1. |
Haponova O., Tarelnyk V.♦, Mościcki T., Tarelnyk N.♦, Hybrid Surface Treatment Technologies Based on the Electrospark Alloying Method: A Review,
Coatings, ISSN: 2079-6412, Vol.15, No.6, pp.1-26, 2025 Streszczenie: Technologies for functional coatings are evolving rapidly, with electrospark alloying (ESA) emerging as a promising method for surface modification due to its efficiency and localized impact. This review analyzes the fundamental principles of ESA and the effects of process parameters on coating characteristics and highlights its advantages and limitations. Particular attention is given to hybrid ESA-based technologies, including combinations with laser treatment, plastic deformation, vapor deposition, and polymer-metal overlays. These hybrid methods significantly improve coating quality by enhancing hardness, adhesion, and structural integrity and reducing roughness and defects. However, the multi-parameter nature of these processes presents optimization challenges. This review identifies knowledge gaps related to process reproducibility, control of microstructure formation, and long-term performance under service conditions. Recent breakthroughs in combining ESA with high-energy surface treatments are discussed. Future research should focus on systematic parameter optimization, in situ diagnostics, and predictive modeling to enable the design of application-specific hybrid coatings. Słowa kluczowe: electrospark alloying, hybrid technologies, surface plastic deformation, laser treatment, vapor phase deposition, metal–polymer material, coating, structure, properties, roughness, coating quality, sustainable development goals Afiliacje autorów:
Haponova O. | - | IPPT PAN | Tarelnyk V. | - | Sumy National Agrarian University (UA) | Mościcki T. | - | IPPT PAN | Tarelnyk N. | - | Sumy National Agrarian University (UA) |
| 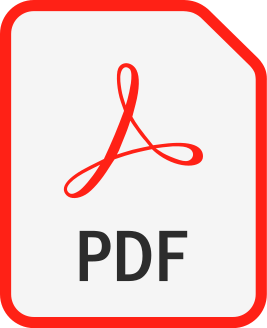 | 100p. |
2. |
Tarelnyk V.♦, Haponova O., Tarelnyk N.♦, Konoplianchenko Y.♦, Sulphurizing of Metal Surfaces by Electrospark-Discharge Alloying. Pt. 2: Tribological Properties of Electrospark Depositing Sulphur-Containing Coating,
Uspekhi Fiziki Metallov, ISSN: 1608-1021, Vol.26, No.2, pp.111-222, 2025 Streszczenie: The essence and technological characteristics of the electrospark alloying (ESA) process, its advantages and disadvantages have been considered in order to use it to improve the tribological properties of bronze and steel parts. A generalization of the available data and results in the literature concerned with the ESA process has been made. Based on the published data, a comparative analysis of various methods for forming combined electrospark coatings (CESC) on bronzes, which include sulphur, the influence of the mode parameters and the compositions of the CESC on the microstructure, mechanical and tribological properties are represented. The methods for practical application in production have been proposed. The methods for forming the self-lubricating electrospark coatings containing molybdenum disulphide on steel substrates have been investigated. There have been represented physical and mechanical characteristics of the coatings, which had been obtained using different strategies, as well as there has been disclosed the nature of their changes depending on the technological parameters of the ESA modes and the types of the starting materials for the anode and cathode, and on the compositions of the environment wherein the ESA process takes place. There have been given the summarized data on the tribological properties of the coatings, which had been obtained on some steel grades using different electrode materials and modes of operation. As demonstrated, the ESA method can be successfully used to reduce the coefficient of friction and to increase the wear resistance of bronze and steel surfaces. There have been specified the proposed electrode materials and ESA process parameters for modifying the surfaces made of some bronzes and steels. Słowa kluczowe: technology, electrospark alloying, coating, microstructure, tribotechnical properties Afiliacje autorów:
