1. |
Sielamowicz I.♦, Czech A.♦, Kowalewski T.A., Comparative analysis of empirical descriptions of eccentricflow in silo model by the linear and nonlinear regressions,
POWDER TECHNOLOGY, ISSN: 0032-5910, DOI: 10.1016/j.powtec.2014.10.007, Vol.270, pp.393-410, 2015 Abstract: This paper is a third of a series of the three where eccentric cases of flow in silo models recorded by the DPIV technique are presented and discussed in detail. The methodology of empirical descriptions of velocities, flow rate and stagnant zone boundaries on the base of registered velocity fields in eccentric filling and discharge in 2D silo model was discussed. In previous two papers [1] and [2] we analyzed also eccentric flows but with different locations of the outlet. It was stated that in practice even tiny eccentricity of filling or discharge processes may lead to quite an unexpected behavior of the silo structure. During asymmetrical processes, flow patterns and wall stresses may be quite different. It is therefore crucial to identify how flow patterns developed in the material during eccentric filling or discharge and to determine both the flow rate and wall stresses occurring under such state of loads. Thus, we discuss here the third case of discharge — located in the center of the silo bottom. A comparison of these three cases of discharge mode will be presented in the next paper. Empirical descriptions of eccentric flow velocities in silo model by the linear and nonlinear regressions are presented here with specific functions like the Gaussian function and “the double logarithmic function”. In both methods the velocity was also descripted by linearization and in the Gaussian method also by the nonlinear method of Gauss–Newton and in the case of the method of double logarithm — the nonlinear method of Levenberg–Marquardt was applied. Velocities were predicted by using interpolation due to the nonlinear model of the Gaussian type and to the nonlinear function of “the double logarithm”. Keywords: Eccentric granular flow, Silo model, Empirical description, Linear and nonlinear regression, Gaussian description, Double logarithm Affiliations:
Sielamowicz I. | - | University of Zielona Góra (PL) | Czech A. | - | Bialystok University of Technology (PL) | Kowalewski T.A. | - | IPPT PAN |
| 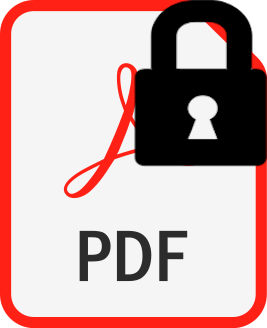 |
2. |
Balevičius R.♦, Sielamowicz I.♦, Mróz Z., Kačianauskas R.♦, Effect of rolling friction on wall pressure, discharge velocity and outflow of granular material from a flat-bottomed bin,
PARTICUOLOGY, ISSN: 1674-2001, DOI: 10.1016/j.partic.2012.07.002, Vol.10, pp.672-682, 2012 Abstract: The present paper provides both experimental and DEM analyses of the filling and discharge of pea grains from a 3D flat-bottomed bin. In the DEM model, the fixed mean values of the experimentally determined single particle data, such as the particle density, Young's modulus, Poisson's ratio as well as the sliding and rolling friction coefficients were incorporated to analyse their effects on the macroscale indicators, such as the wall pressure, discharge velocities and material outflow parameters. The effect of rolling friction was studied based on the experimentally measured single particle rolling friction coefficient. This analysis is aimed at the quantitative prediction of flow parameters as related to the identification of material parameters. Keywords: Visco-elastic granular material, Discrete element method, Rolling friction, Wall pressure, Material velocity, Outflow mass, Outflow rate, Biosystems, Pea grains Affiliations:
Balevičius R. | - | Vilnius Gedyminas Technical University (LT) | Sielamowicz I. | - | University of Zielona Góra (PL) | Mróz Z. | - | IPPT PAN | Kačianauskas R. | - | Vilnius Gedyminas Technical University (LT) |
| 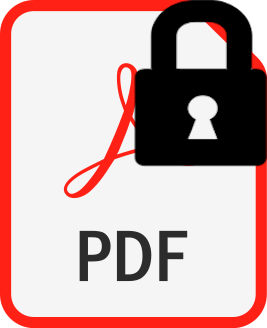 |
3. |
Balevičius R.♦, Sielamowicz I.♦, Mróz Z., Kačianauskas R.♦, Investigation of wall stress and outflow rate in a flat-bottomed bin: a comparison of the DEM model results with the experimental measurements,
POWDER TECHNOLOGY, ISSN: 0032-5910, DOI: 10.1016/j.powtec.2011.08.042, Vol.214, pp.322-336, 2011 Abstract: The present paper provides a discrete element method (DEM) analysis of the filling and discharge processes of granular material in a 3D flat-bottomed bin. A granular aggregate of nearly round particles (20,400 pea grains, 7.2–7.8 mm in diameter) is considered. The numerical results are compared with the experimental data. The DEM analysis provides an accurate prediction of wall stress distribution and the outflow rate of discharge throughout the bottom orifice. The stress distribution developed within the granular material after filling and during the discharge phase is considered, and the transition from the active to passive stress state is discussed. This analysis aims to quantitatively predict the flow parameters related to the careful identification of the material parameters. The investigation presented may be useful for the ongoing development of DEM. Keywords: Visco-elastic granular material, Discrete element method, Wall pressure, Granular material stress, Micro-properties, Bulk properties Affiliations:
Balevičius R. | - | Vilnius Gedyminas Technical University (LT) | Sielamowicz I. | - | University of Zielona Góra (PL) | Mróz Z. | - | IPPT PAN | Kačianauskas R. | - | Vilnius Gedyminas Technical University (LT) |
| 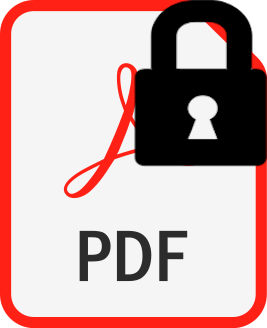 |
4. |
Sielamowicz I.♦, Czech M.♦, Kowalewski T.A., Empirical analysis of eccentric flow registered by the DPIV technique inside a silo model,
POWDER TECHNOLOGY, ISSN: 0032-5910, DOI: 10.1016/j.powtec.2011.04.022, Vol.212, pp.38-56, 2011 Abstract: In this paper we continue empirical description of eccentric granular flow registered by the DPIV (Digital Particle Image Velocimetry) technique. The first results concerning eccentric flow with the outlet located on the right were published in Sielamowicz et al. [30]. Here we present a methodology of empirical descriptions of velocities, flow rate and the flow channel boundary (FCB) in another eccentric case. The analysis is based on the experimental results (velocity profiles) obtained in the DPIV technique. Statistical analysis of the experimental results was also performed. We show how to fit the proper type of function to describe flow parameters in the silo model. The presented methodology is universal and can be applied in any case of eccentric flow of any granular material. Keywords: Universal methodology of empirical analysis, DPIV technique, Eccentric granular flow, Discharge on the left, Vertical model, Plexiglas, Velocity, Gaussian type function, Ch function, Multiple regression, “Joined functions”, Flow channel boundary (FCB) Affiliations:
Sielamowicz I. | - | University of Zielona Góra (PL) | Czech M. | - | Technical University of Białystok (PL) | Kowalewski T.A. | - | IPPT PAN |
| 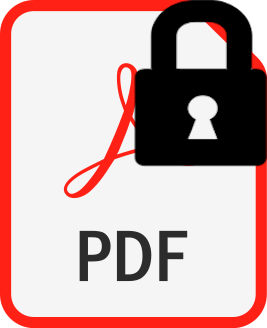 |
5. |
Balevičius R.♦, Kačianauskas R.♦, Mróz Z., Sielamowicz I.♦, Analysis and DEM simulation of granular material flow patterns in hopper models of different shapes,
