1. |
Levintant-Zayonts N., Jozwik I.♦, Chrominski W.♦, Akhmadaliev S.♦, Kucharski S., Micromechanical Characterization of 10 MeV High-Energy Fe+ Ion-Irradiated NiTi SMA in Two-Direction Nanoindentation Tests,
METALLURGICAL AND MATERIALS TRANSACTIONS A-PHYSICAL METALLURGY AND MATERIALS SCIENCE, ISSN: 1073-5623, DOI: 10.1007/s11661-025-07931-0, pp.1-14, 2025 Streszczenie: The objective of the present study is to investigate the hardening behavior, superelastic recovery, and structural properties of NiTi Shape Memory Alloy (SMA) after 10 MeV high-energy Fe+ ion irradiation to damage levels of 1.2 and 6.0 d.p.a (displacements per atom). According to Stopping and Range of Ions in Matter (SRIM) calculations, Secondary Ion Mass Spectroscopy (SIMS) analysis, and Transmission Electron Microscopy (TEM) imaging, a 3-micron irradiation layer was obtained with an amorphous structure; the maximum values of damage and Fe+ ion concentration occurred at 2.4 and 2.7 microns, respectively. The mechanical response was characterized in two-direction nanoindentation tests: parallel and perpendicular to the ion beam direction. Cross-sectional nanoindentation indicates that the maximum hardening corresponds to the maximum of the Fe+ ion concentration; the maximum hardness was found at 2.7 microns for both d.p.a. levels. The changes in superelastic properties were achieved in the amorphous layer that suppressed the B2-B19′ phase transformation at a sub-micron scale. We show that cross-sectional nanoindentation is an appropriate method for determining the subtle micromechanical property changes in near-surface regions. It also allows the material and structural properties at a selected point in the non-homogeneous irradiated layer to be correlated with the local level of irradiation damage or ion concentration. This is very important in the development of SMAs and their applications in nuclear technologies Afiliacje autorów:
Levintant-Zayonts N. | - | IPPT PAN | Jozwik I. | - | inna afiliacja | Chrominski W. | - | inna afiliacja | Akhmadaliev S. | - | inna afiliacja | Kucharski S. | - | IPPT PAN |
| 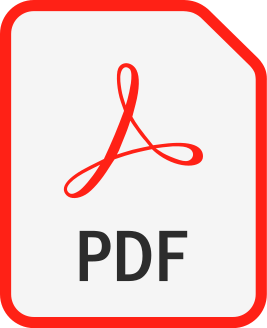 | 200p. |
2. |
Kucharski S., Doan V., Maj M., Deformation Mechanisms of Zinc Single Crystal Investigated with Spherical Nanoindentation Test,
METALLURGICAL AND MATERIALS TRANSACTIONS A-PHYSICAL METALLURGY AND MATERIALS SCIENCE, ISSN: 1073-5623, pp.1-28, 2025 Streszczenie: Pure Zinc single crystal was examined with instrumented spherical indentation on the basal-oriented surface with different tips’ radii. Atomic force microscopy (AFM) and electron backscatter diffraction (EBSD) were used to investigate the topography and orientation changes within the imprint and the surrounding surface. Noticeable pop-ins were reproducible in the majority of tests. Contrary to the literature reports on zinc, plastic deformation was observed prior to the first pop-in, resulting in a hysteresis between loading and unloading curves. Therefore, pop-ins were associated not with the onset of plastic deformation but with slip deformation and contraction twinning because the twins were found inside and outside the imprint after pop-in event. Numerous cells with different orientations resulting from slip and twinning were revealed by EBSD analysis of the residual impressions. The external twins manifested as sink-in patterns. To illustrate the experimental observations, schemes for the evolution of the complex pile-up/sink-in pattern in terms of the parameters of the pop-in event and the increase of the load after the pop-in event have been proposed. Some novel aspects of Zinc nanoindentation were observed including pop-in bursts occurred during unloading process and detwinning properties after indentation. Finally, the difference between indentation results corresponding to two different tips, including the inverse size effect in the indentation phase prior to the pop-in event, was briefly discussed. Afiliacje autorów:
Kucharski S. | - | IPPT PAN | Doan V. | - | IPPT PAN | Maj M. | - | IPPT PAN |
| 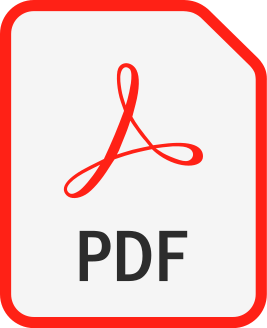 | 200p. |
3. |
Kucharski S. J., Maj M., Ryś M., Petryk H., Size effects in spherical indentation of single crystal copper,
INTERNATIONAL JOURNAL OF MECHANICAL SCIENCES, ISSN: 0020-7403, DOI: 10.1016/j.ijmecsci.2024.109138, Vol.272, pp.1-15, 2024 Słowa kluczowe: Hardness, Lattice rotation, Plasticity, Strain Gradient Afiliacje autorów:
Kucharski S. J. | - | IPPT PAN | Maj M. | - | IPPT PAN | Ryś M. | - | IPPT PAN | Petryk H. | - | IPPT PAN |
| 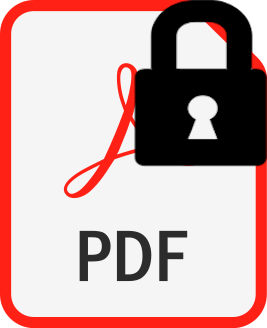 | 140p. |
4. |
Levintant-Zayonts N., Starzyński G., Kucharski S. J., Constituting and Investigation of Ion-Implanted Protective Layer on NiTi Alloy for Mechanical and Tribological Applications,
Journal of Tribology, ISSN: 0742-4787, DOI: 10.1115/1.4066204, Vol.147, No.011401, pp.1-13, 2024 Streszczenie: NiTi exhibits an excellent wear resistance, which can be further enhanced by ion implantation. However, there are some limitations to the implantation effects: only a thin layer of about 100 nm can be created. In this paper, the effect of nitrogen ion implantation on the NiTi wear response is investigated. The different loads and durations of tests are taken into account to show that the implanted layer has the most beneficial effect only in a certain range of contact pressure. It was found that the wear volume changes in a nonlinear manner with respect to the load and sliding length, for both non- and implanted samples. For the latter, two distinct stages can be distinguished in the wear process: an initial stage characterized by a low wear-rate and a low coefficient of friction, and a second stage in which the wear-rate drastically increases. The duration of the first stage is longer for lower loads. This specific behavior is explained by differences in the hardness distribution, energy dissipation due to the normal load, and differences in the microstructure of the wear tracks. Our results show that the lifetime of NiTi can be improved by ion implantation, thus boding well for applications in harsh environments. Słowa kluczowe: ion implantation, NiTi shape memory alloy, sliding wear, pseudoelasticity, abrasion, dry friction, surface treatments Afiliacje autorów:
Levintant-Zayonts N. | - | IPPT PAN | Starzyński G. | - | IPPT PAN | Kucharski S. J. | - | IPPT PAN |
| 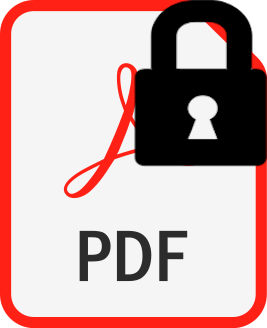 | 100p. |
5. |
Mróz Z., Paczelt I.♦, Kucharski S.J., Contact interaction and wear of beam supports resting on a frictional substrate,
INTERNATIONAL JOURNAL OF MECHANICAL SCIENCES, ISSN: 0020-7403, DOI: 10.1016/j.ijmecsci.2023.108628, Vol.260, No.108628, pp.1-16, 2023 Streszczenie: The frictional contact response of a beam with attached spherical indenters and supported on a plane substrate is considered for periodically varying normal load. An oblique loading case then occurs as the structural load induces both normal and tangential forces on the contact zone. The cyclic tangential sliding and spin of indenter on the substrate are then accompanied by evolving contact zone related to load variation. Rigid-sliding and slip-sliding friction models have been used to describe analytically cyclic contact response, load-deflection hysteretic relation, wear scar evolution and dissipated energy per cycle assuming linear-elastic material model. The analytical solution has been verified by experimental tests providing data on mechanical response, load-deflection diagrams illustrating transient and steady states and wear scar evolution. The effect of wear debris adhesively bonded to the indenter was found to be essential for increasing friction and wear. The relation of wear volume to the dissipated energy is presented. The analysis is aimed to develop a new type of wear tester applicable to oblique loading cases. Słowa kluczowe: Frictional contact, Oblique loading, Friction models, Hysteretic diagrams, Wear growth Afiliacje autorów:
Mróz Z. | - | IPPT PAN | Paczelt I. | - | inna afiliacja | Kucharski S.J. | - | IPPT PAN |
| 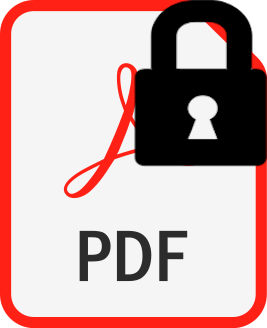 | 140p. |
