1. |
Matsui R.♦, Takeda K.♦, Tobushi H.♦, Pieczyska E.A., Mechanical properties and advanced subjects in shape memory alloys and polymers,
JOURNAL OF THEORETICAL AND APPLIED MECHANICS, ISSN: 1429-2955, DOI: 10.15632/jtam-pl.56.2.447, Vol.56, No.2, pp.447-456, 2018 Abstract: Advanced subjects in mechanical properties of shape memory alloys and polymers are discussed. In the subloop loading under a stress-controlled condition of the shape memory alloy, the transformation-induced stress relaxation appears due to variation in temperature. The enhancement of corrosion and corrosion fatigue life of the shape memory alloy is discussed. The development of a functionally-graded shape memory alloy and polymer is expected to obtain better performance. Three-way motion appears in the shape memory composite with the shape memory alloy and polymer. Keywords: shape memory alloy, shape memory polymer, functionally-graded shape memory material, shape memory composite Affiliations:
Matsui R. | - | Aichi Institute of Technology (JP) | Takeda K. | - | Aichi Institute of Technology (JP) | Tobushi H. | - | Aichi Institute of Technology (JP) | Pieczyska E.A. | - | IPPT PAN |
| 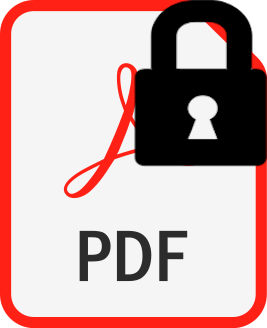 |
2. |
Pieczyska E.A., Staszczak M., Kowalczyk-Gajewska K., Maj M., Golasiński K.M., Golba S.♦, Tobushi H.♦, Hayashi S.♦, Experimental and numerical investigation of yielding phenomena in a shape memory polymer subjected to cyclic tension at various strain rates,
POLYMER TESTING, ISSN: 0142-9418, DOI: 10.1016/j.polymertesting.2017.04.014, Vol.60, pp.333-342, 2017 Abstract: This paper presents experimental and numerical results of a polyurethane shape memory polymer (SMP) subjected to cyclic tensile loading. The goal was to investigate the polymer yielding phenomena based on the effects of thermomechanical coupling. Mechanical characteristics were obtained with a testing machine, whereas the SMP temperature accompanying its deformation process was simultaneously measured in a contactless manner with an infrared camera. The SMP glass transition temperature was approximately 45oC; therefore, when tested at room temperature, the polymer is rigid and behaves as solid material. The stress and related temperature changes at various strain rates showed how the SMP yield limit evolved in subsequent loading-unloading cycles under various strain rates. A two-phase model of the SMP was applied to describe its mechanical response in cyclic tension. The 3D Finite Element model of a tested specimen was used in simulations. Good agreement between the model predictions and experimental results was observed for the first tension cycle. Keywords: Shape memory polymer, Tension cyclic loading, Thermomechanical coupling, Yield limit, Thermoelastic effect, Constitutive model Affiliations:
Pieczyska E.A. | - | IPPT PAN | Staszczak M. | - | IPPT PAN | Kowalczyk-Gajewska K. | - | IPPT PAN | Maj M. | - | IPPT PAN | Golasiński K.M. | - | IPPT PAN | Golba S. | - | University of Silesia (PL) | Tobushi H. | - | Aichi Institute of Technology (JP) | Hayashi S. | - | SMP Technologies Inc. (JP) |
| 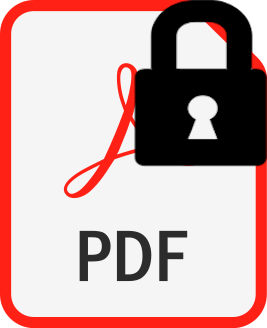 |
3. |
Takeda K.♦, Matsui R.♦, Tobushi H.♦, Pieczyska E.A., Torsional deformation properties of SMA tapes and their application to bias-type reciprocating rotary driving actuator,
ARCHIVES OF MECHANICS, ISSN: 0373-2029, Vol.69, No.4-5, pp.289-303, 2017 Abstract: In order to develop the reciprocating rotary driving actuator with a simple mechanism using shape memory alloy (SMA) tapes, the graphical method to design the actuator was proposed based on the torsional deformation properties of SMA tapes. The torsional deformation properties of the SME tape showing the shape memory effect (SME) and the SE tape showing superelasticity (SE) were obtained. The bias-type reciprocating rotary actuator was composed of the pretwisted SME tape and the flat SE tape in series. The design chart expressed by the relationship between torque and twisting angle of the SME tape and the SE tape was proposed. The rotational angle and torque, which vary depending on temperature, can be estimated based on the design chart. The rotational angle is controlled by adjusting the mounting angle of the SME tape and the heating temperature. The automatically opening and closing blind driven by sunlight was demonstrated. The blind was controlled by using the reciprocating rotary element composed of the SME tape and the SE tape. The behavior of the blind can be achieved based on the proposed design method of the reciprocating rotary driving element Keywords: shape memory alloy, tape, torsion, actuator, reciprocating rotation, design chart, bias-type Affiliations:
Takeda K. | - | Aichi Institute of Technology (JP) | Matsui R. | - | Aichi Institute of Technology (JP) | Tobushi H. | - | Aichi Institute of Technology (JP) | Pieczyska E.A. | - | IPPT PAN |
| 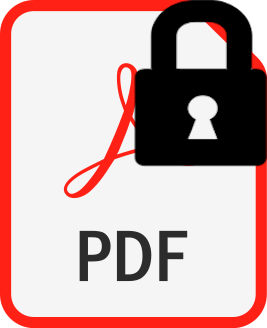 |
4. |
Pieczyska E.A., Staszczak M., Maj M., Kowalczyk-Gajewska K., Golasiński K.M., Cristea M.♦, Tobushi H.♦, Hayashi S.♦, Investigation of thermomechanical couplings, strain localization and shape memory properties in a shape memory polymer subjected to loading at various strain rates,
SMART MATERIALS AND STRUCTURES, ISSN: 0964-1726, DOI: 10.1088/0964-1726/25/8/085002, Vol.25, No.8, pp.085002-1-15, 2016 Abstract: This paper presents experimental and modeling results of the effects of thermomechanical couplings occurring in a polyurethane shape memory polymer (SMP) subjected to tension at various strain rates within large strains. The SMP mechanical curves, recorded using a testing machine, and the related temperature changes, measured in a contactless manner using an IR camera, were used to investigate the polymer deformation process at various loading stages. The effects of thermomechanical couplings allowed the determination of the material yield point in the initial loading stage, the investigation of nucleation and development of the strain localization at larger strains and the estimation of the effects of thermoelastic behavior during the unloading process. The obtained stress–strain and thermal characteristics, the results of the dynamic mechanical analysis and estimated values of the shape fixity and shape recovery parameters confirmed that the shape memory polymer (T g = 45°C) is characterized by good mechanical and shape memory properties, as well as high sensitivity to the strain rate. The mechanical response of the SMP subjected to tension was simulated using the finite element method and applying the large strain, two-phase model. Strain localization observed in the experiment was well reproduced in simulations and the temperature spots were correlated with the accumulated viscoplastic deformation of the SMP glassy phase. Keywords: shape memory polymer, thermomechanical coupling, infrared camera, tension test, strain rate, strain localization, constitutive model Affiliations:
Pieczyska E.A. | - | IPPT PAN | Staszczak M. | - | IPPT PAN | Maj M. | - | IPPT PAN | Kowalczyk-Gajewska K. | - | IPPT PAN | Golasiński K.M. | - | IPPT PAN | Cristea M. | - | Petru Poni Institute of Macromolecular Chemistry (RO) | Tobushi H. | - | Aichi Institute of Technology (JP) | Hayashi S. | - | SMP Technologies Inc. (JP) |
| 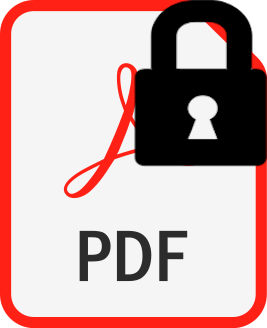 |
5. |
Staszczak M., Pieczyska E.A., Maj M., Kukla D., Tobushi H.♦, Infrared thermographic analysis of shape memory polymer during cyclic loading,
MEASUREMENT SCIENCE AND TECHNOLOGY, ISSN: 0957-0233, DOI: 10.1088/0957-0233/27/12/124007, Vol.27, No.12, pp.124007-1-6, 2016 Abstract: In this paper we present the effects of thermomechanical couplings occurring in polyurethane shape memory polymer subjected to cyclic tensile loadings conducted at various strain rates. Stress–strain characteristics were elaborated using a quasistatic testing machine, whereas the specimen temperature changes accompanying the deformation process were obtained with an infrared camera. We demonstrate a tight correlation between the mechanical and thermal results within the initial loading stage. The polymer thermomechanical behaviour in four subsequent loading-unloading cycles and the influence of the strain rate on the stress and the related temperature changes were also examined. In the range of elastic deformation the specimen temperature drops below the initial level due to thermoelastic effect whereas at the higher strains the temperature always increased, due to the dissipative deformation mechanisms. The difference in the characteristics of the specimen temperature has been applied to determine a limit of the polymer reversible deformation and analyzed for various strain rates. It was shown that at the higher strain rates higher values of the stress and temperature changes are obtained, which are related to higher values of the polymer yield points. During the cyclic loading a significant difference between the first and the second cycle was observed. The subsequent loading-unloading cycles demonstrated similar sharply shaped stress and temperature profiles and gradually decrease in values. Keywords: thermomechanical couplings, infrared camera, shape memory polymer, tension, strain rate, thermoelastic effect, yield point Affiliations:
Staszczak M. | - | IPPT PAN | Pieczyska E.A. | - | IPPT PAN | Maj M. | - | IPPT PAN | Kukla D. | - | IPPT PAN | Tobushi H. | - | Aichi Institute of Technology (JP) |
| 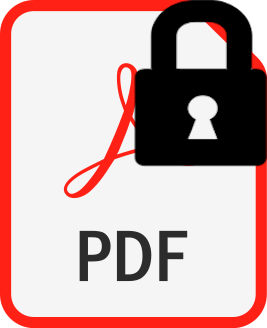 |
6. |
Pieczyska E.A., Maj M., Kowalczyk-Gajewska K., Staszczak M., Gradys A., Majewski M., Cristea M.♦, Tobushi H.♦, Hayashi S.♦, Thermomechanical properties of polyurethane shape memory polymer–experiment and modelling,
SMART MATERIALS AND STRUCTURES, ISSN: 0964-1726, DOI: 10.1088/0964-1726/24/4/045043, Vol.24, pp.045043-1-16, 2015 Abstract: In this paper extensive research on the polyurethane shape memory polymer (PU-SMP) is reported, including its structure analysis, our experimental investigation of its thermomechanical properties and its modelling. The influence of the effects of thermomechanical couplings on the SMP behaviour during tension at room temperature is studied using a fast and sensitive infrared camera. It is shown that the thermomechanical behaviour of the SMP significantly depends on the strain rate: at a higher strain rate higher stress and temperature values are obtained. This indicates that an increase of the strain rate leads to activation of different deformation mechanisms at the micro-scale, along with reorientation and alignment of the molecular chains. Furthermore, influence of temperature on the SMP's mechanical behaviour is studied. It is observed during the loading in a thermal chamber that at the temperature 20°C below the glass transition temperature (Tg) the PU-SMP strengthens about six times compared to the material above Tg but does not exhibit the shape recovery. A finite-strain constitutive model is formulated, where the SMP is described as a two-phase material composed of a hyperelastic rubbery phase and elastic-viscoplastic glassy phase. The volume content of phases is governed by the current temperature. Finally, model predictions are compared with the experimental results. Keywords: shape memory polyurethane, thermomechanical couplings, infrared camera, temperature change, dynamic mechanical analysis, strain rate, constitutive model Affiliations:
Pieczyska E.A. | - | IPPT PAN | Maj M. | - | IPPT PAN | Kowalczyk-Gajewska K. | - | IPPT PAN | Staszczak M. | - | IPPT PAN | Gradys A. | - | IPPT PAN | Majewski M. | - | IPPT PAN | Cristea M. | - | Petru Poni Institute of Macromolecular Chemistry (RO) | Tobushi H. | - | Aichi Institute of Technology (JP) | Hayashi S. | - | SMP Technologies Inc. (JP) |
| 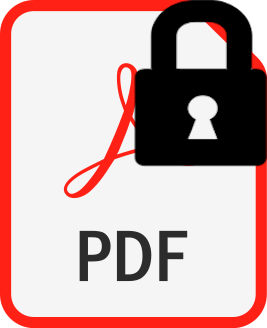 |
7. |
Takeda K.♦, Matsui R.♦, Tobushi H.♦, Homma S.♦, Levintant-Zayonts N., Kucharski S., Enhancement of bending fatigue life in TiNi shape-memory alloy tape by nitrogen ion implantation,
ARCHIVES OF MECHANICS, ISSN: 0373-2029, Vol.67, No.4, pp.293-310, 2015 Abstract: A shape-memory alloy (SMA) is expected to be applied as intelligent or smart material since it shows the functional characteristics of the shape memory effect and superelasticity. Most SMA elements, with these characteristics, perform cyclic motions. In these cases, the fatigue property of SMA is one of the most important issues in view of evaluating functional characteristics of SMA elements. The fatigue properties are complex since they depend on stress, strain, temperature and their hysteresis. If an SMA is implanted with high-energy ions, the thermomechanical properties of the material may change, resulting in long fatigue life. In the present study, the nitrogen ion implantation was applied to modify the surface of a TiNi SMA tape and the influence of implantation treatment on the bending fatigue properties was investigated. Keywords: shape-memory alloy, titanium-nickel alloy, superelasticity, nitrogen ion implantation, fatigue, bending Affiliations:
Takeda K. | - | Aichi Institute of Technology (JP) | Matsui R. | - | Aichi Institute of Technology (JP) | Tobushi H. | - | Aichi Institute of Technology (JP) | Homma S. | - | Nippon Trex Co. (JP) | Levintant-Zayonts N. | - | IPPT PAN | Kucharski S. | - | IPPT PAN |
| 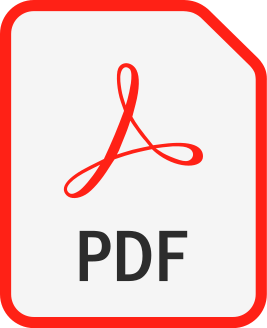 |
8. |
Pieczyska E.A., Staszczak M., Maj M., Tobushi H.♦, Hayashi S.♦, Investigation of thermal effects accompanying tensile deformation of Shape Memory Polymer PU-SMP,
Measurement Automation Monitoring, ISSN: 0032-4140, Vol.61, No.6, pp.203-205, 2015 Abstract: Experimental results of effects of thermomechanical couplings occurring in shape memory polymer subjected to tension are presented. Stress-strain curves were recorded by testing machine, while their related temperature changes were measured with infrared camera. The mechanical and thermal characteristics were used to investigate the polymer properties. Three various stages were distinguished during the deformation process. The first, elastic, is accompanied by a drop in the specimen temperature; the second, plastic, is associated with change of the material structure and the temperature increase; the third stage, related to the specimen rupture and damage mechanisms, is accompanied by the significant increase in temperature. Keywords: shape memory polymer, tension, thermomechanical coupling, temperature change, infrared camera Affiliations:
Pieczyska E.A. | - | IPPT PAN | Staszczak M. | - | IPPT PAN | Maj M. | - | IPPT PAN | Tobushi H. | - | Aichi Institute of Technology (JP) | Hayashi S. | - | SMP Technologies Inc. (JP) |
| 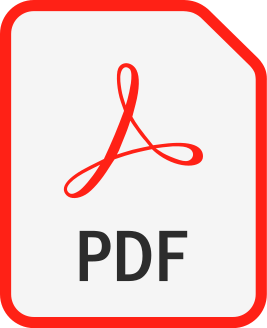 |
9. |
Dunić V.♦, Pieczyska E.A., Tobushi H.♦, Staszczak M., Slavković R.♦, Experimental and numerical thermo-mechanical analysis of shape memory alloy subjected to tension with various stress and strain rates,
SMART MATERIALS AND STRUCTURES, ISSN: 0964-1726, DOI: 10.1088/0964-1726/23/5/055026, Vol.23, pp.055026-1-11, 2014 Abstract: TiNi shape memory alloy (SMA) is experimentally and numerically investigated in tension tests under different loading rates. The thermomechanical behaviour of the SMA, related to the stress-induced martensitic transformation (SIMT) noticed during the experimental tests, is analysed and the observations are considered for numerical analysis. Initiation, development and saturation of the SIMT are monitored by a fast and sensitive infrared camera. The estimated temperature changes of the SMA sample, related to the exothermic martensitic forward and endothermic reverse transformation, have been analysed with the focus on the rate-dependent response and on the influence of the heat transfer on the mechanical behaviour. The effectively modified constitutive model, proposed by Lagoudas, is implemented in structural PAK finite element method (FEM) software and is thermomechanically coupled with the heat transfer FEM software in a partitioned approach. The experimental results are quantitatively and qualitatively reproduced by the numerical FEM model, which verifies the efficiency and accuracy of the proposed investigation method. Keywords: shape memory alloy, stressinduced martensitic transformation, modelling, TiNi, tension, infrared camera, temperature changes Affiliations:
Dunić V. | - | University of Kragujevac (XS) | Pieczyska E.A. | - | IPPT PAN | Tobushi H. | - | Aichi Institute of Technology (JP) | Staszczak M. | - | IPPT PAN | Slavković R. | - | University of Kragujevac (XS) |
| 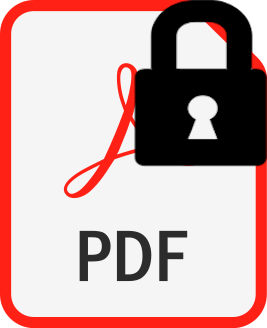 |
10. |
Takeda K.♦, Matsui R.♦, Tobushi H.♦, Pieczyska E.A., Transformation-Induced Relaxation and Stress Recovery of TiNi Shape Memory Alloy,