ADVANCED POWDER TECHNOLOGY, ISSN: 0921-8831, DOI: 10.1016/j.apt.2010.12.005, Vol.22, pp.226-235, 2011 Abstract: By using the discrete element method (DEM) a comparison and observations on material flow patterns in plane-wedged, space-wedged, and flat-bottomed hopper were accounted for. Numerical results obtained by combining data of individual particles, statistical processing of particle assemblies and evaluation of the field variables provided the essential characteristics for different regimes of the discharge flow (within steady or unsteady state of flow) and the differences in differently shaped hoppers due to different microscopic inter-particle friction. For validation of the performed simulations, velocity patterns developed in three-dimensional flat-bottomed hopper containing 20,400 pea grains were also analysed. To represent the continuum by avoiding the local effects produced by the individual grains, the simulation results were focused on the mean velocity distributions with data smoothening. The effect of rolling resistance on granular material flow was also considered. Keywords: DEM, Mass flow rate, Velocity distribution, Plane-wedged, Space-wedged, Flat-bottomed hoppers Affiliations:
Balevičius R. | - | Vilnius Gedyminas Technical University (LT) | Kačianauskas R. | - | Vilnius Gedyminas Technical University (LT) | Mróz Z. | - | IPPT PAN | Sielamowicz I. | - | University of Zielona Góra (PL) |
| 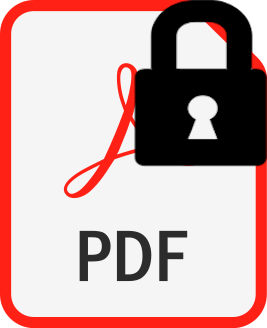 |
6. |
Sielamowicz I.♦, Czech M.♦, Kowalewski T.A., Empirical description of granular flow inside a model silo with vertical walls,
BIOSYSTEMS ENGINEERING, ISSN: 1537-5110, DOI: 10.1016/j.biosystemseng.2011.01.004, Vol.108, pp.334-344, 2011 Abstract: DPIV (Digital Particle Image Velocimetry) is often used to record the flows in silo models and to recognise the flow in two-dimensional structures. Flow in a two-dimensional laboratory model with transparent walls was recorded using the DPIV technique. Recorded images were processed and the velocities of the flowing material were obtained. Statistical analysis of the readings taken from velocity profiles was also performed. To describe the flow the theoretical model of velocity presented in Choi, Kudrolli, and Bazant (2005) was modified. An empirical description of the flow rate was carried out. An analysis of the kinematic parameter b was carried out and compared to the solutions given by Medina, Córdova, Luna, and Treviño (1998) and Choi et al. (2005). Comparisons between the experimental measurements and the empirical descriptions are presented. Comparing the Gaussian based kinematic model of Choi et al. (2005) and a modified empirical kinematic model, a better description of velocity was obtained by using the latter. In further comparisons using the two aformentioned models and a parabolic description the best description of velocity was given by the parabolic function. Flow rate was analysed using the three types of functions. Both the Gaussian and modified empirical kinematic model gave almost the same values for calculated levels h = 5, 10 cm. Using the parabolic description the value of flow rates differed slightly. The flow channel boundary was analysed using parabolic and hyperbolic descriptions. Both descriptions were good because the correlation coefficients, had values ranging from 0.928 to 0.997. Affiliations:
Sielamowicz I. | - | University of Zielona Góra (PL) | Czech M. | - | Technical University of Białystok (PL) | Kowalewski T.A. | - | IPPT PAN |
| 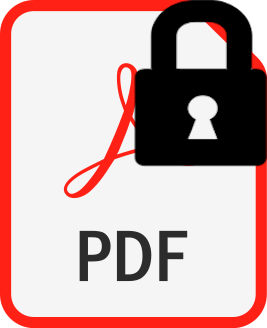 |
