1. |
Staszczak M., Nabavian Kalat M., Golasiński K.M., Urbański L., Takeda K.♦, Matsui R.♦, Pieczyska E.A., Characterization of Polyurethane Shape Memory Polymer and Determination of Shape Fixity and Shape Recovery in Subsequent Thermomechanical Cycles,
Polymers, ISSN: 2073-4360, DOI: 10.3390/polym14214775, Vol.14, No.4775, pp.1-19, 2022 Abstract: Multifunctional polyurethane shape memory polymers (PU-SMPs) have been of increasing interest in various applications. Here we report structure characterization, detailed methodology, and obtained results on the identification of functional properties of a thermoset PU-SMP (MP4510) with glass transition temperature of 45 C. The stable, chemically crosslinked network of this thermoset PU-SMP results in excellent shape memory behavior. Moreover, the proximity of the activation temperature range of this smart polymer to room and body temperature enables the PU-SMP to be used in more critical industrial applications, namely fast-response actuators. The thermomechanical behavior of a shape memory polymer determines the engineering applications of the material. Therefore, investigation of the shape memory behavior of this class of commercial PU-SMP is of particular importance. The conducted structural characterization confirms its shape memory properties. The shape fixity and shape recovery properties were determined by a modified experimental approach, considering the polymer’s sensitivity to external conditions, i.e., the temperature and humidity variations. Three thermomechanical cycles were considered and the methodology used is described in detail. The obtained shape fixity ratio of the PU-SMP was approximately 98% and did not change significantly in the subsequent cycles of the thermomechanical loading due to the stability of chemical crosslinks in the thermoset materials structure. The shape recovery was found to be approximately 90% in the first cycle and reached a value higher than 99% in the third cycle. The results confirm the effect of the thermomechanical training on the improvement of the PU-SMP shape recovery after the first thermomechanical cycle as well as the effect of thermoset material stability on the repeatability of the shape memory parameters quantities. Keywords: polyurethane shape memory polymer, thermomechanical loading program, shape fixity, shape recovery Affiliations:
Staszczak M. | - | IPPT PAN | Nabavian Kalat M. | - | IPPT PAN | Golasiński K.M. | - | IPPT PAN | Urbański L. | - | IPPT PAN | Takeda K. | - | Aichi Institute of Technology (JP) | Matsui R. | - | Aichi Institute of Technology (JP) | Pieczyska E.A. | - | IPPT PAN |
| 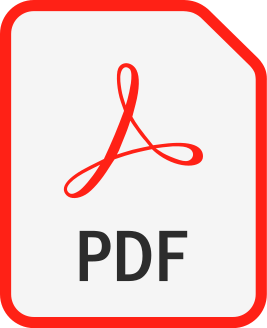 |
2. |
Matsui R.♦, Takeda K.♦, Tobushi H.♦, Pieczyska E.A., Mechanical properties and advanced subjects in shape memory alloys and polymers,
JOURNAL OF THEORETICAL AND APPLIED MECHANICS, ISSN: 1429-2955, DOI: 10.15632/jtam-pl.56.2.447, Vol.56, No.2, pp.447-456, 2018 Abstract: Advanced subjects in mechanical properties of shape memory alloys and polymers are discussed. In the subloop loading under a stress-controlled condition of the shape memory alloy, the transformation-induced stress relaxation appears due to variation in temperature. The enhancement of corrosion and corrosion fatigue life of the shape memory alloy is discussed. The development of a functionally-graded shape memory alloy and polymer is expected to obtain better performance. Three-way motion appears in the shape memory composite with the shape memory alloy and polymer. Keywords: shape memory alloy, shape memory polymer, functionally-graded shape memory material, shape memory composite Affiliations:
Matsui R. | - | Aichi Institute of Technology (JP) | Takeda K. | - | Aichi Institute of Technology (JP) | Tobushi H. | - | Aichi Institute of Technology (JP) | Pieczyska E.A. | - | IPPT PAN |