6. |
Kucharski S., Mackiewicz S., Katz T., Starzyński G., Ranachowski Z., Woźniacka S., Evaluation of fatigue damage of a railhead using an indentation test, acoustic methods and microstructural observations,
INTERNATIONAL JOURNAL OF FATIGUE, ISSN: 0142-1123, DOI: 10.1016/j.ijfatigue.2022.107346, pp.107346-1-107346-13, 2022 Streszczenie: The paper presents an investigation of the railhead steel R260. Brinell hardness was measured, spherical microindentation tests were performed and the microstructure was analysed using optical microscopy and SEM images. Fatigue damage in various near-surface regions of the railhead was estimated on the basis of local deterioration of elastic modulus and the development of plastic work in cyclic microindentation tests. There is a clear difference in hardness and fatigue damage between the used and the virgin regions of the railhead. The Brinell hardness and ultrasonic measurements show a change in material properties due to rail manufacturing process. Słowa kluczowe: Fatigue damage, Microindentation, Brinell hardness, Ultrasonic measurements, Railhead Afiliacje autorów:
Kucharski S. | - | IPPT PAN | Mackiewicz S. | - | IPPT PAN | Katz T. | - | IPPT PAN | Starzyński G. | - | IPPT PAN | Ranachowski Z. | - | IPPT PAN | Woźniacka S. | - | IPPT PAN |
| 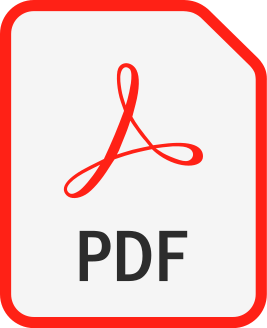 | 140p. |
7. |
Levintant-Zayonts N., Starzyński G., Kucharski S., Effect of N ion implantation on tribological properties of spring steels,
APPLIED SURFACE SCIENCE, ISSN: 0169-4332, DOI: 10.1016/j.apsusc.2022.153117, Vol.591, pp.153117-1-13, 2022 Streszczenie: D6A and C75S spring steels were implanted by nitrogen ions at an energy of 65 keV and a fluence of 6 × 10^17 ions/cm2. The hardness and tribological properties of implanted samples were studied. In a reciprocating ball-on-plate wear test, a relatively low contact pressure was applied (9 mm diameter ball under load up to 0.5 N). In the implanted samples two stages of wear process can be distinguished. In the first stage a low friction coefficient and low wear rate are observed while in the second stage their values considerably increase. The duration of the first stage depends on the applied load (contact pressure). At low contact pressure, the wear life can be extended considerably, and at high contact pressure the first stage practically disappears and the effect of ion implantation is negligible. The evolution of wear process in the second stage is similar to that of non-implanted sample. Analysis of morphology and chemical composition of wear tracks with SEM reveals different mechanisms at different stages of wear in implanted samples wear. At the first stage, adhesive and abrasive wear predominate, while in the second stage, oxidative and fatigue mechanisms occur that are similar to those observed for a non-implanted material. Słowa kluczowe: ion implantation, indentation, sliding wear, scanning profilometry, surface topography, electron microscopy Afiliacje autorów:
Levintant-Zayonts N. | - | IPPT PAN | Starzyński G. | - | IPPT PAN | Kucharski S. | - | IPPT PAN |
| 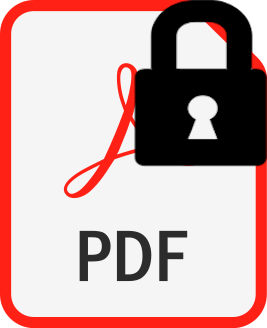 | 140p. |
8. |
Białas M.♦, Maciejewski J.♦, Kucharski S., Friction coefficient of solid lubricating coating as a function of contact pressure: experimental results and microscale modeling,
CONTINUUM MECHANICS AND THERMODYNAMICS, ISSN: 0935-1175, DOI: 10.1007/s00161-021-00999-0, Vol.33, pp.1733-1745, 2021 Streszczenie: The paper presents experimental analysis of relation between friction coefficient and contact pressure of MoS2 film deposited on Ti6Al4V substrate in contact with sapphire ball during reciprocating sliding motion. It is shown that the value of friction coefficient decreases with increasing contact pressure. A microscale modeling approach is next developed to mimic the experimental observations. Representative volume element is defined based on the actual topography of outer surface of MoS2 film. Assuming thermo-elastic material properties, the calculations on the asperity level are performed in two steps. Firstly, the mechanical contact between two surfaces is calculated. As a result, the relation between the global load and micro-stress distribution is obtained. Secondly, for a given stress load, thermal analysis is performed providing temperature fluctuation within simplified conical asperity. By assuming relation between friction coefficient and temperature on the microscale, it is possible to obtain macroscopic friction coefficient as a function of contact pressure. In the end, model results are compared with experimental data. The novel aspects of presented approach lie in the selection of three main factors on a micro-level defining macroscopic friction. They are actual surface topography, microscopic temperature and microscopic friction-temperature relation. Słowa kluczowe: microscale modeling, friction coefficient, flash temperature, reciprocating motion test Afiliacje autorów:
Białas M. | - | inna afiliacja | Maciejewski J. | - | inna afiliacja | Kucharski S. | - | IPPT PAN |
| 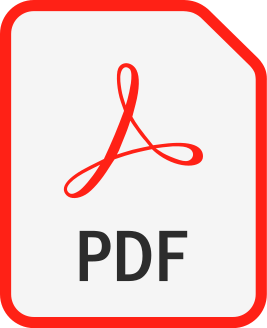 | 100p. |
9. |
Ustrzycka A., Mróz Z., Kowalewski Z.L., Kucharski S., Analysis of fatigue crack initiation in cyclic microplasticity regime,
INTERNATIONAL JOURNAL OF FATIGUE, ISSN: 0142-1123, DOI: 10.1016/j.ijfatigue.2019.105342, Vol.131, pp.105342-1-15, 2020 Streszczenie: The present work provides description of fatigue crack initiation in metals subjected to cyclic loading within the nominal elastic or initial elastic-plastic regimes next passing to elastic response during cyclic deformation and shake down process. It is assumed that damage growth proceeds due to action of local stress, specified as the sum of mean stress and its fluctuations induced by material inhomogeneities such as grain boundaries, inclusions, cavities, boundary asperities, also due to design notches or holes introduced into the element. The damage growth model is proposed, based on the critical plane concept. The macrocrack initiation then corresponds to a critical value of accumulated damage. The modelling of damage growth is supported by Electronic Speckle Pattern Interferometry (ESPI) apparatus using the coherent laser light. The damage growth effect is analysed by microindentation tests. The fatigue tests are performed for high strength steel specimens with central hole. Słowa kluczowe: fatigue crack initiation, micro-plasticity, damage evolution, optical ESPI method, micro indentation Afiliacje autorów:
Ustrzycka A. | - | IPPT PAN | Mróz Z. | - | IPPT PAN | Kowalewski Z.L. | - | IPPT PAN | Kucharski S. | - | IPPT PAN |
| 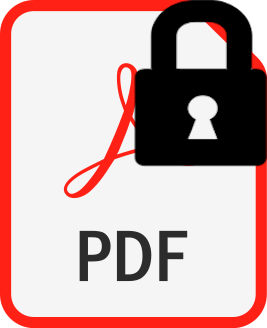 | 140p. |
10. |
Levintant-Zayonts N., Starzyński G., Kucharski S., On the origin of superiority in wear response of superelastic NiTi compared to conventional Ti6Al4V,
TRIBOLOGY TRANSACTIONS, ISSN: 1040-2004, DOI: 10.1080/10402004.2020.1836295, pp.1-15, 2020 Streszczenie: The difference in wear behaviour of superelastic NiTi and conventional Ti6Al4V alloys with similar elastic limits was investigated. Reciprocating dry-sliding wear tests were performed with a ball-on-plate tribometer machine at different normal loads and sliding times. Mechanical properties were also examined using different microindentation tests, and wear track morphologies and chemical compositions in the scar area were characterised by scanning electron microscopy and energy dispersive spectrometry. Superelasticity of the NiTi alloy was significantly beneficial to its tribological properties, and wear resistance of the NiTi alloy was up to forty times higher than that of the Ti6Al4V alloy. Such a significant difference cannot be attributed only to the relatively small difference in hardness (H) or H/E ratios (E - elastic modulus) of the materials but, rather, a difference in strain energy, which dissipates in the material and results from normal load of the sliding ball. To estimate this energy, spherical microindentation tests in wear scar were carried out. Understanding the difference between tribological behaviour of the NiTi shape memory alloy and the conventional Ti6Al4V material provides insight into wear progression, and an investigation of its mechanisms can effectively prevent the destruction of components, prolonging their safe service life. Słowa kluczowe: wear mechanisms, unlubricated friction, non-ferrous alloys, titanium Afiliacje autorów:
Levintant-Zayonts N. | - | IPPT PAN | Starzyński G. | - | IPPT PAN | Kucharski S. | - | IPPT PAN |
| 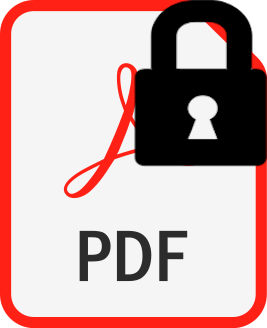 | 100p. |
11. |
Muszalski J.♦, Sankowska I.♦, Kucharski S., Nanoindentation of GaAs/AlAs distributed bragg reflector grown on GaAs substrate,
Materials Science in Semiconductor Processing, ISSN: 1369-8001, DOI: 10.1016/j.mssp.2020.104912, Vol.109, pp.104912-1-8, 2020 Streszczenie: Nanoindentation was used to investigate the mechanical parameters of GaAs/AlAs Distributed Bragg Reflectors. Such heterostructures are commonly employed in surface-emitting optoelectronic devices as LED or lasers. The investigation was carried for fully pseudomorphic AlAs/GaAs heterostructures and compared with bulk GaAs. The nanoindentation tests with sharp (Vickers) and spherical tip were conducted, and pop-in events were observed. We show that below pop-in load, the response of both materials is similar i.e., elastic parameters of the heterostructure and GaAs are practically the same. However, the pop-in events take place at higher loads for heterostructures than for GaAs. This in turn indicates that the heterostructure has a higher resistance to damage. For both materials, the pop-in load depends on loading rate. The possible mechanisms of pop-in are discussed. In the elastic-plastic stage (after pop-in), the heterostructure exhibits lower stiffness and lower hardness than GaAs does. The surface cracks that are generated in the heterostructure during the indentation test continue to grow even when the load is removed. Afiliacje autorów:
Muszalski J. | - | Łukasiewicz Research Network‒Institute of Electronic Materials Technology (PL) | Sankowska I. | - | Łukasiewicz Research Network‒Institute of Electronic Materials Technology (PL) | Kucharski S. | - | IPPT PAN |
| 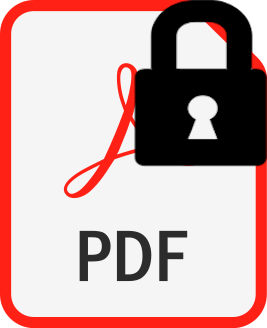 | 70p. |
12. |
Kucharski S., Starzyński G., Contact of rough surfaces under normal and tangential loading,
WEAR, ISSN: 0043-1648, DOI: 10.1016/j.wear.2019.203075, Vol.440-441, pp.203075-1-14, 2019 Streszczenie: Contact between a deformable, random rough surface and a rigid flat counterpart was investigated experimentally and theoretically. In the experimental setup, two modes of rough surface flattening were performed, namely normal compression and sliding (tangential load) in presence of normal compression. The load-approach relationship and friction coefficient were measured. After unloading the surface, the topography was measured using scanning profilometry. The deformation of roughness zone, i.e. evolution of the real contact area (RCA), and roughness parameters were analysed. A model based on statistical analysis and a finite element solution was applied to predict the load–approach relationship. The numerical and experimental results were compared. The effect of friction coefficient was discussed. Słowa kluczowe: contact mechanics, roughness, normal load, tangential load Afiliacje autorów:
Kucharski S. | - | IPPT PAN | Starzyński G. | - | IPPT PAN |
| 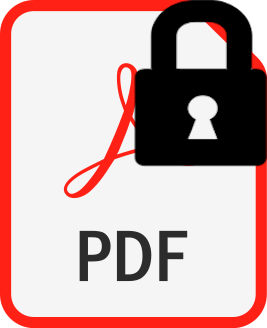 | 200p. |
13. |
Levintant-Zayonts N., Starzyński G., Kopeć M., Kucharski S., Characterization of NiTi SMA in its unusual behaviour in wear tests,
TRIBOLOGY INTERNATIONAL, ISSN: 0301-679X, DOI: 10.1016/j.triboint.2019.05.005, Vol.137, pp.313-323, 2019 Streszczenie: The manuscript presents experimental investigations of an unusual behaviour of shape memory alloys (NiTi) having different characteristic temperatures in wear test. The studies are focused on the different wear mechanism at varying loads and sliding times and include a description of the phenomena accompanying the wear process. The ball-on-plate reciprocating sliding wear tests were conducted on NiTi shape memory alloys against a sapphire ball. We show that the wear resistance of NiTi is affected by its specific stress-strain characteristic. The understanding of the tribological behaviour of NiTi, a knowledge of the course of wear and an examination of its mechanisms can enable an effective prevention of the destruction of devices components and prolong their safe working life. Słowa kluczowe: wear behaviour of NiTi SMA, friction coefficient, superelasticity, shape memory effect Afiliacje autorów:
Levintant-Zayonts N. | - | IPPT PAN | Starzyński G. | - | IPPT PAN | Kopeć M. | - | IPPT PAN | Kucharski S. | - | IPPT PAN |
| 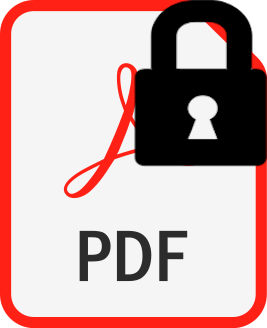 | 200p. |
14. |
Kucharski S., Woźniacka S., Size effect in single crystal copper examined with spherical indenters,
METALLURGICAL AND MATERIALS TRANSACTIONS A-PHYSICAL METALLURGY AND MATERIALS SCIENCE, ISSN: 1073-5623, DOI: 10.1007/s11661-019-05160-w, Vol.50A, pp.2139-2154, 2019 Streszczenie: The increasing hardness with decreasing penetration depth, referred to as indentation size effect (ISE) was previously investigated experimentally and theoretically by many researchers, however the mechanisms responsible for ISE are still being discussed. Generally, ISE is related to the density of geometrically necessary dislocation stored within a small volume beneath the indenter tip. In this study ISE is investigated experimentally in a single crystal copper using spherical indenter tips of different radii. Some new aspects of ISE are shown: a qualitative change of shape of residual impression (pile-up/sink-in pattern) when tip radius or load is modified, an increase of maximum pop-in load with decrease of tip radius as well as the well-known increase of hardness when tip radius decreases are analyzed. As we observe a difference of the residual imprint morphology which depends on tip radius and load, we apply two methods of hardness estimation: true hardness and nominal hardness. The former is determined on the basis of direct measurement of the contact area while accounting for a specific pile-up pattern, while the latter is determined by measuring the contact area using residual penetration depth. We show that hardness–tip radius relationship has a linear form for the nominal hardness and bilinear form for the true hardness. Afiliacje autorów:
Kucharski S. | - | IPPT PAN | Woźniacka S. | - | IPPT PAN |
| 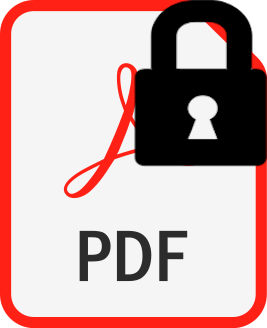 | 200p. |
15. |
Mróz Z., Kucharski S., Páczelt I.♦, Anisotropic friction and wear rules with account for contact state evolution,
WEAR, ISSN: 0043-1648, DOI: 10.1016/j.wear.2017.11.004, Vol.396-397, pp.1-11, 2018 Streszczenie: The present study is related to analysis of coupled friction and wear process in sliding along the rough surface with an anisotropic asperity pattern characterized by single or mutually orthogonal striations. Due to wear process the initial anisotropic response evolves with the variation of asperity distribution, tending to a steadystate pattern. The orthotropic friction sliding model and the related wear rule are analytically formulated assuming evolution of contact anisotropy to its steady state. The orthotropic frictional sliding model and the related wear rule are analytically formulated assuming evolution of contact anisotropy to its steady state. The experimental study is next presented for orthotropic asperity patterns induced on steel plate surface. The transient and steady states are characterized and the respective evolution parameters calibrated. The numerical finite element wear analysis aimed at validation of model-predictions and wear parameter calibration is presented at the end of paper Słowa kluczowe: Anisotropic contact, Friction sliding and wear rules, Evolution of contact anisotropy, Experimental study, Numerical wear analysis Afiliacje autorów:
Mróz Z. | - | IPPT PAN | Kucharski S. | - | IPPT PAN | Páczelt I. | - | University of Miskolc (HU) |
| 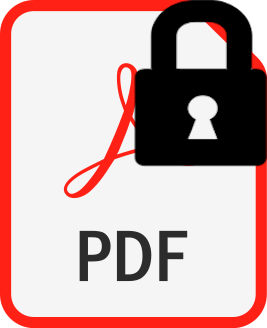 | 35p. |
16. |