7. |
Sielamowicz I.♦, Czech M.♦, Kowalewski T.A., Empirical description of flow parameters in eccentric flow inside a silo model,
POWDER TECHNOLOGY, ISSN: 0032-5910, Vol.198, pp.381-394, 2010 Abstract: The paper presents the methodology of empirical description and statistical analysis of velocity profiles that were depicted by the Digital Particle Image Velocimetry technique (DPIV). Experimental runs were recorded by the high resolution camera in the model with vertical walls. Here we analyze the eccentric discharge with the outlet located in the bottom close to the right vertical wall of the model. On the base of the experimental results we present an empirical analysis of velocities and calculation of the flow rate in two proposed descriptions of the flow. Velocity functions were presented by the exponential function (the modi fi ed Gauss type), by the multiple regression and by the ch function. Also the fl ow rate was calculated for two presented descriptions. Empirical calculations of the stagnant zone boundary was also presented using the readings from velocity profiles. Keywords: Particle Image Velocimetry, granular flow, Multiple regression Affiliations:
Sielamowicz I. | - | University of Zielona Góra (PL) | Czech M. | - | Technical University of Białystok (PL) | Kowalewski T.A. | - | IPPT PAN |
| 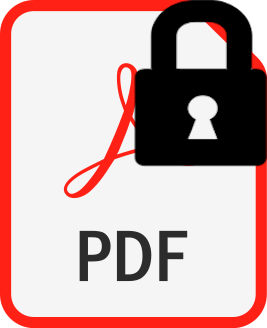 |
8. |
Balevičius R.♦, Kačianauskas R.♦, Mróz Z., Sielamowicz I.♦, Discrete particle investigation of friction effect in filling and unsteady/steady discharge in three-dimensional wedge shaped hopper,
POWDER TECHNOLOGY, ISSN: 0032-5910, DOI: 10.1016/j.powtec.2008.02.006, Vol.187, No.2, pp.159-174, 2008 Abstract: The friction effect in filling and unsteady/steady discharge of three-dimensional wedge-shaped hopper was considered numerically by the discrete element method. The presented model is based on contact mechanics of a single spherical particle involving Hooke's law of spring interaction, static and dynamic friction as well as viscous damping forces. The hopper filling process en masse was performed while the modeling of uncontrolled and controlled discharge was simulated. The evolution of the kinetic energy of filling, the distribution of stresses within granular material and stresses acting on the walls, as well as the change in fields of material porosity were investigated at the stages of filling and discharge of the hopper. The variation of flow velocities, the discharged mass fractions as well as discharge fraction rates were analyzed. The friction effect was analyzed by varying inter-particle friction coefficient over the range of 0–0.6. A comparison of the numerical results with available continuum-based predictions was also presented. Keywords: Visco-elastic granular material, 3D wedge-shaped hopper, Discrete element method, Wall pressure, Granular stresses, Fraction discharged, Bulk porosity Affiliations:
Balevičius R. | - | Vilnius Gedyminas Technical University (LT) | Kačianauskas R. | - | Vilnius Gedyminas Technical University (LT) | Mróz Z. | - | IPPT PAN | Sielamowicz I. | - | University of Zielona Góra (PL) |
| 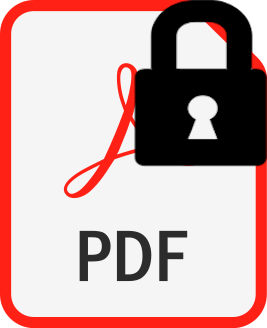 |
9. |
Balevičius R.♦, Kačianauskas R.♦, Mróz Z., Sielamowicz I.♦, Microscopic and macroscopic analysis of granular material behaviour in 3D flat-bottomed hopper by the discrete element methody,
