1. |
Psiuk R., Chrzanowska-Giżyńska J.♦, Denis P., Wyszkowska E.♦, Wiśniewska M.♦, Lipińska M.♦, Wojtiuk E.♦, Kurpaska Ł.♦, Smolik J.♦, Mościcki T. P., Microstructural and properties investigations of tantalum-doped tungsten diboride ceramic coatings via HiPIMS and RF magnetron sputtering,
ARCHIVES OF CIVIL AND MECHANICAL ENGINEERING, ISSN: 1644-9665, DOI: 10.1007/s43452-024-01050-0, Vol.24, No.239, pp.1-16, 2024 Streszczenie: In this work, tantalum-doped tungsten boride ceramic coatings were deposited from a single sputtering target with the radio frequency (RF) and high-power impulse magnetron sputtering (HiPIMS) methods. Two-inch torus targets were synthesised from pure elements with the spark plasma sintering (SPS) method with a stoichiometric composition of W1-xTaxB2.5 (x = 0, 0.08, 0.16, 0.24). Films were deposited with RF and HiPIMS power suppliers at process temperatures from RT to 600 °C. The substrate heating and the energy of the ionised material impacting the substrate increase the surface diffusivity of adatoms and are crucial in the deposition process. The results of SEM and XRD investigations clearly show that the addition of tantalum also changes the microstructure of the deposited films. The coatings without tantalum possess a finer microstructure than those with 24% of tantalum. The structure of films is homogeneous along the film thickness and composed mainly of columns with a (0001) preferred orientation. Deposited coatings are composed mainly of P6/mmm α-WB2 structures. The analysis of nanoindentation results allowed us to determine that ceramic coatings obtained with the HiPIMS method possess hardness above 41 GPa and a ratio of hardness to reduced Young modulus above 0.1. The thickness of HiPIMS-deposited films is relatively small: only around 60% of the RF magnetron sputtered coatings even when the average power input was two times higher. However, it has been shown that the RF coatings require heating the substrate above 400 °C to obtain a crystalline structure, while the HiPIMS method allows for a reduction of the substrate temperature to 300 °C. Słowa kluczowe: RF magnetron sputtering, HiPIMS magnetron sputtering, Superhard ceramic coatings, Transition metal borides, Deposition temperature Afiliacje autorów:
Psiuk R. | - | IPPT PAN | Chrzanowska-Giżyńska J. | - | inna afiliacja | Denis P. | - | IPPT PAN | Wyszkowska E. | - | National Centre for Nuclear Research (PL) | Wiśniewska M. | - | Łukasiewicz Research Network – Metal Forming Institute (PL) | Lipińska M. | - | inna afiliacja | Wojtiuk E. | - | inna afiliacja | Kurpaska Ł. | - | National Centre for Nuclear Research (PL) | Smolik J. | - | inna afiliacja | Mościcki T. P. | - | IPPT PAN |
| 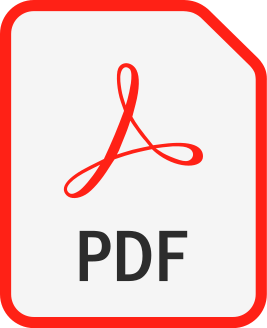 | 140p. |
2. |
Strojny-Nędza A.♦, Pietrzak K. Z., Jóźwik I.♦, Bucholc B., Wyszkowska E.♦, Kurpaska Ł.♦, Grabias A.♦, Malinowska A.♦, Chmielewski M.♦, Effect of Nitrogen Atmosphere Annealing of Alloyed Powders on the Microstructure and Properties of ODS Ferritic Steels,