Tarelnyk V. | - | Sumy National Agrarian University (UA) | Haponova O. | - | IPPT PAN | Tarelnyk N. | - | Sumy National Agrarian University (UA) | Konoplianchenko Y. | - | inna afiliacja |
| | 70p. |
3. |
Tarelnyk V.♦, Haponova O., Tarelnyk N.♦, Konoplianchenko Y.♦, Sulphurizing of Metal Surfaces by Electrospark-Discharge Alloying. Pt. 1: Structural–Phase State of Sulphur-Containing Coatings on Constructional Steels,
Uspekhi Fiziki Metallov, ISSN: 1608-1021, Vol.26, No.1, pp.146-200, 2025 Streszczenie: The methods of surface sulphur saturation of metal surfaces to provide them with special tribotechnical properties are reviewed and analysed. The main attention is focused on technologies based on the method of electrospark alloying (ESA). As shown, the process of sulphur saturation can be realised by using a special sulphur-containing saturating technical substance (STS). The methods of forming sulphided, sulphocarburized, sulphoaluminized, Al–C–S, and sulphomolybdenum coatings on steels using STS by ESA are considered. The results of sulphur distribution in the surface layer during ESA sulphurizing with a metal electrode using STS are presented. As shown, the sulphur concentration on the surface is of about 0.53–0.60% that gradually decreases deeper into the substrate. The topography of the treated surface and its structure after sulphocarburized of steel surfaces with a graphite electrode using STS containing sulphur are investigated. As found, the coating consists of several layers: a ‘soft’ layer saturated with sulphur, a hardened layer saturated with carbon, and the substrate metal. The thickness, microhardness, and continuity of the coating increase with the discharge energy. The qualitative parameters of sulphoaluminized coatings obtained by the ESA method with an aluminium electrode using STS are analysed. The microstructures reveal three zones: a near-surface, non-continuous loose layer with sulphur enrichment, 10–100-µm thick, and microhardness of 1368–2073 MPa; a ‘white’ hardened layer containing aluminium, 20–40 µm-thick, and microhardness of 4094–5157 MPa; a diffusion zone; and a substrate material. The sulphoaluminized-coatings’ phase composition depends on the ESA energy parameters. Intermetallics FeAl and FeAl2 are formed in the surface layer. The structural–phase state and properties of sulphomolybdenum coatings obtained by the ESA method with a molybdenum electrode using STS are discussed. The near-surface loose layer saturated with sulphur contains up to 8% of molybdenum disulphide formed due to ESA. Beneath this layer is a hardened layer saturated with molybdenum and having a microhardness of 10596–10731 MPa. It is proposed to use sulphurizing methods based on ESA using STS as cheap and effective methods of surface modification of friction surfaces to reduce seizure and friction coefficient. Słowa kluczowe: sulphurizing, electrospark alloying, coating, microstructure, tribotechnical properties Afiliacje autorów:
Tarelnyk V. | - | Sumy National Agrarian University (UA) | Haponova O. | - | IPPT PAN | Tarelnyk N. | - | Sumy National Agrarian University (UA) | Konoplianchenko Y. | - | inna afiliacja |
| 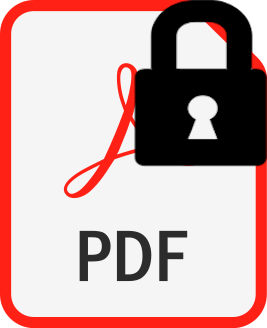 | 70p. |
4. |
Tarelnyk V.♦, Haponova O., Tarelnyk N.♦, Dumanchuk M.♦, Maifat M.♦, Gerasimenko V.♦, Mikulina M.♦, Polyvanyi A.♦, Ohrimenko V.♦, Semernya O.♦, Vasylenko M.♦, Kozin V.♦, Surface Properties of HighStrength Cast Iron Parts with Wear-Resistant Composite Coatings Synthesized by Electrospark Alloying Method. Pt. 1. Specific Aspects of Mass Transfer; Geometric, Topographic, and Mechanical Characteristic Features of Strengthened Surfaces,
Metallofizika i Noveishie Tekhnologii, ISSN: 1024-1809, Vol.47, No.4, pp.427-451, 2025 | 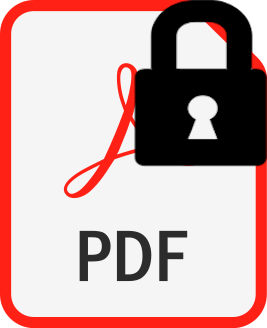 | 40p. |
5. |
Tarelnyk V.♦, Haponova O., Tarelnyk N.♦, Rogovskii I.♦, IMPROVEMENT OF SURFACE LAYER QUALITY PARAMETERS OF STEEL PARTS AFTER NITROСARBURUZING BY ELECTROSPARK ALLOYING METHOD
Part 1 FEATURES OF THE STRUCTURAL STATE AND TOPOGRAPHY OF STEEL SURFACES AFTER NITROCARBURIZING,