Zajączkowska U.♦, Kucharski S., Nowak Z., Grabowska K.♦, Morphometric and mechanical characteristics of Equisetum hyemale stem enhance its vibration,
PLANTA, ISSN: 0032-0935, DOI: 10.1007/s00425-017-2648-1, Vol.245, No.4, pp.835-848, 2017 Streszczenie: The order of the internodes, and their geometry and mechanical characteristics influence the capability of theEquisetumstem to vibrate, potentially stimulating spore liberation at the optimum stress setting along the stem. Equisetum hyemale L. plants represent a special example of cellular solid construction with mechanical stability achieved by a high second moment of area and relatively high resistance against local buckling. We proposed the hypothesis that the order of E. hyemale L. stem internodes, their geometry and mechanical characteristics influence the capability of the stem to vibrate, stimulating spore liberation at the minimum stress setting value along the stem. An analysis of apex vibration was done based on videos presenting the behavior of an Equisetum clump filmed in a wind tunnel and also as a result of excitation by bending the stem by 20°. We compared these data with the vibrations of stems of the same size but deprived of the three topmost internodes. Also, we created a finite element model (FEM), upon which we have based the 'natural' stem vibration as a copy of the real object, 'random' with reshuffled internodes and 'uniform', created as one tube with the characters averaged from all internodes. The natural internode arrangement influences the frequency and amplitude of the apex vibration, maintaining an equal stress distribution in the stem, which may influence the capability for efficient spore spreading. Słowa kluczowe: mechanical properties, plant biomechanics, segmented structure, stem vibration, stress distribution, wind Afiliacje autorów:
Zajączkowska U. | - | inna afiliacja | Kucharski S. | - | IPPT PAN | Nowak Z. | - | IPPT PAN | Grabowska K. | - | inna afiliacja |
| 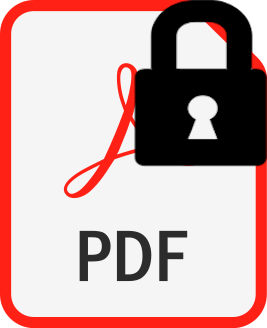 | 40p. |
17. |
Petryk H., Stupkiewicz S., Kucharski S., On direct estimation of hardening exponent in crystal plasticity from the spherical indentation test,
INTERNATIONAL JOURNAL OF SOLIDS AND STRUCTURES, ISSN: 0020-7683, DOI: 10.1016/j.ijsolstr.2016.09.025, Vol.112, pp.209-221, 2017 Streszczenie: A novel methodology is proposed for estimating the strain hardening exponent of a metal single crystal directly from the spherical indentation test, without the need of solving the relevant inverse problem. The attention is focused on anisotropic piling-up and sinking-in that occur simultaneously in different directions, in contrast to the standard case of axial symmetry for isotropic materials. To correlate surface topography parameters with the value of material hardening exponent, a finite-element study of spherical indentation has been performed within a selected penetration depth range using a finite-strain crystal plasticity model. It is shown how the power-law hardening exponent can be estimated from the measured pile-up/sink-in pattern around the residual impression after indentation in a (001)-oriented fcc single crystal of a small initial yield stress. For this purpose, a new parameter of surface topography is defined as the normalized material volume displaced around the nominal contact zone, calculated by integration of the local residual height (positive or negative) over a centered circular ring. That indicator can be easily determined from an experimental topography map available in a digital form. Comparison is made with the estimates based on measurements of the contact area and the slope of the load–penetration depth curve in logarithmic coordinates. The proposed methodology is extended to estimation of the hardening exponent simultaneously with the initial yield stress when the latter is not negligible. Experimental verification for a Cu single crystal leads to promising conclusions. Słowa kluczowe: metal crystal, elastoplasticity, finite deformation, strain hardening, experimental identification Afiliacje autorów:
Petryk H. | - | IPPT PAN | Stupkiewicz S. | - | IPPT PAN | Kucharski S. | - | IPPT PAN |
| 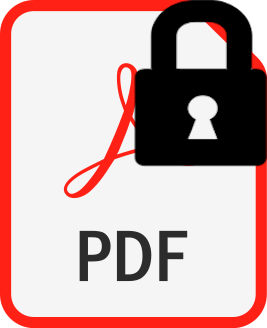 | 40p. |
18. |
Mackiewicz M.♦, Mikulski J.L.♦, Wańkowicz J.♦, Kucharski S., Ranachowski P., Ranachowski Z., Study of composite insulator sheds subjected to wheel test,
ARCHIVES OF METALLURGY AND MATERIALS, ISSN: 1733-3490, DOI: 10.1515/amm-2017-0101, Vol.62, No.2, pp.679-686, 2017 Streszczenie: The paper presents investigation of the properties of the surface and the material stiffness – flexibility of series of samples taken from the sheds of the composite insulators. The insulators were previously subjected to wheel test. The wheel test and 1000 h salt fog test are regarded as alternative examination of the material resistance to the effects of electrical surface discharges. There were investigated two series of the samples of the composite insulators sheds. Examined specimens, made of HTV silicone rubber, were taken from the sheds of medium-voltage composite insulators of two different manufacturers. Insulators of both types passed the 1000 h salt fog test without reservation. Meanwhile, the wheel test can provide a basis for better distinguishing between physical properties of the tested materials. In the case of the insulators of one of the manufacturers the wheel test result was negative. Cross puncture effect of the sheds took place in several places. In addition, sheds were covered with dark coating of varying thicknesses. The results of the study indicated a significantly stronger influence of electrical and temperature factors on the sheds under investigations during the wheel test than in the case of the 1000 h salt fog test. It can be stated that these tests cannot be considered as alternative and it seems that wheel test enables better distinguishing between properties of the materials. Słowa kluczowe: composite insulators, silicone rubber, wheel test, electrical surface discharges, tracking and erosion Afiliacje autorów:
Mackiewicz M. | - | inna afiliacja | Mikulski J.L. | - | inna afiliacja | Wańkowicz J. | - | inna afiliacja | Kucharski S. | - | IPPT PAN | Ranachowski P. | - | IPPT PAN | Ranachowski Z. | - | IPPT PAN |
| 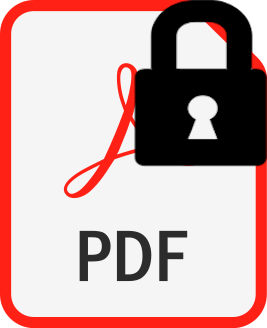 | 30p. |
19. |
Kucharski S., Jarząbek D.M., Piątkowska A.♦, Woźniacka S., Decrease of Nano-hardness at Ultra-low Indentation Depths in Copper Single Crystal,
EXPERIMENTAL MECHANICS, ISSN: 0014-4851, DOI: 10.1007/s11340-015-0105-2, Vol.56, No.3, pp.381-393, 2016 Streszczenie: In the present study, we report a detailed investigation of the unusual size effect in single crystals. For the experiments we specified the hardness in single crystalline copper specimens with different orientations ((001), (011) and (111)) using Oliver-Pharr method. Our results indicates that with decreasing load, after the value of the hardness reached its maximum, it starts to decrease for very small indentation depths (<150 nm). For the sake of accuracy of hardness determination we have developed two AFM-based methods to evaluate contact area between tip and indented material. The proposed exact measurement of the contact area, which includes the effect of pile-up and sink-in patterns, can partially explain the strange behaviour, however, the decrease of hardness at low loads is still observed. At higher loads range the specified hardness is practically constant. Słowa kluczowe: Copper, Single crystal, Nanoindentation, AFM, Size effect Afiliacje autorów:
Kucharski S. | - | IPPT PAN | Jarząbek D.M. | - | IPPT PAN | Piątkowska A. | - | Institute of Electronic Materials Technology (PL) | Woźniacka S. | - | IPPT PAN |
| 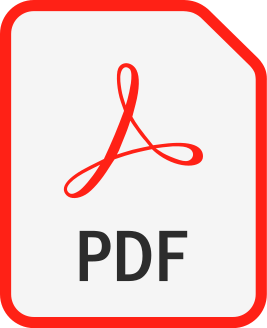 | 35p. |
20. |
Stupkiewicz S., Lengiewicz J., Sadowski P., Kucharski S., Finite deformation effects in soft elastohydrodynamic lubrication problems,