Materials, ISSN: 1996-1944, DOI: 10.3390/ma17081743, Vol.17, No.8, pp.1-19, 2024 Streszczenie: Oxide Dispersion Strengthened (ODS) ferritic steels are promising materials for the nuclear power sector. This paper presents the results of a study on the sintering process using the Spark Plasma Sintering (SPS) technique, focusing on ODS ferritic steel powders with different contents (0.3 and 0.6 vol.%) of Y2O3. The novelty lies in the analysis of the effect of pre-annealing treatment on powders previously prepared by mechanical alloying on the microstructure, mechanical, and thermal properties of the sinters. Using the SPS method, it was possible to obtain well-densified sinters with a relative density above 98%. Pre-annealing the powders resulted in an increase in the relative density of the sinters and a slight increase in their thermal conductivity. The use of low electron energies during SEM analysis allowed for a fairly good visualization of the reinforcing oxides uniformly dispersed in the matrix. Analysis of the Mössbauer spectroscopy results revealed that pre-annealing induces local atomic rearrangements within the solid solution. In addition, there was an additional spectral component, indicating the formation of a Cr-based paramagnetic phase. The ODS material with a higher Y2O3 content showed increased Vickers hardness values, as well as increased Young’s modulus and nanohardness, as determined by nanoindentation tests. Słowa kluczowe: spark plasma sintering, ODS ferritic steel, mechanical alloying, Mössbauer spectroscopy, nanoindentation Afiliacje autorów:
Strojny-Nędza A. | - | Institute of Electronic Materials Technology (PL) | Pietrzak K. Z. | - | IPPT PAN | Jóźwik I. | - | Institute of Electronic Materials Technology (PL) | Bucholc B. | - | IPPT PAN | Wyszkowska E. | - | National Centre for Nuclear Research (PL) | Kurpaska Ł. | - | National Centre for Nuclear Research (PL) | Grabias A. | - | Lukasiewicz Institute of Microelectronics and Photonics (PL) | Malinowska A. | - | inna afiliacja | Chmielewski M. | - | Institute of Electronic Materials Technology (PL) |
| 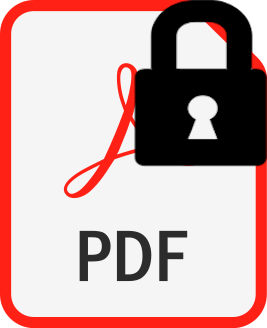 | 140p. |
3. |
Psiuk R., Mościcki T., Chrzanowska-Giżyńska J., Kurpaska ♦, Radziejewska J.♦, Denis P., Garbiec D.♦, Chmielewski M.♦, Mechanical and Thermal Properties of W-Ta-B Coatings Deposited by High-Power Impulse Magnetron Sputtering (HiPIMS),
Materials, ISSN: 1996-1944, DOI: 10.3390/ma16020664, Vol.16, No.2, pp.1-12, 2023 Streszczenie: We present the deposition and characterization of tungsten-tantalum diboride (W,Ta)B2 coatings prepared by the high-power impulse magnetron sputtering technique. We evaluated the influence of pulse duration and substrate bias on the properties of (W,Ta)B2 films. A high hardness of up to 35 GPa measured by nanoindentation was simultaneously obtained with good elastic properties. Changing the pulse duration greatly affected the B/(W+Ta) atomic ratio, which influenced the properties of the coatings. The deposited films are thermally stable at up to 1000 ◦C in vacuum and are able to withstand oxidation at 500 ◦C. Słowa kluczowe: tungsten diboride, high power impulse magnetron sputtering (HiPIMS), hardness, thermal stability, oxidation resistance Afiliacje autorów:
Psiuk R. | - | IPPT PAN | Mościcki T. | - | IPPT PAN | Chrzanowska-Giżyńska J. | - | IPPT PAN | Kurpaska | - | National Centre for Nuclear Research (PL) | Radziejewska J. | - | inna afiliacja | Denis P. | - | IPPT PAN | Garbiec D. | - | Metal Forming Institute, Poznań (PL) | Chmielewski M. | - | Institute of Electronic Materials Technology (PL) |
| 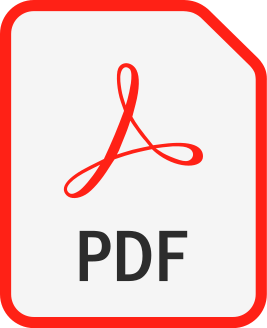 | 140p. |
4. |
Nowak M., Mulewska K.♦, Azarov A.♦, Kurpaska Ł.♦, Ustrzycka A., A peridynamic elasto-plastic damage model for ion-irradiated materials,