| 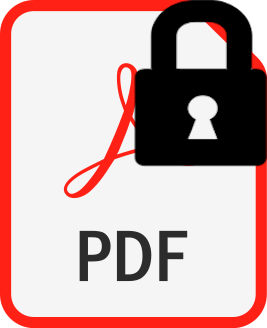 |
3. |
Takeda K.♦, Matsui R.♦, Tobushi H.♦, Pieczyska E.A., Torsional deformation properties of SMA tapes and their application to bias-type reciprocating rotary driving actuator,
ARCHIVES OF MECHANICS, ISSN: 0373-2029, Vol.69, No.4-5, pp.289-303, 2017 Abstract: In order to develop the reciprocating rotary driving actuator with a simple mechanism using shape memory alloy (SMA) tapes, the graphical method to design the actuator was proposed based on the torsional deformation properties of SMA tapes. The torsional deformation properties of the SME tape showing the shape memory effect (SME) and the SE tape showing superelasticity (SE) were obtained. The bias-type reciprocating rotary actuator was composed of the pretwisted SME tape and the flat SE tape in series. The design chart expressed by the relationship between torque and twisting angle of the SME tape and the SE tape was proposed. The rotational angle and torque, which vary depending on temperature, can be estimated based on the design chart. The rotational angle is controlled by adjusting the mounting angle of the SME tape and the heating temperature. The automatically opening and closing blind driven by sunlight was demonstrated. The blind was controlled by using the reciprocating rotary element composed of the SME tape and the SE tape. The behavior of the blind can be achieved based on the proposed design method of the reciprocating rotary driving element Keywords: shape memory alloy, tape, torsion, actuator, reciprocating rotation, design chart, bias-type Affiliations:
Takeda K. | - | Aichi Institute of Technology (JP) | Matsui R. | - | Aichi Institute of Technology (JP) | Tobushi H. | - | Aichi Institute of Technology (JP) | Pieczyska E.A. | - | IPPT PAN |
| 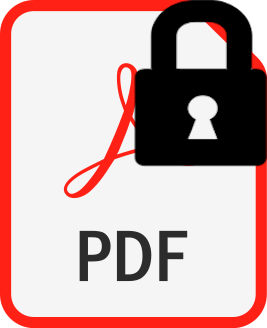 |
4. |
Takeda K.♦, Matsui R.♦, Tobushi H.♦, Homma S.♦, Levintant-Zayonts N., Kucharski S., Enhancement of bending fatigue life in TiNi shape-memory alloy tape by nitrogen ion implantation,
ARCHIVES OF MECHANICS, ISSN: 0373-2029, Vol.67, No.4, pp.293-310, 2015 Abstract: A shape-memory alloy (SMA) is expected to be applied as intelligent or smart material since it shows the functional characteristics of the shape memory effect and superelasticity. Most SMA elements, with these characteristics, perform cyclic motions. In these cases, the fatigue property of SMA is one of the most important issues in view of evaluating functional characteristics of SMA elements. The fatigue properties are complex since they depend on stress, strain, temperature and their hysteresis. If an SMA is implanted with high-energy ions, the thermomechanical properties of the material may change, resulting in long fatigue life. In the present study, the nitrogen ion implantation was applied to modify the surface of a TiNi SMA tape and the influence of implantation treatment on the bending fatigue properties was investigated. Keywords: shape-memory alloy, titanium-nickel alloy, superelasticity, nitrogen ion implantation, fatigue, bending Affiliations:
Takeda K. | - | Aichi Institute of Technology (JP) | Matsui R. | - | Aichi Institute of Technology (JP) | Tobushi H. | - | Aichi Institute of Technology (JP) | Homma S. | - | Nippon Trex Co. (JP) | Levintant-Zayonts N. | - | IPPT PAN | Kucharski S. | - | IPPT PAN |
| 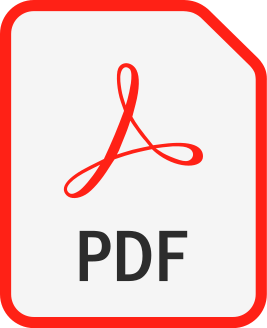 |
5. |
Takeda K.♦, Matsui R.♦, Tobushi H.♦, Pieczyska E.A., Transformation-Induced Relaxation and Stress Recovery of TiNi Shape Memory Alloy,