Materials, ISSN: 1996-1944, DOI: 10.3390/ma7031912, Vol.7, pp.1912-1926, 2014 Abstract: The transformation-induced stress relaxation and stress recovery of TiNi shape memory alloy (SMA) in stress-controlled subloop loading were investigated based on the local variation in temperature and transformation band on the surface of the tape in the tension test. The results obtained are summarized as follows. (1) In the loading process, temperature increases due to the exothermic martensitic transformation (MT) until the holding strain and thereafter temperature decreases while holding the strain constant, resulting in stress relaxation due to the MT; (2) In the unloading process, temperature decreases due to the endothermic reverse transformation until the holding strain and thereafter temperature increases while holding the strain constant, resulting in stress recovery due to the reverse transformation; (3) Stress varies markedly in the initial stage followed by gradual change while holding the strain constant; (4) If the stress rate is high until the holding strain in the loading and unloading processes, both stress relaxation and stress recovery are large; (5) It is important to take into account this behavior in the design of SMA elements, since the force of SMA elements varies even if the atmospheric temperature is kept constant. Keywords: shape memory alloy, superelasticity, titanium-nickel alloy, subloop, stress relaxation, stress recovery, martensitic transformation Affiliations:
Takeda K. | - | Aichi Institute of Technology (JP) | Matsui R. | - | Aichi Institute of Technology (JP) | Tobushi H. | - | Aichi Institute of Technology (JP) | Pieczyska E.A. | - | IPPT PAN |
| 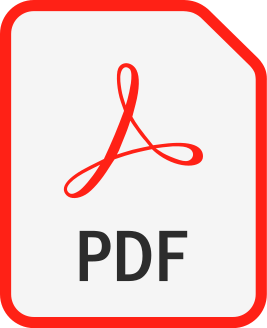 |
11. |
Pieczyska E.A., Maj M., Kowalczyk-Gajewska K., Staszczak M., Urbański L., Tobushi H.♦, Hayashi S.♦, Cristea M.♦, Mechanical and Infrared Thermography Analysis of Shape Memory Polyurethane,
Journal of Materials Engineering and Performance, ISSN: 1059-9495, DOI: 10.1007/s11665-014-0963-2, Vol.23, No.7, pp.2553-2560, 2014 Abstract: Multifunctional new material—polyurethane shape memory polymer (PU-SMP)—was subjected to tension carried out at room temperature at various strain rates. The influence of effects of thermomechanical couplings on the SMP mechanical properties was studied, based on the sample temperature changes, measured by a fast and sensitive infrared camera. It was found that the polymer deformation process strongly depends on the strain rate applied. The initial reversible strain is accompanied by a small drop in temperature, called thermoelastic effect. Its maximal value is related to the SMP yield point and increases upon increase of the strain rate. At higher strains, the stress and temperature significantly increase, caused by reorientation of the polymer molecular chains, followed by the stress drop and its subsequent increase accompanying the sample rupture. The higher strain rate, the higher stress, and temperature changes were obtained, since the deformation process was more dynamic and has occurred in almost adiabatic conditions. The constitutive model of SMP valid in finite strain regime was developed. In the proposed approach, SMP is described as a two-phase material composed of hyperelastic rubbery phase and elastic-viscoplastic glassy phase, while the volume content of phases is specified by the current temperature. Keywords: constitutive model, dynamic mechanical analysis, shape memory polyurethane, strain rate, temperature change, thermomechanical couplings Affiliations:
Pieczyska E.A. | - | IPPT PAN | Maj M. | - | IPPT PAN | Kowalczyk-Gajewska K. | - | IPPT PAN | Staszczak M. | - | IPPT PAN | Urbański L. | - | IPPT PAN | Tobushi H. | - | Aichi Institute of Technology (JP) | Hayashi S. | - | SMP Technologies Inc. (JP) | Cristea M. | - | Petru Poni Institute of Macromolecular Chemistry (RO) |
| 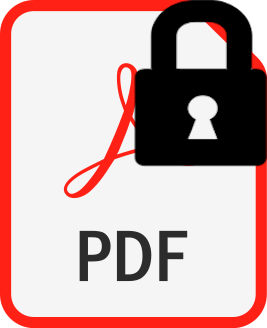 |
12. |
Pieczyska E.A., Staszczak M., Dunić V.♦, Slavković R.♦, Tobushi H.♦, Takeda K.♦, Development of Stress-Induced Martensitic Transformation in TiNi Shape Memory Alloy,
Journal of Materials Engineering and Performance, ISSN: 1059-9495, DOI: 10.1007/s11665-014-0959-y, Vol.23, No.7, pp.2505-2514, 2014 Abstract: TiNi shape memory alloy (SMA) was subjected to tension at strain-controlled test on quasistatic testing machine. The nucleation, development, and saturation of the stress-induced martensitic transformation were investigated, taking into account the obtained dependency of mechanical parameters and the specimen temperature changes measured by an infrared camera (IR). Three kinds of data obtained by the IR system were analyzed: the temperature distribution on the SMA sample surface, the temperature changes derived as average from the chosen sample area, and the temperature profiles obtained along the sample length. The temperature distribution shows nucleation of the transformation process and a creation of the transformation bands. The average temperature reflects the effects of thermomechanical coupling, accompanying exothermic martensitic forward and endothermic reverse transformation. The temperature profiles revealed the temperature difference between the band and the rest of the sample. The experimental results were supported with finite element method numerical analysis (FEM). The FEM software components for structural and heat transfer problems, coupled in partitioned approach, were used for thermomechanical analysis. Keywords: finite element modeling, infrared camera, material testing, martensitic transformation, TiNi shape memory alloy, tension, thermomechanical couplings Affiliations:
Pieczyska E.A. | - | IPPT PAN | Staszczak M. | - | IPPT PAN | Dunić V. | - | University of Kragujevac (XS) | Slavković R. | - | University of Kragujevac (XS) | Tobushi H. | - | Aichi Institute of Technology (JP) | Takeda K. | - | Aichi Institute of Technology (JP) |
| 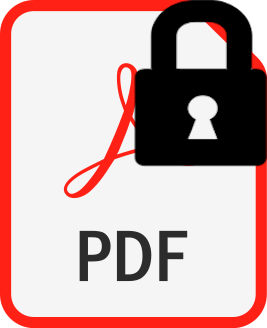 |
13. |
Pieczyska E.A., Kowalczyk-Gajewska K., Maj M., Staszczak M., Tobushi H.♦, Thermomechanical investigation of TiNi shape memory alloy and PU shape memory polymer subjected to cyclic loading,
Procedia Engineering, ISSN: 1877-7058, DOI: 10.1016/j.proeng.2014.06.264, Vol.74, pp.287-292, 2014 Abstract: In applications to sensors, actuators, guide wires, special grips for handicapped people, a shape memory alloy (SMA) or shape memory polymer (SMP) are used as working elements that perform cyclic motions. In order to evaluate the reliability of the shape memory materials (SMM), cycling and fatigue deformation properties are investigated. Since the SMM are very sensitive to temperature, not only mechanical properties but also their related temperature changes accompanying the deformation process should be taken into account. The presented paper embraces experimental investigation of effects of thermomechanical couplings occurring in shape memory alloy and shape memory polymer subjected to various kinds of cycling loading. The deformation was carried out on MTS 858 Testing machine. The strain was measured by a mechanical extensometer, so the stress-strain characteristics were elaborated with high accuracy. Furthermore, a fast and sensitive FLIR Co Phoenix infrared (IR) measurement system was used in order to record infrared radiation from the sample surface. It enables obtaining temperature distribution of the sample as a function of the deformation parameters. For each strain cycle, an increase in temperature during the loading and the temperature decrease during the unloading processes was observed. It was found that the temperature increment recorded during the cyclic deformation depends on the strain rate, the kind of the material and the test conditions. The higher the strain rate the higher the stress and temperature changes were obtained, since the deformation process was more dynamic and has occurred in almost adiabatic conditions. It was shown that various deformation mechanisms are active during various loading stages. Keywords: shape memory alloy, shape memory polymer, cyclic deformation, thermomechanical coupling, infrared camera Affiliations:
Pieczyska E.A. | - | IPPT PAN | Kowalczyk-Gajewska K. | - | IPPT PAN | Maj M. | - | IPPT PAN | Staszczak M. | - | IPPT PAN | Tobushi H. | - | Aichi Institute of Technology (JP) |
| 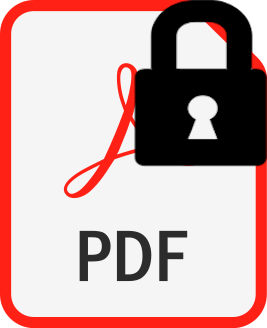 |
14. |
Pieczyska E.A., Tobushi H.♦, Kulasiński K., Development of transformation bands in TiNi SMA for various stress and strain rates studied by a fast and sensitive infrared camera,