INTERNATIONAL JOURNAL OF MECHANICAL SCIENCES, ISSN: 0020-7403, DOI: 10.1016/j.ijmecsci.2022.107806, No.107806, pp.1-46, 2022 Streszczenie: This study presents the novel peridynamic constitutive relations formulated in order to predict the plastic deformation and damage evolution in irradiated materials. The plastic behaviour of the material in which radiation induced defects contribute to the defined peridynamic porosity is described by the Gurson-Tvergaard-Needleman (GTN) yield criterion with irradiation hardening. The definition of peridynamic porosity is proposed as a volume of discontinuities created in the volume of peridynamic particles. The new constitutive relations for irradiation hardening based on the dilatational part of elastic strain energy are formulated. The physical relevance of coupling the porosity with the nonlinear irradiation hardening is discussed. The expressions for the yield function, kinetics of evolution of radiation induced porosity, irradiation hardening and plastic flow rule are derived in terms of the peridynamics variables. The peridynamic predictions are calibrated based on the experimental data obtained during the advanced experimental campaigns dedicated to irradiated materials to verify the validity of the proposed constitutive model. Ion irradiation campaigns were carried out to mimic the effects of neutron irradiation. A series of indentation experiments were conducted to elucidate the effects of material structure modification and assess the hardening effect originating from radiation defects. Słowa kluczowe: Peridynamics,Constitutive modeling,Radiation induced damage,Peridynamic porosity,Gurson yield function,Irradiation hardening,Ion irradiation,Nano-indentation test Afiliacje autorów:
Nowak M. | - | IPPT PAN | Mulewska K. | - | National Centre for Nuclear Research (PL) | Azarov A. | - | inna afiliacja | Kurpaska Ł. | - | National Centre for Nuclear Research (PL) | Ustrzycka A. | - | IPPT PAN |
| 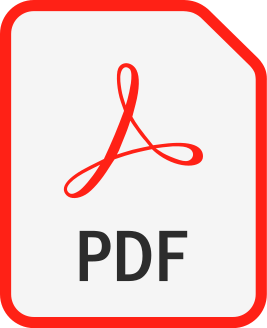 | 140p. |
5. |
Mościcki T., Chrzanowska-Giżyńska J., Psiuk R., Denis P., Mulewska K.♦, Kurpaska Ł.♦, Chmielewski M.♦, Wiśniewska M.♦, Garbiec D.♦, Thermal and mechanical properties of (W,Zr)B2-z coatings deposited by RF magnetron sputtering method,
International Journal of Refractory Metals and Hard Materials, ISSN: 0263-4368, DOI: 10.1016/j.ijrmhm.2022.105811, Vol.105, pp.105811-1-8, 2022 Streszczenie: Magnetron sputtered WB2 coatings doped with 8, 11 and 16 at.% zirconium were analysed using energy dispersive spectroscopy, X-ray diffraction and nanoindentation under the load of 4, 7 and 10 mN. It has been observed that these coatings crystallize in the α-AlB2 and ω-W2B5 prototype structure. Phenomenon responsible for this is an increase of the zirconium content which causes an increase in the ω-W2B5 phase. All the deposited coatings have a hardness of about 45 GPa while Young's modulus drops down from 497 to 480 GPa with increasing zirconium content. Coatings without doping and doped with 16 at.% zirconium were annealed at 650 °C and subjected to cyclic thermal loads using a maximum temperature 600 °C and cooling with a compressed air. It has been observed that addition of zirconium improved coatings phase stability. Słowa kluczowe: superhard coatings, tungsten diboride, zirconia doping, magnetron sputtering, cycling thermal loads, annealing Afiliacje autorów:
Mościcki T. | - | IPPT PAN | Chrzanowska-Giżyńska J. | - | IPPT PAN | Psiuk R. | - | IPPT PAN | Denis P. | - | IPPT PAN | Mulewska K. | - | National Centre for Nuclear Research (PL) | Kurpaska Ł. | - | National Centre for Nuclear Research (PL) | Chmielewski M. | - | Institute of Electronic Materials Technology (PL) | Wiśniewska M. | - | Łukasiewicz Research Network – Metal Forming Institute (PL) | Garbiec D. | - | Metal Forming Institute, Poznań (PL) |
