques: high velocity oxygen fuel spraying (HVOF), atmospheric plasma spraying (APS), and direct laser cladding were employed to obtain novel NiCr-Re and NiCr-Re-Al2O3 coatings intended for application in combustion boilers. The main objective was to assess the suitability of these three techniques to deposit NiCr-Re and NiCr-Re-Al2O3 composite coatings on a 16Mo3 steel substrate. For this purpose, a comparative analysis of the coatings behavior in selected tests was conducted. Of the three processing techniques, thermal spraying by HVOF turned out to be the optimum choice for the studied coatings. From among several variants of the HVOF-sprayed coatings, namely NiCr+1%Re, NiCr+2%Re, NiCr+1%Re+5%Al2O3, and NiCr+1%Re+10%Al2O3 (all vol.%), the NiCr+1%Re material exhibited the lowest extent of cracking in the disk bend test, the highest tensile strength (405 MPa) in the in-plane tension test, the highest Vickers hardness (379 HV2), the lowest specific wear rate (2.23·10-4 mm3/N m), and the lowest level of average residual tensile stress (120 MPa). Słowa kluczowe: alumina, HVOF, mechanical behavior, nickel-chromium coatings, rhenium, residual stress, wear resistance Afiliacje autorów:
Bochenek K. | - | IPPT PAN | Węglewski W. | - | IPPT PAN | Strojny-Nędza A. | - | Institute of Electronic Materials Technology (PL) | Pietrzak K. | - | IPPT PAN | Chmielewski T. | - | Politechnika Warszawska (PL) | Chmielewski M. | - | Institute of Electronic Materials Technology (PL) | Basista M. | - | IPPT PAN |
| 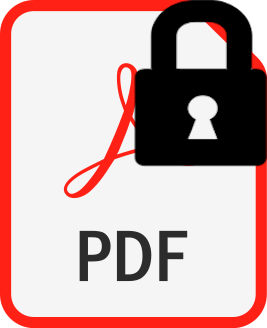 | 140p. |
18. |
Maj J., Węglewski W., Bochenek K., Rogal Ł.♦, Woźniacka S., Basista M., A comparative study of mechanical properties, thermal conductivity, residual stresses, and wear resistance of aluminum-alumina composites obtained by squeeze casting and powder metallurgy,
METALLURGICAL AND MATERIALS TRANSACTIONS A-PHYSICAL METALLURGY AND MATERIALS SCIENCE, ISSN: 1073-5623, DOI: 10.1007/s11661-021-06401-7, pp.1-10, 2021 Streszczenie: Squeeze casting and powder metallurgy techniques were employed to fabricate AlSi12/Al2O3 composites, which are lightweight structural materials with potential applications in the automotive industry. The impact of the processing route on the material properties was studied. Comparative analyses were conducted for the Vickers hardness, flexural strength, fracture toughness, thermal conductivity, thermal residual stresses, and frictional wear. Our results show that the squeeze cast composite exhibits superior properties to those obtained using powder metallurgy. Afiliacje autorów:
Maj J. | - | IPPT PAN | Węglewski W. | - | IPPT PAN | Bochenek K. | - | IPPT PAN | Rogal Ł. | - | Institute of Metallurgy and Materials Science, Polish Academy of Sciences (PL) | Woźniacka S. | - | IPPT PAN | Basista M. | - | IPPT PAN |
| 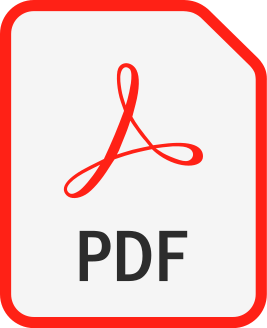 | 200p. |
19. |
Krajewski M., Tokarczyk M.♦, Lewińska S.♦, Bochenek K., Ślawska-Waniewska A.♦, Impact of thermal oxidation on morphological, structural and magnetic properties of Fe-Ni wire-like nanochains,
