1. |
Bigoni D.♦, Bordignon N.♦, Piccolroaz A.♦, Stupkiewicz S., Bifurcation of elastic solids with sliding interfaces,
PROCEEDINGS OF THE ROYAL SOCIETY A-MATHEMATICAL PHYSICAL AND ENGINEERING SCIENCES, ISSN: 1364-5021, DOI: 10.1098/rspa.2017.0681, Vol.474, pp.20170681-1-21, 2018 Abstract: Lubricated sliding contact between soft solids is an interesting topic in biomechanics and for the design of small-scale engineering devices. As a model of this mechanical set-up, two elastic nonlinear solids are considered jointed through a frictionless and bilateral surface, so that continuity of the normal component of the Cauchy traction holds across the surface, but the tangential component is null. Moreover, the displacement can develop only in a way that the bodies in contact do neither detach, nor overlap. Surprisingly, this finite strain problem has not been correctly formulated until now, so this formulation is the objective of the present paper. The incremental equations are shown to be non-trivial and different from previously (and erroneously) employed conditions. In particular, an exclusion condition for bifurcation is derived to show that previous formulations based on frictionless contact or 'spring-type' interfacial conditions are not able to predict bifurcations in tension, while experiments—one of which, ad hoc designed, is reported—show that these bifurcations are a reality and become possible when the correct sliding interface model is used. The presented results introduce a methodology for the determination of bifurcations and instabilities occurring during lubricated sliding between soft bodies in contact Keywords: frictionless contact, large strains, nonlinear elasticity Affiliations:
Bigoni D. | - | University of Trento (IT) | Bordignon N. | - | University of Trento (IT) | Piccolroaz A. | - | University of Trento (IT) | Stupkiewicz S. | - | IPPT PAN |
| 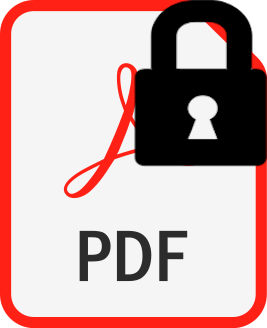 |
2. |
Stupkiewicz S., Piccolroaz A.♦, Bigoni D.♦, Finite-strain formulation and FE implementation of a constitutive model for powder compaction,
COMPUTER METHODS IN APPLIED MECHANICS AND ENGINEERING, ISSN: 0045-7825, DOI: 10.1016/j.cma.2014.09.027, Vol.283, pp.856-880, 2015 Abstract: A finite-strain formulation is developed, implemented and tested for a constitutive model capable of describing the transition from granular to fully dense state during cold forming of ceramic powder. This constitutive model (as well as many others employed for geomaterials) embodies a number of features, such as pressure-sensitive yielding, complex hardening rules and elastoplastic coupling, posing considerable problems in a finite-strain formulation and numerical implementation. A number of strategies are proposed to overcome the related problems, in particular, a neo-Hookean type of modification to the elastic potential and the adoption of the second Piola–Kirchhoff stress referred to the intermediate configuration to describe yielding. An incremental scheme compatible with the formulation for elastoplastic coupling at finite strain is also developed, and the corresponding constitutive update problem is solved by applying a return mapping algorithm. Keywords: Plasticity, Elastoplastic coupling, Finite element method, Automatic differentiation Affiliations:
Stupkiewicz S. | - | IPPT PAN | Piccolroaz A. | - | University of Trento (IT) | Bigoni D. | - | University of Trento (IT) |
| 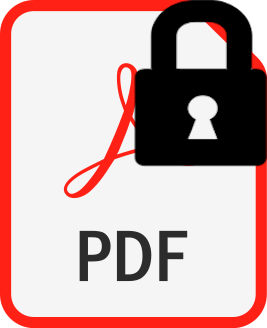 |
3. |
Stupkiewicz S., Piccolroaz A.♦, Bigoni D.♦, Elastoplastic coupling to model cold ceramic powder compaction,
JOURNAL OF THE EUROPEAN CERAMIC SOCIETY, ISSN: 0955-2219, DOI: 10.1016/j.jeurceramsoc.2013.11.017, Vol.34, pp.2839-2848, 2014 Abstract: The simulation of industrial processes involving cold compaction of powders allows for the optimization of the production of both traditional and advanced ceramics. The capabilities of a constitutive model previously proposed by the authors are explored to simulate simple forming processes, both in the small and in the large strain formulation. The model is based on the concept of elastoplastic coupling – providing a relation between density changes and variation of elastic properties – and has been tailored to describe the transition between a granular ceramic powder and a dense green body. Finite element simulations have been compared with experiments on an alumina ready-to-press powder and an aluminum silicate spray-dried granulate. The simulations show that it is possible to take into account friction at the die wall and to predict the state of residual stress, density distribution and elastic properties in the green body at the end of the forming process. Keywords: Ceramic forming, Granular material, Elastoplasticity, Constitutive model, Material modelling Affiliations:
Stupkiewicz S. | - | IPPT PAN | Piccolroaz A. | - | University of Trento (IT) | Bigoni D. | - | University of Trento (IT) |
| 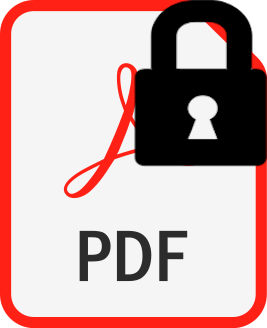 |
4. |
Stupkiewicz S., Denzer R.♦, Piccolroaz A.♦, Bigoni D.♦, Implicit yield function formulation for granular and rock-like materials,
COMPUTATIONAL MECHANICS, ISSN: 0178-7675, DOI: 10.1007/s00466-014-1047-8, Vol.54, pp.1163-1173, 2014 Abstract: The constitutive modelling of granular, porous and quasi-brittle materials is based on yield (or damage) functions, which may exhibit features (for instance, lack of convexity, or branches where the values go to infinity, or ‘false elastic domains’) preventing the use of efficient return-mapping integration schemes. This problem is solved by proposing a general construction strategy to define an implicitly defined convex yield function starting from any convex yield surface. Based on this implicit definition of the yield function, a return-mapping integration scheme is implemented and tested for elastic–plastic (or -damaging) rate equations. The scheme is general and, although it introduces a numerical cost when compared to situations where the scheme is not needed, is demonstrated to perform correctly and accurately. Keywords: Plasticity, Return mapping algorithm, Automatic differentiation Affiliations:
Stupkiewicz S. | - | IPPT PAN | Denzer R. | - | Technische Universität Dortmund (DE) | Piccolroaz A. | - | University of Trento (IT) | Bigoni D. | - | University of Trento (IT) |
| 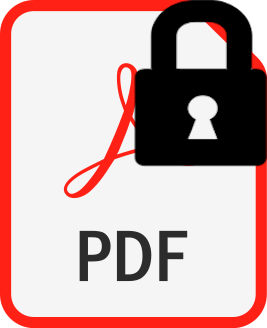 |