| 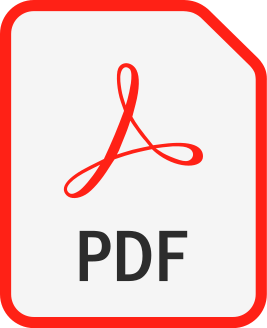 | 140p. |
6. |
Nosewicz S., Bazarnik P.♦, Clozel M.♦, Kurpaska Ł.♦, Jenczyk P., Jarząbek D., Chmielewski M.♦, Romelczyk-Baishya B.♦, Lewandowska M.♦, Pakieła Z.♦, Huang Y.♦, Langdon T.G.♦, A multiscale experimental analysis of mechanical properties and deformation behavior of sintered copper–silicon carbide composites enhanced by high-pressure torsion,
ARCHIVES OF CIVIL AND MECHANICAL ENGINEERING, ISSN: 1644-9665, DOI: 10.1007/s43452-021-00286-4, Vol.21, pp.131-1-19, 2021 Streszczenie: Experiments were conducted to investigate, within the framework of a multiscale approach, the mechanical enhancement, deformation and damage behavior of copper–silicon carbide composites (Cu–SiC) fabricated by spark plasma sintering (SPS) and the combination of SPS with high-pressure torsion (HPT). The mechanical properties of the metal–matrix composites were determined at three different length scales corresponding to the macroscopic, micro- and nanoscale. Small punch testing was employed to evaluate the strength of composites at the macroscopic scale. Detailed analysis of microstructure evolution related to SPS and HPT, sample deformation and failure of fractured specimens was conducted using scanning and transmission electron microscopy. A microstructural study revealed changes in the damage behavior for samples processed by HPT and an explanation for this behavior was provided by mechanical testing performed at the micro- and nanoscale. The strength of copper samples and the metal–ceramic interface was determined by microtensile testing and the hardness of each composite component, corresponding to the metal matrix, metal–ceramic interface, and ceramic reinforcement, was measured using nano-indentation. The results confirm the advantageous effect of large plastic deformation on the mechanical properties of Cu–SiC composites and demonstrate the impact on these separate components on the deformation and damage type. Słowa kluczowe: copper–silicon carbide composite, high-pressure torsion, metal–matrix composites, multiscale analysis, nano-indentation, small punch test Afiliacje autorów:
Nosewicz S. | - | IPPT PAN | Bazarnik P. | - | Politechnika Warszawska (PL) | Clozel M. | - | National Centre for Nuclear Research (PL) | Kurpaska Ł. | - | National Centre for Nuclear Research (PL) | Jenczyk P. | - | IPPT PAN | Jarząbek D. | - | IPPT PAN | Chmielewski M. | - | Institute of Electronic Materials Technology (PL) | Romelczyk-Baishya B. | - | Politechnika Warszawska (PL) | Lewandowska M. | - | inna afiliacja | Pakieła Z. | - | Politechnika Warszawska (PL) | Huang Y. | - | Bournemouth University (GB) | Langdon T.G. | - | University of Southampton (GB) |
| 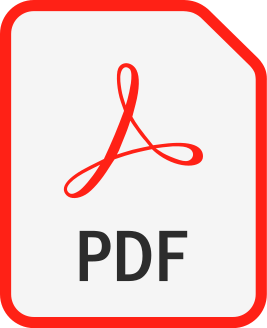 | 140p. |
7. |
Ustrzycka A., Skoczeń B.♦, Nowak M., Kurpaska Ł.♦, Wyszkowska E.♦, Jagielski J.♦, Elastic–plastic-damage model of nano-indentation of the ion-irradiated 6061 aluminium alloy,