METALLURGICAL AND MATERIALS TRANSACTIONS A-PHYSICAL METALLURGY AND MATERIALS SCIENCE, ISSN: 1073-5623, DOI: 10.1007/s11661-021-06326-1, Vol.52, No.8, pp.3530-3540, 2021 Streszczenie: This work presents the evolution of morphological, structural and magnetic properties of amorphous Fe-Ni wire-like nanochains caused by thermal oxidation. The initial Fe1−xNix samples (x = 0.75; 0.50; 0.25) were prepared through the magnetic-field-induced synthesis, and then they were heated in dry air at 400 °C and 500 °C. These treatments led to two competing simultaneous processes occurring in the investigated samples, i.e., (i) a conversion of amorphous material into crystalline material, and (ii) their oxidation. Both of them strictly affected the morphological and structural properties of the Fe-Ni nanochains which, in turn, were associated with the amount of iron in material. It was found that the Fe0.75Ni0.25 and Fe0.50Ni0.50 nanochains were covered during thermal treatment by the nanoparticle oxides. This coverage did not constitute a good barrier against oxidation, and these samples became more oxidized than the Fe0.25Ni0.75 sample which was covered by oxide nanosheets and contained additional Ni3B phase. The specific morphological evolutions of the Fe-Ni nanochains also influenced their saturation magnetizations, whereas their coercivities did not vary significantly. The obtained results constitute an important source of information for future application of the thermally treated Fe-Ni nanochains which could be applied in the energy storage devices or catalysis. Afiliacje autorów:
Krajewski M. | - | IPPT PAN | Tokarczyk M. | - | Uniwersytet Warszawski (PL) | Lewińska S. | - | Institute of Physics, Polish Academy of Sciences (PL) | Bochenek K. | - | IPPT PAN | Ślawska-Waniewska A. | - | inna afiliacja |
| 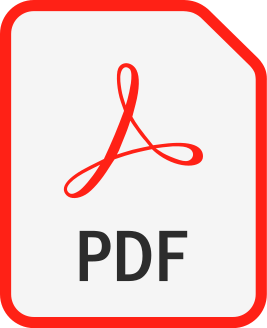 | 200p. |
20. |
Krajewski M., Tokarczyk M.♦, Lewińska S.♦, Brzózka K.♦, Bochenek K., Ślawska-Waniewska A.♦, Evolution of structural and magnetic properties of Fe-Co wire-like nanochains caused by annealing atmosphere,
Materials, ISSN: 1996-1944, DOI: 10.3390/ma14164748, Vol.14, No.16, pp.4748-1-14, 2021 Streszczenie: Thermal treatment is a post-synthesis treatment that aims to improve the crystallinity and interrelated physical properties of as-prepared materials. This process may also cause some unwanted changes in materials like their oxidation or contamination. In this work, we present the post-synthesis annealing treatments of the amorphous Fe1−xCox (x = 0.25; 0.50; 0.75) Wire-like nanochains performed at 400 °C in two different atmospheres, i.e., a mixture of 80% nitrogen and 20% hydrogen and argon. These processes caused significantly different changes of structural and magnetic properties of the initially-formed Fe-Co nanostructures. All of them crystallized and their cores were composed of body-centered cubic Fe-Co phase, whereas their oxide shells comprised of a mixture of CoFe2O4 and Fe3O4 phases. However, the annealing carried out in hydrogen-containing atmosphere caused a decomposition of the initial oxide shell layer, whereas a similar process in argon led to its slight thickening. Moreover, it was found that the cores of thermally-treated Fe0.25Co0.75 nanochains contained the hexagonal closest packed (hcp) Co phase and were covered by the nanosheet-like shell layer in the case of annealing performed in argon. Considering the evolution of magnetic properties induced by structural changes, it was observed that the coercivities of annealed Fe-Co nanochains increased in comparison with their non-annealed counterparts. The saturation magnetization (MS) of the Fe0.25Co0.75 nanomaterial annealed in both atmospheres was higher than that for the non-annealed sample. In turn, the MS of the Fe0.75Co0.25 and Fe0.50Co0.50 nanochains annealed in argon were lower than those recorded for non-annealed samples due to their partial oxidation during thermal processing. Słowa kluczowe: annealing, amorphous materials, Fe-Co nanochains, magnetic-field-induced synthesis, wire-like nanostructure Afiliacje autorów:
Krajewski M. | - | IPPT PAN | Tokarczyk M. | - | Uniwersytet Warszawski (PL) | Lewińska S. | - | Institute of Physics, Polish Academy of Sciences (PL) | Brzózka K. | - | University of Technology and Humanities in Radom (PL) | Bochenek K. | - | IPPT PAN | Ślawska-Waniewska A. | - | inna afiliacja |
| 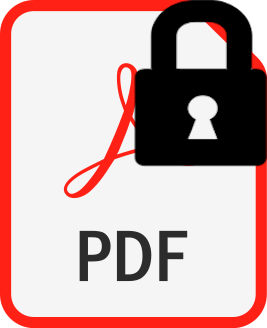 | 140p. |
21. |
Węglewski W., Pitchai P.♦, Bochenek K., Bolzon G.♦, Konetschnik R.♦, Sartory B.♦, Ebner R.♦, Kiener D.♦, Basista M., Experimental and numerical investigation of the deformation and fracture mode of microcantilever beams made of Cr(Re)/Al2O3 metal–matrix composite,
METALLURGICAL AND MATERIALS TRANSACTIONS A-PHYSICAL METALLURGY AND MATERIALS SCIENCE, ISSN: 1073-5623, DOI: 10.1007/s11661-020-05687-3, Vol.51, No.5, pp.2377-2390, 2020 Streszczenie: This work presents a combined experimental and computational study of the deformation and fracture of microcantilever specimens made of chromium(rhenium)-alumina metal–matrix composite (MMC), with a particular focus on the failure properties of the metal–ceramic interfaces. The obtained experimental results show that the bending strength of microcantilevers containing alumina particles in critical cross-sections near specimen's fixed end is considerably higher than that of unreinforced chromium(rhenium) samples. Brittle cracking along chromium–alumina interfaces is the dominant fracture mode of the composite microcantilevers. The interface characteristics are determined in an indirect way by numerical simulations of the experiment with account of the actual specimen microstructure from the scanning electron microscope (SEM) images. A parametric study demonstrates that the overall material response may be reproduced by different sets of model parameters, whereas the actual failure mode permits to discriminate among the possible alternatives. Using this approach, the in situ values of the chromium–alumina interface cohesive strength and the fracture energy are estimated. Afiliacje autorów:
Węglewski W. | - | IPPT PAN | Pitchai P. | - | Indian Institute of Science (IN) | Bochenek K. | - | IPPT PAN | Bolzon G. | - | inna afiliacja | Konetschnik R. | - | inna afiliacja | Sartory B. | - | inna afiliacja | Ebner R. | - | inna afiliacja | Kiener D. | - | inna afiliacja | Basista M. | - | IPPT PAN |
| 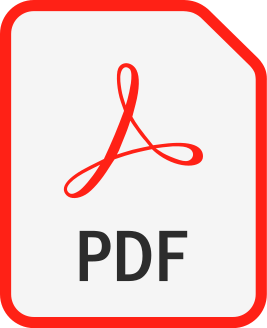 | 200p. |
22. |
Bochenek K., Węglewski W., Morgiel J.♦, Maj M., Basista M., Enhancement of fracture toughness of hot-pressed NiAl-Re material by aluminum oxide addition,
MATERIALS SCIENCE AND ENGINEERING A-STRUCTURAL MATERIALS PROPERTIES MICROSTRUCTURE AND PROCESSING, ISSN: 0921-5093, DOI: 10.1016/j.msea.2020.139670, Vol.790, pp.139670-1-6, 2020 Streszczenie: In the search for a remedy to increase the fracture toughness of NiAl, the effect of rhenium and aluminum oxide addition is explored. Using a powder metallurgy processing route an optimum composition of NiAl-Re-Al2O3 material is found which manifests KIC over two times higher than as-received NiAl sintered under the same conditions. Słowa kluczowe: fracture behavior, stress/strain measurements, intermetallics, composites, powder metallurgy, grains and interfaces Afiliacje autorów:
Bochenek K. | - | IPPT PAN | Węglewski W. | - | IPPT PAN | Morgiel J. | - | Institute of Metallurgy and Materials Science, Polish Academy of Sciences (PL) | Maj M. | - | IPPT PAN | Basista M. | - | IPPT PAN |
| 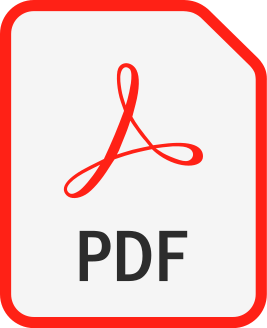 | 140p. |
23. |
Węglewski W., Krajewski M., Bochenek K., Denis P., Wysmołek A.♦, Basista M., Anomalous size effect in thermal residual stresses in pressure sintered alumina-chromium composites,
MATERIALS SCIENCE AND ENGINEERING A-STRUCTURAL MATERIALS PROPERTIES MICROSTRUCTURE AND PROCESSING, ISSN: 0921-5093, DOI: 10.1016/j.msea.2019.138111, Vol.762, pp.138111-1-10, 2019 Streszczenie: This paper explores an anomalous size effect in thermal residual stresses occurring in the alumina matrix of Al2O3/Cr sintered composite upon varying the particle size of the chromium reinforcement. When a coarse chromium powder (45 µm mean particle size) is used the average residual stress in the alumina phase after cooling is compressive in accordance with the classical Eshelby solution. However, in the case of a fine chromium (5 µm mean particle size) it switches to tension. This effect, detected by photoluminescence piezospectroscopy, is also confirmed by X-ray and neutron diffraction experiments. As the classical micromechanics models are incapable to capture it, a finite element model is developed with the actual composite microstructure being reconstructed from the microtomography images. It is shown by numerical simulations that the anomalous size effect is associated with the complex microstructure of the composite fabricated with the fine chromium powder. It is also pointed out that the temperature dependence of the coefficients of thermal expansion of the matrix and the reinforcement affects the residual stress levels. Słowa kluczowe: thermal residual stress, metal-ceramic composites, size effect, microcomputed tomography, finite element analysis Afiliacje autorów:
Węglewski W. | - | IPPT PAN | Krajewski M. | - | IPPT PAN | Bochenek K. | - | IPPT PAN | Denis P. | - | IPPT PAN | Wysmołek A. | - | Uniwersytet Warszawski (PL) | Basista M. | - | IPPT PAN |
| 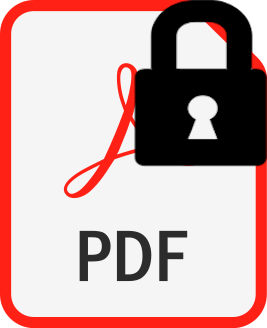 | 140p. |
24. |
Krajewski M., Węglewski W., Bochenek K., Wysmołek A.♦, Basista M., Optical measurements of thermal residual stresses in alumina reinforced with chromium,
JOURNAL OF APPLIED PHYSICS, ISSN: 0021-8979, DOI: 10.1063/1.5083115, Vol.125, No.13, pp.135104-1-10, 2019 Streszczenie: This work describes optical measurements of processing-induced thermal residual stresses in an alumina matrix reinforced with chromium particles. This ceramic-metal composite is manufactured by the powder metallurgy method comprising powder mixing in a planetary ball mill and consolidation by hot pressing. Two different chromium powders (5 μm and 45 μm mean particle size) are used, while the average alumina particle size is kept constant (1 μm). The residual stresses in aluminum oxide are determined by applying two optical methods: photoluminescence piezo-spectroscopy (PLPS) and Raman spectroscopy (RS). Both experimental techniques reveal a chromium size effect in the residual stress measurements. When the fine chromium powder (5 μm) is used, the average residual stress in the ceramic phase is tensile (unusual effect), whereas for the coarser chromium powder (45 μm) it becomes compressive. The PLPS measurements of the hydrostatic residual stress component in the ceramic phase yield the values of 0.290 and −0.130 GPa for samples with 5 μm and 45 μm chromium powders, respectively. In the RS experiments, the corresponding stress component in the alumina equals 0.351 GPa for the composite with 5 μm chromium and −0.158 GPa for that with 45 μm chromium powder. These values indicate that the residual stress in the alumina reinforced with 5 μm chromium is approximately twice higher than that in the alumina reinforced with 45 μm chromium. Finally, the validity of the results obtained with the optical techniques is confirmed by the neutron diffraction measurements. Afiliacje autorów:
Krajewski M. | - | IPPT PAN | Węglewski W. | - | IPPT PAN | Bochenek K. | - | IPPT PAN | Wysmołek A. | - | Uniwersytet Warszawski (PL) | Basista M. | - | IPPT PAN |
| 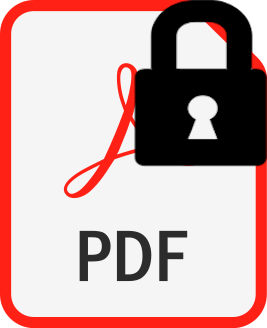 | 70p. |
25. |
Bochenek K., Węglewski W., Morgiel J.♦, Basista M., Influence of rhenium addition on microstructure, mechanical properties and oxidation resistance of NiAl obtained by powder metallurgy,
MATERIALS SCIENCE AND ENGINEERING A-STRUCTURAL MATERIALS PROPERTIES MICROSTRUCTURE AND PROCESSING, ISSN: 0921-5093, DOI: 10.1016/j.msea.2018.08.032, Vol.735, pp.121-130, 2018 Streszczenie: The search for new materials capable of replacing nickel-based superalloys in aerospace applications has increased rapidly in the recent years. One of the candidates for this purpose is nickel aluminide NiAl provided that its main drawback, namely the inferior fracture toughness at room temperature is overcome. We propose rhenium as an addition to NiAl to improve its mechanical properties without compromising on the oxidation resistance. Two powder metallurgy techniques (HP and SPS) were used to obtain NiAl/Re sinters. Small amounts of rhenium (0.6 at.%; 1.25at.%; 1.5 at.%) almost doubled the flexural strength of NiAl and improved its fracture toughness by 60%. Microscopic investigations revealed rhenium particles at the boundaries of NiAl grains resulting in an enhanced fracture toughness. Mass changes during oxidation at 900 oC, 1100 oC and 1300 oC were relatively low. Plausible mechanisms of the fracture toughness enhancement and the oxidation behavior are discussed. Słowa kluczowe: nickel aluminide, rhenium, fracture toughness, oxidation resistance, powder metallurgy, grain boundary strengthening Afiliacje autorów:
Bochenek K. | - | IPPT PAN | Węglewski W. | - | IPPT PAN | Morgiel J. | - | Institute of Metallurgy and Materials Science, Polish Academy of Sciences (PL) | Basista M. | - | IPPT PAN |
| 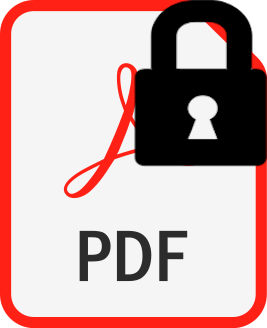 | 35p. |
26. |
Maj J., Basista M., Węglewski W., Bochenek K., Strojny-Nędza A.♦, Naplocha K.♦, Panzner T.♦, Tatarkova M.♦, Fiori F.♦, Effect of microstructure on mechanical properties and residual stresses in interpenetrating aluminum-alumina composites fabricated by squeeze casting,
MATERIALS SCIENCE AND ENGINEERING A-STRUCTURAL MATERIALS PROPERTIES MICROSTRUCTURE AND PROCESSING, ISSN: 0921-5093, DOI: 10.1016/j.msea.2017.12.091, Vol.715, pp.154-162, 2018 Streszczenie: Aluminum-alumina composites with interpenetrating network structure are interesting structural materials due to their high resistance to elevated temperature and frictional wear, good heat conductivity, enhanced mechanical strength and fracture toughness. In this paper aluminum-alumina bulk composites and FGMs are manufactured by pressure infiltration of porous alumina preforms with molten aluminium alloy (EN AC-44200). Influence of the interpenetrating microstructure on the macroscopic bending strength, fracture toughness, hardness and heat conduction is examined. Special