Materials, ISSN: 1996-1944, DOI: 10.3390/ma7031912, Vol.7, pp.1912-1926, 2014 Abstract: The transformation-induced stress relaxation and stress recovery of TiNi shape memory alloy (SMA) in stress-controlled subloop loading were investigated based on the local variation in temperature and transformation band on the surface of the tape in the tension test. The results obtained are summarized as follows. (1) In the loading process, temperature increases due to the exothermic martensitic transformation (MT) until the holding strain and thereafter temperature decreases while holding the strain constant, resulting in stress relaxation due to the MT; (2) In the unloading process, temperature decreases due to the endothermic reverse transformation until the holding strain and thereafter temperature increases while holding the strain constant, resulting in stress recovery due to the reverse transformation; (3) Stress varies markedly in the initial stage followed by gradual change while holding the strain constant; (4) If the stress rate is high until the holding strain in the loading and unloading processes, both stress relaxation and stress recovery are large; (5) It is important to take into account this behavior in the design of SMA elements, since the force of SMA elements varies even if the atmospheric temperature is kept constant. Keywords: shape memory alloy, superelasticity, titanium-nickel alloy, subloop, stress relaxation, stress recovery, martensitic transformation Affiliations:
Takeda K. | - | Aichi Institute of Technology (JP) | Matsui R. | - | Aichi Institute of Technology (JP) | Tobushi H. | - | Aichi Institute of Technology (JP) | Pieczyska E.A. | - | IPPT PAN |
| 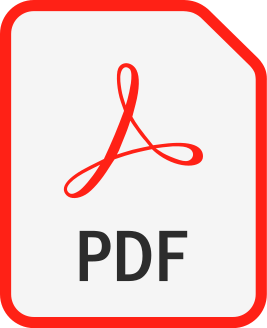 |
6. |
Pieczyska E.A., Staszczak M., Dunić V.♦, Slavković R.♦, Tobushi H.♦, Takeda K.♦, Development of Stress-Induced Martensitic Transformation in TiNi Shape Memory Alloy,
Journal of Materials Engineering and Performance, ISSN: 1059-9495, DOI: 10.1007/s11665-014-0959-y, Vol.23, No.7, pp.2505-2514, 2014 Abstract: TiNi shape memory alloy (SMA) was subjected to tension at strain-controlled test on quasistatic testing machine. The nucleation, development, and saturation of the stress-induced martensitic transformation were investigated, taking into account the obtained dependency of mechanical parameters and the specimen temperature changes measured by an infrared camera (IR). Three kinds of data obtained by the IR system were analyzed: the temperature distribution on the SMA sample surface, the temperature changes derived as average from the chosen sample area, and the temperature profiles obtained along the sample length. The temperature distribution shows nucleation of the transformation process and a creation of the transformation bands. The average temperature reflects the effects of thermomechanical coupling, accompanying exothermic martensitic forward and endothermic reverse transformation. The temperature profiles revealed the temperature difference between the band and the rest of the sample. The experimental results were supported with finite element method numerical analysis (FEM). The FEM software components for structural and heat transfer problems, coupled in partitioned approach, were used for thermomechanical analysis. Keywords: finite element modeling, infrared camera, material testing, martensitic transformation, TiNi shape memory alloy, tension, thermomechanical couplings Affiliations:
Pieczyska E.A. | - | IPPT PAN | Staszczak M. | - | IPPT PAN | Dunić V. | - | University of Kragujevac (XS) | Slavković R. | - | University of Kragujevac (XS) | Tobushi H. | - | Aichi Institute of Technology (JP) | Takeda K. | - | Aichi Institute of Technology (JP) |
| 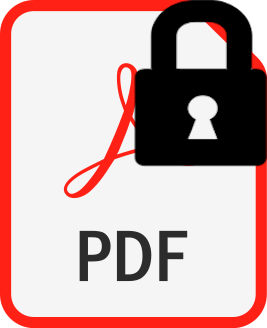 |
7. |
Takeda K.♦, Mitsui K.♦, Tobushi H.♦, Levintant-Zayonts N., Kucharski S., Influence of nitrogen ion implantation on deformation and fatigue properties of TiNi shape memory alloy wire,
