1. |
Jenczyk P., Michałowski M.♦, Warcholiński B.♦, Milczarek M., Gilewicz A.♦, Tribology of ZrC Coatings and Spherical Tips Acquired with Extraordinarily Stiff, Metal Atomic Force Microscopy Probes,
Advanced Engineering Materials, ISSN: 1438-1656, DOI: 10.1002/adem.202500243, No.2500243, pp.1-11, 2025 Abstract: Friction and wear are among the most crucial limiting factors for micro-electro-mechanical systems reliability. In this article, it introduces a novel approach to microtribological research by developing ultrastiff atomic force microscopy (AFM) probes capable of applying millinewton-range normal loads. This innovation enables friction measurements in operational ranges relevant to microbearings, overcoming limitations of conventional AFM probes. This article investigates the tribological performance of zirconium carbide (ZrC) coatings, fabricated via physical vapor deposition sputtering, in combination with various microspherical counterfaces. Its findings reveal that ZrC coatings with high carbon content exhibit coefficient of friction as low as 0.08 when paired with borosilicate glass. Additionally, it provides insights into wear behavior, advancing the selection of tribo-pairs for next-generation microbearings. Affiliations:
Jenczyk P. | - | IPPT PAN | Michałowski M. | - | Warsaw University of Technology (PL) | Warcholiński B. | - | other affiliation | Milczarek M. | - | IPPT PAN | Gilewicz A. | - | other affiliation |
| 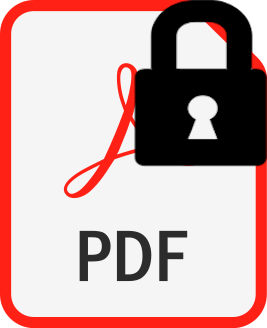 |
2. |
Jarząbek D. M., Włoczewski M.♦, Milczarek M., Jenczyk P., Takesue N.♦, Golasiński K.♦, Pieczyska E. A., Deformation Mechanisms of (100) and (110) Single-Crystal BCC Gum Metal Studied by Nanoindentation and Micropillar Compression,
METALLURGICAL AND MATERIALS TRANSACTIONS A-PHYSICAL METALLURGY AND MATERIALS SCIENCE, ISSN: 1073-5623, DOI: 10.1007/s11661-024-07605-3, pp.1-11, 2024 Abstract: In this paper, small-scale testing techniques—nanoindentation and micropillar compression—were used to investigate the deformation mechanisms, size effects, and strain rate sensitivity of (100) and (110) single-crystal Gum Metal at the micro/nanoscale. It was observed that the (100) orientation exhibits a significant size effect, resulting in hardness values ranging from 1 to 5 GPa. Conversely, for the (110) orientation, this effect was weaker. Furthermore, the yield strength obtained from the micropillar compression tests was approximately 740 MPa for the (100) orientation and 650 MPa for the (110) orientation. The observed deformations were consistent with the established features of the deformation behavior of body-centered cubic (bcc) alloys: significant strain rate sensitivity with no depth dependence, pile-up patterns comparable to those reported in the literature, and shear along the {112}<111> slip directions. However, the investigated material also exhibited Gum Metal-like high ductility, a relatively low modulus of elasticity, and high yield strength, which distinguishes it from classic bcc alloys. Affiliations:
Jarząbek D. M. | - | IPPT PAN | Włoczewski M. | - | other affiliation | Milczarek M. | - | IPPT PAN | Jenczyk P. | - | IPPT PAN | Takesue N. | - | Fukuoka University (JP) | Golasiński K. | - | other affiliation | Pieczyska E. A. | - | IPPT PAN |
| 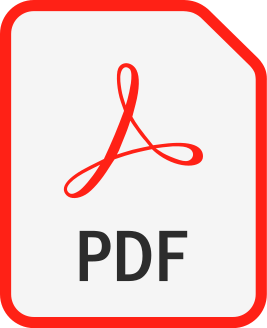 |
3. |
Milczarek M., Jarząbek D., Jenczyk P., Bochenek K., Filipiak M.♦, Novel paradigm in AFM probe fabrication: Broadened range of stiffness, materials, and tip shapes,