focus is on processing-induced thermal residual stresses in aluminium-alumina composites due to their potentially detrimental effects on material performance in structural elements under in-service conditions. The residual stresses are measured experimentally in the ceramic phase by neutron diffraction and simulated numerically using a micro-CT based Finite Element model, which takes into account the actual interpenetrating microstructure of the composite. The model predictions for two different volume fractions of alumina agree fairly well with the neutron diffraction measurements Słowa kluczowe: A. stress measurements, X-ray analysis, finite element analysis, B. composites, C. casting methods Afiliacje autorów:
Maj J. | - | IPPT PAN | Basista M. | - | IPPT PAN | Węglewski W. | - | IPPT PAN | Bochenek K. | - | IPPT PAN | Strojny-Nędza A. | - | Institute of Electronic Materials Technology (PL) | Naplocha K. | - | Wroclaw University of Science and Technology (PL) | Panzner T. | - | Paul Scherrer Institut (CH) | Tatarkova M. | - | Institute of Materials Research, Slovak Academy of Sciences (SK) | Fiori F. | - | Universita Politecnica delle Marche (IT) |
| 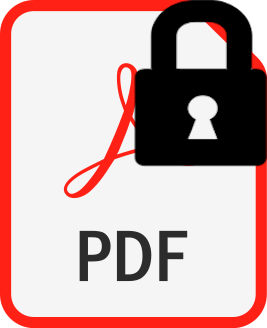 | 35p. |
27. |
Basista M., Węglewski W., Bochenek K., Poniżnik Z., Nowak Z., Micro-CT Finite Element Analysis of Thermal Residual Stresses and Fracture in Metal-Ceramic Composites,
Advanced Engineering Materials, ISSN: 1438-1656, DOI: 10.1002/adem.201600725, Vol.19, No.8, pp.1600725-1-9, 2017 Streszczenie: This paper presents a simple way of using X-ray micro-computed tomography (micro-CT) in numerical modeling of material properties of metal-ceramic composites. It shows step by step the proposed methodology with details of the finite element mesh creation, so that it can easily be reproduced by interested researchers. Two case studies are considered to show the proposed approach at work: i) determination of processing-induced residual stresses in hot pressed Cr/Al2O3 and NiAl/Al2O3 particulate composites and ii) determination of J-integral for an interpenetrating phase composite made of porous alumina preform infiltrated with molten copper. The method is straightforward and effective but has its limitations that are pointed out. Afiliacje autorów:
Basista M. | - | IPPT PAN | Węglewski W. | - | IPPT PAN | Bochenek K. | - | IPPT PAN | Poniżnik Z. | - | IPPT PAN | Nowak Z. | - | IPPT PAN |
| 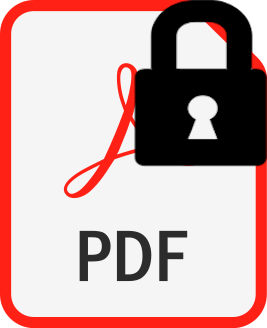 | 30p. |
28. |
Jurczak K., Rojek J., Nosewicz S., Lumelskyj D., Bochenek K., Chmielewski M.♦, Pietrzak K.♦, Modelowanie wstępnego prasowania proszków metodą elementów dyskretnych,
HUTNIK - WIADOMOŚCI HUTNICZE, ISSN: 1230-3534, DOI: 10.15199/24.2016.1.1, Vol.83, No.1, pp.3-7, 2016 Streszczenie: W niniejszym artykule zaprezentowano wyniki modelowania zagęszczania proszku stanowiącego wstępny etap procesu prasowania na gorąco. Modelowanie numeryczne zrealizowano metodą elementów dyskretnych z wykorzystaniem kulistych cząstek. Analizę skoncentrowano na badaniu mechanizmów zagęszczania proszku przy ciśnieniu do 50 MPa oraz poszukiwaniu modeli odpowiednich przy zastosowanych warunkach realizacji procesu. Symulacje numeryczne wykonano wykorzystując dwa modele oddziaływania cząstek proszku: sprężysty model Hertza-Mindlina-Deresiewicza oraz plastyczny model Storåkersa. Wyniki numeryczne zostały porównane z wynikami laboratoryjnymi prasowania proszku NiAl. Otrzymano dużą zgodność wyników eksperymentalnych i numerycznych.