ARCHIVES OF MECHANICS, ISSN: 0373-2029, Vol.59, No.3, pp.231-257, 2007 Abstract: The paper presents the application of the discrete element method to modelling of granular material filling and discharge in 3D flat-bottomed hopper. A mathematical model, as well as the developed software code, operates with spherical visco-elastic non-cohesive frictional particles. The evolution of granular flow, internal forces and densification (rarefaction) are characterized by macroscopic parameters such as the discharge rates, the porosity fields and the wall pressures, as well as by microscopic evaluations in terms of coordination number, velocity patter ns and inter-particle contact forces. It was shown that qualitative characterization of flow may be done even by relatively rough models with small number of particles, which required to be increased, however, for more precise description of the localize d phenomena. Unsatisfactory evaluation of the stress peak during discharge is p resented as an illustrative example. The main focus of the paper is the analysis of particle friction effect and the consistency of micro and macro-phenomena in the time-dependent flow process. Keywords: discrete element method, spherical particles, visco-elastic granular material, three-dimensional flat bottomed hopper Affiliations:
Balevičius R. | - | Vilnius Gedyminas Technical University (LT) | Kačianauskas R. | - | Vilnius Gedyminas Technical University (LT) | Mróz Z. | - | IPPT PAN | Sielamowicz I. | - | University of Zielona Góra (PL) |
| 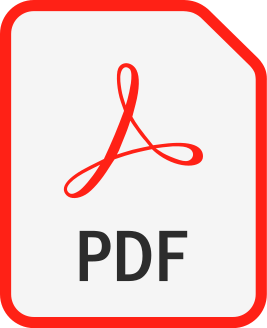 |
10. |
Balevičius R.♦, Kačianauskas R.♦, Mróz Z., Sielamowicz I.♦, Discrete element method applied to multiobjective optimization of discharge flow parameters in hoppers,
STRUCTURAL AND MULTIDISCIPLINARY OPTIMIZATION, ISSN: 1615-147X, DOI: 10.1007/s00158-005-0596-z, Vol.31, pp.163-175, 2006 Abstract: Multiobjective approach for optimization of the discharge flow parameters of viscoelastic frictional granular material in a wedge-shaped hopper with fixed outlet orifice is considered. The discharge time and the discharge flow rate are taken as optimality criteria, while the discharge mass of material and the shape of the hopper are considered as design variables. The discrete concept and numerical discrete element method (DEM) are applied to the analysis of granular flow. The filling problem considered as numerical generation of the initial conditions for discharge flow was initially solved. The presented DEM model was validated by examining the wall pressures and comparing them with the results of classical macroscopic pressure prediction. Variation of optimality criteria and Pareto set is demonstrated by the numerical results. Sensitivity of optimality criteria to interparticle friction is also investigated. Keywords: Viscoelastic granular material, Hopper, Discrete element method, Optimization of flow parameters Affiliations:
Balevičius R. | - | Vilnius Gedyminas Technical University (LT) | Kačianauskas R. | - | Vilnius Gedyminas Technical University (LT) | Mróz Z. | - | IPPT PAN | Sielamowicz I. | - | University of Zielona Góra (PL) |
| 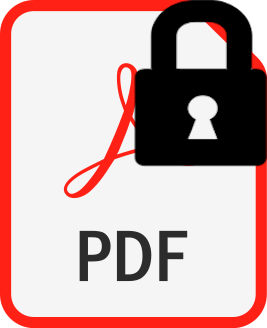 |
11. |
Sielamowicz I.♦, Błoński S., Kowalewski T.A., Digital Particle Image Velocimetry (DPIV) technique in measurements of granular material flows, Part 2 of 3 - converging hoppers,