TRIBOLOGY INTERNATIONAL, ISSN: 0301-679X, DOI: 10.1016/j.triboint.2023.108308, Vol.180, No.108308, pp.1-12, 2023 Abstract: Atomic force microscopes could be used in wide range of nanotribology experiments but probes available on the market are only made of silicon or silicon nitride with a stiffness in the range of 0.01–100 N/m, which significantly limits the possible research. We strive to solve this problem by designing all-metal probes. The proposed fabrication method is characterised by the use of a copper substrate and electrodeposition in a mould prepared by indentation and photolithography. Prototype probes fabricated with this method were made of nickel with a stiffness of 20 N/m and 2800 N/m and were used for topography and friction measurements. Both the method and all-metal probes showed flexibility and great potential, especially in the field of nano/microtribology. Keywords: Atomic force microscopy, Microfabrication, Cantilever, Metal probe, Friction, Nanotribology Affiliations:
Milczarek M. | - | IPPT PAN | Jarząbek D. | - | IPPT PAN | Jenczyk P. | - | IPPT PAN | Bochenek K. | - | IPPT PAN | Filipiak M. | - | other affiliation |
| 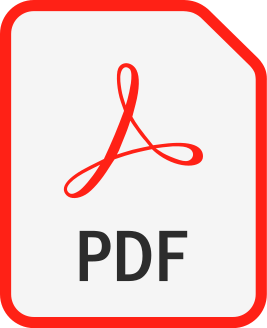 |
4. |
Alvi S.♦, Milczarek M., Jarząbek D.M., Hedman D.♦, Kohan M.G.♦, Levintant-Zayonts N., Vomiero A.♦, Akhtar F.♦, Enhanced mechanical, thermal and electrical properties of high-entropy HfMoNbTaTiVWZr thin film metallic glass and its nitrides,
Advanced Engineering Materials, ISSN: 1438-1656, DOI: 10.1002/adem.202101626, pp.2101626-1-10, 2022 Abstract: The inception of high-entropy alloy promises to push the boundaries for new alloy design with unprecedented properties. This work reports entropy stabilisation of an octonary refractory, HfMoNbTaTiVWZr, high-entropy thin film metallic glass, and derived nitride films. The thin film metallic glass exhibited exceptional ductility of ≈60% strain without fracture and compression strength of 3 GPa in micro-compression, due to the presence of high density and strength of bonds. The thin film metallic glass shows thermal stability up to 750 °C and resistance to Ar-ion irradiation. Nitriding during film deposition of HfMoNbTaTiVWZr thin film of strong nitride forming refractory elements results in deposition of nanocrystalline nitride films with compressive strength, hardness, and thermal stability of up to 10 GPa, 18.7 GPa, and 950 °C, respectively. The high amount of lattice distortion in the nitride films leads to its insulating behaviour with electrical conductivity as low as 200 S cm−1 in the as-deposited film. The design and exceptional properties of the thin film metallic glass and derived nitride films may open up new avenues of development of bulk metallic glasses and the application of refractory-based high entropy thin films in structural and functional applications. Affiliations:
Alvi S. | - | Luleå University of Technology (SE) | Milczarek M. | - | IPPT PAN | Jarząbek D.M. | - | IPPT PAN | Hedman D. | - | Luleå University of Technology (SE) | Kohan M.G. | - | Luleå University of Technology (SE) | Levintant-Zayonts N. | - | IPPT PAN | Vomiero A. | - | Luleå University of Technology (SE) | Akhtar F. | - | Luleå University of Technology (SE) |
| 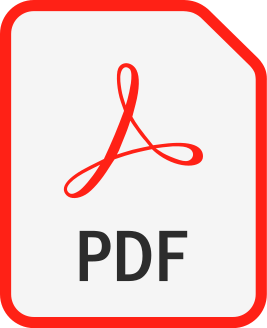 |
5. |
Grzywacz H., Jenczyk P., Milczarek M., Michałowski M.♦, Jarząbek D.M., Burger model as the best option for modeling of viscoelastic behavior of resists for nanoimprint lithography,