ARCHIVES OF MECHANICS, ISSN: 0373-2029, Vol.65, No.5, pp.391-405, 2013 Abstract: A shape memory alloy (SMA) is expected to be applied as intelligent material since it shows the unique characteristics of the shape memory effect and superelasticity. Most SMA elements, with these characteristics, perform cyclic motions. In these cases, fatigue of SMA is one of the important properties in view of evaluating functional characteristics. The fatigue properties are complex since they depend on stress, strain, temperature and time. If SMA is implanted by high energy ions, the thermomechanical properties may change, resulting in long fatigue life. In the present study, the nitrogen ion implantation was applied to modify TiNi SMA wire surface and the influence of implantation treatment on the tensile deformation and bending fatigue properties was investigated. Keywords: shape memory effect, titanium-nickel alloy, nitrogen ion implantation, superelasticity, fatigue Affiliations:
Takeda K. | - | Aichi Institute of Technology (JP) | Mitsui K. | - | Masupuro Denkoh Corp. (JP) | Tobushi H. | - | Aichi Institute of Technology (JP) | Levintant-Zayonts N. | - | IPPT PAN | Kucharski S. | - | IPPT PAN |
| 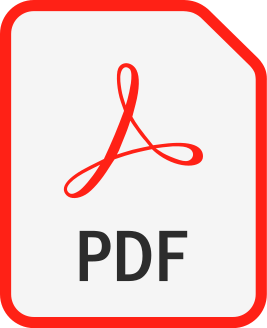 |
8. |
Takeda K.♦, Matsui R.♦, Tobushi H.♦, Pieczyska E.A., Creep and creep recovery under stress-controlled subloop loading in TiNi shape memory alloy,
ARCHIVES OF MECHANICS, ISSN: 0373-2029, Vol.65, No.5, pp.429-444, 2013 Abstract: If a shape memory alloy (SMA) is subjected to the subloop loading under the stress-controlled condition, creep and creep recovery can appear based on the martensitic transformation. In the design of SMA elements, these deformation properties are important since the deflection of SMA elements can change under constant load. The conditions for the progress of the martensitic transformation are discussed based on the kinetics of the martensitic transformation for the SMA. The creep deformation properties are investigated experimentally for TiNi SMA. The creep strain rate increases in proportion to the martensitic transformation strain; the creep recovery strain rate increases in proportion to the reverse transformation strain. Keywords: shape memory alloy, superelasticity, subloop, transformation band, creep, creep recovery, strain rate, local deformation Affiliations:
Takeda K. | - | Aichi Institute of Technology (JP) | Matsui R. | - | Aichi Institute of Technology (JP) | Tobushi H. | - | Aichi Institute of Technology (JP) | Pieczyska E.A. | - | IPPT PAN |
| 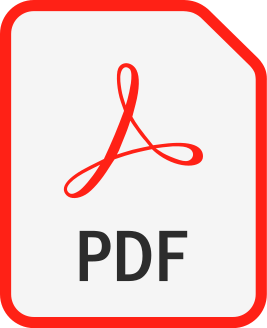 |
9. |
Pieczyska E.A., Tobushi H.♦, Kulasiński K., Takeda K.♦, Impact of Strain Rate on Thermomechanical Coupling Effects in TiNi SMA Subjected to Compression,
MATERIALS TRANSACTIONS, ISSN: 1345-9678, DOI: 10.2320/matertrans.M2012212, Vol.53, No.11, pp.1905-1909, 2012 Abstract: In this study, the thermomechanical coupling effects accompanying stress-induced martensitic transformation in TiNi shape memory alloy subjected to compression test were investigated. The mechanical characteristics were elaborated and the temperature changes related to the exothermic martensitic forward transformation and the endothermic reverse one were measured in a contactless manner by a fast and sensitive infrared camera. The obtained temperature changes of the specimen depend on the strain rate applied. At higher strain rate, greater temperature changes were observed, because the heat flow to the surroundings was lower and the process was closer to adiabatic conditions. The temperature changes of the shape memory alloy significantly influence its stressstrain characteristics. Moreover, the energy dissipated during a compression cycle was calculated for various strain rates. The study revealed that both the loading work and recoverable strain energy increase with increasing strain rate, while the dissipated energy fraction decreases.