CHEMICAL ENGINEERING SCIENCE, ISSN: 0009-2509, Vol.61, pp.5307-5317, 2006 Abstract: The flow evolution of an amaranth seed is being investigated in a wedge-shaped model made of Plexiglas. The objective of this paper is to recognise flow patterns in the flowing material, and also to depict evolution of velocity fields, flow field discontinuities, velocity profiles for cross-sections of the model, shear zones and flow streamlines using the digital particle image velocimetry (DPIV) optical technique. It is demonstrated that the DPIV technique used in the experiments enables quantitative analysis of the flow zones geometry. The technique also allows to reveal boundaries between flowing and stagnant zones and to extract velocity profiles at any selected sections of the model. Keywords: Optical technique, DPIV, Granular material flows, Converging hopper, Particle, Plug flow, Shear zones, Discharge flow rate Affiliations:
Sielamowicz I. | - | University of Zielona Góra (PL) | Błoński S. | - | IPPT PAN | Kowalewski T.A. | - | IPPT PAN |
| 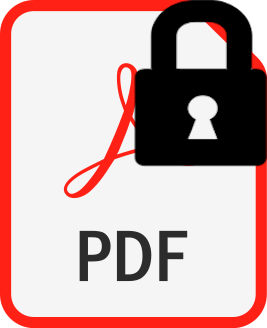 |
12. |
Sielamowicz I.♦, Kowalewski T.A., Błoński S., Optical technique DPIV in measurements of granular material flows, Part 1/3 - plane hoppers,
CHEMICAL ENGINEERING SCIENCE, ISSN: 0009-2509, DOI: 10.1016/j.ces.2004.07.135, Vol.60, pp.589-598, 2005 Abstract: The aim of this paper is to present the evolution of plug flow developing in three densely packed granular materials in the model of a hopper made of Plexiglas. For this purpose, the digital particle image velocimetry (DPIV) technique is applied to analyse the flow field of the granular material. When discharge starts, a plug flow zone in the flowing material expands upward. This zone changes its width reaching the upper surface of the material. The plug flow evolution as a function of time is described using DPIV. This technique yields the velocity profiles of flowing granular materials, velocity magnitude contours, vector fields, velocity distributions on certain levels in the model and traces of the selected particles. The results obtained for the evolution of the vertical velocity, height and width of the plug flow zone as a function of time, measured at the symmetry axis of the model for the amarantus seed are compared to the results obtained by Waters and Drescher. Measurements of the stagnant boundary as a function of time are compared to the results available in the literature Keywords: Optical technique, Experiments, Granular, Materials, Flow, Particle, Plug flow Affiliations:
Sielamowicz I. | - | University of Zielona Góra (PL) | Kowalewski T.A. | - | IPPT PAN | Błoński S. | - | IPPT PAN |
| 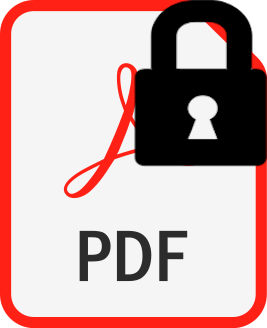 |
13. |
Mróz Z., Sielamowicz I.♦, Deformation Zones in Granular Materials in Hoppers During Filling and Emptying Processes,
ENGINEERING TRANSACTIONS (ROZPRAWY INŻYNIERSKIE), ISSN: 0867-888X, Vol.51, No.4, pp.461-491, 2003 Abstract: The present paper is concerned with the simplified analysis of deformation and stress states in converging hoppers during filling and discharge of a granular material. The equilibrium conditions and stress-strain relations are satisfied for cylindrical slice elements assuming dependence of displacement and stress on radial coordinate. The elastic or elasto-plastic material model is used with the Coulomb yield condition and non-associated flow rule. The paper presents a detailed analysis of pressure evolution of a granular material on a hopper wall during the emptying process when the initial active state of pressure is transformed into the passive state. The growth of wall pressure associated with this process is demonstrated. The analytical treatment presented in this paper can be compared with the respective finite element solution. Affiliations:
Mróz Z. | - | IPPT PAN | Sielamowicz I. | - | University of Zielona Góra (PL) |
| 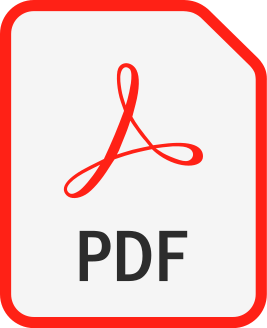 |