Materials, ISSN: 1996-1944, DOI: 10.3390/ma14216639, Vol.14, No.21, pp.6639-1-12, 2021 Abstract: In this study, Atomic Force Microscopy-based nanoindentation (AFM-NI) with diamond-like carbon (DLC) coated tip was used to analyze the mechanical response of poly(methyl methacrylate) (PMMA) thin films (thicknesses: 235 and 513 nm) on a silicon substrate. Then, Oliver and Pharr (OP) model was used to calculate hardness and Young’s modulus, while three different Static Linear Solid models were used to fit the creep curve and measure creep compliance, Young’s modulus, and viscosity. Values were compared with each other, and the best-suited method was suggested. The impact of four temperatures below the glass transition temperature and varied indentation depth on the mechanical properties has been analyzed. The results show high sensitivity on experiment parameters and there is a clear difference between thin and thick film. According to the requirements in the nanoimprint lithography (NIL), the ratio of hardness at demolding temperature to viscosity at molding temperature was introduced as a simple parameter for prediction of resist suitability for NIL. Finally, thinner PMMA film was tentatively attributed as more suitable for NIL. Keywords: PMMA, atomic force microscopy-based nanoindentation, Young’s modulus, hardness, viscosity, Burger creep model, nanoimprint lithography Affiliations:
Grzywacz H. | - | IPPT PAN | Jenczyk P. | - | IPPT PAN | Milczarek M. | - | IPPT PAN | Michałowski M. | - | Warsaw University of Technology (PL) | Jarząbek D.M. | - | IPPT PAN |
| 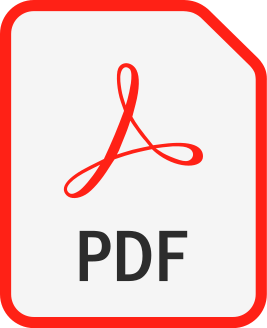 |
6. |
Psiuk R., Milczarek M., Jenczyk P., Denis P., Jarząbek D., Bazarnik P.♦, Pisarek M.♦, Mościcki T., Improved mechanical properties of W-Zr-B coatings deposited by hybrid RF magnetron – PLD method,
APPLIED SURFACE SCIENCE, ISSN: 0169-4332, DOI: 10.1016/j.apsusc.2021.151239, Vol.570, pp.151239-1-11, 2021 Abstract: In this work, novel W-Zr-B coatings were developed by a hybrid process combining pulsed laser deposited ZrB2 and radio frequency magnetron sputtered W2B5. The influence of the laser power density on the structure and mechanical properties of the deposited films was studied. Addition of zirconium causes a change in the structure of the deposited films from columnar to mainly amorphous. The nanoindentation tests and compression of nanopillars showed that doped W-Zr-B layers are still super-hard and incompressible in comparison to WB2 films without doping, but they change their behaviour from brittle to ductile. Films obtained with a fluence of 1.06 J/cm2 are superhard (H = 40 ± 4 GPa) and incompressible (12 ± 1 GPa), but possess a relatively low Young’s modulus (E = 330 ± 32 GPa) and a high elastic recovery (We = 0.9). Further increase in the fluence causes films to consist of deeply embedded fragments of laser ablated ZrB2 target in the deposited layer. Taking into account that the particles are made of ZrB2 which possess extraordinary thermal properties, and the matrix is made of W-Zr-B, a super-hard material, such a composite can also be interesting for industrial applications. Keywords: superhard tungsten borides, hybrid magnetron sputtering – pulsed laser deposition, nanopillar compression Affiliations:
Psiuk R. | - | IPPT PAN | Milczarek M. | - | IPPT PAN | Jenczyk P. | - | IPPT PAN | Denis P. | - | IPPT PAN | Jarząbek D. | - | IPPT PAN | Bazarnik P. | - | Warsaw University of Technology (PL) | Pisarek M. | - | Institute of Physical Chemistry, Polish Academy of Sciences (PL) | Mościcki T. | - | IPPT PAN |
| 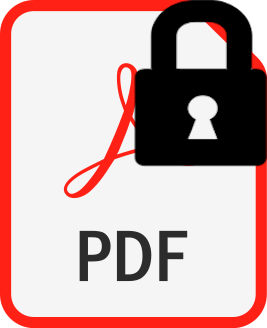 |
7. |