Problems of Atomic Science and Technology, ISSN: 1562-6016, Vol.156, No.2, pp.131-137, 2025 Streszczenie: The paper analyses modern methods for improving the surface quality of steel parts of nuclear power plant pumps. The aim of the work was to improve the technology of nitrocarburisation by the method of electrospark alloying (ESA) by studying the effect of the ESA process performance on the quality parameters of the formed surfaces. As a result of the studies, the dependence of the quality parameters of the surfaces of steel parts during nitrocarburizing by the ESA method on the energy parameters of the equipment (discharge energy Wp) and the technological parameters of the process (productivity Q) was established. Experimental studies have shown that as Wp increases, the thickness of the hardened layer, its microhardness and continuity, and surface roughness grow. As Q decreases, the thickness, microhardness and continuity of the hardened layer rise, while the roughness remains practically unchanged. The proposed technology can be recommended for implementation in manufacturing Afiliacje autorów:
Tarelnyk V. | - | Sumy National Agrarian University (UA) | Haponova O. | - | IPPT PAN | Tarelnyk N. | - | Sumy National Agrarian University (UA) | Rogovskii I. | - | inna afiliacja |
| 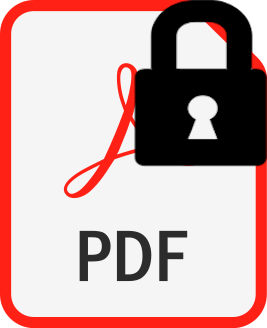 | 20p. |
6. |
Haponova O., Tarelnyk V.♦, Mościcki T. P., Tarelnyk N.♦, Investigating the effect of electrospark alloying parameters on structure formation of modified nitrogen coatings,
BULLETIN OF THE POLISH ACADEMY OF SCIENCES: TECHNICAL SCIENCES, ISSN: 0239-7528, DOI: 10.24425/bpasts.2024.150802, Vol.72, No.5, pp.1-8, 2024 Streszczenie: The quality parameters of surface layers synthesised using electrospark alloying (ESA) technology were analysed in this paper. The main focus was on the influence of equipment energy parameters on structure formation, specifically the effect of discharge energy and productivity. Microstructural analysis of the modified surface of C40 steel after nitriding by ESA using a paste containing nitrogen compounds injected into the interelectrode gap was conducted. The layer structure for all studied ESA parameters includes three areas: the upper “white layer”, the diffusion zone below it, and the substrate. The roughness of the surface is Ra ∼ 0.9 μm at low discharge energy Wp = 0.13 J and Ra ∼ 6 μm at Wp = 3.4 J. The microhardness, continuity, and surface roughness of the layers varied with Wp. The influence of ESA productivity on the structure was studied. The thickness of the hardened layer and the diffusion zone, as well as the microhardness and continuity, are affected by reduced productivity. For the same discharge energy, the thickness of the hardened layer increases by 10-18% with a decrease in productivity compared to the classical mode. Słowa kluczowe: electrospark alloying, discharge energy, productivity, coating, structure Afiliacje autorów:
Haponova O. | - | IPPT PAN | Tarelnyk V. | - | Sumy National Agrarian University (UA) | Mościcki T. P. | - | IPPT PAN | Tarelnyk N. | - | Sumy National Agrarian University (UA) |
| 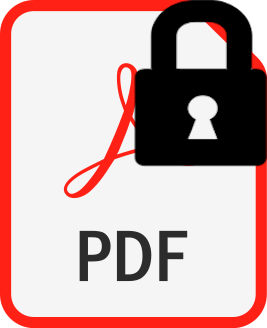 | 100p. |
7. |
Haponova O., Tarelnyk V.♦, Mościcki T. P., Tarelnyk N.♦, Półrolniczak J.♦, Myslyvchenko O.♦, Adamczyk-Cieślak B.♦, Sulej-Chojnacka J.♦, Investigation of the Structure and Properties of MoS2 Coatings Obtained by Electrospark Alloying,
Coatings, ISSN: 2079-6412, DOI: 10.3390/coatings14050563, Vol.14, No.563, pp.1-15, 2024 Streszczenie: Electrospark coatings alloyed with MoS2 have been studied. The coatings were obtained by the following two strategies: the first consisted of pre-applying molybdenum disulfide to the treated surface and alloying with a molybdenum electrode (Mo + MoS2 coating); the second consisted of applying a paste with a sulfur content of 33.3% to the treated surface and alloying with a molybdenum electrode (Mo + S coating). The structure, phase composition, and tribological properties of the coatings were investigated. The coatings have a complex structure consisting of an upper soft layer, a hardened white layer, a diffusion zone, and a substrate. Element analysis and cross-sectional