1. |
Sequeira A., Węglewski W., Bochenek K., Hutsch T.♦, Jain A., Weissgaerber T.♦, Basista M.A., Thermal Conductivity of AlSi12/Al2O3-Graded Composites Consolidated by Hot Pressing and Spark Plasma Sintering: Experimental Evaluation and Numerical Modeling,
METALLURGICAL AND MATERIALS TRANSACTIONS A-PHYSICAL METALLURGY AND MATERIALS SCIENCE, ISSN: 1073-5623, DOI: 10.1007/s11661-024-07506-5, pp.1-18, 2024 Abstract: Functionally graded metal matrix composites have attracted the attention of various industries as materials with tailorable properties due to spatially varying composition of constituents. This research work was inspired by an application, such as automotive brake disks, which requires advanced materials with improved wear resistance on the outer surface as combined with effective heat flux dissipation of the graded system. To this end, graded AlSi12/Al2O3 composites (FGMs) with a stepwise gradient in the volume fraction of alumina reinforcement were produced by hot pressing and spark plasma sintering techniques. The thermal conductivities of the individual composite layers and the FGMs were evaluated experimentally and simulated numerically using 3D finite element (FE) models based on micro-computed X-ray tomography (micro-XCT) images of actual AlSi12/Al2O3 microstructures. The numerical models incorporated the effects of porosity of the fabricated AlSi12/Al2O3 composites, thermal resistance, and imperfect interfaces between the AlSi12 matrix and the alumina particles. The obtained experimental data and the results of the numerical models are in good agreement, the relative error being in the range of 4 to 6 pct for different compositions and FGMstructure. The predictive capability of the proposed micro-XCT-based FE model suggests that this model can be applied to similar types of composites and different composition gradients. Affiliations:
Sequeira A. | - | IPPT PAN | Węglewski W. | - | IPPT PAN | Bochenek K. | - | IPPT PAN | Hutsch T. | - | other affiliation | Jain A. | - | IPPT PAN | Weissgaerber T. | - | other affiliation | Basista M.A. | - | IPPT PAN |
| 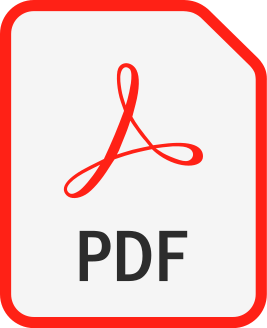 |
2. |
Węglewski W., Sequeira A., Bochenek K., Rosc J.♦, Brunner R.♦, Basista M.A., Finite element modeling of thermal residual stresses in functionally graded aluminum-matrix composites using X-ray micro-computed tomography,
FINITE ELEMENTS IN ANALYSIS AND DESIGN, ISSN: 0168-874X, DOI: 10.1016/j.finel.2024.104239, Vol.241, No.104239, pp.1-16, 2024 Abstract: Metal-ceramic composites by their nature have thermal residual stresses at the micro-level, which can compromise the integrity of structural elements made from these materials. The evaluation of thermal residual stresses is therefore of continuing research interest both experimentally and by modeling. In this study, two functionally graded aluminum alloy matrix composites, AlSi12/Al2O3 and AlSi12/SiC, each consisting of three composite layers with a stepwise gradient of ceramic content (10, 20, 30 vol%), were produced by powder metallurgy. Thermal residual stresses in the AlSi12 matrix and the ceramic reinforcement of the ungraded and graded composites were measured by neutron diffraction. Based on the X-ray micro-computed tomography (micro-XCT) images of the actual microstructure, a series of finite element models were developed to simulate the thermal residual stresses in the AlSi12 matrix and the reinforcing ceramics Al2O3 and SiC. The accuracy of the numerical predictions is high for all cases considered, with a difference of less than 5 % from the neutron diffraction measurements. It is shown numerically and validated by neutron diffraction data that the average residual stresses in the graded AlSi12/Al2O3 and AlSi12/SiC composites are lower than in the corresponding ungraded composites, which may be advantageous for engineering applications. Keywords: Finite element modeling,Micro-XCT,Thermal residual stress,Hot pressing,Aluminum matrix composites Affiliations:
Węglewski W. | - | IPPT PAN | Sequeira A. | - | IPPT PAN | Bochenek K. | - | IPPT PAN | Rosc J. | - | other affiliation | Brunner R. | - | other affiliation | Basista M.A. | - | IPPT PAN |
| 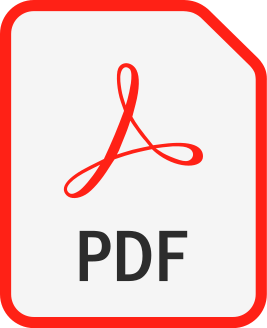 |
3. |
Sequeira A. A., Mohan M.♦, Sachidananda H.♦, Tribological behavior of alumina (Al2O3) and zirconia (ZrO2) plungers used in high pressure pumps,
Discover Applied Sciences, ISSN: 3004-9261, DOI: 10.1007/s42452-024-05654-2, Vol.6, No.254, pp.1-11, 2024 Abstract: Ceramic materials are commonly used in plungers due to high resistance to wear, abrasion, and low coefficient of thermal expansion. Also, they are commonly used in dry conditions without permanent damage, ceasing of pump head and better corrosion resistance than metals due to their inert characteristics. Zirconia (ZrO2) ceramic is used due to its high strength whereas, alumina (Al2O3) is commonly used in industries for high pressure pumps. The toughness of zirconia ceramics is higher than alumina ceramics as it overcomes the inherent brittleness of ceramic materials. It also has higher wear resistance and extends the life of the product. Whereas alumina has better mechanical characteristics such as hardness compared to Zirconia. In this research work tribological behavior of Alumina and Zirconia ceramics used in high pressure pumps have been studied. The wear test using end face wear testing apparatus has been conducted under flat contact for both alumina and ceramic material considering a mean contact pressure of 10 N, 20 N, 30 N and 40 N and sliding velocity of 40 mm/s. The wear test was conducted for 30 min considering a total sliding distance of 1500 m and 3000 m. The wear test results indicate that both alumina and ceramic exhibit lower wear factors and superior mechanical properties. The findings also reveal that the wear rates of Al2O3 and ZrO2 are influenced by friction forces, subsequently impacting the overall wear rate. Also, as the load increases the surface contact area also increases which in turn increases the wear rate. However, zirconia could be a potential substitute for alumina due to its high strength and fracture toughness. Keywords: Ceramics, Composites, Alumina, Zirconia, Wear rate, Toughness Affiliations:
Sequeira A. A. | - | IPPT PAN | Mohan M. | - | other affiliation | Sachidananda H. | - | other affiliation |
| 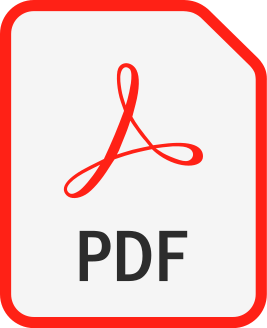 |