1. |
Kopeć M., Gunputh U.♦, Williams G.♦, Wojcieck M.♦, Kowalewski Z., Wood P.♦, On the Cover: Fatigue Damage Evolution in SS316L Produced by Powder Bed Fusion in Different Orientations with Reused Powder Feedstock,
EXPERIMENTAL MECHANICS, ISSN: 0014-4851, DOI: 10.1007/s11340-025-01179-w, pp.1-1, 2025, EDITORIAL Abstract: Background Metal Laser Powder Bed Fusion Melting (LPBF-M) is considered economically viable and environmentally
sustainable because of the possibility of reusing the residual powder feedstock leftover in the build chamber after a part
build is completed. There is however limited information on the fatigue damage development of LPBF-M samples made
from reused feedstock.
Objective In this paper, the stainless steel 316 L (SS316L) powder feedstock was examined and characterised after 25
reuses, following which the fatigue damage development of material samples made from the reused powder was assessed.
Methods The suitability of the powder to LPBF-M technology was evaluated by microstructural observations and measurements of Hall flow, apparent and tapped density as well as Carr’s Index and Hausner ratio. LPBF-M bar samples in three
build orientations (Z – vertical, XY – horizontal, ZX – 45° from the build plate) were built for fatigue testing. They were
then subjected to fatigue testing under load control using full tension and compression cyclic loading and stress asymmetry
coefficient equal to -1 in the range of stress amplitude from ± 300 MPa to ± 500 MPa.
Results Samples made from reused powder (25 times) in the LPBF-M process exhibited similar fatigue performance to fresh
unused powder although a lower ductility for vertical samples was observed during tensile testing. Printing in horizontal
(XY) and diagonal (ZX) directions, with reused powder, improved the service life of the SS316L alloy in comparison to
the vertical (Z).
Conclusions Over the 25 reuses of the powder feedstock there was no measurable difference in the flowability between the
fresh (Hall Flow: 21.4 s/50 g) and reused powder (Hall Flow: 20.6 s/50 g). This confirms a uniform and stable powder feeding
process during LPBF-M for both fresh and reused powder. The analysis of fatigue damage parameter, D, concluded cyclic
plasticity and ratcheting to be the main mechanism of damage. Keywords: SS316L ,Stainless steel,Fatigue,Additive manufacturing,Laser Powder Bed Fusion Melting (LPBF-M) Affiliations:
Kopeć M. | - | IPPT PAN | Gunputh U. | - | other affiliation | Williams G. | - | University of Derby (GB) | Wojcieck M. | - | other affiliation | Kowalewski Z. | - | IPPT PAN | Wood P. | - | University of Derby (GB) |
| 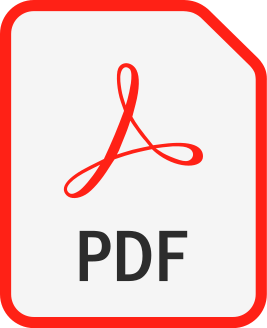 |
2. |
Kopeć M., Gunputh U.♦, Williams G.♦, Macek W.♦, Kowalewski Z.L., Wood P.♦, Fatigue Damage Evolution in SS316L Produced by Powder Bed Fusion in Different Orientations with Reused Powder Feedstock,
EXPERIMENTAL MECHANICS, ISSN: 0014-4851, DOI: 10.1007/s11340-024-01118-1, pp.1-16, 2024 Abstract: Background
Metal Laser Powder Bed Fusion Melting (LPBF-M) is considered economically viable and environmentally sustainable because of the possibility of reusing the residual powder feedstock leftover in the build chamber after a part build is completed. There is however limited information on the fatigue damage development of LPBF-M samples made from reused feedstock.
Objective
In this paper, the stainless steel 316 L (SS316L) powder feedstock was examined and characterised after 25 reuses, following which the fatigue damage development of material samples made from the reused powder was assessed.
Methods
The suitability of the powder to LPBF-M technology was evaluated by microstructural observations and measurements of Hall flow, apparent and tapped density as well as Carr’s Index and Hausner ratio. LPBF-M bar samples in three build orientations (Z – vertical, XY – horizontal, ZX – 45° from the build plate) were built for fatigue testing. They were then subjected to fatigue testing under load control using full tension and compression cyclic loading and stress asymmetry coefficient equal to -1 in the range of stress amplitude from ± 300 MPa to ± 500 MPa.
Results
Samples made from reused powder (25 times) in the LPBF-M process exhibited similar fatigue performance to fresh unused powder although a lower ductility for vertical samples was observed during tensile testing. Printing in horizontal (XY) and diagonal (ZX) directions, with reused powder, improved the service life of the SS316L alloy in comparison to the vertical (Z).
Conclusions
Over the 25 reuses of the powder feedstock there was no measurable difference in the flowability between the fresh (Hall Flow: 21.4 s/50 g) and reused powder (Hall Flow: 20.6 s/50 g). This confirms a uniform and stable powder feeding process during LPBF-M for both fresh and reused powder. The analysis of fatigue damage parameter, D, concluded cyclic plasticity and ratcheting to be the main mechanism of damage. Keywords: SS316L ,Stainless steel,Fatigue ,Additive manufacturing,Laser Powder Bed Fusion Melting (LPBF-M) Affiliations:
Kopeć M. | - | IPPT PAN | Gunputh U. | - | other affiliation | Williams G. | - | University of Derby (GB) | Macek W. | - | other affiliation | Kowalewski Z.L. | - | IPPT PAN | Wood P. | - | University of Derby (GB) |
| 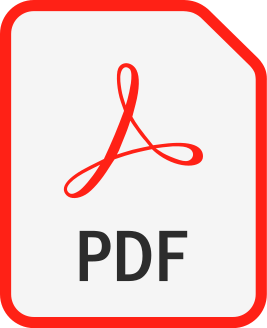 |
3. |
Kopeć M., Gunputh U.♦, Macek W.♦, Kowalewski Z.L., Wood P.♦, Orientation effects on the fracture behaviour of additively manufactured stainless steel 316L subjected to high cyclic fatigue,
Theoretical and Applied Fracture Mechanics, ISSN: 0167-8442, DOI: 10.1016/j.tafmec.2024.104287, pp.1-20, 2024 Abstract: In this paper, stainless steel 316L (SS316L) bars were additively manufactured (AM) in three orientations (Z – vertical, XY – horizontal, ZX45 – midway between vertical and horizontal) by using the Laser Powder Bed Fusion Melting (LPBF-M) method. The AM specimens were subjected to load control fatigue testing under full tension and compression (R = -1) at stress amplitudes ±350, ±400 and ±450 MPa. The XY and ZX45 printing orientations were found to significantly improve service life. Although similar strain response was found for each orientation when the same stress amplitude was applied, slightly different fracture mechanisms were identified during the post-mortem surface observations. Keywords: SS316L,stainless steel,fatigue,additive manufacturing,Laser Powder Bed Fusion Melting (LPBF-M) Affiliations:
Kopeć M. | - | IPPT PAN | Gunputh U. | - | other affiliation | Macek W. | - | other affiliation | Kowalewski Z.L. | - | IPPT PAN | Wood P. | - | University of Derby (GB) |
| 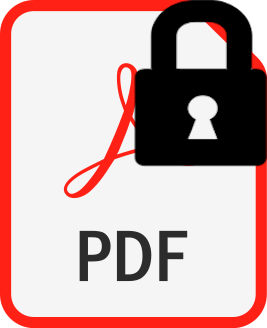 |