hardness changes indicated that element diffusion occurred at the coating/substrate interface. The phase composition of the coatings is represented by BCC and FCC solid solutions on Fe, and MoS2 is also detected. In Mo + S coatings, the molybdenum disulfide on the surface is about 8%; in Mo + MoS2 coatings, it is 27%–46%. The obtained coatings show very good tribological properties compared to molybdenum ESA coatings. The frictional forces and coefficients are reduced by a factor of 10 and 40, depending on the test conditions. Słowa kluczowe: electrospark alloying, coating, structure, molybdenum disulfide, tribological properties, energy conservation Afiliacje autorów:
Haponova O. | - | IPPT PAN | Tarelnyk V. | - | Sumy National Agrarian University (UA) | Mościcki T. P. | - | IPPT PAN | Tarelnyk N. | - | Sumy National Agrarian University (UA) | Półrolniczak J. | - | inna afiliacja | Myslyvchenko O. | - | I. M. Frantsevich Institute for Problems in Materials (UA) | Adamczyk-Cieślak B. | - | inna afiliacja | Sulej-Chojnacka J. | - | inna afiliacja |
| 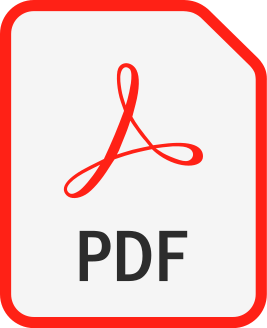 | 100p. |
8. |
Haponova O.♦, Tarelnyk N.♦, Improvement of the Quality Parameters of the Surface Layers of Steel Parts after Alitization by the Electrospark-Alloying Method. Pt 3. Mathematical Model of Forecasting the Quality Parameters of Coatings Taking into Account the Performance of Surface Treatment,
Metallofizika i Noveishie Tekhnologii, ISSN: 1024-1809, DOI: 10.15407/mfint.46.08.0771, Vol.46, No.8, pp.771-795, 2024 | 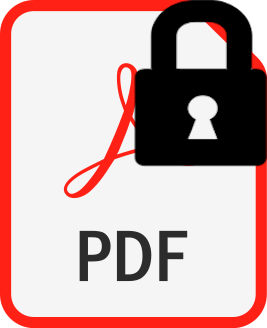 | 40p. |
9. |
Haponova O., Tarelnyk V.♦, Tarelnyk N.♦, Kurp P.♦, The Formation of C-S Coatings by Electrospark Alloying with the Use Special Process Media,
Solid State Phenomena, ISSN: 1662-9779, DOI: 10.4028/p-5KfyZQ, Vol.355, pp.85-93, 2024 Streszczenie: The paper presents an analysis of technologies for improving the quality parameters of the surface layers of parts, which were carried out by the method of electrospark alloying (ESA) and by additional saturation of surfaces with alloying elements from special process media (STM). The technology of sulfocementation was considered. Metallographic and hardness tests after sulfocementation by ESA showed that the treated surface consists of layers: "soft", hardened and base metal. As the discharge energy increases, the thickness, microhardness and integrity of the coating increase. The presence of sulfur in STM promotes the sulfidation process. It is shown that sulfur accumulates on the surface of the metal at a depth of up to 30 μm. This zone is characterized by reduced microhardness. A strengthened layer is formed under this layer, it has an increased carbon content and high microhardness. Słowa kluczowe: electro-spark alloying, special technological environment, coating, sulfocementation, microstructure, microhardness Afiliacje autorów:
Haponova O. | - | IPPT PAN | Tarelnyk V. | - | Sumy National Agrarian University (UA) | Tarelnyk N. | - | Sumy National Agrarian University (UA) | Kurp P. | - | Kielce University of Technology (PL) |
| 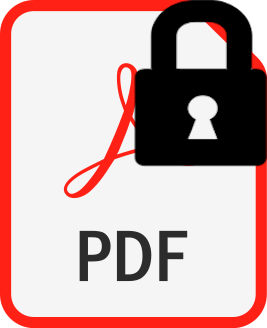 |
10. |
Haponova O.♦, Tarelnyk V.♦, Tarelnyk N.♦, Myslyvchenko M.♦, Nanostructuring of Metallic Surfaces by Electrospark Alloying Method,
The Journal of The Minerals, ISSN: 1047-4838, DOI: 10.1007/s11837-023-05940-1, pp.1-13, 2023 Streszczenie: A new method of nanostructuring of the surface by electrospark alloying method (ESA) using special processing media (SPM) with carbon nanotubes is proposed. The influence on the ESA regimes and the composition of the SPM on the microstructure and hardness of the coatings has been considered. While processing the Armco iron, with an increase in the discharge energy, the thickness and continuity of the coating increase. In the microstructures, the nanoscale phases of 40 nm to 1300 nm are detected, and they are evenly distributed in the coatings. Adding nanotubes helps to increase the continuity, thickness and hardness. Because of the ESA process, coatings with a uniform distribution of molybdenum are formed. Carbon, apparently in the form of the carbon nanotubes, is concentrated on the surfaces of the samples being processed, regardless of the discharge energy during the ESA process. The use of the proposed ESA method has a positive effect on the quality parameters of the coating. Afiliacje autorów:
Haponova O. | - | inna afiliacja | Tarelnyk V. | - | Sumy National Agrarian University (UA) | Tarelnyk N. | - | Sumy National Agrarian University (UA) | Myslyvchenko M. | - | I. M. Frantsevich Institute for Problems in Materials (UA) |
| 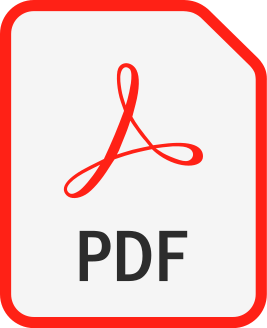 | 100p. |
11. |
Tarelnyk V.♦, Haponova O.♦, Tarelnyk N.♦, Myslyvchenko O.♦, Aluminizing of Metal Surfaces by Electric-Spark Alloying,
Uspekhi Fiziki Metallov, ISSN: 1608-1021, DOI: 10.15407/ufm.24.02.282, Vol.24, No.2, pp.282-318, 2023 Streszczenie: The analysis of the influence of the parameters of electrospark alloying with an aluminium electrode on the quality (roughness, microstructure of the coating, its continuity, phase composition, and microhardness) of the aluminized layer is presented. The effect of finishing methods after aluminizing is evaluated. The heat resistance of the obtained coatings is studied. Metallographic analysis shows that the coating consists of three sections: a ‘white’ layer, a diffusion zone, and the base metal. With an increase in the discharge energy, such quality parameters of the surface layer as thickness, microhardness of both a ‘white’ layer and a transition zone, and roughness are increased. The continuity of a ‘white’ layer at the discharge energy Wp = 0.52 J is low (of 50–60%); with a subsequent increase in the discharge energy, it increases and, at Wp = 6.8 J, it is of 100%. An increase in the discharge energy during electric-spark alloying (ESA) leads to a change in the chemical and phase compositions of the layer: at low discharge energies, a layer is formed, consisting mainly of α-Fe and aluminium oxides. As Wp increases, the layer consists of iron and aluminium intermetallic compounds, as well as free aluminium, that is confirmed by the data of local x-ray microanalysis. For practical application, it is possible to recommend the process of aluminizing by the ESA method, using the modes (discharge energy in the range of 4.6–6.8 J and productivity of 2.0–3.0 cm2/min). Such process provides the formation of a ‘white’ layer with a thickness of 70–130 µm, microhardness of 5000–7500 MPa, roughness (Ra) of 6–9 µm, and continuity of 95–100%. In order to increase the thickness of the aluminized layer, it is recommended to preliminarily apply grease containing aluminium powder to the steel surface and, without waiting for it to dry, carry out ESA with an aluminium electrode. In this case, the coating continuity is of 100%, the layer thickness is of up to 200 µm, and the microhardness is of 4500 MPa. The paper presents the results of study of the quality parameters of multicomponent aluminium-containing coatings of Al–S, Al–C–S, and Al–C–B systems. Replacing the aluminium electrode with graphite one leads to a decrease in the thickness and continuity of a ‘white’ layer, respectively, to 50 µm and 30%. In turn, the microhardness on the surface increases to 9000 MPa. The addition of 0.7 boron to the consistency substance leads to an increase in the thickness and continuity of a ‘white’ layer, respectively, up to 60 µm and 70%. The microhardness on the surface rises to 12000 MPa. In order to reduce the roughness of the surface layer and to obtain continuous coatings, it is recommended to carry out ESA with an aluminium electrode, but at lower modes. Słowa kluczowe: electrospark alloying, coating, aluminizing, microhardness, continuity, roughness, structure, x-ray diffraction analysis, x-ray spectral analysis Afiliacje autorów:
Tarelnyk V. | - | Sumy National Agrarian University (UA) | Haponova O. | - | inna afiliacja | Tarelnyk N. | - | Sumy National Agrarian University (UA) | Myslyvchenko O. | - | I. M. Frantsevich Institute for Problems in Materials (UA) |
| 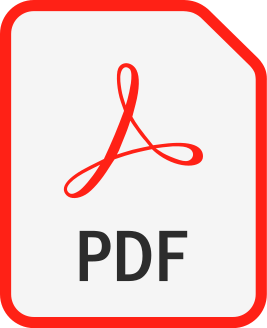 | 70p. |
12. |
