1. |
Haponova O.♦, Tarelnyk V.♦, Zhylenko T.♦, Tarelnyk N.♦, Vasilenko O.♦, Pavlovskyi S.♦, Improvement of the Quality Parameters of the Surface Layers of Steel Parts after Aluminizing by Electrospark Alloying. Pt. 2. Results of the Influence of the Productivity of Aluminizing by Electrospark Alloying on the Structural State of Steel Surfaces,
Metallofizika i Noveishie Tekhnologii, ISSN: 1024-1809, DOI: 10.15407/mfint.46.04.0313, Vol.46, No.4, pp.313-324, 2024 Abstract: In the article, investigation is carried out at the second stage of aluminizing, when a consistent substance containing aluminium powder (the first option) or graphite powder and aluminium powder (the second option) is applied to the surface that has undergone aluminizing at the first stage, before further electrospark alloying with an aluminium electrode, and, regardless of the drying of the consistent substance, the aluminizing process is carried out at a discharge energy of 0.52–2.6 J and a productivity of 1.0–2.0 cm2/min, while the discharge energy and productivity are chosen such that the surface roughness decreases by ≅ 3–4 times. At the second stage aluminizing for both options, when using a consistent substance that contains aluminium powder or aluminium powder and graphite powder, the microhardness of the ‘white layer’ and the diffusion zone are increased (to a greater degree when graphite is present in the consistent substance), the surface roughness is decreased, and the integrity of the coating is of 100%. Before practical implementation, it is recommended to carry out the aluminizing process according to the first option at the discharge energy Wp = 4.6–6.8 J, using a consistent substance containing aluminium powder and graphite powder at the second stage. Keywords: electrospark alloying,aluminizing,productivity,surface layer,quality,structure,roughness,microhardness,thickness of the white layer,coating continuity Affiliations:
Haponova O. | - | other affiliation | Tarelnyk V. | - | other affiliation | Zhylenko T. | - | other affiliation | Tarelnyk N. | - | other affiliation | Vasilenko O. | - | other affiliation | Pavlovskyi S. | - | other affiliation |
| 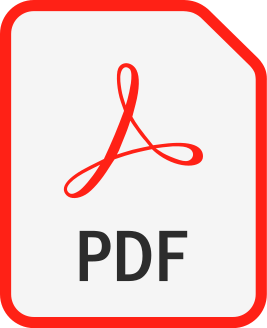 |
2. |
Haponova O.♦, Tarelnyk V.♦, Zhylenko T.♦, Tarelnyk N.♦, Sarzhanov O.♦, Melnyk V.♦, Vlasovets V.♦, Pavlovskyy S.♦, Okhrimenko V.♦, Tkachenko A.♦, Improvement of Quality Parameters of Surface Layers of Steel Parts after Aluminizing by Electrospark Alloying. Pt. 1. Features of the Structural State of Steel Surfaces after Aluminizing,
Metallofizika i Noveishie Tekhnologii, ISSN: 1024-1809, DOI: 10.15407/mfint.45.12.1449, Vol.45, No.12, pp.1449-1472, 2023 Abstract: The structure formation and properties of the surface layers of steel parts after alloying by traditional technologies and the method of electrospark alloying (ESA) is analysed in the article. As a result of the study of the productivity of the ESA process by aluminium electrode-tool, which is one of the important parameters of the ESA technology, reserves are revealed for improving the quality of the surface layers of steel parts during aluminizing. Two options for reducing productivity in relation to the traditional are studied: the first one, when productivity is reduced by ≅ 2 times; the second one, when performance is reduced by ≅ 4 times. As established, in the first variant, when the discharge energy increases from 0.52 to 6.8 J, at the first stage of aluminizing of steel 20 and steel 40, the thickness of the ‘white’ layer from 20 to 75 and from 25 to 110 μm, respectively; the thickness of the diffusion zone increases from 35 to 120 and from 40 to 140 μm, respectively; the microhardness of the ‘white layer’ increases from 2200 to 7400 and from 2400 to 7450 MPa, respectively; the surface roughness Ra increases from 1.1 to 9.0 and from 1.0 to 8.1 μm, respectively, and the continuity increases from 80 to 100% starting with Wp = 4.6 J and from 60 to 100% at Wp = 6.8 J. In the second variant, when the discharge energy increases from 0.52 to 6.8 J, at the first stage of processing steel 20 and steel 40, the thickness of the ‘white’ layer increases for steel 20 from 25 to 60 μm at Wp = 4.6 J, and then it doesn’t change for steel 40 from 30 to 100 μm; the thickness of the diffusion zone increases from 45 to 130, respectively; the microhardness of the ‘white layer’ increases from 2250 to 7300 and from 2450 to 7300 MPa, respectively; the surface roughness Ra increases from 1.3 to 9.0 and from 1.6 to 8.1 μm, respectively, and the continuity for both steel 20 and steel 40 at Wp = 0.52 J is of 95% and further increases to 100%. Keywords: electrospark alloying, aluminizing, productivity, surface layer, structure, roughness, microhardness, thickness of the white layer, coating continuity Affiliations:
Haponova O. | - | other affiliation | Tarelnyk V. | - | other affiliation | Zhylenko T. | - | other affiliation | Tarelnyk N. | - | other affiliation | Sarzhanov O. | - | other affiliation | Melnyk V. | - | other affiliation | Vlasovets V. | - | other affiliation | Pavlovskyy S. | - | other affiliation | Okhrimenko V. | - | other affiliation | Tkachenko A. | - | other affiliation |
| 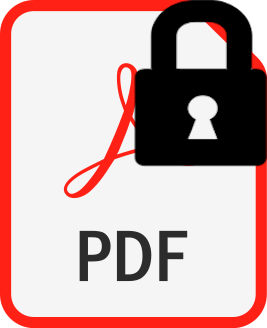 |