This paper presents the results of discrete element simulation of powder compaction which is the initial stage in the hot pressing process. Numerical simulation has been performed by discrete element method with using spherical particles. The research has been focused on densification mechanisms under pressure 50 MPa and models appropriate for these conditions. Numerical simulations have been carried out for two contact models: elastic Hertz-Mindlin-Deresiewicz and plastic - Storåkers. Numerical results and results from laboratory test of the uniaxial pressing of NiAl powder have been compared. The obtained results of numerical simulation and laboratory tests showing a good agreement. Słowa kluczowe: metoda elementów dyskretnych, prasowanie proszków, materiały intermetaliczne, discrete element method, powder compaction, intermetallics Afiliacje autorów:
Jurczak K. | - | IPPT PAN | Rojek J. | - | IPPT PAN | Nosewicz S. | - | IPPT PAN | Lumelskyj D. | - | IPPT PAN | Bochenek K. | - | IPPT PAN | Chmielewski M. | - | Institute of Electronic Materials Technology (PL) | Pietrzak K. | - | inna afiliacja |
| 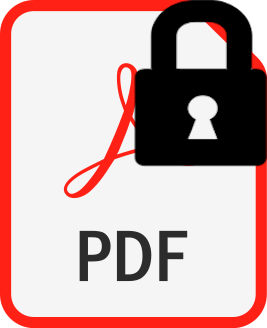 | 7p. |
29. |
Rojek J., Nosewicz S., Jurczak K., Chmielewski M.♦, Bochenek K., Pietrzak K.♦, Discrete element simulation of powder compaction in cold uniaxial pressing with low pressure,
Computational Particle Mechanics, ISSN: 2196-4378, DOI: 10.1007/s40571-015-0093-0, Vol.3, pp.513-524, 2016 Streszczenie: This paper presents numerical studies of powder compaction in cold uniaxial pressing. The powder compaction in this work is considered as an initial stage of a hot pressing process so it is realized with relatively low pressure (up to 50 MPa). Hence the attention has been focused on the densification mechanisms at this range of pressure and models suitable for these conditions. The discrete element method employing spherical particles has been used in the numerical studies. Numerical simulations have been performed for two different contact models—the elastic Hertz–Mindlin–Deresiewicz model and the plastic Storåkers model. Numerical results have been compared with the results of laboratory tests of the die compaction of the NiAl powder. Comparisons have shown that the discrete element method is capable to represent properly the densification mechanisms by the particle rearrangement and particle deformation. Słowa kluczowe: Discrete element method, Simulation, Powder compaction, Cold uniaxial pressing Afiliacje autorów:
Rojek J. | - | IPPT PAN | Nosewicz S. | - | IPPT PAN | Jurczak K. | - | IPPT PAN | Chmielewski M. | - | Institute of Electronic Materials Technology (PL) | Bochenek K. | - | IPPT PAN | Pietrzak K. | - | inna afiliacja |
| 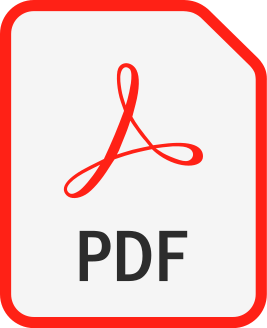 |
30. |
Bochenek K., Basista M., Advances in processing of NiAl intermetallic alloys and composites for high temperature aerospace applications,