Haponova O.♦, Tarelnyk Viacheslav B.♦, Antoszewski B.♦, Radek N.♦, Tarelnyk Nataliia V.♦, Kurp P.♦, Myslyvchenko Oleksandr M.♦, Hoffman J., Technological Features for Controlling Steel Part Quality Parameters by the Method of Electrospark Alloying Using Carburezer Containing Nitrogen—Carbon Components,
Materials, ISSN: 1996-1944, DOI: 10.3390/ma15176085, Vol.15, No.6085, pp.1-14, 2022 Streszczenie: A new method of surface modification based on the method of electrospark alloying (ESA) using carburizer containing nitrogen—carbon components for producing coatings is considered. New processes have been proposed that include the step of applying saturating media in the form of paste-like nitrogenous and nitrogenous-carbon components, respectively, onto the surface without waiting for those media to dry, conducting the ESA process with the use of a steel electrode-tool, as well as with a graphite electrode-tool. Before applying the saturating media, an aluminium layer is applied onto the surface with the use of the ESA method at a discharge energy of Wp = 0.13–6.80 J. A saturating medium in the form of a paste was applied to the surfaces of specimens of steel C22 and steel C40. During nitriding, nitrocarburizing and carburization by ESA (CESA) processes, with an increase in the discharge energy (Wp), the thickness, micro hardness and continuity of the “white layer” coatings, as well as the magnitude of the surface roughness, increase due to saturation of the steel surface with nitrogen and/or carbon, high cooling rates, formation of non-equilibrium structures, formation of special phases, etc. In the course of nitriding, nitrocarburizing and CESA processing of steels C22 and C40, preliminary processing with the use of the ESA method by aluminum increases the thickness, microhardness and continuity of the “white layer”, while the roughness changes insignificantly. Analysis of the phase composition indicates that the presence of the aluminum sublayer leads to the formation of the aluminum-containing phases, resulting in a significant increase in the hardness and, in addition, in an increase in the thickness and quality of the surface layers. The proposed methods can be used to strengthen the surface layers of the critical parts and their elements for compressor and pumping equipment Słowa kluczowe: electrospark alloying,coatings,roughness,structure,microhardness,continuity,X-ray diffraction analysis,nitriding,nitrocarburizing,carburization Afiliacje autorów:
Haponova O. | - | inna afiliacja | Tarelnyk Viacheslav B. | - | Sumy National Agrarian University (UA) | Antoszewski B. | - | Kielce University of Technology (PL) | Radek N. | - | inna afiliacja | Tarelnyk Nataliia V. | - | Sumy National Agrarian University (UA) | Kurp P. | - | Kielce University of Technology (PL) | Myslyvchenko Oleksandr M. | - | I. M. Frantsevich Institute for Problems in Materials (UA) | Hoffman J. | - | IPPT PAN |
| 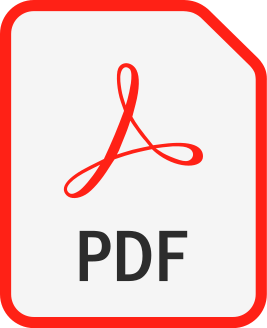 | 140p. |
13. |
Tarelnyk V.♦, Haponova O.♦, Konoplianchenko V.♦, Tarelnyk N.♦, Dumanchuk M.♦, Pirogov V.♦, Voloshko T.♦, Hlushkova D.♦, Development of a System Aimed at Choosing the Most Effective Technology for Improving the Quality of Babbitt Coatings of Sliding Bearings. Pt. 2. Mathematical Model of Wear of Babbitt Coatings. Criteria for Choosing the Technology of Deposition of Babbitt Coatings,
Metallofizika i Noveishie Tekhnologii, ISSN: 1024-1809, DOI: 10.15407/mfint.44.12.1643, Vol.44, No.12, pp.1643-1659, 2022 Streszczenie: In the article, a direct choice system of the most rational technology for applying a babbitt coating on the liners of sliding bearings (SB) is developed, which takes into account both economic and environmental requirements. On the basis of the performed research, a physically substantiated mathematical model of the babbitt-coatings’ wear process (wear equation) is proposed, which allows solving both the direct problem of determining weight and linear wears based on the known work of friction, as well as the inverse problem of finding the necessary work of friction to obtain the required amount of weight or linear wears. With knowing the time to reach a certain amount of wear, it becomes possible to operate the products more rationally, timely assigning the repair time and friction-surface catastrophic-wear preventing. In the course of research, a methodology is developed for determining the constants of the wear equation: activation energy (EA) as well as maximum weight (Δmб.п.н) and linear (Δhб.п.н) wears, which can be used as selection criteria for the most rational technology of applying a babbitt coating. Słowa kluczowe: sliding bearing, babbitt, coating, wear, structure, transition layer, adhesion strength, electrospark alloying, mathematical model Afiliacje autorów:
Tarelnyk V. | - | Sumy National Agrarian University (UA) | Haponova O. | - | inna afiliacja | Konoplianchenko V. | - | inna afiliacja | Tarelnyk N. | - | Sumy National Agrarian University (UA) | Dumanchuk M. | - | inna afiliacja | Pirogov V. | - | inna afiliacja | Voloshko T. | - | inna afiliacja | Hlushkova D. | - | inna afiliacja |
| 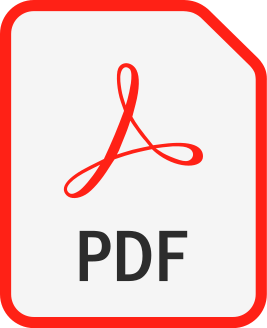 | 40p. |
14. |
Tarelnyk V.♦, Haponova O.♦, Konoplianchenko V.♦, Tarelnyk N.♦, Dumanchuk M.♦, Mikulina M.♦, Pirogov V.♦, Gorovoy S.♦, Medvedchuk N.♦, Development Directed Choice System of the Most Efficient Technology for Improving Sliding Bearings Babbitt Covers Quality. Pt. 1. Peculiarities of Babbitt Coating Technologies,
Metallofizika i Noveishie Tekhnologii, ISSN: 1024-1809, DOI: 10.15407/mfint.44.11.1475, Vol.44, No.11, pp.1475-1493, 2022 Streszczenie: The article substantiates the importance and relevance of increasing problem of the performance and service life of babbitt sliding bearings (SB), which are the rotors supports of a large number of centrifugal pumps, compressors, turbines and other dynamic equipment operating at high operating parameters (speeds, loads and temperatures), as well as in conditions of corrosive, abrasive and other types of working environment’s influence. The analysis of the babbitt SBs production technology and operating conditions showed that the reason for the decrease in their durability are factors that are formed both at the stage of manufacture and during operation. SB failure under normal operating conditions is a consequence of wear various types: cavitation, abrasive wear, damage due to plastic deformations, fatigue damage, etc. The antifriction layer wear resistance depends on the mode of operation and design of the bearing, the physical properties of the connection between the layer and the base, the rigidity of the shaft and the bed under the bearings. As established, the bearing anti-friction layer quality must be evaluated according to the following criteria: adhesion strength of the coating to the base, cohesive strength of the anti-friction layer, porosity, and homogeneity of the structure. As established, during the production of SBs, the formation by the method of electrospark alloying (ESA) of a copper intermediate layer, firmly bonded with steel substrate, and tin layer (formation of solid substitution solutions) and babbitt provides a stronger (by 35%) of adhesion, compared to traditional technology (steel 20 + babbitt), steel substrate with babbitt, as well as more intensive removal of heat from the friction zone. As determined, a new technology in which all operations are carried out by the ESA method can be a reserve for improving the babbitt coatings formation quality, which significantly affects the durability of the SB. As determined, in order to determine a more rational technology for applying babbitt coatings, it is necessary to develop a physically based mathematical model that relates the wear of a certain amount of babbitt to the frictional work spent on it. Słowa kluczowe: sliding bearing, babbitt, coating, wear, structure, transition layer, adhesion strength, electrospark alloying, mathematical model Afiliacje autorów:
Tarelnyk V. | - | Sumy National Agrarian University (UA) | Haponova O. | - | inna afiliacja | Konoplianchenko V. | - | inna afiliacja | Tarelnyk N. | - | Sumy National Agrarian University (UA) | Dumanchuk M. | - | inna afiliacja | Mikulina M. | - | inna afiliacja | Pirogov V. | - | inna afiliacja | Gorovoy S. | - | inna afiliacja | Medvedchuk N. | - | inna afiliacja |