Keywords: shape memory alloy, compression test, exothermic/endothermic transformation, infrared camera, energy dissipation Affiliations:
Pieczyska E.A. | - | IPPT PAN | Tobushi H. | - | Aichi Institute of Technology (JP) | Kulasiński K. | - | IPPT PAN | Takeda K. | - | Aichi Institute of Technology (JP) |
| 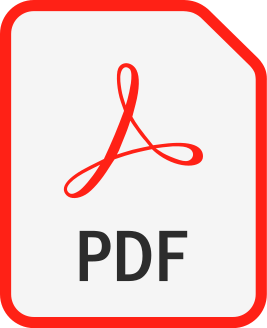 |
10. |
Takeda K.♦, Tobushi H.♦, Miyamoto K.♦, Pieczyska E.A., Superelastic Deformation of TiNi Shape Memory Alloy Subjected to Various Subloop Loadings,
MATERIALS TRANSACTIONS, ISSN: 1345-9678, DOI: 10.2320/matertrans.M2011288, Vol.53, No.1, pp.217-223, 2012 Abstract: This paper investigates the superelastic deformation behaviors of a TiNi shape-memory alloy (SMA) tape subjected to various subloop loadings in relation to local temperature variations and observed surface changes during a tension test. The results obtained are: (1) Upper and lower stress plateaus appear during loading and unloading accompanying the spreading and shrinking of the stress-induced martensitic transformation (SIMT) bands. In the case of unloading from the upper stress plateau under low stress rate, strain increases due to the spreading of the SIMT bands at the start of the unloading. (2) If stress at the upper stress plateau is held constant, creep deformation appears with the spread of the SIMT bands. The volume fraction in the martensitic phase increases in proportion to the increase in strain. (3) Where the strain is made to vary at the stress plateaus during loading or unloading, a return point memory effect can be seen in the reloading stress-strain curve. The spreading or shrinking of the SIMT bands starts from the boundary of the previous SIMT bands remaining from the preceding process. (4) The inclination angle of the SIMT band boundaries to the tensile axis of the tape is 33° for an aspect ratio of 5. The inclination angle is 42° in the center of the tape and 37° in the vicinity of the end secured by the grip, for an aspect ratio of 10.
Keywords: shape memory alloy, superelasticity, titanium-nickel alloy, subloop, transformation band, creep deformation, local deformation Affiliations:
Takeda K. | - | Aichi Institute of Technology (JP) | Tobushi H. | - | Aichi Institute of Technology (JP) | Miyamoto K. | - | Churyo Engineering Co. (JP) | Pieczyska E.A. | - | IPPT PAN |
| 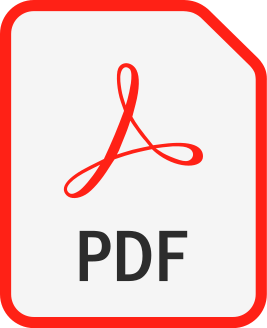 |
11. |
Pieczyska E.A., Tobushi H.♦, Takeda K.♦, Stróż D.♦, Ranachowski Z., Kulasiński K., Kúdela Jr S.♦, Luckner J., Martensite transformation bands studied in TiNi shape memory alloy by infrared and acoustic emission techniques,
KOVOVE MATERIALY-METALLIC MATERIALS, ISSN: 0023-432X, Vol.50, pp.309-318, 2012 Abstract: TiNi shape memory alloy (SMA) specimens have been subjected to tension carried out at various strain rates. The goal was to investigate a nucleation and development of the stressinduced martensitic transformation by infrared (IR) and acoustic emission (AE) techniques. Therefore, both the infrared radiation and acoustic emission data were recorded using a fast infrared camera and acoustic emission set-up, respectively. It has been shown that the initial, macroscopically homogeneous transformation initiates in the elastic stage of the deformation even before the stress-strain curve knee and formation of