Jenczyk P., Grzywacz H., Milczarek M., Jarząbek D.M.♦, Mechanical and tribological properties of co-electrodeposited particulate-reinforced metal matrix composites: a critical review with interfacial aspects,
Materials, ISSN: 1996-1944, DOI: 10.3390/ma14123181, Vol.14, No.12, pp.3181-1-36, 2021 Abstract: Particulate-reinforced metal matrix composites (PRMMCs) with excellent tribo-mechanical properties are important engineering materials and have attracted constant scientific interest over the years. Among the various fabrication methods used, co-electrodeposition (CED) is valued due to its efficiency, accuracy, and affordability. However, the way this easy-to-perform process is carried out is inconsistent, with researchers using different methods for volume fraction measurement and tribo-mechanical testing, as well as failing to carry out proper interface characterization. The main contribution of this work lies in its determination of the gaps in the tribo-mechanical research of CED PRMMCs. For mechanical properties, hardness is described with respect to measurement methods, models, and experiments concerning CED PRMMCs. The tribology of such composites is described, taking into account the reinforcement volume fraction, size, and composite fabrication route (direct/pulsed current). Interfacial aspects are discussed using experimental direct strength measurements. Each part includes a critical overview, and future prospects are anticipated. This review paper provides an overview of the tribo-mechanical parameters of Ni-based co-electrodeposited particulate-reinforced metal matrix composite coatings with an interfacial viewpoint and a focus on hardness, wear, and friction behavior. Keywords: experimental mechanics, tribology, co-electrodeposited composites Affiliations:
Jenczyk P. | - | IPPT PAN | Grzywacz H. | - | IPPT PAN | Milczarek M. | - | IPPT PAN | Jarząbek D.M. | - | other affiliation |
| 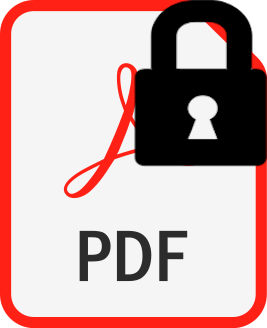 |
8. |
Grzywacz H.♦, Milczarek M., Jenczyk P., Dera W., Michałowski M.♦, Jarząbek D.M.♦, Quantitative measurement of nanofriction between PMMA thin films and various AFM probes,
MEASUREMENT, ISSN: 0263-2241, DOI: 10.1016/j.measurement.2020.108267, Vol.168, pp.108267-1-13, 2020 Abstract: This study reports the quantitative, precise and accurate results of nanoscale friction measurements with the use of an Atomic Force Microscope calibrated with a precise nanoforce sensor. For this purpose, three samples of spin-coated thin Polymethylmethacrylate (PMMA) films were prepared with the following thicknesses: 235, 343, and 513 nm. Three different AFM probes were used for the friction measurements: with diamond-like carbon (DLC) tip with a small (15 nm) or big (2 µm) tip radius, and a reference silicon tip with a small (8 nm) radius. The results show that in all of the studied cases, the coefficient of friction strongly depends on the applied load, being much higher for a lower load. Furthermore, a strong relation of the friction force on the cantilever's geometry, the scanning velocity, and the film thickness was observed. Keywords: lateral force microscopy, friction, thin PMMA films, atomic force microscope, DLC coatings, adhesion Affiliations:
Grzywacz H. | - | other affiliation | Milczarek M. | - | IPPT PAN | Jenczyk P. | - | IPPT PAN | Dera W. | - | IPPT PAN | Michałowski M. | - | Warsaw University of Technology (PL) | Jarząbek D.M. | - | other affiliation |
| 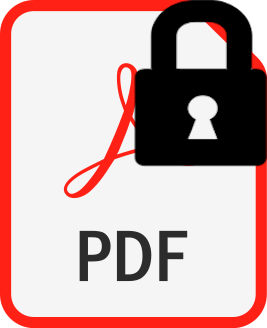 |
9. |
