1. |
Nosewicz S., Jenczyk P., Romelczyk-Baishya B.♦, Bazarnik P.♦, Jarząbek D.M., Majchrowicz K.♦, Pakieła Z.♦, Kowiorski K.♦, Chmielewski M.♦, The influence of spark plasma sintering on multiscale mechanical properties of nickel-based composite materials,
MATERIALS SCIENCE AND ENGINEERING A-STRUCTURAL MATERIALS PROPERTIES MICROSTRUCTURE AND PROCESSING, ISSN: 0921-5093, DOI: 10.1016/j.msea.2023.146001, Vol.891, pp.146001, 2024 Abstract: The paper presents a comprehensive investigation of the influence of the main process parameters of spark plasma sintering on the mechanical and microstructural properties of nickel-silicon carbide composites at various scales. Microstructure analysis performed by scanning and transmission electron microscopy revealed a significant interfacial reaction between nickel and silicon carbide due to the decomposition of silicon carbide. The chemical interaction of the matrix and reinforcement results in the formation of a multicomponent interphase zone formed by silicides (Ni31Si12 or/and Ni3Si) and graphite precipitates. Furthermore, several types of structure defects were observed (mainly nano/micropores at the phase boundaries). These significantly influenced the mechanical response of nickel-silicon carbide composites at different levels. At the macroscopic scale, uniaxial tensile tests confirmed that applying a 1000 oC sintering temperature ensured that the manufactured composite was characterised by satisfactory tensile strength, however, with a considerable reduction of material elongation compared to pure nickel. Moreover, the fractography study allowed us to identify a significant difference in the damage mode for certain nickel-silicon carbide samples. Secondly, the interface of the nickel matrix and silicate interphase was tested by bending with microcantilevers to evaluate its deformation behaviour, strength, and fracture characteristics. It was confirmed that a diffusive kind of interface, such as Ni-NiSi, demonstrates unexpected bonding properties with a relatively large range of plastic deformation. Finally, the nanoindentation of three main components of the nickel-silicon carbide composite was executed to evaluate the evolution of nanohardness, Young’s modulus, and elastic recovery due to the application of various spark plasma sintering conditions. Keywords: nickel-based composite,silicon carbide,spark plasma sintering,multiscale characterization,mechanical properties,nanoindentation,bending of microcantilevers Affiliations:
Nosewicz S. | - | IPPT PAN | Jenczyk P. | - | IPPT PAN | Romelczyk-Baishya B. | - | Warsaw University of Technology (PL) | Bazarnik P. | - | Warsaw University of Technology (PL) | Jarząbek D.M. | - | IPPT PAN | Majchrowicz K. | - | other affiliation | Pakieła Z. | - | Warsaw University of Technology (PL) | Kowiorski K. | - | other affiliation | Chmielewski M. | - | Institute of Electronic Materials Technology (PL) |
| 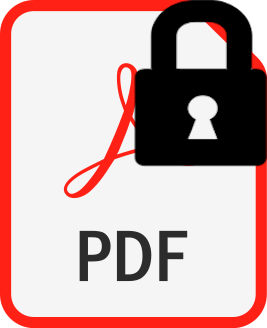 |
2. |
Kowiorski K.♦, Heljak M.♦, Strojny-Nędza A.♦, Bucholc B., Chmielewski M.♦, Djas M.♦, Kaszyca K.♦, Zybała R.♦, Małek M.♦, Swieszkowski W.♦, Chlanda A.♦, Compositing graphene oxide with carbon fibers enables improved dynamical thermomechanical behavior of papers produced at a large scale,
, DOI: 10.1016/j.carbon.2023.02.009, Vol.206, pp.26-36, 2023 Abstract: This article discusses the morphology and thermomechanical properties of graphene oxide (GO) paper sheets and GO paper composites reinforced with carbon fibers. GO paper was fabricated using GO paste obtained by the condensation of GO aqueous solution synthesized using the Hummers' method. Carbon fibers were implemented to improve the mechanical properties of the pristine GO paper. All the investigated papers were subjected to thermal treatment to check thermo-related morphological and mechanical properties. The results presented in this study allowed for the deeper insight into morphological, structural, and mechanical volume and surface-related properties of pristine GO and GO-based composite materials reinforced with carbon fibers. We showed that there are two important factors that should be taken into consideration for the design and fabrication of GO-based papers. These factors were the concentration of the reinforcing agent and the thermal reduction of the papers. Both factors have influenced the final properties of the resulting GO-based papers. For the first time, it was revealed how the addition of the reinforcing material affects the GO paper thermal expansion coefficient. Keywords: Flake graphene, Graphene oxide, Graphene oxide paper, Carbon fibers, Mechanical properties Affiliations:
Kowiorski K. | - | other affiliation | Heljak M. | - | Warsaw University of Technology (PL) | Strojny-Nędza A. | - | Institute of Electronic Materials Technology (PL) | Bucholc B. | - | IPPT PAN | Chmielewski M. | - | Institute of Electronic Materials Technology (PL) | Djas M. | - | other affiliation | Kaszyca K. | - | Lukasiewicz Institute of Microelectronics and Photonics (PL) | Zybała R. | - | Warsaw University of Technology (PL) | Małek M. | - | other affiliation | Swieszkowski W. | - | other affiliation | Chlanda A. | - | Warsaw University of Technology (PL) |
| 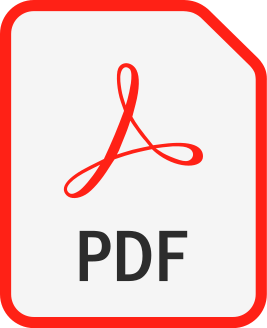 |
3. |
Zybała R.♦, Bucholc B., Kaszyca K.♦, Kowiorski K.♦, Soboń D.♦, Żórawski W.♦, Moszczyńska D.♦, Molak R.♦, Pakieła Z.♦, Properties of Cold Sprayed Titanium and Titanium Alloy Coatings after Laser Surface Treatment,
Materials, ISSN: 1996-1944, DOI: 10.3390/ma15249014, Vol.15(24), No.9014, pp.1-17, 2022 Abstract: Additive manufacturing (AM) has seen remarkable development in recent years due to relatively high efficiency of the process. Cold spraying (CS) is a particular method of AM, in which titanium and titanium alloy powders are used. CS is a very competitive technology enabling the deposition of coatings, repairing machine parts, and manufacturing new components. For specific applications, the surface of cold-sprayed materials may require further processing. This paper reports an attempt to employ laser surface treatment (LST) of cold-sprayed coatings on an aluminium alloy substrate. The influence of laser beam interaction time on the coatings’ properties was analysed. The microstructure was investigated and observed employing scanning electron microscopy (SEM). To evaluate residual stress after CS and LST, the sin2ψ technique was used. Investigations were also performed on Vickers hardness, contact angle, and surface roughness. Significant changes in the surface morphology of the coatings and elevated residual stress levels dependent on the laser beam interaction time were observed. Increased Vickers hardness was recorded for titanium alloy Ti6Al4V. LST also led to increased surface hydrophilicity of the modified materials Ti and Ti6Al4V. Keywords: cold spray, laser surface treatment, titanium coating, Ti6Al4V, residual stresses Affiliations:
Zybała R. | - | Warsaw University of Technology (PL) | Bucholc B. | - | IPPT PAN | Kaszyca K. | - | Lukasiewicz Institute of Microelectronics and Photonics (PL) | Kowiorski K. | - | other affiliation | Soboń D. | - | other affiliation | Żórawski W. | - | other affiliation | Moszczyńska D. | - | other affiliation | Molak R. | - | other affiliation | Pakieła Z. | - | Warsaw University of Technology (PL) |
| 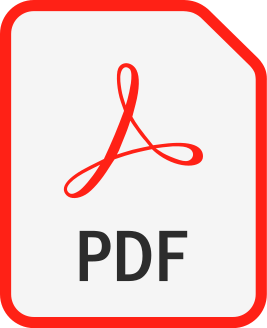 |
4. |
Bucholc B., Kaszyca K.♦, Śpiewak P.♦, Marszałek K.♦, Kruszewski M.♦, Ciupiński Ł.♦, Kowiorski K.♦, Zybała R.♦, Thermoelectric properties of bismuth-doped magnesium silicide obtained by the self-propagating
high-temperature synthesis,
BULLETIN OF THE POLISH ACADEMY OF SCIENCES: TECHNICAL SCIENCES, ISSN: 0239-7528, DOI: 10.24425/bpasts.2022.141007, Vol.70(3), No.e141007, pp.1-7, 2022 Abstract: Doping is one of the possible ways to significantly increase the thermoelectric properties of many different materials. It has been confirmed that by introducing bismuth atoms into Mg sites in the Mg2Si compound, it is possible to increase career concentration and intensify the effect of phonon scattering, which results in remarkable enhancement in the figure of merit (ZT) value. Magnesium silicide has gained scientists’ attention due to its nontoxicity, low density, and inexpensiveness. This paper reports on our latest attempt to employ ultrafast selfpropagating high-temperature synthesis (SHS) followed by the spark plasma sintering (SPS) as a synthesis process of doped Mg2Si. Materials with varied bismuth doping were fabricated and then thoroughly analyzed with the laser flash method (LFA), X-ray diffraction (XRD), scanning electron microscopy (SEM) with an integrated energy-dispersive spectrometer (EDS). For density measurement, the Archimedes method was used. The electrical conductivity was measured using a standard four-probe method. The Seebeck coefficient was calculated from measured Seebeck voltage in the sample subjected to a temperature gradient. The structural analyses showed the Mg2Si phase as dominant and Bi2Mg3 located at grain boundaries. Bismuth doping enhanced ZT for every dopant concentration. ZT = 0:44 and ZT=0.38 were obtained for 3wt% and 2wt% at 770 K, respectively. Keywords: thermoelectric materials, magnesium silicide, bismuth doping, SHS, spark plasma sintering Affiliations:
Bucholc B. | - | IPPT PAN | Kaszyca K. | - | Lukasiewicz Institute of Microelectronics and Photonics (PL) | Śpiewak P. | - | other affiliation | Marszałek K. | - | AGH University of Science and Technology (PL) | Kruszewski M. | - | other affiliation | Ciupiński Ł. | - | Warsaw University of Technology (PL) | Kowiorski K. | - | other affiliation | Zybała R. | - | Warsaw University of Technology (PL) |
| 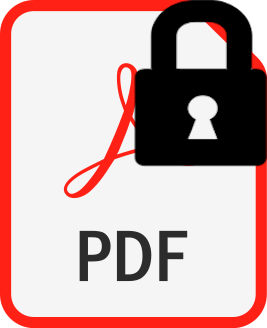 |