INTERNATIONAL JOURNAL OF DAMAGE MECHANICS, ISSN: 1056-7895, DOI: 10.1177/1056789520906209, pp.1-35, 2020 Streszczenie: The paper presents experimental and numerical characterization of damage evolution for ion-irradiated materials subjected to plastic deformation during nano-indentation. Ion irradiation technique belongs to the methods where creation of radiation-induced defects is controlled with a high accuracy (including both, concentration and depth distribution control), and allows to obtain materials having a wide range of damage level, usually expressed in terms of displacements per atom (dpa) scale. Ion affected layers are usually thin, typically less than 1 micrometer thick. Such a low thickness requires to use nano-indentation technique to measure the mechanical properties of the irradiated layers. The He or Ar ion penetration depth reaches approximately 150 nm, which is sufficient to perform several loading-partial-unloading cycles at increasing forces. Damage evolution is reflected by the force-displacement diagram, that is backed by the stress–strain relation including damage. In this work the following approach is applied: dpa is obtained from physics (irradiation mechanisms), afterwards, the radiation-induced damage is defined in the framework of continuum damage mechanics to solve the problem of further evolution of damage fields under mechanical loads. The nature of radiation-induced damage is close to porosity because of formation of clusters of vacancies. The new mathematical relation between radiation damage (dpa) and porosity parameter is proposed. Deformation process experienced by the ion irradiated materials during the nano-indentation test is then numerically simulated by using extended Gurson–Tvergaard– Needleman (GTN) model, that accounts for the damage effects. The corresponding numerical results are validated by means of the experimental measurements. It turns out, that the GTN model quite successfully reflects closure of voids, and increase of material density during the nano-indentation. Słowa kluczowe: radiation-induced damage, evolution of vacancy clusters, nano-indentation test, ion irradiation, radiation hardening Afiliacje autorów:
Ustrzycka A. | - | IPPT PAN | Skoczeń B. | - | Cracow University of Technology (PL) | Nowak M. | - | IPPT PAN | Kurpaska Ł. | - | National Centre for Nuclear Research (PL) | Wyszkowska E. | - | National Centre for Nuclear Research (PL) | Jagielski J. | - | National Centre for Nuclear Research (PL) |
| 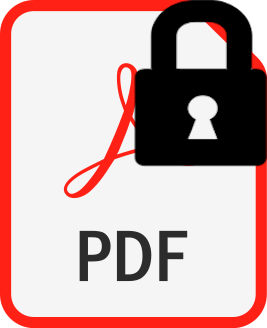 | 100p. |
8. |
Chrzanowska-Giżyńska J., Denis P., Giżyński M.♦, Kurpaska Ł.♦, Mihailescu I.♦, Ristoscu C.♦, Szymański Z., Mościcki T., Thin WBx and WyTi1−yBx films deposited by combined magnetron sputtering and pulsed laser deposition technique,
APPLIED SURFACE SCIENCE, ISSN: 0169-4332, DOI: 10.1016/j.apsusc.2019.02.006, Vol.478, pp.505-513, 2019 Streszczenie: The coatings of tungsten borides (WBx) and tungsten borides doped with titanium (WyTi1−yBx) were deposited by using combined magnetron sputtering - pulsed laser deposition technique. In the case of WBx coatings, pure tungsten target was evaporated by a laser pulse at 1064 nm wavelength and pure boron target was sputtered by a magnetron. In the case of WyTi1−yBx coatings, the W2B5 target was sputtered by the magnetron and titanium target was evaporated by the laser pulse at 1064 nm wavelength. The content of titanium dopant changed from 1.1 to 5.5 at.%. The microstructure, chemical and phase composition of deposited coatings were investigated by means of Scanning Electron Microscopy, Energy Dispersive X-Ray Spectroscopy, X-Ray Photoelectron Spectroscopy and X-Ray Diffractometry, respectively. The Vickers hardness and Young's modulus were determined by using the nanoindentation test. Nanocrystalline WB coatings with dominant WB2 phase were obtained at a substrate temperature of 520 °C. The coatings were superhard with a hardness of 47–50 GPa and the mean value of surface roughness was <6 nm. The WBx coatings doped with 5.5 at.