TRIBOLOGY INTERNATIONAL, ISSN: 0301-679X, DOI: 10.1016/j.triboint.2015.03.016, Vol.93, pp.511-522, 2016 Streszczenie: Soft elastohydrodynamic lubrication regime is typical for many elastomeric and biological contacts. As one or both contacting bodies are then highly compliant, relatively low contact pressures may lead to large deformations which are neglected in the classical EHL theory. In the paper, the related finite-deformation effects are studied for two representative soft-EHL problems. To this end, a fully-coupled nonlinear formulation has been developed which combines finite-strain elasticity for the solid and the Reynolds equation for the fluid, both treated using the finite element method with full account of all elastohydrodynamic couplings. Results of friction measurements are also reported and compared to theoretical predictions for lubricated contact of a rubber ball sliding against a steel disc under high loads. Słowa kluczowe: Soft-EHL problem, Finite deformation, Finite element method, Monolithic scheme Afiliacje autorów:
Stupkiewicz S. | - | IPPT PAN | Lengiewicz J. | - | IPPT PAN | Sadowski P. | - | IPPT PAN | Kucharski S. | - | IPPT PAN |
| 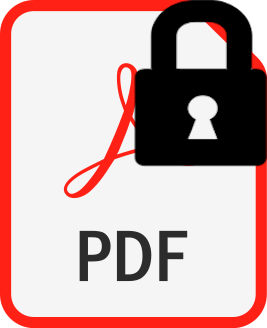 | 35p. |
21. |
Mróz K.P., Kucharski S., Doliński K., Bigos A.♦, Mikułowski G., Bełtowska-Lehman E.♦, Nolbrzak P.♦, Failure modes of coatings on steel substrate,
BULLETIN OF THE POLISH ACADEMY OF SCIENCES: TECHNICAL SCIENCES, ISSN: 0239-7528, DOI: 10.1515/bpasts-2016-0027, Vol.64, No.1, pp.249-256, 2016 Streszczenie: The critical monotonic strain of Ni-W and MoS2(Ti,W) coatings on steel substrates was studied. The idea of axisymmetric bending test (called here as coin bending test) limited to monitoring of the coating failure was used. Experiments revealed mechanism of the coating failure, as cracking initiated from coating surface defects and/or substrate was demonstrated using indentation technique. By pushing the center of the uncoated side of a circular plate, the axisymmetric stress state was generated in the coating. The stress components varied gradually from the greatest value in the center to the smallest value at the edge of the specimen. The changes of the sample surface as a result of loading were monitored step by step via optical microscopy. Słowa kluczowe: Ni-W coating, MoS2(Ti.W) coating, steel substrate, fracture, coatings strength, axisymmetric bending test Afiliacje autorów:
Mróz K.P. | - | IPPT PAN | Kucharski S. | - | IPPT PAN | Doliński K. | - | IPPT PAN | Bigos A. | - | Institute of Metallurgy and Materials Science, Polish Academy of Sciences (PL) | Mikułowski G. | - | IPPT PAN | Bełtowska-Lehman E. | - | Institute of Metallurgy and Materials Science, Polish Academy of Sciences (PL) | Nolbrzak P. | - | Lodz University of Technology (PL) |
| 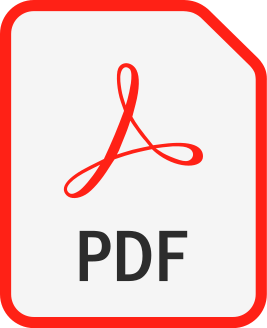 | 20p. |
22. |
Sitko A.♦, Szkodo M.♦, Kucharski S., Influence of nitriding and laser remelting on properties of austenitic stainless steel type x10crni18-8 and cavitation erosion resistance,
Advances in Materials Science, ISSN: 1730-2439, DOI: 10.1515/adms-2016-0006, Vol.16, No.2, pp.21-31, 2016 Streszczenie: The paper presents properties of surface layers. Surface layers were obtained by using low temperature glow–discharge nitriding process and laser remelting carried out on austenitic stainless steel type X10CrNi18-8. Investigations were done by using an Ultra Nanoindentation Tester (UNHT) in the Warsaw Institute of Fundamental Technological Research. The influence of the above mentioned treatments on obtained surface layers is shown. The values of the Vickers hardness (HV), the irreversible indentation work (Wir), the reversible work (We) and the maximum depth (hmax) during indentation were determined using the method proposed by Oliver and Pharr [1]. On the basis of mechanical properties, the elasticity (Ie) and ductility (Iir) indexes were calculated. Moreover, microstructure cross-section of the austenitic stainless steel after nitriding process and laser remelting was observed using a scanning electron microscope. Cavitation test was performed at a vibratory rig with stationary specimen. On the basis of erosion curves the cavitation resistance was evaluated. Słowa kluczowe: glow-discharge nitriding process, laser remelting, austenitic stainless steel, diffusion layer, nitrided case, expanded austenite Afiliacje autorów:
Sitko A. | - | Gdańsk University of Technology (PL) | Szkodo M. | - | Gdańsk University of Technology (PL) | Kucharski S. | - | IPPT PAN |
| 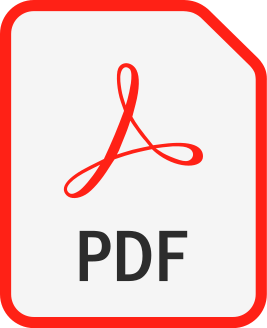 | 11p. |
23. |
Zajączkowska U.♦, Kucharski S., Guzek D.♦, Are trichomes involved in the biomechanical systems of Cucurbita leaf petioles?,
PLANTA, ISSN: 0032-0935, DOI: 10.1007/s00425-015-2388-z, Vol.242, No.6, pp.1453-1465, 2015 Streszczenie: Main conclusion
Trichomes are involved in petiole movement and likely function as a part of the plant biomechanical system serving as an additional reservoir of hydrostatic pressure.
The large, non-glandular trichomes on Cucurbita petioles occur across collenchyma strands. Time-lapse imaging was used to study the leaf reorientation of Cucurbita maxima ‘Bambino’ plants placed in horizontal position. The experiment comprised four variants of the large non-glandular petiole trichomes: (1) intact, (2) mechanically removed, (3) dehydrated, and (4) intact but with longitudinally injured petioles. Isolated strands of collenchyma with intact epidermis or epidermis mechanically removed from the abaxial and adaxial sides of the petiole were subjected to breaking test. The stiffness of the non-isolated tissue with intact epidermis was measured using the micro-indentation method. Petioles without trichomes did not exhibit tropic response, and the dehydration of trichomes slowed and prevented complete leaf reorientation. Isolated strands of collenchyma showed no correlation between strength values and position on the petiole. However, strands of collenchyma with epidermis exhibited a significantly greater strength regardless of their position on the petiole. The indentation test showed that non-isolated collenchyma is stiffer on the abaxial side of the petiole. Trichomes from the abaxial side of the petiole were larger at their base. The application of the ‘tensile triangles method’ revealed that these trichomes had a biomechanically optimized shape in comparison to the adaxial side. We conclude that trichomes can be involved in plant biomechanical system and serve as an additional reservoir of hydrostatic pressure that is necessary for maintaining petioles in the prestressed state. Słowa kluczowe: Collenchyma, Epidermis, Plant biomechanics, Shape optimization, Tropic response Afiliacje autorów:
Zajączkowska U. | - | inna afiliacja | Kucharski S. | - | IPPT PAN | Guzek D. | - | inna afiliacja |
| 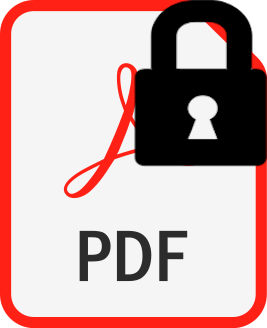 | 40p. |
24. |
Takeda K.♦, Matsui R.♦, Tobushi H.♦, Homma S.♦, Levintant-Zayonts N., Kucharski S., Enhancement of bending fatigue life in TiNi shape-memory alloy tape by nitrogen ion implantation,
ARCHIVES OF MECHANICS, ISSN: 0373-2029, Vol.67, No.4, pp.293-310, 2015 Streszczenie: A shape-memory alloy (SMA) is expected to be applied as intelligent or smart material since it shows the functional characteristics of the shape memory effect and superelasticity. Most SMA elements, with these characteristics, perform cyclic motions. In these cases, the fatigue property of SMA is one of the most important issues in view of evaluating functional characteristics of SMA elements. The fatigue properties are complex since they depend on stress, strain, temperature and their hysteresis. If an SMA is implanted with high-energy ions, the thermomechanical properties of the material may change, resulting in long fatigue life. In the present study, the nitrogen ion implantation was applied to modify the surface of a TiNi SMA tape and the influence of implantation treatment on the bending fatigue properties was investigated. Słowa kluczowe: shape-memory alloy, titanium-nickel alloy, superelasticity, nitrogen ion implantation, fatigue, bending Afiliacje autorów:
Takeda K. | - | Aichi Institute of Technology (JP) | Matsui R. | - | Aichi Institute of Technology (JP) | Tobushi H. | - | Aichi Institute of Technology (JP) | Homma S. | - | Nippon Trex Co. (JP) | Levintant-Zayonts N. | - | IPPT PAN | Kucharski S. | - | IPPT PAN |
