1. |
Nabavian Kalat M., Ziai Y., Dziedzic K., Gradys A. D., Urbański L., Zaszczyńska A., Andrés Díaz L.♦, Kowalewski Z. L., Experimental evaluation of build orientation effects on the microstructure, thermal, mechanical, and shape memory properties of SLA 3D-printed epoxy resin,
EUROPEAN POLYMER JOURNAL, ISSN: 0014-3057, DOI: 10.1016/j.eurpolymj.2025.113829, Vol.228, pp.113829-1-18, 2025 Abstract: Additive manufacturing (AM) methods, popularly known as 3D printing technologies, particularly the pioneering laser stereolithography (SLA), have revolutionized the production of complex polymeric components. However, challenges such as anisotropy, resulting from the layer-by-layer construction method, can affect the thermomechanical properties and dimensional stability of 3D-printed objects. Although anisotropy in SLA 3D printing is often overlooked due to the high precision of this technique, its impact on the properties and structural performance of the 3D-printed prototype becomes more significant when printing small devices designed for precise micro-mechanisms. This experimental study investigates the impact of the chosen printing surface – a less explored factor – on the performance of SLA 4D-printed thermo-responsive shape memory epoxy (SMEp) specimens. Two identical dog-bone specimens were printed from two distinct surfaces: edge and flat surface, to examine how variations in surface area and quantity of layers influence the microstructure, thermal behavior, mechanical properties, and shape memory performance. The results of this experimental investigation reveal that specimens printed from the edge, with a higher number of layers and smaller surface area, exhibit superior interlayer bonding, tensile strength, dimensional stability, and shape recovery efficiency compared to those printed from the flat surface. Conversely, specimens with fewer, larger layers demonstrated greater elongation and thermal expansion but reduced structural integrity and shape recovery performance. These results highlight the importance of experimentally investigating how different build orientations affect the properties and performance of SLA 3D-printed materials, especially before designing and employing them in applications demanding high precision and reliability. Keywords: Additive manufacturing, Laser stereolithography, Shape memory polymers, Materials processing, Anisotropy, Printing orientation Affiliations:
Nabavian Kalat M. | - | IPPT PAN | Ziai Y. | - | IPPT PAN | Dziedzic K. | - | IPPT PAN | Gradys A. D. | - | IPPT PAN | Urbański L. | - | IPPT PAN | Zaszczyńska A. | - | IPPT PAN | Andrés Díaz L. | - | other affiliation | Kowalewski Z. L. | - | IPPT PAN |
| 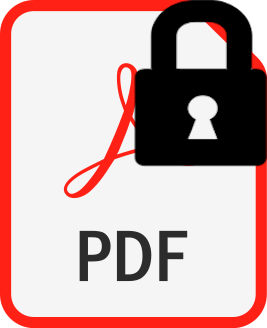 |
2. |
Staszczak M., Urbański L., Gradys A. D., Cristea M.♦, Pieczyska E. A., Nucleation, Development and Healing of Micro-Cracks in Shape Memory Polyurethane Subjected to Subsequent Tension Cycles,
Polymers, ISSN: 2073-4360, DOI: 10.3390/polym16131930, Vol.16, No.13, pp.1-22, 2024 Abstract: Thermoresponsive shape memory polymers (SMPs) have garnered increasing interest for their exceptional ability to retain a temporary shape and recover the original configuration through temperature changes, making them promising in various applications. The SMP shape change and recovery that happen due to a combination of mechanical loading and appropriate temperatures are related to its particular microstructure. The deformation process leads to the formation and growth of micro-cracks in the SMP structure, whereas the subsequent heating over its glass transition temperature Tg leads to the recovery of its original shape and properties. These processes also affect the SMP microstructure. In addition to the observed macroscopic shape recovery, the healing of micro-crazes and micro-cracks that have nucleated and developed during the loading occurs. Therefore, our study delves into the microscopic aspect, specifically addressing the healing of micro-cracks in the cyclic loading process. The proposed