1. |
Jarząbek D.M., Siewert D.♦, Fabianowski W.♦, Schift H.♦, Rymuza Z.♦, Jung T.♦, Influence of Alkali Ions on Tribological Properties of Silicon Surface,
TRIBOLOGY LETTERS, ISSN: 1023-8883, DOI: 10.1007/s11249-015-0603-5, Vol.60, No.2, pp.1-8, 2015 Abstract: Tribological properties of surfaces (friction, adhesion and wear) provide challenging limitations to the design of reliable machines on the micro- and nanometer scale as the surface to volume area increases and volume, mass and inertia of the mobile parts decrease. This study reports on the reduction in the friction force of silicon surfaces after the alkali metal ion exposure in the form of aqueous solutions. A scanning force microscope equipped with a liquid cell was used to investigate the friction force and the pull-off force of a flat silicon surface immersed in water and in different alkali metal chlorides solutions: LiCl, NaCl and CsCl. The concentration ranged from 0.1 up to 1000 µmol/l. The changes in the free surface energy of the initial surface and of the modified surfaces after drying were determined from contact angle measurements and from the acid–base adhesion theory. In both cases, in the liquid environment and after drying of the exposed silicon substrates in air, the friction force is reduced by approximately 50 %. Our results provide new, fundamental insight into the exchange of surface termination layers in particular for tribology. Also it is suggested to use the procedure as a low-cost alternative to improve the tribological properties of the silicon surface in particular in applications where lubricating fluids are not appropriate, e.g., in nanomachines and devices. Keywords: Silicon surface, Scanning force microscopy, Friction, Adhesion, Alkali metal chlorides Affiliations:
Jarząbek D.M. | - | IPPT PAN | Siewert D. | - | Paul Scherrer Institut (CH) | Fabianowski W. | - | Paul Scherrer Institut (CH) | Schift H. | - | Paul Scherrer Institut (CH) | Rymuza Z. | - | other affiliation | Jung T. | - | Paul Scherrer Institut (CH) |
| 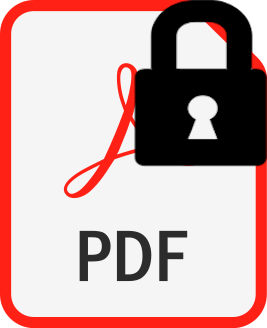 |
2. |
Jarząbek D.M., Kaufmann A.N.♦, Schift H.♦, Rymuza Z.♦, Jung T.A.♦, Elastic modulus and fracture strength evaluation on the nanoscale by scanning force microscope experiments,
NANOTECHNOLOGY, ISSN: 0957-4484, DOI: 10.1088/0957-4484/25/21/215701, Vol.25, pp.215701-1-9, 2014 Abstract: This work first reviews the capability of scanning force microscopy (SFM) to perform experiments with forces in a wide range, from low non-contact forces to high contact forces which induce mechanical deformations in the substrate. In analogy to fracture strength evaluation, as established in materials science, SFM is used to exert forces on pillars with nanometer dimensions while the cantilever deformations are monitored quantitatively. Hence, it is possible to bend the pillars until the threshold for triggering fracture is reached, and to determine the mechanical properties at the different stages of this process. Using this novel approach, in combination with 'state of the art' nanofabrication to produce nanopillar arrays on silicon and silicon dioxide substrates, a number of experiments are performed. Furthermore, quantitative measurements of the fracture strength of Si and of the SiO2/Si interface and E-modulus are presented. To analyze the experimental data obtained in the different experimental procedures and modes, finite element method calculations were used. The methods introduced herein provide a versatile toolbox for addressing a wide range of scientific problems and for applications in materials science and technology. Affiliations:
Jarząbek D.M. | - | IPPT PAN | Kaufmann A.N. | - | Paul Scherrer Institut (CH) | Schift H. | - | Paul Scherrer Institut (CH) | Rymuza Z. | - | other affiliation | Jung T.A. | - | Paul Scherrer Institut (CH) |
| 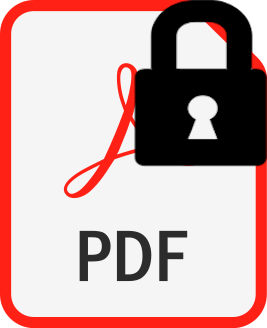 |
3. |
Atasoy H.♦, Vogler M.♦, Haatainen T.♦, Schleunitz A.♦, Jarząbek D.M.♦, Schift H.♦, Reuther F.♦, Gruetzner G.♦, Rymuza Z.♦, Novel thermoplastic polymers with improved release properties for thermal NIL,
MICROELECTRONIC ENGINEERING, ISSN: 0167-9317, DOI: 10.1016/j.mee.2011.01.080, Vol.88, pp.1902-1905, 2011 Abstract: In the nanoimprint lithography (NIL) process the mould release is a limiting step. Regardless of the carefully designed special properties a resist may have, it has to come over this challenging process step to be employed in a NIL process. Generally, the moulds are coated with anti-sticking layers. Here, an alternative solution is developed by modification of two well established NIL polymers through integration of fluorinated additives in their formulation. An effective additive concentration window was successfully defined, in which the substrate adhesion and imprint behaviour is not influenced. Defect-free patterning down to 30 nm is possible. A release force reduction of about 40% was observed with the modified polymer mr-I 7000R compared to the unmodified original Keywords: NIL polymers, Fluorinated additives, Release forces Affiliations:
Atasoy H. | - | other affiliation | Vogler M. | - | other affiliation | Haatainen T. | - | other affiliation | Schleunitz A. | - | other affiliation | Jarząbek D.M. | - | other affiliation | Schift H. | - | Paul Scherrer Institut (CH) | Reuther F. | - | other affiliation | Gruetzner G. | - | other affiliation | Rymuza Z. | - | other affiliation |
| 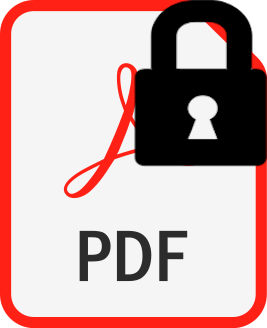 |
4. |
Jarząbek D.M.♦, Rymuza Z.♦, Horiba A.♦, Hirai Y.♦, Development of an experimental technique for testing rheological properties of ultrathin polymer films used in nanoimprint lithography,
JOURNAL OF VACUUM SCIENCE AND TECHNOLOGY B, ISSN: 1071-1023, DOI: 10.1116/1.3656377, Vol.29, No.6, pp.061603-1-6, 2011 Abstract: A new method for the measurement of rheological properties (complex viscosity, viscosity and elasticity) of thin polymeric films is presented. The probe, which is placed on the end of an arm of a mini tuning fork, is caused to oscillate and then is put into poly(methyl methacrylate) films, whose thickness ranges from 30 nm to 1080 nm. All measured properties depend on temperature, thickness of the films, indentation depth and the molecular weight of PMMA. Complex viscosity, viscosity and elasticity are found to be lower at higher temperatures and higher with greater molecular weight. They are also lower for thicker films. The results gained from this experiment may be useful in the development of nanoimprint lithography and many other branches of nanotechnology. Furthermore, the method allows for the measurement of the rheological properties of many different thin films (nanoimprint polymers, oils, lubricants) at different temperatures Affiliations:
Jarząbek D.M. | - | other affiliation | Rymuza Z. | - | other affiliation | Horiba A. | - | other affiliation | Hirai Y. | - | other affiliation |
| 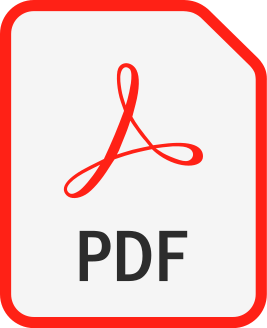 |
5. |
Balabanava N.♦, Wierzbicki R.♦, Zielecka M.♦, Rymuza Z.♦, Effect of roughness on adhesion of polymeric coatings used for microgrippers,
MICROELECTRONIC ENGINEERING, ISSN: 0167-9317, DOI: 10.1016/j.mee.2007.01.183, Vol.84, pp.1227-1230, 2007 Abstract: The purpose of the work was to examine the influence of topography and materials parameters on the value of pull-off force (adhesion) with future application of obtained results to solve the adhesion problem in microhandling. The research consists of two parts: theoretical and experimental. In theoretical research the model of contact, which takes into account the roughness of the contacted bodies is presented. In experimental part polymeric films with low surface energy were investigated as a solution to decrease adhesion at the gripping surface of the micromanipulator. To introduce surface roughness into the solution of polymers the nanoball structures (nanoparticles) were mixed. In result of these modifications three polymer samples were made: with density of nanoballs in the volume 2%, 5% and 10%. In result of these studies the dependences concerning the influence of the roughness on the adhesion were obtained. Keywords: Adhesion, Microgripper, Roughness, Polymer coatings Affiliations:
Balabanava N. | - | other affiliation | Wierzbicki R. | - | other affiliation | Zielecka M. | - | other affiliation | Rymuza Z. | - | other affiliation |
| 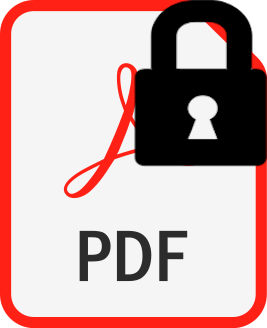 |
6. |
Balabanava N.♦, Wierzbicki R.♦, Heerlein H.♦, Zielecka M.♦, Rymuza Z.♦, Low surface energy films for microgripping applications,
MICROELECTRONIC ENGINEERING, ISSN: 0167-9317, DOI: 10.1016/j.mee.2006.01.061, Vol.83, pp.1389-1392, 2006 Abstract: Polymeric films with low surface energy were investigated as a solution to decrease adhesion at the gripping surface of the micromanipulator. Eight polymeric films were investigated. The polymeric films were tested by an AFM (with standard silicon cantilever in normal environmental conditions) and by a triboscope under controlled conditions with varied substrate temperature. From this number of polymers, three of them: methylsilicone resin and methylphenylsilicone – all in aromatic hydrocarbon solution, were selected to coat the grippers due to their very low roughness (35–55 nm). One of samples was selected as an example of a polymer with a catalyst. The grippers were coated by dipping the working arms (single-crystal silicon) to the solution of polymer and then dried on the heater or in the environment conditions correspondingly. Several gripping experiments were performed to test the functionality of the coatings. Different objects – algae shells (∼250 μm) and silicon parts (5–100 μm) – were manipulated with uncoated and coated grippers. Influence of the polymer coating on the stiction effect was tested. Keywords: Adhesion, Microgripping, Polymer coatings Affiliations:
Balabanava N. | - | other affiliation | Wierzbicki R. | - | other affiliation | Heerlein H. | - | NASCATEC GmbH (DE) | Zielecka M. | - | other affiliation | Rymuza Z. | - | other affiliation |
| 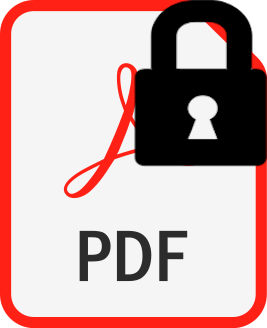 |