% Ti had hardness similar to the coatings sputtered by magnetron from W2B5 target. Słowa kluczowe: The superhard WyBx thin films was deposited with hybrid laser-magnetron technology, The MS-PLD method allows for the deposition of ternary borides such as WyTi1−yBx, The MS-PLD method enables to control the chemical and phase composition of films, The deposited films are smooth with hardness above 50 GPa, Crystalline films were deposited only on a substrate kept an elevated temperature Afiliacje autorów:
Chrzanowska-Giżyńska J. | - | IPPT PAN | Denis P. | - | IPPT PAN | Giżyński M. | - | Politechnika Warszawska (PL) | Kurpaska Ł. | - | National Centre for Nuclear Research (PL) | Mihailescu I. | - | National Institute for Lasers, Plasma and Radiation Physics (RO) | Ristoscu C. | - | National Institute for Lasers, Plasma and Radiation Physics (RO) | Szymański Z. | - | IPPT PAN | Mościcki T. | - | IPPT PAN |
| 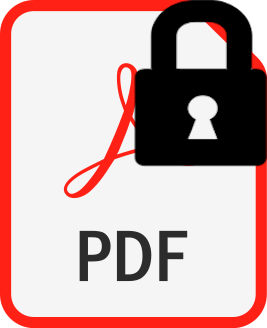 | 140p. |
9. |
Chmielewski M.♦, Nosewicz S., Wyszkowska E.♦, Kurpaska Ł.♦, Strojny-Nędza A.♦, Piątkowska A.♦, Bazarnik P.♦, Pietrzak K., Analysis of the micromechanical properties of copper-silicon carbide composites using nanoindentation measurements,
CERAMICS INTERNATIONAL, ISSN: 0272-8842, DOI: 10.1016/j.ceramint.2019.01.257, Vol.45, No.7A, pp.9164-9173, 2019 Streszczenie: The study presents a detailed analysis of the impact of the coating type of silicon carbide particles and its share by volume on the microstructure and micromechanical properties of Cu-SiC composites. In order to protect the carbide from decomposition during the manufacturing of the composites, the surface of SiC was modified via a plasma vapour deposition technique with a layer of metals (W, Cr, Ti and Ni). Composites with a variable share of the ceramic phase (10–50 %vol.) were obtained at a temperature of 950 °C using spark plasma sintering. An analysis of the structures of the composites, especially in the metal-ceramic boundary region, was conducted with the use of scanning and transmission electron microscopy. The mechanical properties of the composites in the Cu-interface-SiC system were studied via a nanoindentation technique. The comparison of the results of hardness and Young's modulus studies were completed in relation to the actual structures of the materials, which in turn made it possible to determine the impact of the interfacial structure on the global properties of the composite materials. Słowa kluczowe: copper-silicon carbide composites, nanoindentation, SPS, interface study Afiliacje autorów:
Chmielewski M. | - | Institute of Electronic Materials Technology (PL) | Nosewicz S. | - | IPPT PAN | Wyszkowska E. | - | National Centre for Nuclear Research (PL) | Kurpaska Ł. | - | National Centre for Nuclear Research (PL) | Strojny-Nędza A. | - | Institute of Electronic Materials Technology (PL) | Piątkowska A. | - | Institute of Electronic Materials Technology (PL) | Bazarnik P. | - | Politechnika Warszawska (PL) | Pietrzak K. | - | IPPT PAN |
| 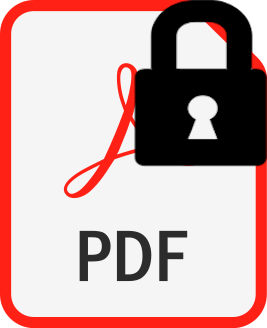 | 100p. |
10. |
Chrzanowska-Giżyńska J., Denis P., Woźniacka S., Kurpaska Ł.♦, Mechanical properties and thermal stability of tungsten boride films deposited by radio frequency magnetron sputtering,
