1. |
Bieniek K., Majewski M.♦, Hołobut P., Kowalczyk-Gajewska K., Anisotropic effect of regular particle distribution in elastic–plastic composites: The modified tangent cluster model and numerical homogenization,
International Journal of Engineering Science, ISSN: 0020-7225, DOI: 10.1016/j.ijengsci.2024.104118, Vol.203, pp.104118-1-104118-27, 2024 Streszczenie: Estimation of macroscopic properties of heterogeneous materials has always posed significant problems. Procedures based on numerical homogenization, although very flexible, consume a lot of time and computing power. Thus, many attempts have been made to develop analytical models that could provide robust and computationally efficient tools for this purpose. The goal of this paper is to develop a reliable analytical approach to finding the effective elastic–plastic response of metal matrix composites (MMC) and porous metals (PM) with a predefined particle or void distribution, as well as to examine the anisotropy induced by regular inhomogeneity arrangements. The proposed framework is based on the idea of Molinari & El Mouden (1996) to improve classical mean-field models of thermoelastic media by taking into account the interactions between each pair of inhomogeneities within the material volume, known as a cluster model. Both elastic and elasto-plastic regimes are examined. A new extension of the original formulation, aimed to account for the non-linear plastic regime, is performed with the use of the modified tangent linearization of the metal matrix constitutive law. The model uses the second stress moment to track the accumulated plastic strain in the matrix. In the examples, arrangements of spherical inhomogeneities in three Bravais lattices of cubic symmetry (Regular Cubic, Body-Centered Cubic and Face-Centered Cubic) are considered for two basic material scenarios: “hard-in-soft” (MMC) and “soft-in-hard” (PM). As a means of verification, the results of micromechanical mean-field modeling are compared with those of numerical homogenization performed using the Finite Element Method (FEM). In the elastic regime, a comparison is also made with several other micromechanical models dedicated to periodic composites. Within both regimes, the results obtained by the cluster model are qualitatively and quantitatively consistent with FEM calculations, especially for volume fractions of inclusions up to 40%. Słowa kluczowe: Periodic composite , Micro-mechanics , Effective properties, Elasto-plasticity, Particle interactions Afiliacje autorów:
Bieniek K. | - | IPPT PAN | Majewski M. | - | inna afiliacja | Hołobut P. | - | IPPT PAN | Kowalczyk-Gajewska K. | - | IPPT PAN |
| 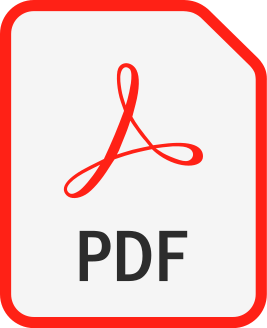 | 200p. |
2. |
Kowalczyk-Gajewska K., Maj M., Bieniek K., Majewski M., Opiela K.C., Zieliński T.G., Cubic elasticity of porous materials produced by additive manufacturing: experimental analyses, numerical and mean-field modelling,
ARCHIVES OF CIVIL AND MECHANICAL ENGINEERING, ISSN: 1644-9665, DOI: 10.1007/s43452-023-00843-z, Vol.24, pp.34-1-34-22, 2024 Streszczenie: Although the elastic properties of porous materials depend mainly on the volume fraction of pores, the details of pore distribution within the material representative volume are also important and may be the subject of optimisation. To study their effect, experimental analyses were performed on samples made of a polymer material with a predefined distribution of spherical voids, but with various porosities due to different pore sizes. Three types of pore distribution with cubic symmetry were considered and the results of experimental analyses were confronted with mean-field estimates and numerical calculations. The mean-field ‘cluster’ model is used in which the mutual interactions between each of the two pores in the predefined volume are considered. As a result, the geometry of pore distribution is reflected in the anisotropic effective properties. The samples were produced using a 3D printing technique and tested in the regime of small strain to assess the elastic stiffness. The digital image correlation method was used to measure material response under compression. As a reference, the solid samples were also 3D printed and tested to evaluate the polymer matrix stiffness. The anisotropy of the elastic response of porous samples related to the arrangement of voids was assessed. Young’s moduli measured for the additively manufactured samples complied satisfactorily with modelling predictions for low and moderate pore sizes, while only qualitatively for larger porosities. Thus, the low-cost additive manufacturing techniques may be considered rather as preliminary tools to prototype porous materials and test mean-field approaches, while for the quantitative and detailed model validation, more accurate additive printing techniques should be considered. Research paves the way for using these computationally efficient models in optimising the microstructure of heterogeneous materials and composites. Słowa kluczowe: Pore configuration, Anisotropy, Elasticity, Micro-mechanics, Additive manufacturing Afiliacje autorów:
Kowalczyk-Gajewska K. | - | IPPT PAN | Maj M. | - | IPPT PAN | Bieniek K. | - | IPPT PAN | Majewski M. | - | IPPT PAN | Opiela K.C. | - | IPPT PAN | Zieliński T.G. | - | IPPT PAN |
| 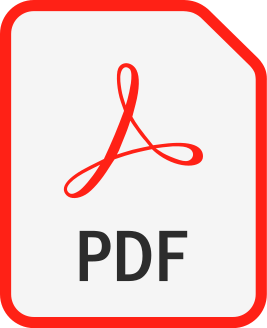 | 140p. |