research concerns a thermoplastic polyurethane shape memory polymer (PU-SMP) MM4520 with a Tg of 45 °C. The objective of the study is to investigate the effect of the number of tensile loading-unloading cycles and thermal shape recovery on the evolution of the PU-SMP microstructure. To this end, comprehensive research starting from structural characterization of the initial state and at various stages of the PU-SMP mechanical loading was conducted. Dynamic mechanical analysis (DMA), differential scanning calorimetry (DSC), wide-angle X-ray scattering (WAXS) and scanning electron microscopy (SEM) were used. Moreover, the shape memory behavior in the thermomechanical loading program was investigated. The obtained average shape fixity value was 99%, while the shape recovery was 92%, which confirmed good shape memory properties of the PU-SMP. Our findings reveal that even during a single loading-unloading tension cycle, crazes and cracks nucleate on the surface of the PU-SMP specimen, whereas the subsequent temperature-induced shape recovery process carried out at the temperature above Tg enables the healing of micro-cracks. Interestingly, the surface of the specimen after three and five loading-unloading cycles did not exhibit crazes and cracks, although some traces of cracks were visible. The traces disappeared after exposing the material to heating at Tg + 20 °C (65 °C) for 30 min. The crack closure phenomenon during deformation, even without heating over Tg, occurred within three and five subsequent cycles of loading-unloading. Notably, in the case of eight loading-unloading cycles, cracks appeared on the surface of the PU-SMP and were healed only after thermal recovery at the particular temperature over Tg. Upon reaching a critical number of cycles, the proper amount of energy required for crack propagation was attained, resulting in wide-open cracks on the material’s surface. It is worth noting that WAXS analysis did not indicate strong signs of typical highly ordered structures in the PU-SMP specimens in their initial state and after the loading history; however, some orientation after the cyclic deformation was observed. Keywords: polyurethane shape memory polymer, glass transition temperature, tensile loading cycles, structure analysis, micro-cracks, healing Affiliations:
Staszczak M. | - | IPPT PAN | Urbański L. | - | IPPT PAN | Gradys A. D. | - | IPPT PAN | Cristea M. | - | Petru Poni Institute of Macromolecular Chemistry (RO) | Pieczyska E. A. | - | IPPT PAN |
| 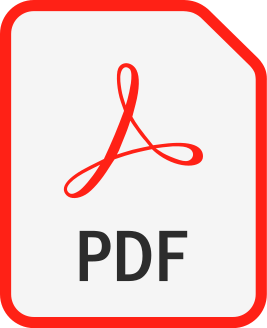 |
3. |
Staszczak M., Urbański L., Cristea M.♦, Ionita D.♦, Pieczyska E.A., Investigation of Shape Memory Polyurethane Properties in Cold Programming Process Towards Its Applications,
Polymers, ISSN: 2073-4360, DOI: 10.3390/polym16020219, Vol.16, No.2, pp.219-1-219-20, 2024 Abstract: Thermoresponsive shape memory polymers (SMPs) with the remarkable ability to remember a temporary shape and recover their original one using temperature have been gaining more and more attention in a wide range of applications. Traditionally, SMPs are investigated using a method named often “hot-programming”, since they are heated above their glass transition temperature (Tg) and after that, reshaped and cooled below Tg to achieve and fix the desired configuration. Upon reheating, these materials return to their original shape. However, the heating of SMPs above their Tg during a thermomechanical cycle to trigger a change in their shape creates a temperature gradient within the material structure and causes significant thermal expansion of the polymer sample resulting in a reduction in its shape recovery property. These phenomena, in turn, limit the application fields of SMPs, in which fast actuation, dimensional stability and low thermal expansion coefficient are crucial. This paper aims at a comprehensive experimental investigation of thermoplastic polyurethane shape memory polymer (PU-SMP) using the cold programming approach, in which the deformation of the SMP into the programmed