CERAMICS INTERNATIONAL, ISSN: 0272-8842, DOI: 10.1016/j.ceramint.2018.07.208, Vol.44, No.16, pp.19603-19611, 2018 Streszczenie: Tungsten and boron compounds belong to the group of superhard materials since their hardness could exceed 40 GPa. In this study, the properties of the tungsten boride WBx coatings deposited by radio frequency magnetron sputtering were investigated. The sputtering was performed from specially prepared targets that were composed of boron and tungsten mixed in a molar ratio of 2.5 and sintered in Spark Plasma Sintering (SPS) process. WB films were deposited on silicon (100) and stainless steel 304 substrates at temperatures of 23 ÷ 770 °C. Microstructure, chemical and phase composition were investigated by using Scanning Electron Microscope (SEM), X-Ray Photoelectron Spectroscopy (XPS) and X-Ray Diffraction (XRD), respectively. The mechanical properties like Vickers hardness and Young's modulus were obtained by using nanoindentation test at a load of 5 ÷ 100 mN. The friction coefficient and wear resistance of αWB coatings were investigated in scratch test and reciprocal sliding wear instrumentation. Moreover, in order to investigate thermal properties, the αWB films were annealed at 1000 °C in argon/air for 1 h and at 250 °C for 2 h in air atmosphere. Results of our research confirm that αWB coatings can be considered as an alternative to superhard materials in the production of wear resistant, long-lasting tools. Słowa kluczowe: Hard coatings, Hard materials, Magnetron sputtering, Mechanical properties, Thermal properties, Tungsten boride Afiliacje autorów:
Chrzanowska-Giżyńska J. | - | IPPT PAN | Denis P. | - | IPPT PAN | Woźniacka S. | - | IPPT PAN | Kurpaska Ł. | - | National Centre for Nuclear Research (PL) |
| 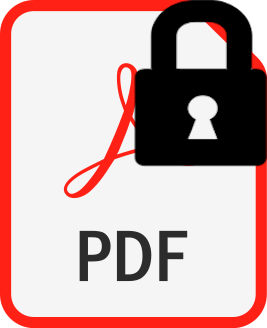 | 40p. |
11. |
Jóźwik I.♦, Strojny-Nędza A.♦, Chmielewski M.♦, Pietrzak K.♦, Kurpaska Ł.♦, Nosewicz S., High resolution SEM characterization of nano-precipitates in ODS steels,
MICROSCOPY RESEARCH AND TECHNIQUE, ISSN: 1059-910X, DOI: 10.1002/jemt.23004, Vol.81, No.5, pp.502-508, 2018 Streszczenie: The performance of the present-day scanning electron microscopy (SEM) extends far beyond delivering electronic images of the surface topography. Oxide dispersion strengthened (ODS) steel is on of the most promising materials for the future nuclear fusion reactor because of its good radiation resistance, and higher operation temperature up to 750°C. The microstructure of ODS should not exceed tens of nm, therefore there is a strong need in a fast and reliable technique for their characterization. In this work, the results of low-kV SEM characterization of nanoprecipitates formed in the ODS matrix are presented. Application of highly sensitive photo-diode BSE detector in SEM imaging allowed for the registration of single nm-sized precipitates in the vicinity of the ODS alloys. The composition of the precipitates has been confirmed by TEM-EDS. Słowa kluczowe: ODS steels, scanning electron microscopy, spark plasma sintering Afiliacje autorów:
Jóźwik I. | - | Institute of Electronic Materials Technology (PL) | Strojny-Nędza A. | - | Institute of Electronic Materials Technology (PL) | Chmielewski M. | - | Institute of Electronic Materials Technology (PL) | Pietrzak K. | - | inna afiliacja | Kurpaska Ł. | - | National Centre for Nuclear Research (PL) | Nosewicz S. | - | IPPT PAN |
| 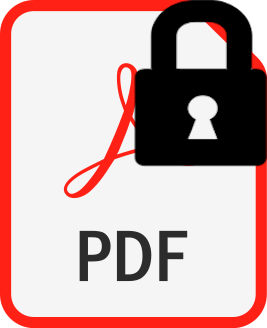 | 25p. |
12. |
Chmielewski M.♦, Nosewicz S., Kurpaska Ł.♦, Romelczyk B.♦, Evolution of material properties during the sintering process of Cr-Re-Al2O3 composites,
