1. |
Kalita D.♦, Mulewska K.♦, Jóźwik I.♦, Zaborowska A.♦, Gawęda M.♦, Chromiński W.♦, Bochenek K., Rogal Ł.♦, Metastable β-Phase Ti–Nb Alloys Fabricated by Powder Metallurgy: Effect of Nb on Superelasticity and Deformation Behavior,
METALLURGICAL AND MATERIALS TRANSACTIONS A-PHYSICAL METALLURGY AND MATERIALS SCIENCE, ISSN: 1073-5623, DOI: 10.1007/s11661-023-07285-5, pp.1-17, 2024 Streszczenie: This study investigates the effect of Nb concentration on the mechanical properties, superelasticity, as well as deformation behavior of metastable β-phase Ti–Nb alloys produced via powder metallurgy. The alloys were fabricated through mechanical alloying, followed by consolidation using hot pressing. The resulting microstructure comprises fine β-phase grains with TiC carbide precipitates at the grain boundaries. The study reveals non-linear variations in the values of yield strength for the manufactured materials, which were attributed to the occurrence of various deformation mechanisms activated during the loading. It was found that the mechanisms change with the increasing concentration of Nb in the manner: stress-induced martensitic transformation, twinning, slip. However, all these mechanisms were activated at a reduced concentration of Nb compared to the materials obtained by casting technology previously reported in the literature. This is most probably associated with the elevated oxygen content, which affects the stability of the parent β-phase. The study revealed that superelasticity in Ti–Nb-based alloys prepared using powder metallurgy may be achieved by reducing the content of β-stabilizing elements compared to alloys obtained by conventional technologies. In this study, the Ti–14Nb (at. pct) alloy exhibited the best superelasticity, whereas conventionally fabricated Ti–Nb alloys displayed superelasticity at an Nb concentration of approximately 26 at. pct. The developed material exhibited a non-conventional, one-stage yielding behavior, resulting in a superelastic response at significantly higher stresses compared to conventionally fabricated Ti–Nb alloys. Afiliacje autorów:
Kalita D. | - | inna afiliacja | Mulewska K. | - | National Centre for Nuclear Research (PL) | Jóźwik I. | - | Institute of Electronic Materials Technology (PL) | Zaborowska A. | - | inna afiliacja | Gawęda M. | - | inna afiliacja | Chromiński W. | - | inna afiliacja | Bochenek K. | - | IPPT PAN | Rogal Ł. | - | Institute of Metallurgy and Materials Science, Polish Academy of Sciences (PL) |
| 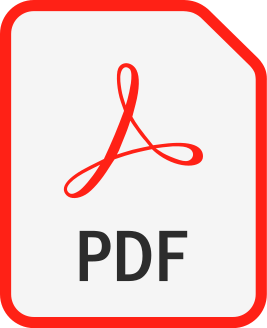 | 200p. |
2. |
Nowak M., Mulewska K.♦, Azarov A.♦, Kurpaska Ł.♦, Ustrzycka A., A peridynamic elasto-plastic damage model for ion-irradiated materials,
INTERNATIONAL JOURNAL OF MECHANICAL SCIENCES, ISSN: 0020-7403, DOI: 10.1016/j.ijmecsci.2022.107806, No.107806, pp.1-46, 2022 Streszczenie: This study presents the novel peridynamic constitutive relations formulated in order to predict the plastic deformation and damage evolution in irradiated materials. The plastic behaviour of the material in which radiation induced defects contribute to the defined peridynamic porosity is described by the Gurson-Tvergaard-Needleman (GTN) yield criterion with irradiation hardening. The definition of peridynamic porosity is proposed as a volume of discontinuities created in the volume of peridynamic particles. The new constitutive relations for irradiation hardening based on the dilatational part of elastic strain energy are formulated. The physical relevance of coupling the porosity with the nonlinear irradiation hardening is discussed. The expressions for the yield function, kinetics of evolution of radiation induced porosity, irradiation hardening and plastic flow rule are derived in terms of the peridynamics variables. The peridynamic predictions are calibrated based on the experimental data obtained during the advanced experimental campaigns dedicated to irradiated materials to verify the validity of the proposed constitutive model. Ion irradiation campaigns were carried out to mimic the effects of neutron irradiation. A series of indentation experiments were conducted to elucidate the effects of material structure modification and assess the hardening effect originating from radiation defects. Słowa kluczowe: Peridynamics,Constitutive modeling,Radiation induced damage,Peridynamic porosity,Gurson yield function,Irradiation hardening,Ion irradiation,Nano-indentation test Afiliacje autorów:
Nowak M. | - | IPPT PAN | Mulewska K. | - | National Centre for Nuclear Research (PL) | Azarov A. | - | inna afiliacja | Kurpaska Ł. | - | National Centre for Nuclear Research (PL) | Ustrzycka A. | - | IPPT PAN |
| 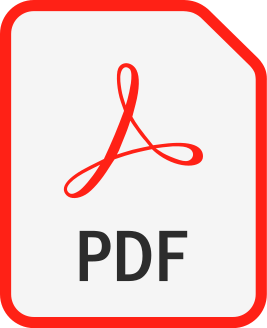 | 140p. |
3. |
Mościcki T., Chrzanowska-Giżyńska J., Psiuk R., Denis P., Mulewska K.♦, Kurpaska Ł.♦, Chmielewski M.♦, Wiśniewska M.♦, Garbiec D.♦, Thermal and mechanical properties of (W,Zr)B2-z coatings deposited by RF magnetron sputtering method,
International Journal of Refractory Metals and Hard Materials, ISSN: 0263-4368, DOI: 10.1016/j.ijrmhm.2022.105811, Vol.105, pp.105811-1-8, 2022 Streszczenie: Magnetron sputtered WB2 coatings doped with 8, 11 and 16 at.% zirconium were analysed using energy dispersive spectroscopy, X-ray diffraction and nanoindentation under the load of 4, 7 and 10 mN. It has been observed that these coatings crystallize in the α-AlB2 and ω-W2B5 prototype structure. Phenomenon responsible for this is an increase of the zirconium content which causes an increase in the ω-W2B5 phase. All the deposited coatings have a hardness of about 45 GPa while Young's modulus drops down from 497 to 480 GPa with increasing zirconium content. Coatings without doping and doped with 16 at.% zirconium were annealed at 650 °C and subjected to cyclic thermal loads using a maximum temperature 600 °C and cooling with a compressed air. It has been observed that addition of zirconium improved coatings phase stability. Słowa kluczowe: superhard coatings, tungsten diboride, zirconia doping, magnetron sputtering, cycling thermal loads, annealing Afiliacje autorów:
Mościcki T. | - | IPPT PAN | Chrzanowska-Giżyńska J. | - | IPPT PAN | Psiuk R. | - | IPPT PAN | Denis P. | - | IPPT PAN | Mulewska K. | - | National Centre for Nuclear Research (PL) | Kurpaska Ł. | - | National Centre for Nuclear Research (PL) | Chmielewski M. | - | Institute of Electronic Materials Technology (PL) | Wiśniewska M. | - | Łukasiewicz Research Network – Metal Forming Institute (PL) | Garbiec D. | - | Metal Forming Institute, Poznań (PL) |
| 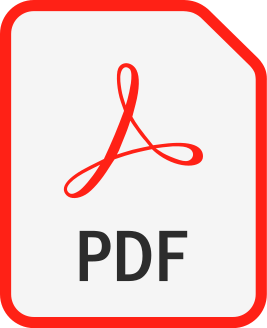 | 140p. |