| 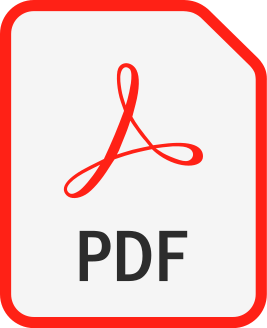 | 20p. |
25. |
Kucharski S., Jarząbek D.M., Depth Dependence of Nanoindentation Pile-Up Patterns in Copper Single Crystals,
METALLURGICAL AND MATERIALS TRANSACTIONS A-PHYSICAL METALLURGY AND MATERIALS SCIENCE, ISSN: 1073-5623, DOI: 10.1007/s11661-014-2437-4, Vol.45A, pp.4997-5008, 2014 Streszczenie: A study of the dependence of nanoindentation pile-up patterns on the indentation load and crystallographic orientation is presented. Three different orientations—(001), (011), and (111)—of single crystal copper were investigated. Experiments were conducted on a CSM ultra-nanoindentation tester using a Berkovich tip. The topographic images were obtained using an atomic force microscope. The evolution of pile-up patterns with different applied loads was observed. The results show that for applied loads equal to 0.45 mN and smaller the pile-up patterns do not depend on the crystallographic orientation of the indented surface; instead, they depend on the tip’s geometry. On the other hand, in the case of indentation loads bigger than 2 mN, pile-up patterns on the surfaces of (001)-, (011)-, and (111)-oriented single crystals have fourfold, twofold, and sixfold (or threefold) symmetry, respectively. An intermediate state was also reported. Furthermore, a detailed analysis of residual impressions with maximal applied loads equal to 2 mN and bigger reveals that both pile-up and sink-in patterns are present. Afiliacje autorów:
Kucharski S. | - | IPPT PAN | Jarząbek D.M. | - | IPPT PAN |
| 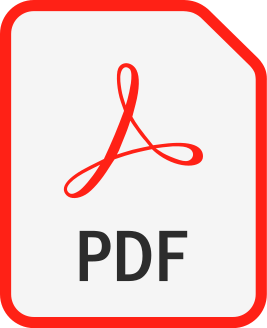 | 35p. |
26. |
Kucharski S., Stupkiewicz S., Petryk H., Surface Pile-Up Patterns in Indentation Testing of Cu Single Crystals,
EXPERIMENTAL MECHANICS, ISSN: 0014-4851, DOI: 10.1007/s11340-014-9883-1, Vol.54, pp.957-969, 2014 Streszczenie: Nano- and micro-indentation of Cu single crystals is performed in directions not aligned with crystallographic axes. Such tests correspond to mechanical characterization of incidentally oriented grains in a polycrystalline or composite material. Orientation and size dependence of complex patterns of surface piling-up and sinking-in around the imprint are investigated. Experimental observations are compared with finite element simulations based on the large deformation crystal plasticity theory. Słowa kluczowe: Copper, Nanoindentation, AFM, EBSD, Crystal plasticity, Finite element method Afiliacje autorów:
Kucharski S. | - | IPPT PAN | Stupkiewicz S. | - | IPPT PAN | Petryk H. | - | IPPT PAN |
| 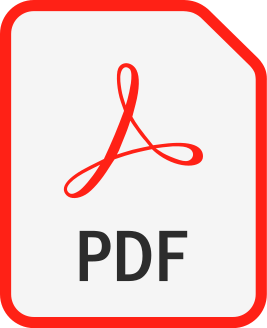 | 35p. |
27. |
Kucharski S., Levintant-Zayonts N., Luckner J., Mechanical response of nitrogen ion implanted NiTi shape memory alloy,
MATERIALS AND DESIGN, ISSN: 0264-1275, DOI: 10.1016/j.matdes.2013.11.056, Vol.56, pp.671-679, 2014 Streszczenie: In the paper a change of material (mechanical) parameters of NiTi shape memory alloy subjected to ion implantation treatment is investigated. The spherical indentation tests in micro- and nano-scale and tension test have been performed to study an evolution of local superelastic effect in different volumes of nonimplanted and nitrogen ion implanted NiTi alloy. The differential scanning calorimetry has been applied to measure the change of characteristic temperatures due to ion implantation treatment. The structure of implanted material has been investigated using electron microscopy technique. It has been found that the ion implantation process changes the properties not only in a thin surface layer but also in bulk material. In the layer the pseudoelastic effect is destroyed, and in the substrate is preserved, however its parameters are changed. The characteristic phase transformation temperatures in substrate are also modified. Słowa kluczowe: Ion implantation, NiTi shape memory alloy, Micro- nano-indentation Afiliacje autorów:
Kucharski S. | - | IPPT PAN | Levintant-Zayonts N. | - | IPPT PAN | Luckner J. | - | IPPT PAN |
| 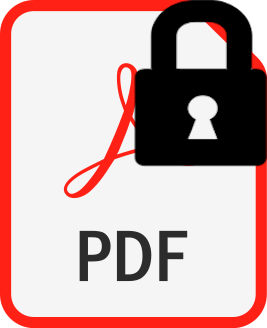 | 35p. |
28. |
Kucharski S., Starzyński G., Study of contact of rough surfaces: Modeling and experiment,
WEAR, ISSN: 0043-1648, DOI: 10.1016/j.wear.2014.01.009, Vol.311, pp.167-179, 2014 Streszczenie: In the paper a problem of contact of rough surface with rigid flat plane is investigated experimentally and numerically. Samples made of three different steels with roughness constituted in a sand-blasting process were compressed in a special experimental setup. 3D surface topographies were measured in initial and deformed state using scanning profilometry. An experimental procedure has been designed that enables specifying load-approach and load-real contact area relations corresponding to plastic deformation of roughness zone. These relations were also simulated using a simple model based on statistical approach with special procedure proposed for a proper specification of sampling interval. The experimental and numerical results have been compared. Słowa kluczowe: Contact mechanics, Roughness, Real contact area, Asperity definition, Sampling interval Afiliacje autorów:
Kucharski S. | - | IPPT PAN | Starzyński G. | - | IPPT PAN |
| 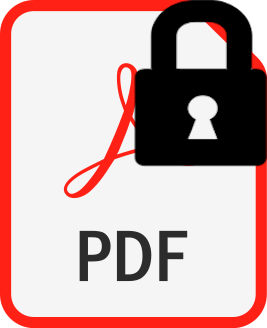 | 35p. |
29. |
Hoffman J., Chrzanowska J., Kucharski S., Mościcki T., Mihailescu I.N.♦, Ristoscu C.♦, Szymański Z., The effect of laser wavelength on the ablation rate of carbon,
APPLIED PHYSICS A-MATERIALS SCIENCE AND PROCESSING, ISSN: 0947-8396, DOI: 10.1007/s00339-014-8506-0, Vol.117, pp.395-400, 2014 Streszczenie: The ablation of graphite is studied as a function of laser fluence for 355, 532 and 1,064 nm wavelength generated by a nanosecond Nd:YAG laser. It has been found that in the case of lower wavelengths, the transition from the thermal ablation to the phase explosion takes place at lower laser fluences. The change of crater shape due to the effect of deep drilling in the proximity of the phase explosion threshold was observed. The calculations of plasma radiation flux to the target surface were made, and the considerable increase of absorbed energy density was found in the case of 355 nm wavelength. Słowa kluczowe: laser ablation, ablation rate, carbon Afiliacje autorów:
Hoffman J. | - | IPPT PAN | Chrzanowska J. | - | IPPT PAN | Kucharski S. | - | IPPT PAN | Mościcki T. | - | IPPT PAN | Mihailescu I.N. | - | National Institute for Lasers, Plasma and Radiation Physics (RO) | Ristoscu C. | - | National Institute for Lasers, Plasma and Radiation Physics (RO) | Szymański Z. | - | IPPT PAN |
| 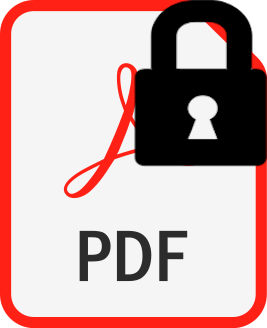 | 30p. |
30. |
Mróz K.P., Bigos A.♦, Kucharski S., Doliński K., Bełtowska-Lehman E.♦, Ni-W Electrodeposited Coatings on Low Carbon Steel Substrate: Fatigue Observations,
Journal of Materials Engineering and Performance, ISSN: 1059-9495, DOI: 10.1007/s11665-014-1149-7, Vol.23, No.10, pp.3459-3466, 2014 Streszczenie: The fatigue response of electrodeposited Ni-W on low carbon steel substrate was studied. The considered Ni-W coatings are a promising substitute for toxic hard chromium coatings which, according to EU directives (2000/53/WE, 2011/37/UE), must be eliminated. Specimens of pure substrate and those covered by coating were compared. Coated specimens exhibited lower fatigue resistance under higher stress amplitudes than their non-coated counterparts in stress-controlled fatigue experiments. However, at lower stress amplitudes, the fatigue strength of both specimen types was similar. The cyclic softening of the coatings was demonstrated using indentation techniques. Słowa kluczowe: fatigue, hardness, indentation, low carbon steel substrate, Ni-W coatings, S-N curve Afiliacje autorów:
Mróz K.P. | - | IPPT PAN | Bigos A. | - | Institute of Metallurgy and Materials Science, Polish Academy of Sciences (PL) | Kucharski S. | - | IPPT PAN | Doliński K. | - | IPPT PAN | Bełtowska-Lehman E. | - | Institute of Metallurgy and Materials Science, Polish Academy of Sciences (PL) |
| 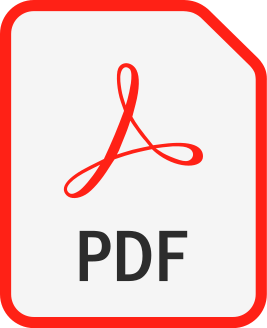 | 20p. |