shape is conducted at temperatures below Tg. The PU-SMP glass transition temperature equals approximately 65 ◦C. Structural, mechanical and thermomechanical characterization was performed, and the results on the identification of functional properties of PU-SMPs in quite a large strain range beyond yield limit were obtained. The average shape fixity ratio of the PU-SMP at room temperature programming was found to be approximately 90%, while the average shape fixity ratio at 45 ◦C (Tg − 20 ◦C) was approximately 97%. Whereas, the average shape recovery ratio was 93% at room temperature programming and it was equal to approximately 90% at 45 ◦C. However, the results obtained using the traditional method, the so-called hot programming at 65 ◦C, indicate a higher shape fixity value of 98%, but a lower shape recovery of 90%. Thus, the obtained results confirmed good shape memory properties of the PU-SMPs at a large strain range at various temperatures. Furthermore, the experiments conducted at both temperatures below Tg demonstrated that cold programming can be successfully applied to PU-SMPs with a relatively high Tg. Knowledge of the PU-SMP shape memory and shape fixity properties, estimated without risk of material degradation, caused by heating above Tg, makes them attractive for various applications, e.g., in electronic components, aircraft or aerospace structures. Keywords: polyurethane shape memory polymer, cold programming, thermal expansion, shape fixity, shape recovery Affiliations:
Staszczak M. | - | IPPT PAN | Urbański L. | - | IPPT PAN | Cristea M. | - | Petru Poni Institute of Macromolecular Chemistry (RO) | Ionita D. | - | other affiliation | Pieczyska E.A. | - | IPPT PAN |
| 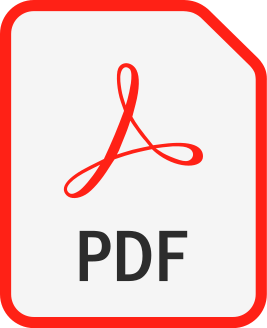 |
4. |
Nabavian Kalat M., Staszczak M., Urbański L., Fernandez C.♦, Vega C.♦, Cristea M.♦, Ionita D.♦, Lantada A.♦, Pieczyska E.A., Investigating a shape memory epoxy resin and its application to engineering shape-morphing devices empowered through kinematic chains and compliant joints,
MATERIALS AND DESIGN, ISSN: 0264-1275, DOI: 10.1016/j.matdes.2023.112263, Vol.233, No.112263, pp.1-15, 2023 Abstract: 4D printing is the additive manufacturing (3D printing) of objects that can transform their shape in a controlled and predictable way when subjected to external stimuli. A thermo-responsive shape memory polymer (SMP) is a highly suitable material to 4D print smart devices, due to its actuation function and the capability of recovering its original shape from the deformed one upon heating. This study presents the results of employing an epoxy resin in the additive manufacturing of complex-shaped smart devices with shape-morphing properties using laser stereolithography (SLA). To quantify the shape memory behaviour of the shape memory epoxy (SMEp), we first investigate the thermomechanical properties of the 3D-printed specimens in a tensile testing machine coupled with an environmental thermal chamber. This approach allows us to determine the shape fixity and recovery of SMEp. Next, we propose effective designs of complex-shaped devices, with the aim of promoting shape morphing through micro-actuators and compliant joints acting as active regions in combination with multiplying mechanisms or kinematic chains in each of the devices. We manufacture the complex-shaped prototypes by using SLA directly from the computer-aided designs. The shape memory trials of the 3D-printed prototypes reveal quite precise shape recovery of the devices, illustrating their shape-memory. In fact, the inclusion of micro-actuators and compliant joints within the complex-geometry devices allows for local triggering, deformation and recovery, resulting in a prompt response of the devices to heat. Therefore, innovative designs, along with the suitable smart material and high-quality manufacturing process, lead to 4D printed devices with fast actuation and shape-morphing properties. Overall, this research may contribute to the development of smart materials and 4D printing technology for applications in fields such as biomedical engineering, robotics, transport and aerospace engineering. Keywords: Shape memory polymers,Shape memory epoxy,Shape morphing structures,Laser stereolithography,3D and 4D printing Affiliations:
Nabavian Kalat M. | - | IPPT PAN | Staszczak M. | - | IPPT PAN | Urbański L. | - | IPPT PAN | Fernandez C. | - | other affiliation | Vega C. | - | other affiliation | Cristea M. | - | Petru Poni Institute of Macromolecular Chemistry (RO) | Ionita D. | - | other affiliation | Lantada A. | - | other affiliation | Pieczyska E.A. | - | IPPT PAN |
| 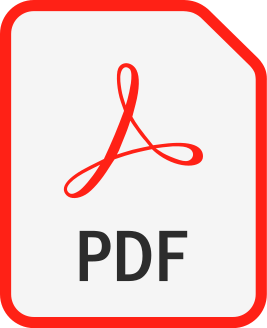 |
5. |
Golasiński K., Maj M., Urbański L., Staszczak M., Gradys A.D., Pieczyska E.A., Experimental study of thermomechanical behaviour of Gum Metal during cyclic tensile loadings: the quantitative contribution of IRT and DIC,
Quantitative InfraRed Thermography Journal, ISSN: 1768-6733, DOI: 10.1080/17686733.2023.2205762, pp.1-18, 2023 Abstract: Thermomechanical behaviour of Gum Metal (Ti–23Nb–0.7Ta–2.0Zr–1.2O, at.%) under cyclic tension was experimentally investigated using infrared thermography and digital image correlation. The thermomechanical characteristics of particular stages of the subsequent loading-unloading cycles of Gum Metal were identified, i.e. (I) the linear, elastic loading accompanied by the temperature drop, (II) the nonlinear super-elastic loading related to the temperature growth, (III) the transient stage (at which both the superelastic-like behaviour and the plastic one are present simultaneously) and the temperature starts growing fast, (IV) the plastic deformation with a significant growth of temperature, (V) the superelastic-like unloading accompanied by a fast drop in temperature, (VI) the transient unloading with a slower decrease in temperature and (VII) the elastic unloading, with a slight increase in temperature. Thermoelastic effect in Gum Metal during both loading and unloading was analysed in each tensile cycle. Finally, the evolution of strain and temperature fields just before unloading in each cycle was discussed and a comparison of the fields at selected stages of cycles 12 and 24 was presented. The results of this work enabled us to identify the non-dissipative processes of elastic and superelastic-like deformations as well as the dissipative process of plastic deformation. Keywords: Gum Metal,β-Ti alloy,cyclic tension,superelasticity,thermoelastic effect,infrared thermography,digital image correlation Affiliations:
Golasiński K. | - | IPPT PAN | Maj M. | - | IPPT PAN | Urbański L. | - | IPPT PAN | Staszczak M. | - | IPPT PAN | Gradys A.D. | - | IPPT PAN | Pieczyska E.A. | - | IPPT PAN |
| 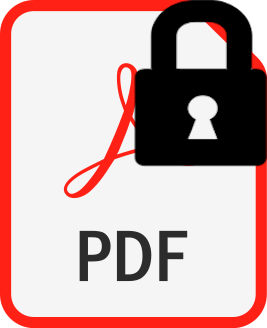 |
6. |
Musiał S., Maj M., Urbański L., Nowak M., Field analysis of energy conversion during plastic deformation of 310S stainless steel,
INTERNATIONAL JOURNAL OF SOLIDS AND STRUCTURES, ISSN: 0020-7683, DOI: 10.1016/j.ijsolstr.2021.111411, Vol.238, pp.111411-1-20, 2022 Abstract: The paper concerns the experimental analysis of the energy conversion process during uniaxial tension of 310S austenitic steel. The plastic work distributions were obtained taking into account the influence of strain rate and plastic anisotropy based on the displacement gradient determined experimentally using Digital Image Correlation (DIC) method. On the other hand, the energy dissipated as heat was obtained by the calculation of heat sources from the transient heat conduction equation basing on both the evolution of the temperature field determined by Infrared Thermography and mechanical field provided by DIC. It was shown that the proportions between the terms of the heat conduction equation and between the particular components of the energy dissipated as heat are significantly different for various process durations. As a measure of energy conversion the energy storage rate was used. At the beginning of the plastic deformation, the values are in the range from 0.4 to 0.6 depending on the strain rate and then decrease monotonically up to the level of around 0.15 with the increasing strain. Moreover, just before the end of the process the values decrease significantly and become close to 0 or even negative, which means that the material loses its ability to store the energy. Keywords: digital image correlation, infrared thermography, energy conversion, transient heatconduction equation, heat sources, energy storage rate Affiliations:
Musiał S. | - | IPPT PAN | Maj M. | - | IPPT PAN | Urbański L. | - | IPPT PAN | Nowak M. | - | IPPT PAN |
| 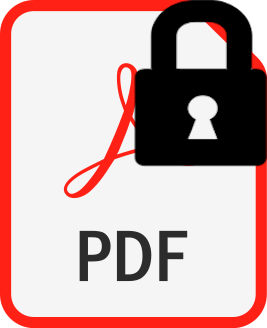 |
7. |
Staszczak M., Nabavian Kalat M., Golasiński K.M., Urbański L., Takeda K.♦, Matsui R.♦, Pieczyska E.A., Characterization of Polyurethane Shape Memory Polymer and Determination of Shape Fixity and Shape Recovery in Subsequent Thermomechanical Cycles,
Polymers, ISSN: 2073-4360, DOI: 10.3390/polym14214775, Vol.14, No.4775, pp.1-19, 2022 Abstract: Multifunctional polyurethane shape memory polymers (PU-SMPs) have been of increasing interest in various applications. Here we report structure characterization, detailed methodology, and obtained results on the identification of functional properties of a thermoset PU-SMP (MP4510) with glass transition temperature of 45 C. The stable, chemically crosslinked network of this thermoset PU-SMP results in excellent shape memory behavior. Moreover, the proximity of the activation temperature range of this smart polymer to room and body temperature enables the PU-SMP to be used in more critical industrial applications, namely fast-response actuators. The thermomechanical behavior of a shape memory polymer determines the engineering applications of the material. Therefore, investigation of the shape memory behavior of this class of commercial PU-SMP is of particular importance. The conducted structural characterization confirms its shape memory properties. The shape fixity and shape recovery properties were determined by a modified experimental approach, considering the polymer’s sensitivity to external conditions, i.e., the temperature and humidity variations. Three thermomechanical cycles were considered and the methodology used is described in detail. The obtained shape fixity ratio of the PU-SMP was approximately 98% and did not change significantly in the subsequent cycles of the thermomechanical loading due to the stability of chemical crosslinks in the thermoset materials structure. The shape recovery was found to be approximately 90% in the first cycle and reached a value higher than 99% in the third cycle. The results confirm the effect of the thermomechanical training on the improvement of the PU-SMP shape recovery after the first thermomechanical cycle as well as the effect of thermoset material stability on the repeatability of the shape memory parameters quantities. Keywords: polyurethane shape memory polymer, thermomechanical loading program, shape fixity, shape recovery Affiliations:
Staszczak M. | - | IPPT PAN | Nabavian Kalat M. | - | IPPT PAN | Golasiński K.M. | - | IPPT PAN | Urbański L. | - | IPPT PAN | Takeda K. | - | Aichi Institute of Technology (JP) | Matsui R. | - | Aichi Institute of Technology (JP) | Pieczyska E.A. | - | IPPT PAN |
| 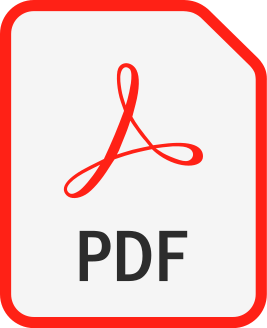 |
8. |
Grodzki W.♦, Oliferuk W., Doroszko M.♦, Szusta J.♦, Urbański L., Prediction of crack initiation based on energy storage rate during low-cycle fatigue of austenitic stainless steel,