PROGRESS IN AEROSPACE SCIENCES, ISSN: 0376-0421, DOI: 10.1016/j.paerosci.2015.09.003, Vol.79, pp.136-146, 2015 Streszczenie: Over the last few decades intermetallic compounds such as NiAl have been considered as potential high temperature structural materials for aerospace industry. A large number of investigations have been reported describing complex fabrication routes, introducing various reinforcing/alloying elements along with theoretical analyses. These research works were mainly focused on the overcoming of main disadvantage of nickel aluminides that still restricts their application range, i.e. brittleness at room temperature. In this paper we present an overview of research on NiAl processing and indicate methods that are promising in solving the low fracture toughness issue at room temperature. Other material properties relevant for high temperature applications are also addressed. The analysis is primarily done from the perspective of NiAl application in aero engines in temperature regimes from room up to the operating temperature (over 1150 °C) of turbine blades. Słowa kluczowe: Nickel aluminide, Intermetallics, Turbine blades, Fracture toughness, Manufacturing techniques Afiliacje autorów:
Bochenek K. | - | IPPT PAN | Basista M. | - | IPPT PAN |
| 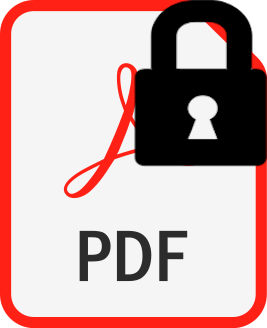 | 50p. |
31. |
Węglewski W., Bochenek K., Basista M., Schubert Th.♦, Jehring U.♦, Litniewski J., Mackiewicz S., Comparative assessment of Young’s modulus measurements of metal-ceramic composites using mechanical and non-destructive tests and micro-CT based computational modeling,
COMPUTATIONAL MATERIALS SCIENCE, ISSN: 0927-0256, DOI: 10.1016/j.commatsci.2013.04.007, Vol.77, pp.19-30, 2013 Streszczenie: It is commonly known that the available non-destructive and mechanical methods of the Young modulus measurement yield different results. This paper presents comparison of the results of experimental determination and numerical modeling of the Young modulus of Cr–Al2O3–Re composites (MMC) processed by a powder metallurgical method (SPS). In the computational model a finite element analysis is combined with images of the real material microstructure obtained from micro-computed tomography (micro-CT). Experimental measurements were carried out by four testing methods: three-point bending, resonance frequency damping analysis (RFDA), ultrasonic pulse-echo technique, and scanning acoustic microscopy. The paper also addresses the issue which of the four experimental methods at hand gives results closest to the theoretical predictions of the micro-CT based FEM model. Słowa kluczowe: Finite element analysis (FEA), Micro-CT based FE model, Metal matrix composites, Elastic modulus, Mechanical and nondestructive techniques Afiliacje autorów:
Węglewski W. | - | IPPT PAN | Bochenek K. | - | IPPT PAN | Basista M. | - | IPPT PAN | Schubert Th. | - | Fraunhofer Institut für Fertigungstechnik und Angewandte Materialforschung (DE) | Jehring U. | - | Fraunhofer Institut für Fertigungstechnik und Angewandte Materialforschung (DE) | Litniewski J. | - | IPPT PAN | Mackiewicz S. | - | IPPT PAN |
| 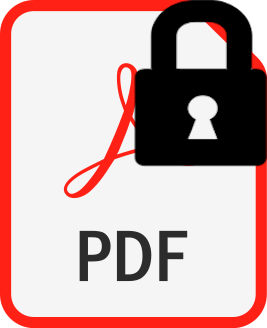 | 30p. |