SMART MATERIALS AND STRUCTURES, ISSN: 0964-1726, DOI: 10.1088/0964-1726/22/3/035007, Vol.22, No.3, pp.035007-1-8, 2013 Abstract: TiNi shape memory alloy (SMA) was subjected to tension at various strain rates for stress- and strain-controlled tests. The nucleation, development and saturation of the stress-induced martensitic transformation were investigated, based on the specimen temperature changes, measured by a fast and sensitive infrared camera. It was found that the initial, macroscopically homogeneous phase transformation occurs at the same stress level for all strain rates applied, regardless of the loading manner, while the stress of the localized transformation increases with the strain rate. At higher strain rate, a more dynamic course of the transformation process was observed, revealed in the creation of numerous fine transformation bands. An inflection point was noticed on the stress–strain curve, dividing the transformation range into two stages: the first heterogeneous, where transformation bands nucleate and evolve throughout the sample; the second, where the bands overlap, related to significant temperature increase and an upswing region of the curve. In the final part of the SMA loading a decrease of the average sample temperature revealed the saturation stage of the transformation. It was also observed that nucleation of the localized martensitic forward transformation takes place in the weakest area of the sample in both approaches, whereas the reverse transformation always initiates in its central part. Keywords: shape memory alloy, various strain rates, stress- and strain-controlled tests, stress-induced martensitic transformation, fast and sensitive infrared camera, transformation bands, localized martensitic forward transformation, reverse transformation Affiliations:
Pieczyska E.A. | - | IPPT PAN | Tobushi H. | - | Aichi Institute of Technology (JP) | Kulasiński K. | - | IPPT PAN |
| 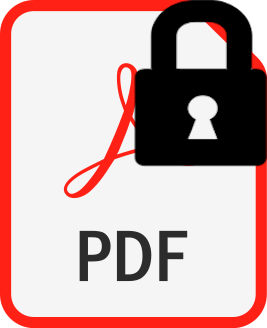 |
15. |
Tobushi H.♦, Pieczyska E.A., Miyamoto K.♦, Mitsui K.♦, Torsional deformation characteristics of TiNi SMA tape and application to rotary actuator,
JOURNAL OF ALLOYS AND COMPOUNDS, ISSN: 0925-8388, DOI: 10.1016/j.jallcom.2011.10.108, Vol.577S, pp.S745-S748, 2013 Abstract: In order to develop novel shape memory actuators, the torsional deformation of a shape memory alloy (SMA) tape and the actuator models driven by the tape were investigated. The results obtained can be summarized as follows. In the SMA tape subjected to torsion, the martensitic transformation appears along the edge of the tape due to elongation of the edge of the tape and grows to the central part. The fatigue life in both the pulsating torsion and the alternating torsion is expressed by the unified relationship of the dissipated work in each cycle. Based on an opening and closing door model and a solar-powered active blind model, the two-way rotary driving actuator with a small and simple mechanism can be developed by using torsion of the SMA-tape. Keywords: Shape memory alloy, Actuator, Two-way, Tape, Torsion, Fatigue Affiliations:
Tobushi H. | - | Aichi Institute of Technology (JP) | Pieczyska E.A. | - | IPPT PAN | Miyamoto K. | - | Churyo Engineering Co. (JP) | Mitsui K. | - | Masupuro Denkoh Corp. (JP) |
| 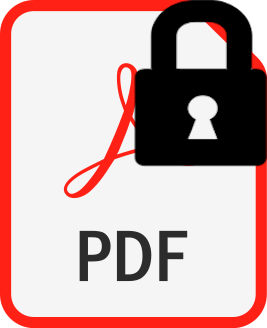 |
16. |
Takeda K.♦, Mitsui K.♦, Tobushi H.♦, Levintant-Zayonts N., Kucharski S., Influence of nitrogen ion implantation on deformation and fatigue properties of TiNi shape memory alloy wire,
ARCHIVES OF MECHANICS, ISSN: 0373-2029, Vol.65, No.5, pp.391-405, 2013 Abstract: A shape memory alloy (SMA) is expected to be applied as intelligent material since it shows the unique characteristics of the shape memory effect and superelasticity. Most SMA elements, with these characteristics, perform cyclic motions. In these cases, fatigue of SMA is one of the important properties in view of evaluating functional characteristics. The fatigue properties are complex since they depend on stress, strain, temperature and time. If SMA is implanted by high energy ions, the thermomechanical properties may change, resulting in long fatigue life. In the present study, the nitrogen ion implantation was applied to modify TiNi SMA wire surface and the influence of implantation treatment on the tensile deformation and bending fatigue properties was investigated. Keywords: shape memory effect, titanium-nickel alloy, nitrogen ion implantation, superelasticity, fatigue Affiliations:
Takeda K. | - | Aichi Institute of Technology (JP) | Mitsui K. | - | Masupuro Denkoh Corp. (JP) | Tobushi H. | - | Aichi Institute of Technology (JP) | Levintant-Zayonts N. | - | IPPT PAN | Kucharski S. | - | IPPT PAN |
| 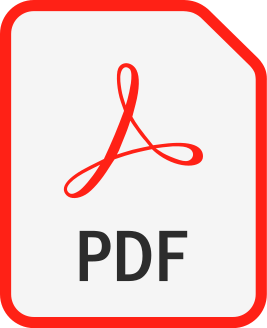 |
17. |
Takeda K.♦, Matsui R.♦, Tobushi H.♦, Pieczyska E.A., Creep and creep recovery under stress-controlled subloop loading in TiNi shape memory alloy,
ARCHIVES OF MECHANICS, ISSN: 0373-2029, Vol.65, No.5, pp.429-444, 2013 Abstract: If a shape memory alloy (SMA) is subjected to the subloop loading under the stress-controlled condition, creep and creep recovery can appear based on the martensitic transformation. In the design of SMA elements, these deformation properties are important since the deflection of SMA elements can change under constant load. The conditions for the progress of the martensitic transformation are discussed based on the kinetics of the martensitic transformation for the SMA. The creep deformation properties are investigated experimentally for TiNi SMA. The creep strain rate increases in proportion to the martensitic transformation strain; the creep recovery strain rate increases in proportion to the reverse transformation strain. Keywords: shape memory alloy, superelasticity, subloop, transformation band, creep, creep recovery, strain rate, local deformation Affiliations:
Takeda K. | - | Aichi Institute of Technology (JP) | Matsui R. | - | Aichi Institute of Technology (JP) | Tobushi H. | - | Aichi Institute of Technology (JP) | Pieczyska E.A. | - | IPPT PAN |
| 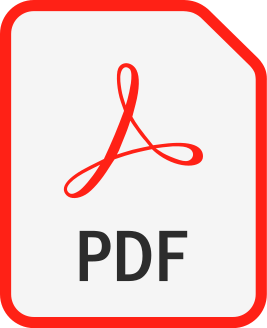 |
18. |
Staszczak M., Pieczyska E.A., Maj M., Urbański L., Tobushi H.♦, Hayashi S.♦, Właściwości mechaniczne oraz zmiany temperatury polimeru z pamięcią kształtu w procesie rozciągania,
POMIARY AUTOMATYKA KONTROLA, ISSN: 0032-4140, Vol.59, No.9, pp.1002-1005, 2013 Abstract: This paper presents experimental evaluation of a new polyurethane shape memory polymer (PU-SMP) produced by SMP Technologies Inc. It discusses mechanical characteristics and temperature changes of the SMP specimens subjected to tension test performed at room temperature with various strain rates. Basing on the mechanical data and the relevant temperature changes, we have studied the thermomechanical properties of the PU-SMP and influence of the strain rate on the strain localization behavior. Finally, we have identified the material parameters for the one-dimensional rheological model of the SMP. Keywords: shape memory polyurethane, tension test, dynamic mechanical analysis, infrared camera, temperature change, thermomechanical properties, rheological model Affiliations:
Staszczak M. | - | IPPT PAN | Pieczyska E.A. | - | IPPT PAN | Maj M. | - | IPPT PAN | Urbański L. | - | IPPT PAN | Tobushi H. | - | Aichi Institute of Technology (JP) | Hayashi S. | - | SMP Technologies Inc. (JP) |
| 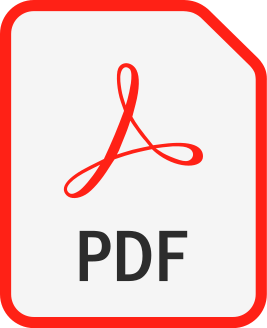 |
19. |
Pieczyska E.A., Tobushi H.♦, Kulasiński K., Takeda K.♦, Impact of Strain Rate on Thermomechanical Coupling Effects in TiNi SMA Subjected to Compression,
MATERIALS TRANSACTIONS, ISSN: 1345-9678, DOI: 10.2320/matertrans.M2012212, Vol.53, No.11, pp.1905-1909, 2012 Abstract: In this study, the thermomechanical coupling effects accompanying stress-induced martensitic transformation in TiNi shape memory alloy subjected to compression test were investigated. The mechanical characteristics were elaborated and the temperature changes related to the exothermic martensitic forward transformation and the endothermic reverse one were measured in a contactless manner by a fast and sensitive infrared camera. The obtained temperature changes of the specimen depend on the strain rate applied. At higher strain rate, greater temperature changes were observed, because the heat flow to the surroundings was lower and the process was closer to adiabatic conditions. The temperature changes of the shape memory alloy significantly influence its stressstrain characteristics. Moreover, the energy dissipated during a compression cycle was calculated for various strain rates. The study revealed that both the loading work and recoverable strain energy increase with increasing strain rate, while the dissipated energy fraction decreases.