COMPOSITES PART B-ENGINEERING, ISSN: 1359-8368, DOI: 10.1016/j.compositesb.2016.04.065, Vol.98, pp.88-96, 2016 Streszczenie: This paper constitutes an analysis of the effect of heat treatment time on the properties of Cr-Re-Al2O3 composite materials. It was found that as a result of sintering, rhenium is dissolved in chromium to create chromium-rhenium solid solution. This process is time-dependent, therefore as the time extends, the structure of material becomes homogenous, which improves its mechanical properties. Within the frame of herein presented studies, a series of technological tests have been carried out for a constant sintering temperature (1450°C) and pressure (30 MPa), with the use of a variable holding time in the maximum temperature. As a result, changes in the structure of Crsingle bondRe matrix have been determined and the resulting changes in the properties of composite. Based on those tests, optimal conditions of the sintering process have been determined from the point of view of obtaining a homogenous structure and the most beneficial properties of Cr-Re-Al2O3 composites. Słowa kluczowe: Metal-matrix composites (MMCs), Mechanical properties, Mechanical testing, Sintering Afiliacje autorów:
Chmielewski M. | - | Institute of Electronic Materials Technology (PL) | Nosewicz S. | - | IPPT PAN | Kurpaska Ł. | - | National Centre for Nuclear Research (PL) | Romelczyk B. | - | Politechnika Warszawska (PL) |
| 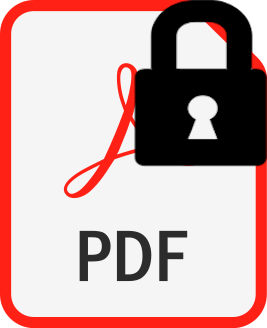 | 45p. |
13. |
Chrzanowska J., Kurpaska Ł.♦, Giżyński M.♦, Hoffman J., Szymański Z., Mościcki T., Fabrication and characterization of superhard tungsten boride layers deposited by radio frequency magnetron sputtering,
CERAMICS INTERNATIONAL, ISSN: 0272-8842, DOI: 10.1016/j.ceramint.2016.04.166, Vol.42, No.10, pp.12221-12230, 2016 Streszczenie: The most promising areas of research of new super-hard materials are transition metal borides. These materials are one of the candidates for future superhard layers that will be competitive to DLC and c-BN layers. In this paper MoB-type tungsten boride (WB) layers were examined. WB layers have been deposited by radio frequency magnetron sputtering on Silicon (100), 304 stainless steel (SS 304) and Inconel 601 substrates. Measured thickness of herein prepared layers was about 1 µm, and all studied samples were dense, uniform and smooth. Surface investigation was performed by using an optical profilometer, atomic force microscopy, and scanning electron microscopy. The structure analysis was examined by using X-ray diffractometer (XRD) and transmission electron microscopy (TEM) techniques. Results from the XRD and TEM analysis showed that WB layers were dominated by (101) reflection and indicated a fine grain structure with a grain size of 20–40 nm. The effect of target sputtering power and ambient gas pressure was investigated. The hardness of WB layers deposited on silicon substrate was compared under the load from 1 mN to 5 mN. The hardness of WB layers deposited on SS 304 and Inconel was measured up to 50 mN. All layers of WB revealed excellent hardness exceeding 40 GPa. Słowa kluczowe: Borides, Nanohardness, RF magnetron sputtering, Superhard layers, Tungsten boride Afiliacje autorów:
Chrzanowska J. | - | IPPT PAN | Kurpaska Ł. | - | National Centre for Nuclear Research (PL) | Giżyński M. | - | Politechnika Warszawska (PL) | Hoffman J. | - | IPPT PAN | Szymański Z. | - | IPPT PAN | Mościcki T. | - | IPPT PAN |
| 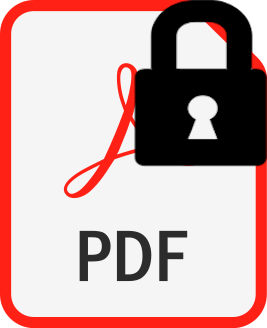 | 40p. |