Jarząbek D.M., Milczarek M., Nosewicz S., Bazarnik P.♦, Schift H.♦, Size effects of hardness and strain rate sensitivity in amorphous silicon measured by nanoindentation,
METALLURGICAL AND MATERIALS TRANSACTIONS A-PHYSICAL METALLURGY AND MATERIALS SCIENCE, ISSN: 1073-5623, DOI: 10.1007/s11661-020-05648-w, Vol.51, No.4, pp.1625-1633, 2020 Abstract: In this work, dynamic mechanical properties of amorphous silicon and scale effects were investigated by the means of nanoindentation. An amorphous silicon sample was prepared by plasma-enhanced chemical vapor deposition (PECVD). Next, two sets of the samples were investigated: as-deposited and annealed in 500 °C for 1 hour. A three-sided pyramidal diamond Berkovich's indenter was used for the nanoindentation tests. In order to determine the strain rate sensitivity (SRS), indentations with different loading rates were performed: 0.1, 1, 10, 100 mN/min. Size effects were studied by application of maximum indentation loads in the range from 1 up to 5 mN (penetrating up to approximately one-third of the amorphous layer). The value of hardness was determined by the Oliver-Pharr method. An increase of hardness with decrease of the indentation depth was observed for both samples. Furthermore, the significant dependence of hardness on the strain rate has been reported. Finally, for the annealed samples at low strain rates a characteristic "elbow" during unloading was observed on the force-indentation depth curves. It could be attributed to the transformation of (β-Sn)-Si to the PI (pressure-induced) a-Si end phase. Affiliations:
Jarząbek D.M. | - | IPPT PAN | Milczarek M. | - | IPPT PAN | Nosewicz S. | - | IPPT PAN | Bazarnik P. | - | Warsaw University of Technology (PL) | Schift H. | - | Paul Scherrer Institut (CH) |
| 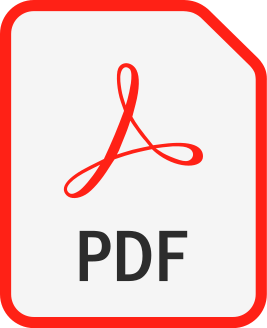 |
10. |
Jarząbek D.M., Milczarek M.♦, Wojciechowski T.♦, Dziekoński C., Chmielewski M.♦, The effect of metal coatings on the interfacial bonding strength of ceramics to copper in sintered Cu-SiC composites,
CERAMICS INTERNATIONAL, ISSN: 0272-8842, DOI: 10.1016/j.ceramint.2017.01.056, Vol.43, No.6, pp.5283-5291, 2017 Abstract: Cu-SiC composites are very promising materials which have high thermal and electrical conductivity and may find many applications. Unfortunately, the main disadvantage of these materials is the dissolution of silicon in copper at elevated temperature, which significantly reduces their properties. In order to overcome this problem particles can be coated with a protective material before sintering. In this paper– the influence of three different metallic coatings on bonding strength were investigated. SiC particles were coated with tungsten, chromium or titanium. As reference a material with uncoated particles was prepared. The experiments were carried out with the use of microtensile tester. The highest increase in strength was observed in the case of chromium coating. On the other hand, the titanium coating, which was of very poor quality, decrease the bonding strength in comparison with uncoated particles. Furthermore, scanning electron and optical microscopes were used to determine the mechanism of debonding. Keywords: interfacial bonding strength, metal matrix composites, tensile strength, silicon carbide particles Affiliations:
Jarząbek D.M. | - | IPPT PAN | Milczarek M. | - | other affiliation | Wojciechowski T. | - | Institute of Physics, Polish Academy of Sciences (PL) | Dziekoński C. | - | IPPT PAN | Chmielewski M. | - | Institute of Electronic Materials Technology (PL) |
| 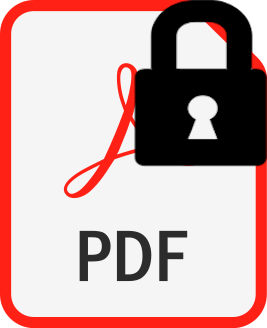 |