Materials, ISSN: 1996-1944, DOI: 10.3390/ma14195526, Vol.14, No.19, pp.5526-1-13, 2021 Abstract: The low-cycle deformation of 304L austenitic stainless steel was examined in terms of energy conversion. Specimens were subjected to cyclic loading at the frequency of 2 Hz. The loading process was carried out in a hybrid strain–stress manner. In each cycle, the increase in elongation of the gauge part of the specimen was constant. During experimental procedures, infrared and visible-range images of strain and temperature fields were recorded simultaneously using infrared thermography (IR) and digital image correlation (DIC) systems. On the basis of the obtained test results, the energy storage rate, defined as the ratio of the stored energy increment to the plastic work increment, was calculated and expressed in reference to selected sections of the specimen. It was shown that, before the specimen fracture in a specific area, the energy storage rate is equal to zero (the material loses the ability to store energy), and the energy stored during the deformation process is released and dissipated as heat. Negative and close-to-zero values of the energy storage rate can be used as a plastic instability criterion on the macroscale. Thus, the loss of energy storage ability by a deformed material can be treated as an indicator of fatigue crack initiation. Keywords: low-cycle fatigue, infrared thermography, plastic strain localization, digital image correlation, energy storage rate, plastic instability criterion Affiliations:
Grodzki W. | - | Bialystok University of Technology (PL) | Oliferuk W. | - | IPPT PAN | Doroszko M. | - | Bialystok University of Technology (PL) | Szusta J. | - | Bialystok University of Technology (PL) | Urbański L. | - | IPPT PAN |
| 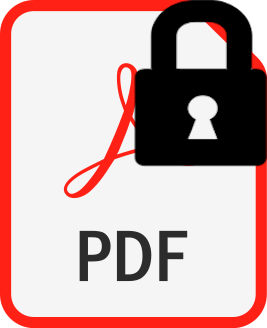 |
9. |
Frydrych K., Maj M., Urbański L., Kowalczyk-Gajewska K., Twinning-induced anisotropy of mechanical response of AZ31B extruded rods,
MATERIALS SCIENCE AND ENGINEERING A-STRUCTURAL MATERIALS PROPERTIES MICROSTRUCTURE AND PROCESSING, ISSN: 0921-5093, DOI: 10.1016/j.msea.2019.138610, Vol.771, pp.138610-1-14, 2020 Abstract: Texture and twinning-induced anisotropy of the yield stress and hardening of AZ31B extruded rods is investigated. The multidirectional compression tests involving strain path changes are performed in order to: i. assess which slip and twinning systems are active in the polycrystalline sample with a strong texture, ii. analyze the influence of the preliminary deformation upon twin formation, iii. observe the resulting change of the mechanical response. In order to fulfil these goals mechanical testing is supplemented by microstructure analysis. Experimental observations are used to validate the proposed crystal plasticity framework when it is combined with the viscoplastic self-consistent scheme. On the other hand, the results of numerical simulations are used to confirm an advocated interpretation of experimental findings. Finally, the experimental and numerical results are discussed with respect to the theoretical study of slip and twinning activity on the basis of the generalized Schmid criterion. It is concluded that twinning activity influences the mechanical response predominantly by the texture change and to lesser extent by modification of strain hardening due to slip-twin interactions. Keywords: crystal plasticity, anisotropy, plastic deformation, twinning, hcp Affiliations:
Frydrych K. | - | IPPT PAN | Maj M. | - | IPPT PAN | Urbański L. | - | IPPT PAN | Kowalczyk-Gajewska K. | - | IPPT PAN |
| 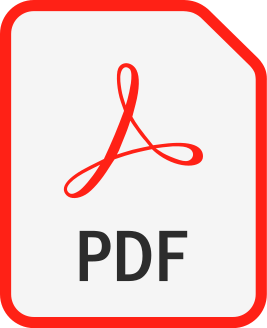 |
10. |
Golasiński K.M., Pieczyska E.A., Maj M., Mackiewicz S., Staszczak M., Kowalewski Z.L., Urbański L., Zubko M.♦, Takesue N.♦, Anisotropy of gum metal analysed by ultrasonic measurement and digital image correlation,
MATERIALS SCIENCE AND TECHNOLOGY, ISSN: 0267-0836, DOI: 10.1080/02670836.2019.1629539, Vol.36, No.9, pp.996-1002, 2020 Abstract: The mechanical anisotropy of a multifunctional titanium alloy, Gum Metal, is investigated in this paper. The structural characterisation showed a strong <110> texture for Gum Metal, that is a result of the cold-swaging process applied during its manufacture. Gum Metal was treated as a transversally isotropic solid because of this texture. A significant difference from Young's moduli of the alloy was detected from the ultrasonic measurement of parallel and perpendicular directions to the alloy swaging direction. Samples of Gum Metal cubes were compressed in two different orientations. During the deformation process, two perpendicular walls of each sample were monitored by two visible range cameras for further two-dimensional digital image correlation analysis, this confirmed a strong plastic anisotropy in Gum Metal. Keywords: gum metal, compression, mechanical anisotropy, digital image correlation, ultrasonic measurement, texture, titanium alloy, full-field deformation measurement Affiliations:
Golasiński K.M. | - | IPPT PAN | Pieczyska E.A. | - | IPPT PAN | Maj M. | - | IPPT PAN | Mackiewicz S. | - | IPPT PAN | Staszczak M. | - | IPPT PAN | Kowalewski Z.L. | - | IPPT PAN | Urbański L. | - | IPPT PAN | Zubko M. | - | other affiliation | Takesue N. | - | Fukuoka University (JP) |
| 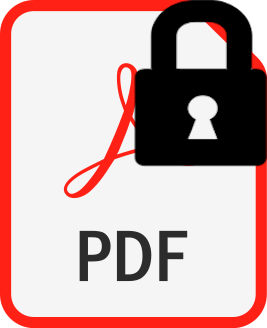 |
11. |
Staszczak M., Pieczyska E.A., Maj M., Urbański L., Odriozola I.♦, Martin R.♦, Thermomechanical Properties of Vulcanized Rubber investigated by Testing Machine and Infrared Camera,
Measurement Automation Monitoring, ISSN: 0032-4140, Vol.61, No.6, pp.206-209, 2015 Abstract: Experimental results of effects of thermomechanical couplings occurring both in natural vulcanized rubber and rubber with self-healing polyurethane subjected to tension at different strain rates are presented. Mechanical characteristics were recorded by testing machine, while the sample temperature changes accompanying the deformation process was measured by infrared camera. The goal was to investigate influence of self-healing polyurethane on the rubber mechanical and thermomechanical properties. It was found that the introduction of the self-healing polyurethane ensures the higher elasticity and the lower tensile strength of the rubber. It was also confirmed that the material is very sensitive to the strain rate; the higher the strain rate, the higher the values of the stress and temperature increases have been obtained. Keywords: vulcanized rubber, self-healing polyurethane, tension test, thermomechanical couplings, temperature changes, infrared camera Affiliations:
Staszczak M. | - | IPPT PAN | Pieczyska E.A. | - | IPPT PAN | Maj M. | - | IPPT PAN | Urbański L. | - | IPPT PAN | Odriozola I. | - | IK4-CIDETEC (ES) | Martin R. | - | IK4-CIDETEC (ES) |
| 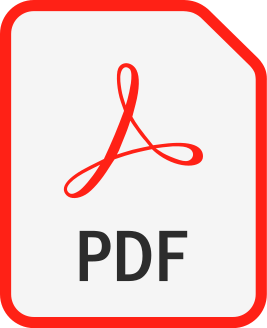 |
12. |
Pieczyska E.A., Maj M., Kowalczyk-Gajewska K., Staszczak M., Urbański L., Tobushi H.♦, Hayashi S.♦, Cristea M.♦, Mechanical and Infrared Thermography Analysis of Shape Memory Polyurethane,
Journal of Materials Engineering and Performance, ISSN: 1059-9495, DOI: 10.1007/s11665-014-0963-2, Vol.23, No.7, pp.2553-2560, 2014 Abstract: Multifunctional new material—polyurethane shape memory polymer (PU-SMP)—was subjected to tension carried out at room temperature at various strain rates. The influence of effects of thermomechanical couplings on the SMP mechanical properties was studied, based on the sample temperature changes, measured by a fast and sensitive infrared camera. It was found that the polymer deformation process strongly depends on the strain rate applied. The initial reversible strain is accompanied by a small drop in temperature, called thermoelastic effect. Its maximal value is related to the SMP yield point and increases upon increase of the strain rate. At higher strains, the stress and temperature significantly increase, caused by reorientation of the polymer molecular chains, followed by the stress drop and its subsequent increase accompanying the sample rupture. The higher strain rate, the higher stress, and temperature changes were obtained, since the deformation process was more dynamic and has occurred in almost adiabatic conditions. The constitutive model of SMP valid in finite strain regime was developed. In the proposed approach, SMP is described as a two-phase material composed of hyperelastic rubbery phase and elastic-viscoplastic glassy phase, while the volume content of phases is specified by the current temperature. Keywords: constitutive model, dynamic mechanical analysis, shape memory polyurethane, strain rate, temperature change, thermomechanical couplings Affiliations:
Pieczyska E.A. | - | IPPT PAN | Maj M. | - | IPPT PAN | Kowalczyk-Gajewska K. | - | IPPT PAN | Staszczak M. | - | IPPT PAN | Urbański L. | - | IPPT PAN | Tobushi H. | - | Aichi Institute of Technology (JP) | Hayashi S. | - | SMP Technologies Inc. (JP) | Cristea M. | - | Petru Poni Institute of Macromolecular Chemistry (RO) |
| 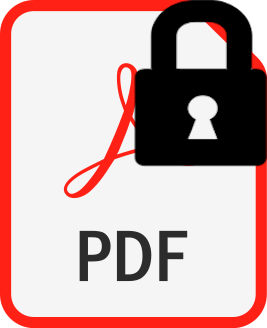 |
13. |
Staszczak M., Pieczyska E.A., Maj M., Urbański L., Tobushi H.♦, Hayashi S.♦, Właściwości mechaniczne oraz zmiany temperatury polimeru z pamięcią kształtu w procesie rozciągania,
POMIARY AUTOMATYKA KONTROLA, ISSN: 0032-4140, Vol.59, No.9, pp.1002-1005, 2013 Abstract: This paper presents experimental evaluation of a new polyurethane shape memory polymer (PU-SMP) produced by SMP Technologies Inc. It discusses mechanical characteristics and temperature changes of the SMP specimens subjected to tension test performed at room temperature with various strain rates. Basing on the mechanical data and the relevant temperature changes, we have studied the thermomechanical properties of the PU-SMP and influence of the strain rate on the strain localization behavior. Finally, we have identified the material parameters for the one-dimensional rheological model of the SMP. Keywords: shape memory polyurethane, tension test, dynamic mechanical analysis, infrared camera, temperature change, thermomechanical properties, rheological model Affiliations:
Staszczak M. | - | IPPT PAN | Pieczyska E.A. | - | IPPT PAN | Maj M. | - | IPPT PAN | Urbański L. | - | IPPT PAN | Tobushi H. | - | Aichi Institute of Technology (JP) | Hayashi S. | - | SMP Technologies Inc. (JP) |
| 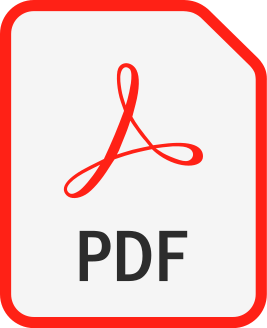 |
14. |
Oliferuk W., Maj M., Litwinko R.♦, Urbański L., Thermomechanical coupling in the elastic regime and elasto-plastic transition during tension of austenitic steel, titanium and aluminium alloy at strain rates from 10-4 to 10-1 s-1,
EUROPEAN JOURNAL OF MECHANICS A-SOLIDS, ISSN: 0997-7538, DOI: 10.1016/j.euromechsol.2011.08.007, Vol.35, pp.111-118, 2012 Abstract: The temperature variation phenomenon during uniaxial deformation of materials with positive coefficient of linear thermal expansion is studied. The formula for a change in the specimen temperature during non-adiabatic tensile deformation is briefly derived. Thermomechanical behaviour of austenitic stainless steel, titanium and aluminium alloy during initial stage of tension at strain rates from 10−4 to 10−1 s−1 has been investigated. It was confirmed, that with increasing stress the temperature of each tested specimen first decreases linearly, reaches a minimum and then starts to rise. The decrease in the specimen temperature corresponds to elastic deformation whereas the temperature rise is related to the plastic one. Thus, the change in the specimen temperature can be used for study of elasto-plastic transition. From the viewpoint of strict theoretical analysis, the yield point will be defined as the stress corresponding to the lowest temperature, if tensile deformation process is adiabatic. The processes of deformation considered in this work are not adiabatic; there is a heat exchange between the specimen and the surroundings. The influence of this fact on the change in the specimen temperature vs. stress is discussed. The problem of yield point as the value of stress corresponding to minimum temperature of the specimen is considered. The influence of the strain rate on the yield point for tested materials is studied. Comparing of the obtained results with theoretical model, the limit above which the deformation process can be treated as the adiabatic one was determined. The values of the yield points determined on the basis of the thermoelastic effect were compared with the stress corresponding to the 0.2% of plastic strain. Keywords: Thermoelastic effect, Yield point, Non-adiabatic deformation Affiliations:
Oliferuk W. | - | IPPT PAN | Maj M. | - | IPPT PAN | Litwinko R. | - | other affiliation | Urbański L. | - | IPPT PAN |
| 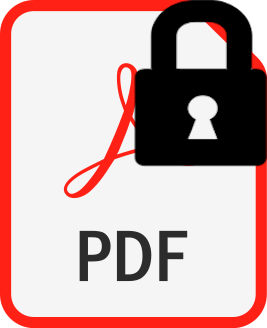 |