31. |
Takeda K.♦, Mitsui K.♦, Tobushi H.♦, Levintant-Zayonts N., Kucharski S., Influence of nitrogen ion implantation on deformation and fatigue properties of TiNi shape memory alloy wire,
ARCHIVES OF MECHANICS, ISSN: 0373-2029, Vol.65, No.5, pp.391-405, 2013 Streszczenie: A shape memory alloy (SMA) is expected to be applied as intelligent material since it shows the unique characteristics of the shape memory effect and superelasticity. Most SMA elements, with these characteristics, perform cyclic motions. In these cases, fatigue of SMA is one of the important properties in view of evaluating functional characteristics. The fatigue properties are complex since they depend on stress, strain, temperature and time. If SMA is implanted by high energy ions, the thermomechanical properties may change, resulting in long fatigue life. In the present study, the nitrogen ion implantation was applied to modify TiNi SMA wire surface and the influence of implantation treatment on the tensile deformation and bending fatigue properties was investigated. Słowa kluczowe: shape memory effect, titanium-nickel alloy, nitrogen ion implantation, superelasticity, fatigue Afiliacje autorów:
Takeda K. | - | Aichi Institute of Technology (JP) | Mitsui K. | - | Masupuro Denkoh Corp. (JP) | Tobushi H. | - | Aichi Institute of Technology (JP) | Levintant-Zayonts N. | - | IPPT PAN | Kucharski S. | - | IPPT PAN |
| 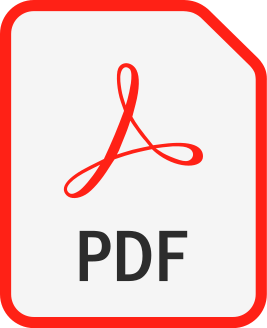 | 20p. |
32. |
Páczelt I.♦, Kucharski S., Mróz Z., The experimental and numerical analysis of quasi-steady wear processes for a sliding spherical indenter,
WEAR, ISSN: 0043-1648, DOI: 10.1016/j.wear.2011.08.026, Vol.274-275, pp.127-148, 2012 Streszczenie: The wear process on a frictional interface in a relative sliding motion of a punch on a substrate induces shape evolution of contact interface. For fixed contact zone the process tends to a steady state with fixed contact stress and strain distribution. Such steady state wear regimes were analyzed in the previous papers [1], [2], [3], [4] and [5] by applying the principle of minimum wear dissipation rate. However, when the contact zone evolves in time due to wear process, as in the case of sliding spherical indenter, a quasi-steady state is reached with stress intensity dependent on the contact size parameter. On the other hand, the contact pressure distribution satisfies the condition of steady state. The simplified numerical analysis of wear process is presented by applying the quasi-steady conditions. The numerical predictions are confronted with experimental test results for two specific cases of soft and hard substrates. The quantitative specification of wear parameters is provided, first assuming constant values throughout the whole wear process, next assuming linearly or exponentially varying during the initial period and tending to constant values. Słowa kluczowe: Spherical indenter, Sliding wear, Contact zone evolution, Wear parameters, Experimental data, Numerical simulation Afiliacje autorów:
Páczelt I. | - | University of Miskolc (HU) | Kucharski S. | - | IPPT PAN | Mróz Z. | - | IPPT PAN |
| 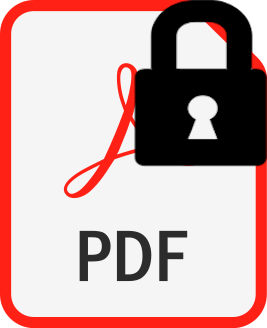 | 40p. |
33. |
Piątkowska A.♦, Kucharski S., Detekcja uszkodzeń pomiarem EA oraz metodami mikroskopowymi,
PROBLEMY EKSPLOATACJI. MAINTENANCE PROBLEMS, ISSN: 1232-9312, Vol.84, No.1, pp.17-25, 2012 Streszczenie: W pracy opisane zostały pomiary emisji akustycznej EA generowanych podczas badania mikrotwardości wgłębnikiem Vickersa, na próbkach krzemowej i stalowej 3 l6L z warstwą węglową. Otrzymane wyniki w postaci wykresów w dziedzinie czasu są porównywane z obserwacjami mikroskopowymi. Za pomocą analitycznego elektronowego mikroskopu skaningowego SEM zobrazowano powierzchnie odcisków, z uwidocznieniem powierzchniowych pęknięć i uszkodzeń. Odcisk mikrotwardości został przecięty z użyciem systemu FIB, zapewniającego odsłonięcie rzeczywistej struktury wewnętrznej materiału w otoczeniu odcisku. Wykonanie sekwencji przekrojów pozwoliło na zobrazowanie SEM przestrzenne uszkodzeń, zwłaszcza typu pęknięcia i rozwarstwienia, a także usytuowanie elementów warstwy wierzchniej i podłoża oraz zasięg odkształceń plastycznych. Zastosowanie obu metod pomiarowych: emisji akustycznej oraz obrazowania mikroskopowego, wzajemnie uzupełniających się, daje wnikliwą diagnostykę do analizy właściwości mechanicznych materiału. Słowa kluczowe: emisja akustyczna, badanie twardości, uszkodzenia, warstwa węglowa RF PACVD, FIB Afiliacje autorów:
Piątkowska A. | - | Institute of Electronic Materials Technology (PL) | Kucharski S. | - | IPPT PAN |
| 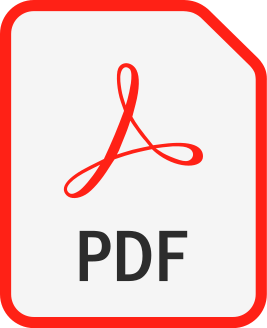 | 5p. |
34. |
Kucharski S., Mróz Z., Identification of wear process parameters in reciprocating ball-on-disc tests,
TRIBOLOGY INTERNATIONAL, ISSN: 0301-679X, DOI: 10.1016/j.triboint.2010.10.010, Vol.44, pp.154-164, 2011 Streszczenie: Wear test results are presented for a spherical indenter in reciprocal motion interacting with soft (aluminium alloy) and hard (construction steel) substrates. The aim of this paper is to provide evidence of the evolution of the contact zone, specification of wear scar depth and surface roughness in the contact zone. Numerical analysis of the interaction of the sliding sphere with the wear track provided contact zone dimensions, although these differed from the experimental data. The incremental wear factor is also introduced in the paper, while the formulae for the wear volume of the sphere recommended by ASTM have been improved. Słowa kluczowe: Dry wear, Contact area, Wear factor, Finite element method Afiliacje autorów:
Kucharski S. | - | IPPT PAN | Mróz Z. | - | IPPT PAN |
| 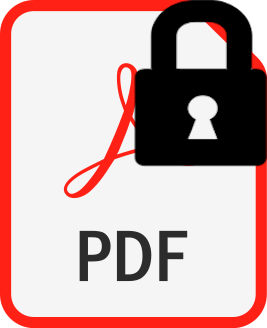 | 40p. |
35. |
Levintant-Zayonts N., Kucharski S., Influence of High Fluence Nitrogen Ion Implantation on Pseudoelastic Behaviour of NiTi Shape Memory Alloy,
ACTA PHYSICA POLONICA A, ISSN: 0587-4246, Vol.120, No.1, pp.79-82, 2011 Streszczenie: An attempt to evaluate mechanical properties changes (superelastic phenomena) in the shape memory NiTi alloy (austenitic form) due to ion implantation (N+, fluences of 1x10^17 and 4x10^18 cm-2 ) has been made. We applied the differential scanning calorimetry technique and spherical indentation (micro- and nanoindentation scale) test to study superelastic effect. The results of investigations of selected functional properties, i.e. characteristic temperatures, total and recovered penetration depth on the implanted and non-implanted NiTi samples are presented. Słowa kluczowe: superelastic phenomena, shape memory alloy, nitinol, nitrogen ion implantation Afiliacje autorów:
Levintant-Zayonts N. | - | IPPT PAN | Kucharski S. | - | IPPT PAN |
| 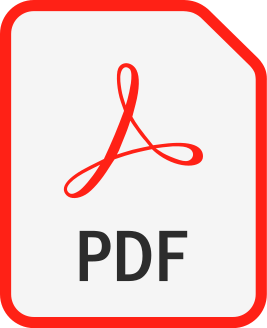 | 15p. |
36. |
Levintant-Zayonts N., Kucharski S., Lokalny efekt pamięci kształtu w stopie NiTi przed i po implantacji jonowej,
INŻYNIERIA MATERIAŁOWA, ISSN: 0208-6247, Vol.183, No.5, pp.855-861, 2011 Streszczenie: W przedstawionej pracy zastosowano metodę implantacji jonowej (jako techniki konstytuowania warstw wierzchnich) do modyfikacji własności stopu z pamięcią kształtu (SMA-Shape Memory Alloy) NiTi (w postaci martenzytycznej). Przedmiotem badań było określenie zmian własności kompozytu „warstwa implantowana+rdzeń” (rys. 2) po implantacji azotem (1x1018j/cm2, 65keV) na stopie NiTi oraz określenie wpływu implantacji jonowej na własności lokalnego efektu pamięci kształtu (EPK). Przedstawiono badania wybranych charakterystyk funkcjonalnych: temperatur charakterystycznych implantowanego stopu NiTi, a także zmian trwałych odkształceń w zależności od temperatury. Wykorzystano test mikroindentacji i profilometrii skaningowej. Metodą transmisyjnej mikroskopii elektronowej (TEM) badano mikrostrukturę stopu NiTi, a pomiary RBS zastosowano do oszacowania profili rozkładów pierwiastków po implantacji jonowej. W pracy potwierdzono, że zachowanie materiału NiTi bardzo zależy od temperatury. Pokazano, również, że test wgniatania wgłębnika kulistego w powierzchnie może posłużyć do identyfikacji implantowanej warstwy.