| 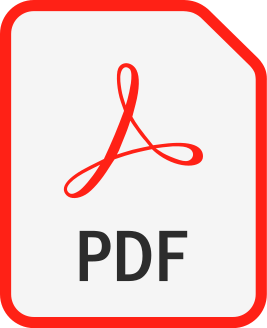 | 40p. |
15. |
Tarelnyk V.♦, Haponova O.♦, Konoplianchenko V.♦, Tarelnyk N.♦, Mikulina M.♦, Gerasimenko V.♦, Vasylenko O.♦, Zubko V.♦, Melnyk V.♦, Properties of Surfaces Parts from X10CrNiTi18-10 Steel Operating in Conditions of Radiation Exposure Retailored by Electrospark Alloying. Pt. 3. X-ray Spectral Analysis of Retailored Coatings,
Metallofizika i Noveishie Tekhnologii, ISSN: 1024-1809, DOI: 10.15407/mfint.44.10.1323, Vol.44, No.10, pp.1323-1333, 2022 Streszczenie: In article we present the results of studies of the local x-ray spectral analysis of coatings formed by the electrospark alloying (ESA) method at the discharge energy Wp = 0.13, 0.52 and 0.9 J by anodes from nickel and stainless steel X10CrNiTi18-10 on the cathode surface from X10CrNiTi18-10 steel. During ESA by stainless steel X10CrNiTi18-10 anode with an increase Wp in characteristic points and from the entire investigated surface of the coating, the quantitative elemental composition is not changed. The analysis of elements distribution over the depth of the formed layer is showed that when using the electrode tool from steel X10CrNiTi18-10 with an increase in Wp, there are a slight decrease in chromium and an increase in nickel and titanium in the surface layer. When steel X10CrNiTi18-10 is replaced by nickel with an increase in Wp, the concentration of nickel on the coating surface decreases from 95.38 to 89.04%. As the recession deepens from the coating surface, the concentration of nickel gradually decreases, respectively, at Wp = 0.13, 0.52 and 0.9 J from 96.29, 90.29 and 89.04% on the surface to 9.0, 10.30 and 9.9% at depth: 120, 165 and 240 μm. At the same time, the concentration of chromium, titanium and iron gradually increases. Słowa kluczowe: electrospark alloying, nickel, steel, x-ray spectral analysis, scan step, topography, spectrum Afiliacje autorów:
Tarelnyk V. | - | Sumy National Agrarian University (UA) | Haponova O. | - | inna afiliacja | Konoplianchenko V. | - | inna afiliacja | Tarelnyk N. | - | Sumy National Agrarian University (UA) | Mikulina M. | - | inna afiliacja | Gerasimenko V. | - | inna afiliacja | Vasylenko O. | - | inna afiliacja | Zubko V. | - | inna afiliacja | Melnyk V. | - | inna afiliacja |
| 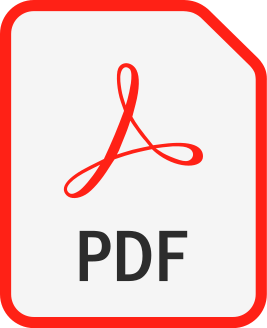 | 40p. |
16. |
Haponova O.♦, Tarelnyk N.♦, Properties of Surfaces Parts from X10CrNiTi18-10 Steel Operating in Conditions of Radiation Exposure Retailored by Electrospark Alloying. Pt. 2. Features of the Structural State of the Retailored Surfaces,
Metallofizika i Noveishie Tekhnologii, ISSN: 1024-1809, DOI: 10.15407/mfint.44.09.1103, Vol.44, No.9, pp.1103-1115, 2022 Streszczenie: In article we present the results of studies of the structural state of coatings formed by the method of electrospark alloying at the discharge energy Wp = 0.13, 0.52 and 0.9 J by anodes from nickel and stainless steel X10CrNiTi18-10 on the cathode surface from X10CrNiTi18-10 steel. Anode materials, such as nickel and X10CrNiTi18-10 steel are recommended as materials, which is advisable to use for restoring the surfaces of parts from X10CrNiTi18-10 steel operating in conditions of radiation exposure. Metallographic analysis of the formed coatings showed that their microstructure consists of 3 zones: 1) ‘white layer’ is the layer that cannot be etched with conventional reagents, 2) transition zone or diffuse zone, 3) base metal. Using nickel and steel X10CrNiTi18-10 with increasing discharge energy, the thickness of the hardened layer, microhardness, continuity and thickness of the white layer, as well as the surface roughness are increased. Replacing the nickel anode with steel X10CrNiTi18-10 surface roughness is increased and the thickness of the hardened layer is decreased. Słowa kluczowe: electrospark alloying, nickel, steel, metallographic analysis, structure, layer thickness, microhardness, roughness, continuity Afiliacje autorów:
Haponova O. | - | inna afiliacja | Tarelnyk N. | - | Sumy National Agrarian University (UA) |
| 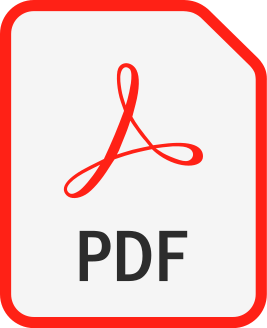 | 40p. |