Keywords: shape memory alloy, compression test, exothermic/endothermic transformation, infrared camera, energy dissipation Affiliations:
Pieczyska E.A. | - | IPPT PAN | Tobushi H. | - | Aichi Institute of Technology (JP) | Kulasiński K. | - | IPPT PAN | Takeda K. | - | Aichi Institute of Technology (JP) |
| 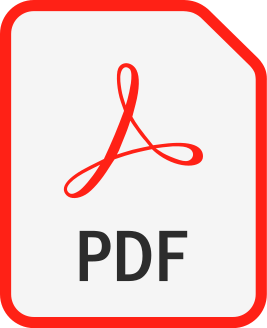 |
20. |
Takeda K.♦, Tobushi H.♦, Miyamoto K.♦, Pieczyska E.A., Superelastic Deformation of TiNi Shape Memory Alloy Subjected to Various Subloop Loadings,
MATERIALS TRANSACTIONS, ISSN: 1345-9678, DOI: 10.2320/matertrans.M2011288, Vol.53, No.1, pp.217-223, 2012 Abstract: This paper investigates the superelastic deformation behaviors of a TiNi shape-memory alloy (SMA) tape subjected to various subloop loadings in relation to local temperature variations and observed surface changes during a tension test. The results obtained are: (1) Upper and lower stress plateaus appear during loading and unloading accompanying the spreading and shrinking of the stress-induced martensitic transformation (SIMT) bands. In the case of unloading from the upper stress plateau under low stress rate, strain increases due to the spreading of the SIMT bands at the start of the unloading. (2) If stress at the upper stress plateau is held constant, creep deformation appears with the spread of the SIMT bands. The volume fraction in the martensitic phase increases in proportion to the increase in strain. (3) Where the strain is made to vary at the stress plateaus during loading or unloading, a return point memory effect can be seen in the reloading stress-strain curve. The spreading or shrinking of the SIMT bands starts from the boundary of the previous SIMT bands remaining from the preceding process. (4) The inclination angle of the SIMT band boundaries to the tensile axis of the tape is 33° for an aspect ratio of 5. The inclination angle is 42° in the center of the tape and 37° in the vicinity of the end secured by the grip, for an aspect ratio of 10.
Keywords: shape memory alloy, superelasticity, titanium-nickel alloy, subloop, transformation band, creep deformation, local deformation Affiliations:
Takeda K. | - | Aichi Institute of Technology (JP) | Tobushi H. | - | Aichi Institute of Technology (JP) | Miyamoto K. | - | Churyo Engineering Co. (JP) | Pieczyska E.A. | - | IPPT PAN |
| 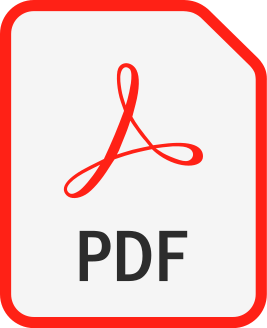 |
21. |
Pieczyska E.A., Tobushi H.♦, Takeda K.♦, Stróż D.♦, Ranachowski Z., Kulasiński K., Kúdela Jr S.♦, Luckner J., Martensite transformation bands studied in TiNi shape memory alloy by infrared and acoustic emission techniques,
KOVOVE MATERIALY-METALLIC MATERIALS, ISSN: 0023-432X, Vol.50, pp.309-318, 2012 Abstract: TiNi shape memory alloy (SMA) specimens have been subjected to tension carried out at various strain rates. The goal was to investigate a nucleation and development of the stressinduced martensitic transformation by infrared (IR) and acoustic emission (AE) techniques. Therefore, both the infrared radiation and acoustic emission data were recorded using a fast infrared camera and acoustic emission set-up, respectively. It has been shown that the initial, macroscopically homogeneous transformation initiates in the elastic stage of the deformation even before the stress-strain curve knee and formation of the localized transformation bands. It has also been found that the homogeneous transformation occurs at similar stress level for all strain rates applied, while the localized martensitic transformation depends on the strain rate. Nucleation and development of the localized transformation bands, detected by the infrared camera, were confirmed by acoustic emission technique. The differences between the IR and AE activities were recorded during the TiNi SMA loading and unloading process, manifesting different dynamics of the stress-induced martensitic forward and reverse transformation. Keywords: shape memory alloy, TiNi, superelasticity, martensitic transformation, tension test, acoustic emission Affiliations:
Pieczyska E.A. | - | IPPT PAN | Tobushi H. | - | Aichi Institute of Technology (JP) | Takeda K. | - | Aichi Institute of Technology (JP) | Stróż D. | - | other affiliation | Ranachowski Z. | - | IPPT PAN | Kulasiński K. | - | IPPT PAN | Kúdela Jr S. | - | Institute of Materials and Machine Mechanics, Slovak Academy of Sciences (SK) | Luckner J. | - | IPPT PAN |
| 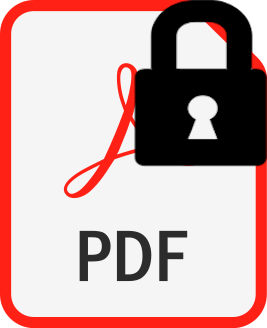 |
22. |
Takeda K.♦, Tobushi H.♦, Pieczyska E.A., Transformation-Induced Creep and Creep Recovery of Shape Memory Alloy,
Materials, Vol.5, pp.909-921, 2012 | 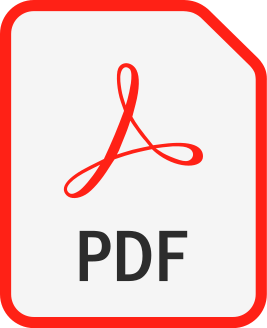 |
23. |
Tobushi H.♦, Hayashi S.♦, Pieczyska E.A., Date K.♦, Nishimura Y.♦, Three-way actuation of shape memory composite,
ARCHIVES OF MECHANICS, ISSN: 0373-2029, Vol.63, No.5-6, pp.443-457, 2011 | 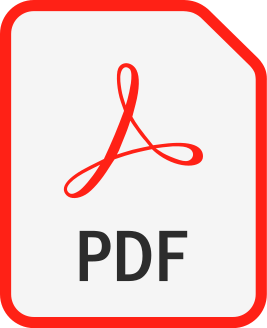 |
24. |
Pieczyska E.A., Tobushi H.♦, TiNi shape memory alloy tension at various temperatures - infrared imaging of shape memory effect and pseudoelasticity,
MECHANICS AND CONTROL, ISSN: 2083-6759, Vol.30, No.1, pp.20-26, 2011 | 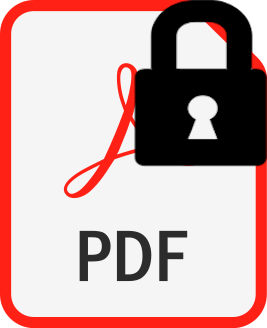 |
25. |
Takeda K.♦, Tobushi H.♦, Miyamoto K.♦, Pieczyska E.A., Subloop Superelastic Deformation of TiNi Shape Memory Alloy,
