1. |
Nisar F., Rojek J., Nosewicz S., Kaszyca K.♦, Chmielewski M.♦, Coupled thermo-electric discrete element model for spark plasma sintering,
POWDER TECHNOLOGY, ISSN: 0032-5910, DOI: 10.1016/j.powtec.2025.120957, Vol.458, No.120957, pp.1-23, 2025 Keywords: Spark plasma sintering, Discrete element method, Thermo-electric coupling, Joule heating Affiliations:
Nisar F. | - | IPPT PAN | Rojek J. | - | IPPT PAN | Nosewicz S. | - | IPPT PAN | Kaszyca K. | - | Lukasiewicz Institute of Microelectronics and Photonics (PL) | Chmielewski M. | - | Institute of Electronic Materials Technology (PL) |
| 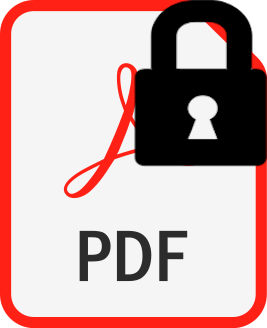 |
2. |
Kaszyca K.♦, Chmielewski M.♦, Bucholc B., Błyskun P.♦, Nisar F., Rojek J., Zybała R.♦, Using the Spark Plasma Sintering System for Fabrication of Advanced Semiconductor Materials,
Materials, ISSN: 1996-1944, DOI: 10.3390/ma17061422, Vol.17, No.1422, pp.1-15, 2024 Abstract: The interest in the Spark Plasma Sintering (SPS) technique has continuously increased over the last few years. This article shows the possibility of the development of an SPS device used for material processing and synthesis in both scientific and industrial applications and aims to present manufacturing methods and the versatility of an SPS device, presenting examples of processing Arc-Melted- (half-Heusler, cobalt triantimonide) and Self-propagating High-temperature Synthesis (SHS)-synthesized semiconductor (bismuth telluride) materials. The SPS system functionality development is presented, the purpose of which was to broaden the knowledge of the nature of SPS processes. This approach enabled the precise design of material sintering processes and also contributed to increasing the repeatability and accuracy of sintering conditions. Keywords: spark plasma sintering, arc melting, semiconductor materials, half-Heusler, bismuth telluride, cobalt triantimonide, SHS, SPS Affiliations:
Kaszyca K. | - | Lukasiewicz Institute of Microelectronics and Photonics (PL) | Chmielewski M. | - | Institute of Electronic Materials Technology (PL) | Bucholc B. | - | IPPT PAN | Błyskun P. | - | other affiliation | Nisar F. | - | IPPT PAN | Rojek J. | - | IPPT PAN | Zybała R. | - | Warsaw University of Technology (PL) |
| 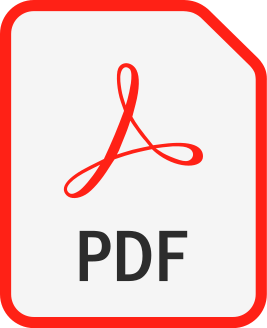 |
3. |
Nisar F., Rojek J., Nosewicz S., Kaszyca K.♦, Chmielewski M.♦, Evaluation of effective thermal conductivity of sintered porous materials using an improved discrete element model,
POWDER TECHNOLOGY, ISSN: 0032-5910, DOI: 10.1016/j.powtec.2024.119546, Vol.437, pp.119546, 2024 Abstract: This work aims to revise and apply an original discrete element model (DEM) to evaluate effective thermal conductivity of sintered porous materials. The model, based on two-particle sintering geometry, calculates inter-particle neck using Constant Volume (CV) criterion. The model was validated using experimental measurements on sintered porous NiAl. For DEM simulations, heterogeneous samples with real particle size distribution and different densities were obtained by simulation of hot pressing. Neck size evaluated using Coble’s and CV models were compared to show that commonly used Coble’s model overestimates neck size and conductivity. The proposed model was improved by neck-size correction to compensate for non-physical overlaps at higher densities and by adding grain-boundary resistance to account for porosity within necks. Resistance contribution from grain boundaries was shown to decrease with increasing density. Thermal conductivity obtained from the improved model was close to experimental results, suggesting validity of the model. Keywords: Discrete element method,Effective thermal conductivity,Porous materials,Sintering,Heat conduction simulation Affiliations:
Nisar F. | - | IPPT PAN | Rojek J. | - | IPPT PAN | Nosewicz S. | - | IPPT PAN | Kaszyca K. | - | Lukasiewicz Institute of Microelectronics and Photonics (PL) | Chmielewski M. | - | Institute of Electronic Materials Technology (PL) |
| 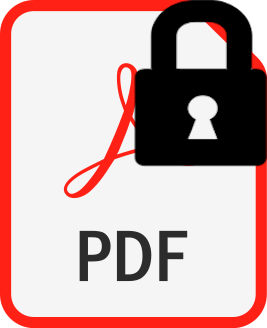 |
4. |
Munawar A.♦, Nisar F., Masood A.♦, Aamer A.♦, Shahin M.♦, Munir K.♦, Umer M.♦, Kargl F.♦, Development of 4- Component Eutectic High Entropy Alloys Using Electromagnetic Levitation Technique,
The Journal of The Minerals, ISSN: 1047-4838, DOI: 10.1007/s11837-024-06988-3, pp.1-9, 2024 | 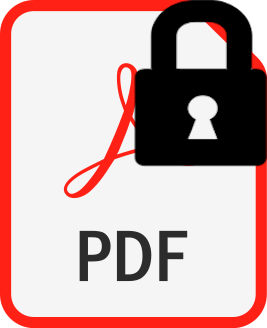 |
5. |
Nisar F., Rojek J., Nosewicz S., Szczepański J., Kaszyca K.♦, Chmielewski M.♦, Discrete element model for effective electrical conductivity of spark plasma sintered porous materials,
Computational Particle Mechanics, ISSN: 2196-4378, DOI: 10.1007/s40571-024-00773-4, pp.1-11, 2024 Abstract: This paper aims to analyse electrical conduction in partially sintered porous materials using an original resistor network model within discrete element framework. The model is based on sintering geometry, where two particles are connected via neck. Particle-to-particle conductance depends on neck size in sintered materials. Therefore, accurate evaluation of neck size is essential to determine conductance. The neck size was determined using volume preservation criterion. Additionally, grain boundary correction factor was introduced to compensate for any non-physical overlaps between particles, particularly at higher densification. Furthermore, grain boundary resistance was added to account for the porosity within necks. For numerical analysis, the DEM sample was generated using real particle size distribution, ensuring a heterogeneous and realistic microstructure characterized by a maximum-to-minimum particle diameter ratio of 15. The DEM sample was subjected to hot press simulation to obtain geometries with different porosity levels. These representative geometries were used to simulate current flow and determine effective electrical conductivity as a function of porosity. The discrete element model (DEM) was validated using experimentally measured electrical conductivities of porous NiAl samples manufactured using spark plasma sintering (SPS). The numerical results were in close agreement with the experimental results, hence proving the accuracy of the model. The model can be used for microscopic analysis and can also be coupled with sintering models to evaluate effective properties during the sintering process. Keywords: Discrete element method, Effective electrical conductivity, Porous materials, Sintering, Resistor network model Affiliations:
Nisar F. | - | IPPT PAN | Rojek J. | - | IPPT PAN | Nosewicz S. | - | IPPT PAN | Szczepański J. | - | IPPT PAN | Kaszyca K. | - | Lukasiewicz Institute of Microelectronics and Photonics (PL) | Chmielewski M. | - | Institute of Electronic Materials Technology (PL) |
| 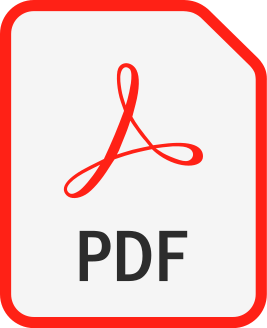 |
6. |
Munawar A.♦, Sadeeda .♦, Asif V.♦, Jafri A.♦, Nisar F.♦, Wegener M.♦, Su J.♦, Kargl F.♦, Effect of Undercooling on the Microstructure and Mechanical Properties of Hyper-eutectic Ni–Sn Alloy,