the localized transformation bands. It has also been found that the homogeneous transformation occurs at similar stress level for all strain rates applied, while the localized martensitic transformation depends on the strain rate. Nucleation and development of the localized transformation bands, detected by the infrared camera, were confirmed by acoustic emission technique. The differences between the IR and AE activities were recorded during the TiNi SMA loading and unloading process, manifesting different dynamics of the stress-induced martensitic forward and reverse transformation. Keywords: shape memory alloy, TiNi, superelasticity, martensitic transformation, tension test, acoustic emission Affiliations:
Pieczyska E.A. | - | IPPT PAN | Tobushi H. | - | Aichi Institute of Technology (JP) | Takeda K. | - | Aichi Institute of Technology (JP) | Stróż D. | - | other affiliation | Ranachowski Z. | - | IPPT PAN | Kulasiński K. | - | IPPT PAN | Kúdela Jr S. | - | Institute of Materials and Machine Mechanics, Slovak Academy of Sciences (SK) | Luckner J. | - | IPPT PAN |
| 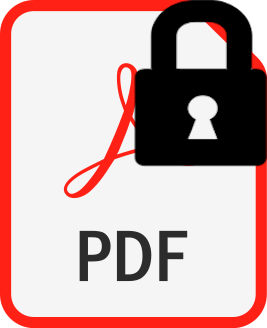 |
12. |
Takeda K.♦, Tobushi H.♦, Pieczyska E.A., Transformation-Induced Creep and Creep Recovery of Shape Memory Alloy,
Materials, Vol.5, pp.909-921, 2012 | 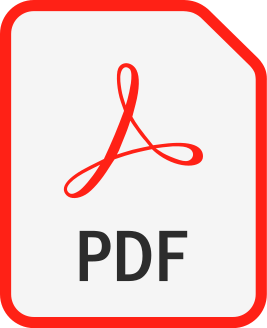 |
13. |
Takeda K.♦, Tobushi H.♦, Miyamoto K.♦, Pieczyska E.A., Subloop Superelastic Deformation of TiNi Shape Memory Alloy,
TRANSACTIONS OF THE JAPAN SOCIETY OF MECHANICAL ENGINEERS Series A , ISSN: 1884-8338, DOI: 10.1299/kikaia.77.1509, Vol.77, No.781, pp.1509-1517, 2011 Abstract: The various subloop behaviors for the superelastic deformation of TiNi shape memory alloy were investigated based on the local temperature variation and the surface observation in the tension test. The results obtained are summarized as bellows. (1) The upper and lower stress plateaus during loading and unloading appear accompanying the progress and reduction of the martensitic transformation (MT) band, respectively. In the case of unloading from the upper stress plateau under low stress rate, strain increases due to the progress of the MT band in the initial stage of unloading. (2) If stress is held constant in the upper stress plateau, creep deformation appears. The creep deformation appears based on the progress of the MT band. The volume fraction of the martensitic phase increases in proportion to an increase in strain. (3) If the transformation strain varies in the stress plateau during loading and unloading, the return point memory appears in the reloading stress-strain curve. The progress and reduction of the MT band start from the boundary of the MT band which has appeared in the preceding process. (4) The angle of boundary of the MT band inclined to the tensile axis is 33° for an aspect ratio of 5 and 42° in the central part of the specimen and 37° in the vicinity of the gripping part for an aspect ratio of 10. Keywords: Shape Memory Alloy, Superelasticity, Titanium-Nickel Alloy, Subloop, Transformation Band, Creep Deformation Affiliations:
Takeda K. | - | Aichi Institute of Technology (JP) | Tobushi H. | - | Aichi Institute of Technology (JP) | Miyamoto K. | - | Churyo Engineering Co. (JP) | Pieczyska E.A. | - | IPPT PAN |
| 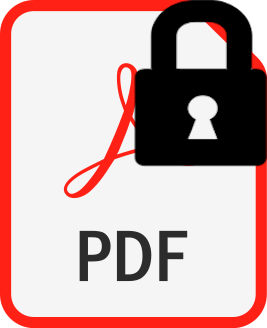 |