TRANSACTIONS OF THE JAPAN SOCIETY OF MECHANICAL ENGINEERS Series A , ISSN: 1884-8338, DOI: 10.1299/kikaia.77.1509, Vol.77, No.781, pp.1509-1517, 2011 Abstract: The various subloop behaviors for the superelastic deformation of TiNi shape memory alloy were investigated based on the local temperature variation and the surface observation in the tension test. The results obtained are summarized as bellows. (1) The upper and lower stress plateaus during loading and unloading appear accompanying the progress and reduction of the martensitic transformation (MT) band, respectively. In the case of unloading from the upper stress plateau under low stress rate, strain increases due to the progress of the MT band in the initial stage of unloading. (2) If stress is held constant in the upper stress plateau, creep deformation appears. The creep deformation appears based on the progress of the MT band. The volume fraction of the martensitic phase increases in proportion to an increase in strain. (3) If the transformation strain varies in the stress plateau during loading and unloading, the return point memory appears in the reloading stress-strain curve. The progress and reduction of the MT band start from the boundary of the MT band which has appeared in the preceding process. (4) The angle of boundary of the MT band inclined to the tensile axis is 33° for an aspect ratio of 5 and 42° in the central part of the specimen and 37° in the vicinity of the gripping part for an aspect ratio of 10. Keywords: Shape Memory Alloy, Superelasticity, Titanium-Nickel Alloy, Subloop, Transformation Band, Creep Deformation Affiliations:
Takeda K. | - | Aichi Institute of Technology (JP) | Tobushi H. | - | Aichi Institute of Technology (JP) | Miyamoto K. | - | Churyo Engineering Co. (JP) | Pieczyska E.A. | - | IPPT PAN |
| 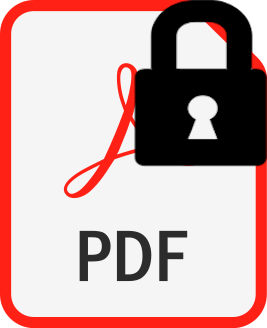 |
26. |
Tobushi H.♦, Hayashi S.♦, Pieczyska E.A., Date K.♦, Nishimura Y.♦, Three-Way Shape Memory Composite Actuator,
MATERIALS SCIENCE FORUM, ISSN: 0255-5476, Vol.674, pp.225-230, 2011 | 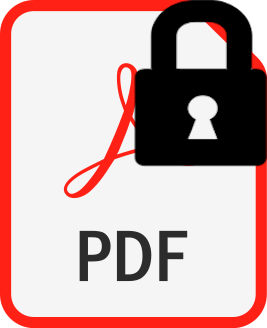 |
27. |
Tobushi H.♦, Pieczyska E.A., Miyamoto K.♦, Mitsui K.♦, Shape-Memory Alloy Thin Strip Rotary Actuator,
MATERIALS SCIENCE FORUM, ISSN: 0255-5476, Vol.674, pp.219-224, 2011 | 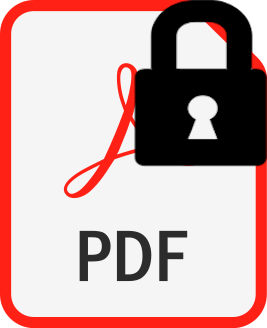 |
28. |
Pieczyska E.A., Tobushi H.♦, Date K.♦, Miyamoto K.♦, Torsional deformation and fatigue properties of TiNi SMA thin strip for rotary driving element,
JSME INTERNATIONAL JOURNAL SERIES A-SOLID MECHANICS AND MATERIAL ENGINEERING, ISSN: 1344-7912, Vol.4, No.8, pp.1306-1314, 2010 | 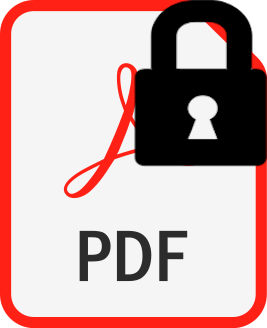 |
29. |
Tobushi H.♦, Pieczyska E.A., Nowacki W.K., Date K.♦, Miyamoto K.♦, Two-way rotary shape memory alloy thin strip actuator,
JOURNAL OF THEORETICAL AND APPLIED MECHANICS, ISSN: 1429-2955, Vol.48, No.4, pp.1043-1056, 2010 Abstract: In order to develop a two-way rotary shape memory alloy thin strip actuator, the torsional deformation and fatigue properties of a TiNi SMA thin strip were investigated. The results obtained are summarized as follows. (1) In the SMA thin strip subjected to torsion, the MT appears along the edge of the strip due to elongation of the edge of the strip and grows to the central part. (2) The number of cycles to failure decreases with an increase in the maximum angle of twist in torsion fatigue. The fatigue life in pulsating torsion is longer than that in alternating torsion by five times. The fatigue limit exists in a certain value of dissipated work of the strip in each cycle. (3) Based on the two-way motion of a lifting actuator model driven by two kinds of SMA thin strip, it is confirmed that the two-way rotary actuator with a small and simple mechanism can be developed by using the SMA thin strips. Keywords: shape memory alloy, thin strip, torsion, cyclic deformation, fatigue, rotary actuator, two-way motion Affiliations:
Tobushi H. | - | Aichi Institute of Technology (JP) | Pieczyska E.A. | - | IPPT PAN | Nowacki W.K. | - | IPPT PAN | Date K. | - | Ochiai Nexus Co. (JP) | Miyamoto K. | - | Churyo Engineering Co. (JP) |
| 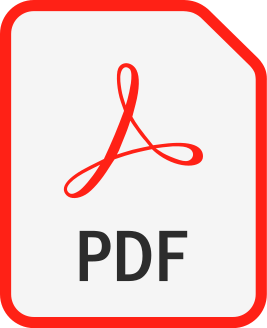 |
30. |
Pieczyska E.A., Gadaj S.P., Nowacki W.K., Luckner J., Tobushi H.♦, Martensite and reverse transformation during simple shear of niti shape memory alloy,
STRAIN, ISSN: 0039-2103, Vol.45, pp.93-100, 2009 | 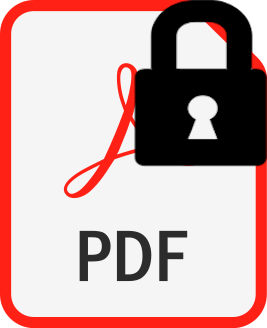 |
31. |
Tobushi H.♦, Pieczyska E.A., Ejiri Y.♦, Sakuragi T.♦, Thermomechanical properties of shape-memory alloy and polymer and their composite,
MECHANICS OF ADVANCED MATERIALS AND STRUCTURES, ISSN: 1537-6494, DOI: 10.1080/15376490902746954, Vol.16, pp.236-247, 2009 Abstract: The shape memory effect and superelasticity appear in shape memory alloy (SMA). The large amount of strain by more than several hundreds percent can be recovered in shape memory polymer (SMP). The shape recovery and shape fixity can be used in SMP elements. These characteristics of shape memory materials (SMMs) can be applied to intelligent elements in various fields. In order to use these characteristics and design the SMM elements properly, it is important to understand the thermomechanical properties of SMAs and SMPs. The deformation behaviors of SMMs differ depending on the thermomechanical loading conditions. The main factors which affect these properties are strain rate, stress rate, temperature, subloop loading, temperature-controlled condition, strain holding condition and cyclic loading. In the present paper, the thermomechanical properties of TiNi shape memory alloy, polyurethane-shape memory polymer and their composite are discussed. Keywords: shape memory alloy, shape memory polymer, composite, cyclic loading, strain rate, fatigue Affiliations:
Tobushi H. | - | Aichi Institute of Technology (JP) | Pieczyska E.A. | - | IPPT PAN | Ejiri Y. | - | other affiliation | Sakuragi T. | - | Aichi Institute of Technology (JP) |
| 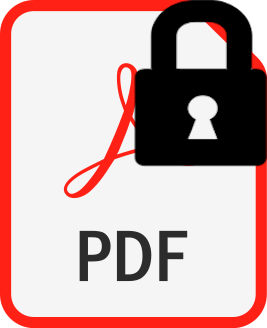 |
32. |
Tobushi H.♦, Pieczyska E.A., Nowacki W.K., Sakuragi T.♦, Sugimoto Y.♦, Torsional deformation and rotary driving characteristics of SMA thin strip,
ARCHIVES OF MECHANICS, ISSN: 0373-2029, Vol.61, No.3-4, pp.241-257, 2009 Abstract: The torsional deformation properties of a TiNi shape-memory alloy thin strip were investigated. The results obtained are summarized as follows. (1) The martensitic transformation starts at the edge of the thin strip. (2) The torsional deformation properties change slightly under thermomechanical cycling. (3) The fatigue life in pul- sating torsion is longer than that in alternating torsion. (4) A simple rotary driving element can be developed by using the SMA thin strip.