Słowa kluczowe: implantacja jonowa, efekt pamięci kształtu, stopy z pamięcią kształtu, indentacja Afiliacje autorów:
Levintant-Zayonts N. | - | IPPT PAN | Kucharski S. | - | IPPT PAN |
| 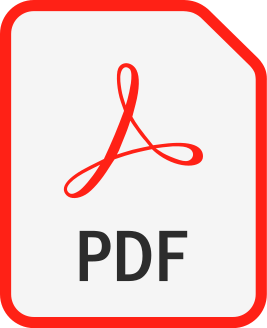 | 7p. |
37. |
Kucharski S., Starzyński G., Bartoszewicz A., Prediction of surface roughness in metal forming with liquid lubricant,
TRIBOLOGY INTERNATIONAL, ISSN: 0301-679X, DOI: 10.1016/j.triboint.2009.04.028, Vol.43, pp.29-39, 2010 Streszczenie: In the paper an experimental study of compression of rough surface in the presence of lubricant and in dry state is presented. The evolution of roughness parameters was analyzed. In the lubrication conditions an existence of asymptotic state was observed where roughness parameters and real contact area stabilize due to hydrostatic response of lubricant. The simplified model was proposed allowing to predict the roughness parameters and real contact area of the deformed surface in the asymptotic state. The model is based on analysis of topography of the undeformed surface and compression of a singular lubricant pit. The analysis was performed both numerically and experimentally. Słowa kluczowe: Hydrostatic lubrication, Normal contact, Surface topography Afiliacje autorów:
Kucharski S. | - | IPPT PAN | Starzyński G. | - | IPPT PAN | Bartoszewicz A. | - | IPPT PAN |
| 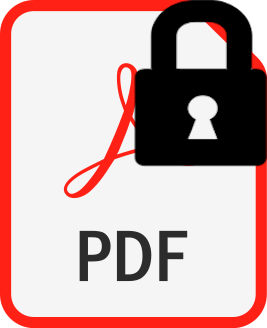 | 32p. |
38. |
Levintant-Zayonts N., Kucharski S., Surface characterization and wear behavior of ion implanted NiTi shape memory alloy,
VACUUM, ISSN: 0042-207X, DOI: 10.1016/j.vacuum.2009.01.068, Vol.83, No.Supplement 1, pp.S220-S223, 2009 Streszczenie: The aim of this study was investigation of changes in the modified near-surface layer on the NiTi shape memory alloy, caused by ion implantation as well as their influence on the mechanical and shape memory properties of this material. Surface of NiTi has been modified by nitrogen ion beam at several fluences 1 × 1017 cm−2, 1 × 1018 cm−2 and 2 × 1018 cm−2 at the energy 50 keV. The effect of implantation parameters on surface characteristics and wear properties was investigated using dry-sliding-wear test, depth sensing indentation test and scanning profilometry method. The experimental results have shown how the ion implantation treatment can change the original surface: reducing Ni content in the surface, increasing the surface hardness (furthermore, the hardness improvement extended to the regions much deeper than the implanted layer), and improving the sliding wear resistance. The experimental results of surface treatment conditions and mechanical properties of the modified NiTi alloys are compared, analyzed and discussed in this paper. Słowa kluczowe: Shape memory NiTi alloy, Ion implantation, Wear, Surface characterization Afiliacje autorów:
Levintant-Zayonts N. | - | IPPT PAN | Kucharski S. | - | IPPT PAN |
| 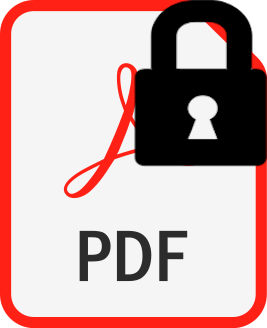 | 27p. |
39. |
Levintant-Zayonts N., Kucharski S., Analiza zmian pseudosprężystych własności stopu NiTi z pamięcią kształtu spowodowanych implantacją jonową,
INŻYNIERIA MATERIAŁOWA, ISSN: 0208-6247, Vol.1, pp.45-53, 2009 Streszczenie: Stopy z osnową NiTi należą do grupy najlepszych materiałów z pamięcią kształtu [1]. Szeroki zakres zastosowań w medycynie i technice [2], [3], [4] powoduje zwiększenie roli stanu ich powierzchni. Zagadnienia modyfikacji powierzchni stopu NiTi w kontekście polepszenia jej charakterystyk – z jednej strony, i zachowania funkcjonalnych własności (efektu pamięci kształtu i pseudosprężystości) z drugiej strony, - stawiane są coraz częściej [6], [7]. W przedstawianej pracy jest pokazana próba oceny zmian własności mechanicznych stopu NiTi implantowanego azotem (zakres dawek 1x1017–3x1018j/cm2). Wykorzystano test mikroindentacji. Przedstawiono badania wybranych charakterystyk funkcjonalnych, głównie zmian odkształceń odzyskiwanych i trwałych, a także temperatur charakterystycznych implantowanego topu NiTi w warunkach pokojowej i podwyższonej temperatury. Słowa kluczowe: stopy z pamięcią kształtu, implantacja jonowa, pseudospręzystość Afiliacje autorów:
Levintant-Zayonts N. | - | IPPT PAN | Kucharski S. | - | IPPT PAN |
| | 9p. |
40. |
Kucharski S., Mróz Z., Identification of yield stress and plastic hardening parameters from a spherical indentation test,
INTERNATIONAL JOURNAL OF MECHANICAL SCIENCES, ISSN: 0020-7403, DOI: 10.1016/j.ijmecsci.2007.03.013, Vol.49, No.11, pp.1238-1250, 2007 Streszczenie: Assuming plastic hardening of metals are specified by the stress–strain curve in the form View the MathML sourceσ=σ0+kεpm, the material parameters σ0, k and m are identified from spherical indentation tests by measuring compliance moduli in loading and unloading of the load–penetration curve. The curve P(hp) is analytically described by a two term expression, each with different exponents. Here, εp and hp denote the plastic strain and permanent penetration. The proposed identification method is illustrated by specific examples including numerical and physical identification tests. Słowa kluczowe: Spherical indentation test, Identification, Finite element modelling, Elasto-plastic material properties Afiliacje autorów:
Kucharski S. | - | IPPT PAN | Mróz Z. | - | IPPT PAN |
| 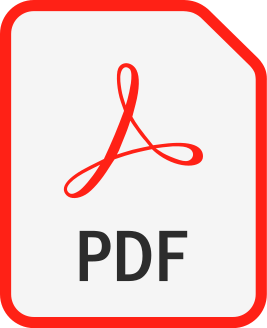 |
41. |
Kucharski S., Wpływ stanu warstwy wierzchniej na trwałość zmęczeniową elementu z karbem,
PRZEGLĄD MECHANICZNY, ISSN: 0033-2259, Vol.3, pp.27-32, 2005 | 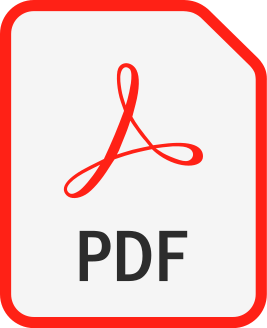 |
42. |
Kucharski S., Starzyński G., Symulacja wpływu nagniatania na ewolucję naprężeń i trwałość zmęczeniową elementu z warstwą wierzchnią,
PRZEGLĄD MECHANICZNY, ISSN: 0033-2259, Vol.3, pp.23-27, 2005 | 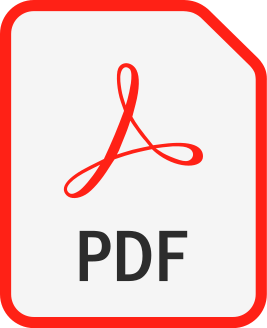 |
43. |
Kucharski S., Mróz Z., Identification of material parameters by means of compliance moduli in spherical indentation test,
MATERIALS SCIENCE AND ENGINEERING A-STRUCTURAL MATERIALS PROPERTIES MICROSTRUCTURE AND PROCESSING, ISSN: 0921-5093, DOI: 10.1016/j.msea.2004.03.030, Vol.379, No.1-2, pp.448-456, 2004 Streszczenie: An identification method of elastic and plastic hardening parameters is proposed by measuring compliance moduli in loading and unloading in the spherical indentation test. The loading program is composed of consecutive loading and unloading steps from which the compliance moduli are determined from the load–penetration (P–h) curve. The hardening parameters k and m occurring in the plastic hardening curve Full-size image (<1 K) are then specified. Identification of materials described by a more complex three parameters constitutive law εp=((σ−σy)/k)′1/m′, where σy denotes the yield stress, is also analysed. The identification of Young’s modulus from the indentation test is also presented. Słowa kluczowe: Spherical indentation test, Identification, Elasto-plastic material properties, Indentation compliance moduli Afiliacje autorów:
Kucharski S. | - | IPPT PAN | Mróz Z. | - | IPPT PAN |
| 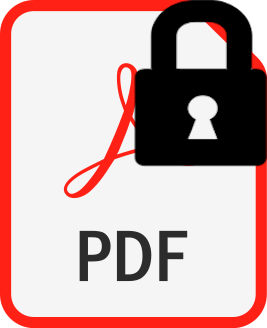 |
44. |
Kucharski S., Mróz Z., Identification of plastic hardening parameters of metals from spherical indentation tests,
MATERIALS SCIENCE AND ENGINEERING A-STRUCTURAL MATERIALS PROPERTIES MICROSTRUCTURE AND PROCESSING, ISSN: 0921-5093, DOI: 10.1016/S0921-5093(01)01334-X, Vol.318, No.1-2, pp.65-76, 2001 Streszczenie: Using the two-parameter power hardening rule σ=kεpm, the parameters k and m are identified from spherical indentation loading–unloading tests which account for the variation of the indentation profile during elastic unloading and sphere deformation. The predicted and measured stress–strain curves are compared for several materials. Both experimental and actual data for 18G2A low-alloy steel are used to assess the accuracy of the identification procedure. Finally, identification of the stress–strain curve of an aluminium alloy is demonstrated. Słowa kluczowe: Spherical indentation tests, Plastic, Low-alloy steel, Metals Afiliacje autorów:
Kucharski S. | - | IPPT PAN | Mróz Z. | - | IPPT PAN |
| 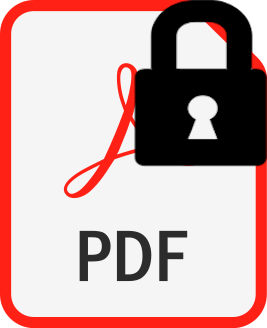 |