METALLURGICAL AND MATERIALS TRANSACTIONS A-PHYSICAL METALLURGY AND MATERIALS SCIENCE, ISSN: 1073-5623, DOI: 10.1007/s11661-023-07172-z, pp.1-9, 2023 Abstract: In this study, container-less solidification of hyper-eutectic Ni–Sn alloy has been performed by using the electromagnetic levitation technique. The effect of undercooling on the formed microstructure and on the mechanical properties have been investigated. Growth velocities were determined by high-speed video-imaging of the solidification process. A step change in the growth velocities that are increasing with increasing undercooling is observed. This aligns with an observed first change in the microstructure between low and intermediate undercoolings. At the lower undercoolings, a pro-eutectic Ni3Sn phase along with lamellar eutectic structure in the inter-dendritic region is found. At intermediate undercooling of 100–150 K, a divorced eutectic microstructure is observed whereas at undercoolings above 165 K α-Ni precipitates are observed within β-Ni3Sn dendrites. Microhardness testing revealed higher strength for the lamellar phase as compared to the non-lamellar phase. Nano-indentation has been performed to determine the hardness and strength of individual phases in the microstructure. Affiliations:
Munawar A. | - | other affiliation | Sadeeda . | - | other affiliation | Asif V. | - | other affiliation | Jafri A. | - | other affiliation | Nisar F. | - | other affiliation | Wegener M. | - | other affiliation | Su J. | - | other affiliation | Kargl F. | - | other affiliation |
| 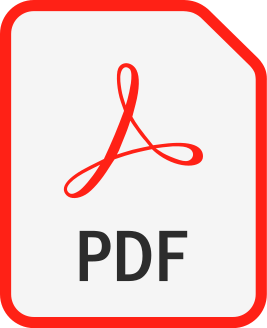 |
7. |
Anwer Z.♦, Umer Malik A.♦, Nisar F.♦, Hafeez Muhammad A.♦, Yaqoob K.♦, Luo X.♦, Ahmad I.♦, Microstructure and mechanical properties of hot isostatic pressed tungsten heavy alloy with FeNiCoCrMn high entropy alloy binder,
Journal of Materials Research and Technology, ISSN: 2238-7854, DOI: 10.1016/j.jmrt.2022.12.078, Vol.22, pp.2897-2909, 2023 Abstract: Microstructural development and mechanical properties of tungsten heavy alloy, WHA, with FeNiCoCrMn high entropy alloy, HEA, binder were investigated and compared to conventional WHA using Fe–Ni binder. Both WHAs, with HEA and conventional Fe–Ni binders, were fabricated by hot isostatic pressing at a temperature of 1450 °C in an argon environment. Scanning electron microscopy revealed that WHA with HEA and conventional binders possessed uniform and well-refined microstructures. Energy dispersive spectroscopy and X-ray diffraction, XRD, spectroscopy validated the formation and composition of HEA, existing as a skeletal network surrounding tungsten grains. HEA binder exhibited an overall increase of 42% in micro Vickers hardness values. Furthermore, hardness values of the tungsten heavy alloy were also seen to rise when fabricated with HEA binder. However, WHA sample with HEA binder was seen to undergo faster strain hardening and a premature failure, leading to lower values of ultimate strength and reduced ductility. Keywords: Tungsten heavy alloys, High entropy alloys, Hot isostatic pressing, Liquid phase sintering Affiliations:
Anwer Z. | - | other affiliation | Umer Malik A. | - | other affiliation | Nisar F. | - | other affiliation | Hafeez Muhammad A. | - | other affiliation | Yaqoob K. | - | other affiliation | Luo X. | - | other affiliation | Ahmad I. | - | other affiliation |
| 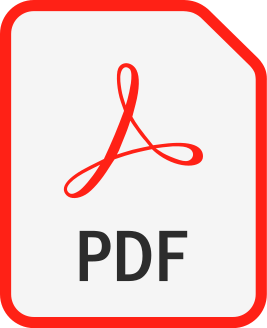 |