Keywords: shape memory alloy, thin strip, torsion, cyclic deformation, fatigue, rotary driving element Affiliations:
Tobushi H. | - | Aichi Institute of Technology (JP) | Pieczyska E.A. | - | IPPT PAN | Nowacki W.K. | - | IPPT PAN | Sakuragi T. | - | Aichi Institute of Technology (JP) | Sugimoto Y. | - | Aichi Institute of Technology (JP) |
| 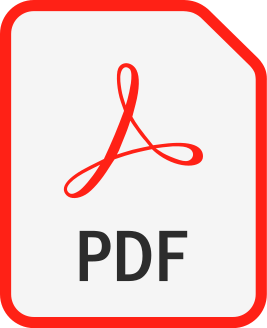 |
33. |
Tobushi H.♦, Pieczyska E.A., Nowacki W.K., Sugimoto Y.♦, SMA thin strip for rotary-driving element,
SOLID STATE PHENOMENA, ISSN: 1012-0394, DOI: 10.4028/www.scientific.net/SSP.154.47, Vol.154, pp.47-52, 2009 Abstract: If a shape-memory alloy (SMA) thin strip is applied as an element subjected to torsion, a rotary driving element with a simple mechanism can be developed. The torsion tests were carried out for the SMA thin strip. Torque and recovery torque, both increase in proportion to the angle of twist and temperature. The recoverable strain energy increases in proportion to temperature. The dissipated work decreases slightly with an increase in temperature. A means of opening and closing a door with an element driven by an SMA thin strip is demonstrated. Keywords: Rotary Driving Element, Shape Memory Alloy Actuator, Strain Energy, Thin Strip, Torsion Affiliations:
Tobushi H. | - | Aichi Institute of Technology (JP) | Pieczyska E.A. | - | IPPT PAN | Nowacki W.K. | - | IPPT PAN | Sugimoto Y. | - | Aichi Institute of Technology (JP) |
| 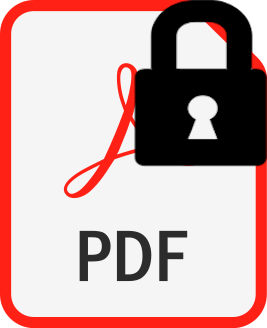 |
34. |
Pieczyska E.A., Nowacki W.K., Tobushi H.♦, Hayashi S.♦, Thermomechanical properties of shape memory polymer subjected to tension in various conditions,
Quantitative InfraRed Thermography Journal, ISSN: 1768-6733, Vol.6, No.2, pp.189-205, 2009 Abstract: Thermomechanical and functional properties of shape memory polyurethane are presented. A background of the polymer shape memory effects is described. Elastic modulus at various temperatures and the polyurethane parameters important for the practical applications, called shape fixity and shape recovery, are derived. Taking advantages from the high quality testing machine and infrared camera, mechanical characteristics and temperature changes of the shape memory polyurethane specimens subjected to tension test carried out in various conditions are clarified and analyzed. Stress-strain curves and the relevant temperature changes are recorded both in the elastic and the plastic ranges of deformation. A significant value of a thermoelastic effect is observed. Taking into account the obtained experimental data from the polyurethane tension tests performed at room temperature, followed by the heating above its glass transition temperature, the shape memory polyurethane properties are studied. Keywords: shape memory polyurethane, glass transition temperature, tension, mechanical characteristics, infrared camera, temperature change, thermoelastic effect, localization Affiliations:
Pieczyska E.A. | - | IPPT PAN | Nowacki W.K. | - | IPPT PAN | Tobushi H. | - | Aichi Institute of Technology (JP) | Hayashi S. | - | SMP Technologies Inc. (JP) |
| 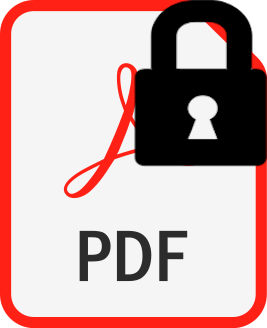 |
35. |
Pieczyska E.A., Tobushi H.♦, Nowacki W.K., Gadaj S.P., Sakuragi T.♦, Subloop deformation behavior of TiNi shape memory alloy subjected to stress-controlled loadings,
MATERIALS TRANSACTIONS, ISSN: 1345-9678, Vol.48, No.10, pp.2679-2686, 2007 Abstract: The main characteristics which appear in shape memory alloys (SMAs) are the shape memory effect and superelasticity. In applications of SMAs, the thermomechanical properties of SMAs are most important. The return-point memory does not appear under the stress-controlled conditions. Creep and stress relaxation can be induced due to the phase transformation in the subloop loading under the stress-controlled conditions. In order to design the SMA elements properly, it is important to understand the influence of the thermomechanical loading conditions on the nucleation and progress of the phase transformation and the corresponding deformation behaviors. In the present paper, the conditions for the nucleation and progress of the phase transformation are investigated for SMAs subjected to the subloop loadings under the stress-controlled conditions. The uniaxial tension tests for the TiNi SMAs were carried out in the superelastic region under the various thermomechanical loading conditions. The thermomechanical conditions for the progress of the phase transformation are discussed in the subloop loading under the stresscontrolled conditions. Strain increases during unloading and decreases during reloading under the stress-controlled subloop loading. These pseudoviscoelastic behaviors are important for the precise control of SMA elements. Keywords: shape-memory alloy, titanium-nickel alloy, subloop, superelasticity, creep, stress relaxation, neutral loading Affiliations:
Pieczyska E.A. | - | IPPT PAN | Tobushi H. | - | Aichi Institute of Technology (JP) | Nowacki W.K. | - | IPPT PAN | Gadaj S.P. | - | IPPT PAN | Sakuragi T. | - | Aichi Institute of Technology (JP) |
| 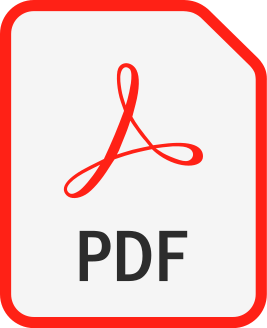 |
36. |
Pieczyska E.A., Nowacki W.K., Sakuragi T.♦, Tobushi H.♦, Superelastic deformation properties of TiNi shape memory alloy,
KEY ENGINEERING MATERIALS, ISSN: 1662-9795, DOI: 10.4028/www.scientific.net/KEM.340-341.1211, Vol.340-341, pp.1211-1216, 2007 Abstract: The characteristics of energy storage and dissipation in TiNi shape memory alloys were investigated experimentally based on the superelastic properties under various thermomechanical loading conditions. The results obtained can be summarized as follows. (1) The recoverable strain energy increases in proportion to the rise in temperature, but the dissipated work per unit volume depends slightly on temperature. In the case of low strain rates, the recoverable strain energy and dissipated work do not depend on both the strain rate and the temperature-controlled condition. (2) In the case of high strain rates, while the recoverable strain energy decreases and the dissipated work increases in proportion to the rise in strain rate under the temperature-controlled condition, the recoverable strain energy increases and the dissipated work decreases under the temperatureuncontrolled condition. Affiliations:
Pieczyska E.A. | - | IPPT PAN | Nowacki W.K. | - | IPPT PAN | Sakuragi T. | - | Aichi Institute of Technology (JP) | Tobushi H. | - | Aichi Institute of Technology (JP) |
| 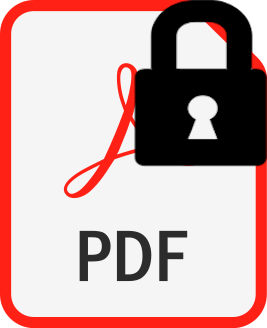 |
37. |
Pieczyska E.A., Gadaj S.P., Nowacki W.K., Tobushi H.♦, Superelastic deformation behaviors based on phase transformation bands in TiNi shape memory alloy,
MATERIALS TRANSACTIONS, ISSN: 1345-9678, Vol.47, No.3, pp.670-676, 2006 Abstract: Properties and characteristics of superelastic deformation behavior based on Lu¨ders-Like phase transformation bands in TiNi shape memory alloy (SMA) are presented. Temperature distributions accompanying the stress-induced phase transformations in the SMA are found using the infrared technique and employed for the investigation into nucleation and further development of the bands of martensitic and reverse transformations. Based on the temperature and the relevant mechanical characteristics it is noticed that just after crossing a certain threshold stress, narrow bands of considerably higher temperature, about 8K, corresponding to the martensitic phase, appear starting from the central part of the specimen and developing towards the both specimen borders. A few such bands parallel to each other occur at higher stresses and move towards the specimen grips, as well as their next generation, developing in almost perpendicular direction. The heterogeneous field of the temperature distribution was observed also during the unloading process, while the reverse transformation occurred, also inhomogeneous and related to the significant temperature decrease. Based on the tests carried out with various strain rates, an influence of the strain rate on the mechanical behavior was presented. Thermomechanical aspects of the martensitic and the reverse transformations were discussed. Keywords: superelastic deformation, shape memory alloy, phase transformation bands, temperature change, infrared camera Affiliations:
Pieczyska E.A. | - | IPPT PAN | Gadaj S.P. | - | IPPT PAN | Nowacki W.K. | - | IPPT PAN | Tobushi H. | - | Aichi Institute of Technology (JP) |
| 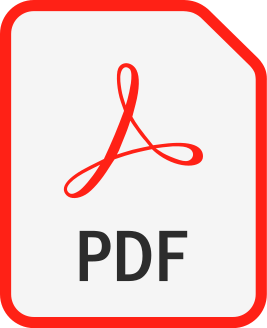 |
38. |
Pieczyska E.A., Gadaj S.P., Nowacki W.K., Tobushi H.♦, Phase-transformation fronts evolution for strain- and stress- controlled tension tests in TiNi Shape Memory Alloy,
EXPERIMENTAL MECHANICS, ISSN: 0014-4851, Vol.46, pp.531-542, 2006 Abstract: Nucleation and development of phase transformation fronts in TiNi shape memory alloy subjected to the stress- and strain-controlled tension tests were investigated. A thermovision camera was applied to register the distribution of infrared radiation emitted by the specimen and to find its temperature variations. During the loading, narrow bands of considerably higher temperature corresponding to the martensitic phase, starting from the central part of the specimen and developing towards the specimen grips, under both approaches, were registered. The inclined bands of heterogeneous temperature distribution were observed also during the unloading process of the SMA, while the reverse transformation accompanied by temperature decrease took place. Thermomechanical aspects of martensitic and reverse transformations for various strain rates were analyzed under both stress- and strain-controlled tests. Keywords: Shape memory alloy, Martensitic transformation, Phase transformation front, Temperature change, Stress-controlled test, Strain-controlled test, Infrared thermography Affiliations:
Pieczyska E.A. | - | IPPT PAN | Gadaj S.P. | - | IPPT PAN | Nowacki W.K. | - | IPPT PAN | Tobushi H. | - | Aichi Institute of Technology (JP) |
| 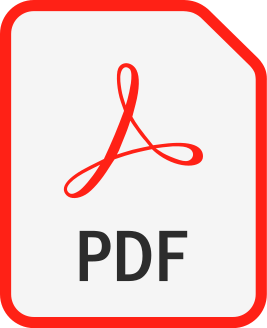 |
39. |
Pieczyska E.A., Gadaj S.P., Nowacki W.K., Tobushi H.♦, Stress relaxation during superelastic behavior of TiNi shape memory alloy,
INTERNATIONAL JOURNAL OF APPLIED ELECTROMAGNETICS AND MECHANICS, ISSN: 1383-5416, Vol.23, pp.3-8, 2006 | |
40. |
Pieczyska E.A., Gadaj S.P., Nowacki W.K., Hoshito K.♦, Makino Y.♦, Tobushi H.♦, Characteristics of energy storage and dissipation in TiNi shape memory alloy,
SCIENCE AND TECHNOLOGY OF ADVANCED MATERIALS, ISSN: 1468-6996, Vol.6, No.8, pp.889-894, 2005 Abstract: The characteristics of energy storage and dissipation in TiNi shape memory alloys were investigated experimentally based on the superelastic properties under various thermomechanical loading conditions. The influence of strain rate, cyclic loading and temperature-controlled condition on the characteristics of energy storage and dissipation of the material was investigated. Temperature on the surface of the material was observed and the influence of variation in temperature on the characteristics was clarified. The results obtained can be summarized as follows. (1) In the case of low strain rate, the stress plateaus appear on the stress-strain curves due to the martensitic transformation and the reverse transformation during loading and unloading. In the case of high strain rate, the slopes of the stress–strain curves are steep in the phase-transformation regions during loading and unloading. The recoverable strain energy per unit volume increases in proportion to temperature, but the dissipated work per unit volume depends slightly on temperature. In the case of low strain rate, the recoverable strain energy and dissipated work do not depend on both strain rate and the temperature-controlled condition. (2) In the case of high strain rate, while the recoverable strain energy density decreases and dissipated work density increases in proportion to strain rate under the temperature-controlled condition, the recoverable strain energy density increases and dissipated work density decreases under the temperature-uncontrolled condition. In the case of the temperature-uncontrolled condition, temperature varies significantly due to the martensitic transformation and therefore the characteristics of energy storage and dissipation differ from these under the temperature-controlled condition. (3) In the case of cyclic loading, both the recoverable strain energy and dissipated work decrease in the early 20 cycles, but change slightly thereafter. (4) The influence of strain rate, cyclic loading and the environment on the characteristics of energy storage and dissipation is important to be considered in the design of shape memory alloy elements. q 2005 Elsevier Ltd. All rights reserved. Keywords: Shape memory ally; Superelasticity; Energy storage; Energy dissipation; Damping; Strain rate; Cyclic deformation; Titanium–nickel alloy; Environment Keywords: Shape memory ally, Superelasticity, Energy storage, Energy dissipation, Damping, Strain rate, Cyclic deformation, Titanium–nickel alloy, Environment Affiliations:
Pieczyska E.A. | - | IPPT PAN | Gadaj S.P. | - | IPPT PAN | Nowacki W.K. | - | IPPT PAN | Hoshito K. | - | other affiliation | Makino Y. | - | other affiliation | Tobushi H. | - | Aichi Institute of Technology (JP) |
| 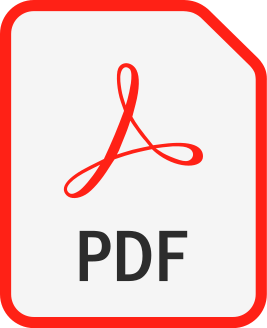 |
41. |
Gadaj S.P., Nowacki W.K., Pieczyska E.A., Tobushi H.♦, Temperature measurement as a new technique applied to the phase transformation study in a TiNi shape memory alloy subjected to tension,
ARCHIVES OF METALLURGY AND MATERIALS, ISSN: 1733-3490, Vol.50, No.3, pp.661-674, 2005 | 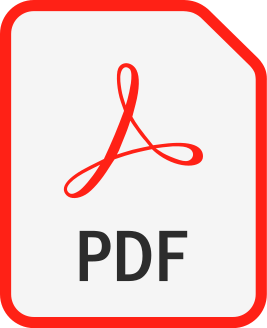 |
42. |
Pieczyska E.A., Gadaj S.P., Nowacki W.K., Tobushi H.♦, Thermomechanical investigations of martensitic and reverse transformations in TiNi shape memory alloy,
BULLETIN OF THE POLISH ACADEMY OF SCIENCES: TECHNICAL SCIENCES, ISSN: 0239-7528, Vol.52, No.3, pp.165-171, 2004 Abstract: Shape memory alloys are characterised by interesting properties, i.e. shape memory effect and pseudoelasticity, which enable their
increasing application. Thermomechanical aspects of martensitic and reverse transformations in TiNi shape memory alloy subjected to tension
tests were investigated. The stress-strain characteristics obtained during the tests were completed by the temperature characteristics. The temperature
changes were calculated on the basis of thermograms determined by an infrared camera. Taking advantages from the infrared technique,
the temperature distributions on the specimen’s surface were found. Heterogeneous temperature distributions, related to the nucleation and
development of the new martensite phase, were registered and analysed. A significant temperature increase, up to 30 K, was registered during
the martensitic transformation. The similar effects of the heterogeneous temperature distribution were observed during unloading, while the
reverse transformation, martensite into austenite took place, accompanied by significant temperature decrease. Keywords: shape memory alloy, pseudoelasticity, transformation front, thermomechanical, investigations Affiliations:
Pieczyska E.A. | - | IPPT PAN | Gadaj S.P. | - | IPPT PAN | Nowacki W.K. | - | IPPT PAN | Tobushi H. | - | Aichi Institute of Technology (JP) |
| 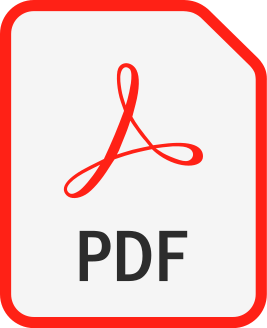 |